Rewriting of Bride Lab
docx
keyboard_arrow_up
School
University of Missouri, Columbia *
*We aren’t endorsed by this school
Course
1100
Subject
Mechanical Engineering
Date
Dec 6, 2023
Type
docx
Pages
3
Uploaded by CorporalLorisPerson977
Bridge Lab
Introduction
The purpose of this lab was to create a bridge out of plastic that could whistand as much sand
as possible. The bridge must cover a gap between two tables that is 18 inches and also must be
at least 3 inches in width. We are supposed to keep the cost in mind while creating and
designing the bridge. Each different length of plastic cost a certain amount ranging from $3,000
to $7,000. Each plastic joint costs an additional $500.
Procedure
We began the lab by brainstorming different designs. We decided to go with a design that was
made up of small triangles which we thought would make the bridge as sturdy as possible. We
wanted to use the least amount of joints thinking that it would allow for our bridge to be stronger
and less likely to collapse. We started with building the base making sure it was at least 18
inches. After that we started to build up using small triangles until we created a large triangle
that we felt was strong enough to hold enough sand. Our design most closely resembled the
Pratt Truss in the end.
Bill of Materials
Part
Quantity
Cost
Joint
20
$4,000
7.5”
6
$42,000
5”
22
$132,000
3”
2
$10,000
2”
8
$32,000
Total Cost:
$220,000
This table is a Bill of Materials that shows all of the parts that we ended up using and their
corresponding costs. Under it is the total cost of materials used that was $220,000
Photos
This picture shows a rough sketch of the front, top, and right side views with approximated
dimensions.
This photo shows a front view of our final design.
This photo shows an isometric view of our final design.
Discussion
After testing our bridge was able to hold a final weight of 10.6 lbs. It did this while itself only
weighing a total of .38 lbs. This resulted in a total efficiency of 2789%. During the test our bridge
began to fail at the second joint from the bottom that can be seen in the front view photo on the
left side. The plastic stick slipped out of the joint causing the bridge to collapse on itself. We
believe this happened because the weight shifted from one side to another causing the stick to
shift outwards from the rest of the bridge. To strengthen our bridge where we failed we
estimated that it would cost roughly $30,000 more than the current cost. The cost of this bridge
today with added maintenance for 50 years would total up to be $1,245,000.
Conclusion
In conclusion, bridges that include fewer square/parallel beams with no supporting cross
members (specifically ones that form triangles)
are both more expensive and less efficient.
Conversely, bridges that include many small triangles and fewer large triangles tend to be just
as efficient while costing more overall. The bridge we built had the lowest cost out of the class
while still maintaining nearly 2800% efficiency. This gave us a cost per percent efficiency of
$78.57 per percent efficiency. Additionally, reducing the amount of zero force members in a
truss while maximizing the member that will experience a compressive force when the load is
applied will reduce the cost while maximizing the efficiency of the bridge. So the ideal bridge is
one that has larger inexpensive triangles, fewer joints, and as few zero force members as
possible.
Your preview ends here
Eager to read complete document? Join bartleby learn and gain access to the full version
- Access to all documents
- Unlimited textbook solutions
- 24/7 expert homework help
Related Documents
Related Questions
Simple Machines-Levers, Inclined Planes, and Pulleys
Directions: Use the appropriate equation to answer the following questions. All answers should be
recorded below or in your Engineering Design journal. Remember to show all work.
A lever has an effort arm that is 5 meters long and a resistance (load) arm that is 3.5 meters
long. How much effort is needed to lift a 100 Newton weight? 5K
i). Draw the figure representing the problem
ii). How much effort is needed to lift a 100 Newton weight?
iii). What is the Actual Mechanical Advantage
1.
5m
i)
AOON 5-5m
arrow_forward
In a room 12'-4" by 13'-9" with 8'-0" high ceilings, there is one door 3'x7' and two windows 4' square. Assume there is no waste in materials, and round off your answer to the next larget unit.
A. How much wall surface in square feet is there to paint?
B. What is the floor area?
C. How many gallons of paint will be required to cover the walls with 2 coats of paint if each gallon covers 200 square feet of surface?
D. How many lineal feet of cove base floor trim will be required?
arrow_forward
5 Look at the flow chart showing the steps of the design process. Then read the list of
steps for designing a thermos. These steps are not in order. Write the letter of each
step in the appropriate box of the flow chart.
The Design Process
Find a problem
Keep records
Plan and build
a prototype
Keep records
Test and
improve
Keep records
Communicate
the solution
arrow_forward
Paper cups are sold in packages of 6, and napkins are sold in packages of 8. Ted wants to buy the same number of each. What is the least number of cups and napkins he needs to buy?
arrow_forward
Please do the last two questions (3 and 4)! Thank you in advance!
A seesaw that weights 45lbs and its 5m long is balanced on the fulcrum in the center.
1- Two children are sitting on opposite sides of each other on the seesaw. One child weights 50lbs and is sitting 0.7m on the left end. Where should the other child sit in order to be balanced on the seesaw if they weigh 42lbs?
2- Now, a third child wants to sit on the seesaw and weighs 30lbs and is sitting 1.25m in front of them and is closer to the fulcrum on the right side. What are the CW and CCW moment of the seesaw now? What is the net moment and direction?
3- Then, a fourth child wants to play on the seesaw and is on the left side of the plank in order to bring the system to equilibrium. How much does the child weigh (Calculate the pounds of force needed in order for rebalance?)
4- Now the fourth child leaves the other three children sitting on the plank. If the three children are sitting in the same potions as they did in…
arrow_forward
1.
This is a question based on the text book ‘’Mechanics of Materials’’ , please reply detail solution with instructions.(This is not a graded assignment. It's just a previous homework which I have finished and wanted to know the solution.)
* I will rate the reply with “Like/Upvote,” if it is a complete step-by-step solution.
* If it is an incomplete solution and there are some shortcuts of solution make me hard to understand, I will rate the reply with “Dislike/Downvote”.
arrow_forward
I am trying to practice this problem using a checker online, but everytime I recalculate my answer it always says it's incorrect. So far I have calculated and tried to input the following values: 1 hp, 1.01 hp, 0.8 hp, and 12.53 hp, but it always keeps saying they are incorrect. Please help show me the correct steps on how to get the correct answer as I am trying to learn this process. Thank you!
arrow_forward
The length of a ribbon is 1.28 m. The length of a rope is 2.74 m longer than the ribbon. What is the length of the rope?
arrow_forward
19
please answer the problems, the answer is already given i just need the solution
please type your answer if you can because i can't view written answers
arrow_forward
hints:
The flask will be filled with water (at a constant rate of 500 gallons per minute).
It will take me exactly 10 minutes to escape from the chains.
The diameter of the tank at 1 foot intervals.
I am 5 feet 9 inches tall, and I'm pretty skinny so that you can ignore both my volume and the volume of the stool in your analysis.
A gallon is equal to 0.13368 cubic feet.
You can think of the volume and the height of the water as functions of time. You can easily find an expression for V (t), and then use your expression for volume in terms of height to solve for h(t).
after 10 minutes amount of water in the tank=66.84 ft3
t=69.3 minutes
h(t)=e66.84t/100? -1
h(10)=e66.84(10)/100? -1=7.39 ft
Height of stool=1.64 ft
Height of water in the tank=7.39 ft
Questions: show work
How fast is the water rising?
I would like to know how long I will have to hold my breath during the last part of the stunt.
arrow_forward
Please do the last three questions (2, 3 and 4)! Thank you in advance!
A seesaw that weights 45lbs and its 5m long is balanced on the fulcrum in the center.
1- Two children are sitting on opposite sides of each other on the seesaw. One child weights 50lbs and is sitting 0.7m on the left end. Where should the other child sit in order to be balanced on the seesaw if they weigh 42lbs?
2- Now, a third child wants to sit on the seesaw and weighs 30lbs and is sitting 1.25m in front of them and is closer to the fulcrum on the right side. What are the CW and CCW moment of the seesaw now? What is the net moment and direction?
3- Then, a fourth child wants to play on the seesaw and is on the left side of the plank in order to bring the system to equilibrium. How much does the child weigh (Calculate the pounds of force needed in order for rebalance?)
4- Now the fourth child leaves the other three children sitting on the plank. If the three children are sitting in the same potions as they did…
arrow_forward
Recall the discussion on spacecraft from the chapter opener. The following problems consider a rocket launch from Earth’s surface. The force of gravity on the rocket is given by F(d)=−mk/d2, where m is the mass of the rocket, d is the distance of the rocket from the center of Earth, and k is a constant.
172.
As the rocket travels away from Earth’s surface, there is a distance D where the rocket sheds some of its mass, since it no longer needs the excess fuel storage. We can write this function as F(d)=⎨(−m↓1 k / d^2) if d < D
(−m↓2 k / d^2) if d ≥ D
Is there a D value such that this function is continuous, assuming m1≠m2?
arrow_forward
Seatwork #1: Show your step-by-step solution to solve the given problems and box your final answers.
Pattern your solution as shown in sample problems, if possible,
1.) When water is boiled at a pressure of 2.00 atm, the heat of vaporization is 2.20x10-6
and the
kg
boiling point is 120 C. At this pressure, 1.00 kg of water has a volume of of 1.00x10-3m³ and 1.00 kg of
steam has a volume of 0.824 m3. (a) Compute the work done when 1.00 kg of steam is formed at this
temperature. (b) Compute the increase in internal energy of the water.
2.) A room air conditioner has a coefficient of performance of 2.9 on a hot day and uses 850 W of electrical
power. (a) How many joules of heat does the air conditioner remove from the room in one minute? (b)
How many joules of heat does the air conditioner deliver to the hot outside air in one minute? (c) Explain
why your answers to parts (a) and (b) are not the same.
3.) A Carnot heat engine has a thermal efficiency of 0.600, and the temperature of its…
arrow_forward
Table 1: Mechanical behavior of human cadaver tibial bones
during pure torsional loads applied with the proximal tibia
fixed and the torque applied to the distal tibia until there is
bone fracture.
Medial condyle
Tibial tuberosity-
Medial malleolus
-Lateral condyle
Head of fibula
Ti-6Al-4V grade 5
Stainless Steel 316L
Region of bone
resection
-Lateral malleolus
L = 365 mm
Annealed
Annealed
Torque at ultimate failure (bone fracture)
Displacement (twist angle) at ultimate failure
Torsional Stiffness
Table 2: Mechanical properties of candidate materials for the rod.
Material
Process
Yield Strength
(MPa)
880
220-270
Do = 23 mm
Elastic
Modulus (GPa)
115
190
d₁ = 14 mm
Figure 1: Representative tibia bone showing the resection region (blue arrows) and median length (L). A circular cross section of distal tibia
taken at the level of resection) showing the median inner (di) and outer (Do) diameters of the cortical bone. A tibia bone after resection with the
proposed metal solid rod (black line)…
arrow_forward
Question 2
You are a biomedical engineer working for a small orthopaedic firm that fabricates rectangular shaped fracture
fixation plates from titanium alloy (model = "Ti Fix-It") materials. A recent clinical report documents some problems with the plates
implanted into fractured limbs. Specifically, some plates have become permanently bent while patients are in rehab and doing partial
weight bearing activities.
Your boss asks you to review the technical report that was generated by the previous test engineer (whose job you now have!) and used to
verify the design. The brief report states the following... "Ti Fix-It plates were manufactured from Ti-6Al-4V (grade 5) and machined into
solid 150 mm long beams with a 4 mm thick and 15 mm wide cross section. Each Ti Fix-It plate was loaded in equilibrium in a 4-point bending
test (set-up configuration is provided in drawing below), with an applied load of 1000N. The maximum stress in this set-up was less than the
yield stress for the…
arrow_forward
Please solve the Problem within 20 Minutes.
Very urgent , Please make sure the answer is correct.
arrow_forward
SEE MORE QUESTIONS
Recommended textbooks for you
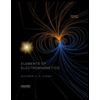
Elements Of Electromagnetics
Mechanical Engineering
ISBN:9780190698614
Author:Sadiku, Matthew N. O.
Publisher:Oxford University Press
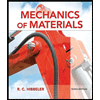
Mechanics of Materials (10th Edition)
Mechanical Engineering
ISBN:9780134319650
Author:Russell C. Hibbeler
Publisher:PEARSON
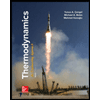
Thermodynamics: An Engineering Approach
Mechanical Engineering
ISBN:9781259822674
Author:Yunus A. Cengel Dr., Michael A. Boles
Publisher:McGraw-Hill Education
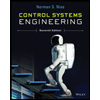
Control Systems Engineering
Mechanical Engineering
ISBN:9781118170519
Author:Norman S. Nise
Publisher:WILEY
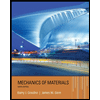
Mechanics of Materials (MindTap Course List)
Mechanical Engineering
ISBN:9781337093347
Author:Barry J. Goodno, James M. Gere
Publisher:Cengage Learning
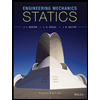
Engineering Mechanics: Statics
Mechanical Engineering
ISBN:9781118807330
Author:James L. Meriam, L. G. Kraige, J. N. Bolton
Publisher:WILEY
Related Questions
- Simple Machines-Levers, Inclined Planes, and Pulleys Directions: Use the appropriate equation to answer the following questions. All answers should be recorded below or in your Engineering Design journal. Remember to show all work. A lever has an effort arm that is 5 meters long and a resistance (load) arm that is 3.5 meters long. How much effort is needed to lift a 100 Newton weight? 5K i). Draw the figure representing the problem ii). How much effort is needed to lift a 100 Newton weight? iii). What is the Actual Mechanical Advantage 1. 5m i) AOON 5-5marrow_forwardIn a room 12'-4" by 13'-9" with 8'-0" high ceilings, there is one door 3'x7' and two windows 4' square. Assume there is no waste in materials, and round off your answer to the next larget unit. A. How much wall surface in square feet is there to paint? B. What is the floor area? C. How many gallons of paint will be required to cover the walls with 2 coats of paint if each gallon covers 200 square feet of surface? D. How many lineal feet of cove base floor trim will be required?arrow_forward5 Look at the flow chart showing the steps of the design process. Then read the list of steps for designing a thermos. These steps are not in order. Write the letter of each step in the appropriate box of the flow chart. The Design Process Find a problem Keep records Plan and build a prototype Keep records Test and improve Keep records Communicate the solutionarrow_forward
- Paper cups are sold in packages of 6, and napkins are sold in packages of 8. Ted wants to buy the same number of each. What is the least number of cups and napkins he needs to buy?arrow_forwardPlease do the last two questions (3 and 4)! Thank you in advance! A seesaw that weights 45lbs and its 5m long is balanced on the fulcrum in the center. 1- Two children are sitting on opposite sides of each other on the seesaw. One child weights 50lbs and is sitting 0.7m on the left end. Where should the other child sit in order to be balanced on the seesaw if they weigh 42lbs? 2- Now, a third child wants to sit on the seesaw and weighs 30lbs and is sitting 1.25m in front of them and is closer to the fulcrum on the right side. What are the CW and CCW moment of the seesaw now? What is the net moment and direction? 3- Then, a fourth child wants to play on the seesaw and is on the left side of the plank in order to bring the system to equilibrium. How much does the child weigh (Calculate the pounds of force needed in order for rebalance?) 4- Now the fourth child leaves the other three children sitting on the plank. If the three children are sitting in the same potions as they did in…arrow_forward1. This is a question based on the text book ‘’Mechanics of Materials’’ , please reply detail solution with instructions.(This is not a graded assignment. It's just a previous homework which I have finished and wanted to know the solution.) * I will rate the reply with “Like/Upvote,” if it is a complete step-by-step solution. * If it is an incomplete solution and there are some shortcuts of solution make me hard to understand, I will rate the reply with “Dislike/Downvote”.arrow_forward
- I am trying to practice this problem using a checker online, but everytime I recalculate my answer it always says it's incorrect. So far I have calculated and tried to input the following values: 1 hp, 1.01 hp, 0.8 hp, and 12.53 hp, but it always keeps saying they are incorrect. Please help show me the correct steps on how to get the correct answer as I am trying to learn this process. Thank you!arrow_forwardThe length of a ribbon is 1.28 m. The length of a rope is 2.74 m longer than the ribbon. What is the length of the rope?arrow_forward19 please answer the problems, the answer is already given i just need the solution please type your answer if you can because i can't view written answersarrow_forward
- hints: The flask will be filled with water (at a constant rate of 500 gallons per minute). It will take me exactly 10 minutes to escape from the chains. The diameter of the tank at 1 foot intervals. I am 5 feet 9 inches tall, and I'm pretty skinny so that you can ignore both my volume and the volume of the stool in your analysis. A gallon is equal to 0.13368 cubic feet. You can think of the volume and the height of the water as functions of time. You can easily find an expression for V (t), and then use your expression for volume in terms of height to solve for h(t). after 10 minutes amount of water in the tank=66.84 ft3 t=69.3 minutes h(t)=e66.84t/100? -1 h(10)=e66.84(10)/100? -1=7.39 ft Height of stool=1.64 ft Height of water in the tank=7.39 ft Questions: show work How fast is the water rising? I would like to know how long I will have to hold my breath during the last part of the stunt.arrow_forwardPlease do the last three questions (2, 3 and 4)! Thank you in advance! A seesaw that weights 45lbs and its 5m long is balanced on the fulcrum in the center. 1- Two children are sitting on opposite sides of each other on the seesaw. One child weights 50lbs and is sitting 0.7m on the left end. Where should the other child sit in order to be balanced on the seesaw if they weigh 42lbs? 2- Now, a third child wants to sit on the seesaw and weighs 30lbs and is sitting 1.25m in front of them and is closer to the fulcrum on the right side. What are the CW and CCW moment of the seesaw now? What is the net moment and direction? 3- Then, a fourth child wants to play on the seesaw and is on the left side of the plank in order to bring the system to equilibrium. How much does the child weigh (Calculate the pounds of force needed in order for rebalance?) 4- Now the fourth child leaves the other three children sitting on the plank. If the three children are sitting in the same potions as they did…arrow_forwardRecall the discussion on spacecraft from the chapter opener. The following problems consider a rocket launch from Earth’s surface. The force of gravity on the rocket is given by F(d)=−mk/d2, where m is the mass of the rocket, d is the distance of the rocket from the center of Earth, and k is a constant. 172. As the rocket travels away from Earth’s surface, there is a distance D where the rocket sheds some of its mass, since it no longer needs the excess fuel storage. We can write this function as F(d)=⎨(−m↓1 k / d^2) if d < D (−m↓2 k / d^2) if d ≥ D Is there a D value such that this function is continuous, assuming m1≠m2?arrow_forward
arrow_back_ios
SEE MORE QUESTIONS
arrow_forward_ios
Recommended textbooks for you
- Elements Of ElectromagneticsMechanical EngineeringISBN:9780190698614Author:Sadiku, Matthew N. O.Publisher:Oxford University PressMechanics of Materials (10th Edition)Mechanical EngineeringISBN:9780134319650Author:Russell C. HibbelerPublisher:PEARSONThermodynamics: An Engineering ApproachMechanical EngineeringISBN:9781259822674Author:Yunus A. Cengel Dr., Michael A. BolesPublisher:McGraw-Hill Education
- Control Systems EngineeringMechanical EngineeringISBN:9781118170519Author:Norman S. NisePublisher:WILEYMechanics of Materials (MindTap Course List)Mechanical EngineeringISBN:9781337093347Author:Barry J. Goodno, James M. GerePublisher:Cengage LearningEngineering Mechanics: StaticsMechanical EngineeringISBN:9781118807330Author:James L. Meriam, L. G. Kraige, J. N. BoltonPublisher:WILEY
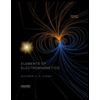
Elements Of Electromagnetics
Mechanical Engineering
ISBN:9780190698614
Author:Sadiku, Matthew N. O.
Publisher:Oxford University Press
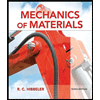
Mechanics of Materials (10th Edition)
Mechanical Engineering
ISBN:9780134319650
Author:Russell C. Hibbeler
Publisher:PEARSON
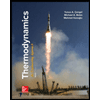
Thermodynamics: An Engineering Approach
Mechanical Engineering
ISBN:9781259822674
Author:Yunus A. Cengel Dr., Michael A. Boles
Publisher:McGraw-Hill Education
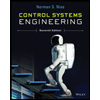
Control Systems Engineering
Mechanical Engineering
ISBN:9781118170519
Author:Norman S. Nise
Publisher:WILEY
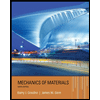
Mechanics of Materials (MindTap Course List)
Mechanical Engineering
ISBN:9781337093347
Author:Barry J. Goodno, James M. Gere
Publisher:Cengage Learning
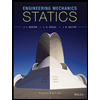
Engineering Mechanics: Statics
Mechanical Engineering
ISBN:9781118807330
Author:James L. Meriam, L. G. Kraige, J. N. Bolton
Publisher:WILEY