FLUIDS_LAB_REPORT_5_1
docx
keyboard_arrow_up
School
California State University, Long Beach *
*We aren’t endorsed by this school
Course
442
Subject
Mechanical Engineering
Date
Dec 6, 2023
Type
docx
Pages
18
Uploaded by kalvarez22
Lab Experiment #5: Energy losses in pipes
CE 336: Fluids Mechanic Laboratory Instructor: Andres Acosta, MS, PE
Submitted by:
Steven Ramirez
Eddie Rangel
Selena Nguyen
Shakir Shihabudeen Justin Nguyen Date of performing lab experiment: 10/12/2022
Date of submitting lab report:11/09/2022
1
Introduction
In this lab experiment a C6-MKII-10 Armfield apparatus was used to measure the major losses when fluid flows through the pipes. The apparatus was powered by the hydraulic bench to allow the fluid flow into the pipes at different flow rates. The apparatus had 5 pipes with various diameters. The 5th pipe had the same diameter as pipe 4, however pipe 5 had a special coating inside to make its inside rough. This was conducted for all 5 pipes. The data that was collected was the pressure drops from 2 different points at the pipe and the volumetric flow rate.The experiment was conducted by allowing the fluid flow into each pipe and a manometer was used to measure pressure at 2 points in the pipe. The 2 points of pressure drop were subtracted to get the measured head loss. The flow rate was decreased 10 times to have 10 different measurements
for each pipe. Using the data, we can calculate the Re,friction factor, and the calculated head loss.
Purpose of Study
The purpose of this experiment is to demonstrate major losses when fluid flows through pipes. We also see how different pipe sizes can affect energy losses in pipes for both laminar and turbulent flows. Theory
Reynolds number was developed by Osbonrne Reynolds to demonstrate that in pipe there are two types of flow which are Laminar flow and Turbulent flow. Reynolds number is defined as:
ℜ=
VD
v
=
ρVD
μ
Where V is the flow velocity through the pipe, D is the diameter of the pipe, v is the kinematic
2
viscosity of the fluid, μ
is the dynamic viscosity of the fluid, and ρ
is the density of the fluid.
For ℜ
< 3000, flow is defined as laminar, ℜ
> 5000 flow is defined as turbulent flow, and
for 3000 < ℜ
< 5000, flow is transitional and it cannot be defined accurately.
The experiments show that frictional head losses in pipes are not dependent on pressure of the fluid flows. Also the head loss is proportional to the length of the pipe and is inversely to the diameter of the pipe. The pipe roughness is related to the head loss when dealing with turbulent flow.
Henry Darcy and Julius Weisbach found the equations for frictional head loss based on the relationships found through several experiments:
h
=
f
L
D
V
2
2
g
Where h is the frictional head loss, f is the Darcy-Weisbach friction factor, L is the length of the pipe, D is the diameter of the pipe, V is the flow velocity.
For the laminar flow:
f
=
64
ℜ
The friction factor can be calculate by using the Swamee-Jain equation:
f
=
0.25
[
log
(
ε
D
3.7
+
5.74
ℜ
0.9
)]
2
Where ε
D
is the relative roughness of the pipe material. ε
is the roughness height of the pipe material and D is the diameter of the pipe.
Your preview ends here
Eager to read complete document? Join bartleby learn and gain access to the full version
- Access to all documents
- Unlimited textbook solutions
- 24/7 expert homework help
3
For turbulent flow, the friction factor can also be determined by the Moody chart which was developed by Lewis Moody. The chart shows four zones of pipe flow:
●
Laminar flow zone ●
Transitional zone
●
Transitional turbulent flow
●
Turbulent zone
Equipment
A C6-MKII-10 Armfield apparatus which consists of the following:
●
4 smooth pipes with different diameters ●
1 rough pipe ●
A hand held pressure measure device that can be attached with the attachments to measure the head loss in pipes which are separated by 1 meter.
●
A 500 ml cylinder and a stopwatch to measure the flow rate of the 5 mm diameter pipe.
Experimental Setup & Procedures: This experiment consists of two exercises: measure the head loss of the flow through smooth pipes and the head loss of the flow through roughened pipe.
The first part of the experiment starts with opening the valve of the roughened 17 mm which is located at the bottom of the apparatus, shutting the valve of the hydraulic bench all the way.
4
Next, turn the hydraulic bench pump. Adjust the valve of the hydraulic bench to establish a slow and steady flow through the pipe, make sure to close the valve of all the different diameter pipes.
Now, measure the head loss of the flow through the roughened pipe by using the pressure measure device, connect the device to the two tapings in the pipe separated by one meter. After absorbing the pressure values from the two tapings, the head loss can be obtained by the difference from the pressure values. The flow rate can be obtained by reading the screen of the hydraulic bench. Next, decrease the flow rate by 0.02 l/s in the hydraulic bench by slowly adjusting the valve and record the head loss by measuring pressure for the two tapings on the pipe. Repeat these steps and observe the head loss for ten different flow rates. The second part of the experiment consists of working on the remaining 4 smooth pipes with different diameters. After establishing the data for the roughened 17 mm pipe, close the valve of this pipe completely and open the 17 mm smooth pipe which is located right upper the roughened pipe. Repeat the pressure drop records for ten different flow rates for this pipe. The flow rate can still be obtained by reading the screen of the hydraulic bench. Do the same things for the 11 mm and 8 mm diameter pipes to obtain the head loss for ten different flow rates, the flow rate values can still be collected by reading the screen of the hydraulic bench. The flow rate for the 5 mm pipe can be obtained by using the 500 ml cylinder and the stopwatch. Open the valve completely for this pipe and measure the time to collect 500 ml of water, from time and volume values, the flow rate can be calculated. After obtaining the flow rate, use the pressure measure to collect the pressure of the two tapings of the pipe and from that the head loss can be calculated. Repeat the steps for ten different flow
5
rates to obtain the head losses.
Calculations:
D
=
8
mm
=
.008
m
.008
¿
2
¿
π
¿
A
=
π D
2
4
=
¿
ε
D
=
0
(
smooth pipe
)
Q
=
∀
t
=
500
mm
3
∗
10
−
3
7.93
s
=
.000063
m
3
s
V
=
Q
A
=
.000063
m
3
s
0.00005027
m
2
=
1.253
m
s
ℜ=
VD
ν
=
1.253
m
s
∗
.008
m
10
−
6
=
10026.761
log
(
ε
/
D
3.7
+
5.74
R e
0.9
)
¿
2
¿
log
(
0
3.7
+
5.74
10026.761
0.9
)
¿
2
¿
¿
¿
f
=
0.25
¿
1.253
m
s
¿
2
(
¿¿
2
(
9.81
))=
0.310
m
H
2
0
¿
h
=
f
L
D
V
2
2
g
=(
0.0309
)(
1
m
.008
m
)
¿
Questions/Discussion
Data
Table 1: Pipe loss data for D=5mm
Table 1
Relative
0
Diameter(m)
0.005
Area
0.0000196
Your preview ends here
Eager to read complete document? Join bartleby learn and gain access to the full version
- Access to all documents
- Unlimited textbook solutions
- 24/7 expert homework help
6
roughness
3
Volume
Time
Flow Rate
Velocity
Reynolds
Number
Calculated
Friction
Factor
Calculated
head loss
Measured
head loss
V (liters)
t (secs)
Q (m^3/s)
V (m/s)
Re
f
h_c
(mH2O)
h_m (m
H2O)
500
7.93
0.000063
3.209
16042.818
0.0273
2.865
3.094
500
8.24
0.000061
3.107
15533.522
0.0275
2.709
3.094
500
8.47
0.000059
3.005
15024.227
0.0278
2.556
3.094
500
8.65
0.000057
2.903
14514.931
0.0280
2.408
3.023
500
8.84
0.000056
2.852
14260.283
0.0282
2.335
2.531
500
10.28
0.000048
2.445
12223.100
0.0293
1.787
1.969
500
16.92
0.000029
1.477
7384.789
0.0337
0.750
0.633
500
19.43
0.000025
1.273
6366.198
0.0352
0.582
0.352
500
27.62
0.000018
0.917
4583.662
0.0389
0.333
0.070
500
117.2
4.30E-06
0.219
1094.986
0.0640
0.031
0.000
Table 2: Pipe loss data for D=8mm
Table 2
Relative
roughness
0
Diameter(m)
0.008
Area
0.0000502
7
Volume
Time
Flow Rate
Velocity
Reynolds
Number
Calculated
Friction
Factor
Calculated
head loss
Measured
head loss
V (liters)
t (secs)
Q (m^3/s)
V (m/s)
Re
f
h_c
(mH2O)
h_m (m
H2O)
-
-
0.000205
4.078
32626.763
0.0229
2.428
2.250
-
-
0.0002
3.979
31830.989
0.0230
2.324
2.180
-
-
0.000195
3.879
31035.214
0.0232
2.223
2.039
-
-
0.00019
3.780
30239.439
0.0233
2.124
1.898
-
-
0.000185
3.680
29443.664
0.0235
2.026
1.758
-
-
0.00018
3.581
28647.890
0.0236
1.931
1.617
-
-
0.000175
3.482
27852.115
0.0238
1.837
1.547
-
-
0.00017
3.382
27056.340
0.0240
1.746
1.406
-
-
0.000165
3.283
26260.566
0.0241
1.657
1.266
-
-
1.60E-04
3.183
25464.791
0.0243
1.570
1.055
7
Table 3: Pipe Loss Calculations for D=11m
Table 3
Relative
roughness
0
Diameter(m)
0.011
Area
0.0000950
3
Volume
Time
Flow Rate
Velocity
Reynolds
Number
Calculated
Friction
Factor
Calculated
head loss
Measured
head loss
V (liters)
t (secs)
Q (m^3/s)
V (m/s)
Re
f
h_c
(mH2O)
h_m (m
H2O)
-
-
0.000324
3.409
37502.692
0.0222
1.194
1.308
-
-
0.000304
3.199
35187.711
0.0225
1.067
1.104
-
-
0.000284
2.988
32872.730
0.0229
0.946
1.146
-
-
0.000264
2.778
30557.749
0.0233
0.832
0.998
-
-
0.000244
2.568
28242.768
0.0237
0.724
0.773
-
-
0.000224
2.357
25927.787
0.0242
0.623
0.738
-
-
0.000204
2.147
23612.806
0.0248
0.529
0.633
-
-
0.000184
1.936
21297.825
0.0254
0.441
0.422
-
-
0.000164
1.726
18982.844
0.0262
0.361
0.316
-
-
0.000144
1.515
16667.863
0.0270
0.288
0.337
Table 4: Pipe Loss Calculations for D=17mm
Table 4
Relative
roughness
0
Diameter(m)
0.017
Area
0.0002269
8
Volume
Time
Flow Rate
Velocity
Reynolds
Number
Calculated
Friction
Factor
Calculated
head loss
Measured
head loss
V (liters)
t (secs)
Q (m^3/s)
V (m/s)
Re
f
h_c
(mH2O)
h_m (m
H2O)
-
-
0.000430
1.894
32205.471
0.0230
0.247
0.141
-
-
0.000410
1.806
30707.542
0.0232
0.227
0.211
-
-
0.000390
1.718
29209.613
0.0235
0.208
0.211
-
-
0.000370
1.630
27711.684
0.0238
0.190
0.211
-
-
0.000350
1.542
26213.755
0.0241
0.172
0.070
-
-
0.000330
1.454
24715.826
0.0245
0.155
0.141
-
-
0.000310
1.366
23217.898
0.0249
0.139
0.070
-
-
0.000290
1.278
21719.969
0.0253
0.124
0.070
8
-
-
0.000270
1.190
20222.040
0.0257
0.109
0.176
-
-
0.000259
1.141
19398.179
0.0260
0.102
0.088
Table 5: Pipe Loss for D=17mm (rough)
Table 5
Relative
roughness
0.0375
Diameter(m)
0.017
Area
0.0002269
8
Volume
Time
Flow Rate
Velocity
Reynolds
Number
Calculated
Friction
Factor
Calculated
head loss
Measured
head loss
V (liters)
t (secs)
Q (m^3/s)
V (m/s)
Re
f
h_c
(mH2O)
h_m (m
H2O)
-
-
0.000391
1.723
29284.510
0.0643
0.572
0.879
-
-
0.000371
1.635
27786.581
0.0644
0.516
0.879
-
-
0.000351
1.546
26288.652
0.0645
0.462
0.717
-
-
0.000331
1.458
24790.723
0.0646
0.412
0.809
-
-
0.000311
1.370
23292.794
0.0647
0.364
0.647
-
-
0.000291
1.282
21794.865
0.0648
0.319
0.492
-
-
0.000271
1.194
20296.936
0.0649
0.277
0.387
-
-
0.000251
1.106
18799.007
0.0650
0.238
0.422
-
-
0.000231
1.018
17301.079
0.0652
0.202
0.141
-
-
0.000211
0.930
15803.150
0.0654
0.169
0.105
Figure 1: Measured Head Loss vs. Velocity for D=5mm
Laminar Flow
Transational Flow
Turbulent Flow
Your preview ends here
Eager to read complete document? Join bartleby learn and gain access to the full version
- Access to all documents
- Unlimited textbook solutions
- 24/7 expert homework help
9
Figure 2: Measured Head Loss vs. Velocity for D=8mm
Figure 3: Measured Head Loss vs. Velocity for D=11mm
10
Figure 4: Measured Head Loss vs. Velocity for D=17mm
Figure 5: Measured Head Loss vs. Velocity for D=17mm(rough)
Figure 6: Log h
m
vs. log V for D=5mm
log h_m
log v
0.4905
0.5063
0.4905
0.4923
0.4905
0.4778
0.4805
0.4628
0.4033
0.4552
0.2942
0.3882
-0.1988
0.1694
11
-0.4540
0.1049
-1.1530
-0.0378
0.0000
-0.6596
Slope (n)
0.8268177026
Figure 7: Log h
m
vs. log V for D=8mm
log h_m
log v
0.3521
0.6105
0.3384
0.5998
0.3094
0.5888
0.2784
0.5775
0.2449
0.5659
0.2087
0.5540
0.1894
0.5418
0.1480
0.5292
0.1023
0.5162
0.0000
0.5029
Slope (n)
3.026094972
Your preview ends here
Eager to read complete document? Join bartleby learn and gain access to the full version
- Access to all documents
- Unlimited textbook solutions
- 24/7 expert homework help
12
Figure 8: Log h
m
vs. log V for D=11mm
log h_m
log v
0.117
0.533
0.043
0.505
0.059
0.475
-0.001
0.444
-0.112
0.410
-0.132
0.372
-0.199
0.332
-0.375
0.287
-0.500
0.237
0.000
0.180
Slope (n)
1.124306416
13
Figure 9: Log h
m
vs. log V for D=17mm
log h_m
log v
-0.8520
0.2775
-0.6759
0.2568
-0.6759
0.2351
-0.6759
0.2122
-1.1530
0.1881
-0.8520
0.1625
-1.1530
0.1354
-1.1530
0.1064
-0.7551
0.0754
0.0000
0.0573
Slope (n)
-0.9022904503
Figure 10: Log h
m
vs. log V for D=17mm (rough)
log h_m
log v
-0.0561
0.2362
-0.0561
0.2134
-0.1444
0.1893
-0.0923
0.1638
-0.1892
0.1368
-0.3079
0.1079
-0.4126
0.0770
-0.3749
0.0437
-0.8520
0.0076
14
0.0000
-0.0317
Slope (n)
1.42192944
Figure 11: h
m
vs Re for all pipe diameters
Your preview ends here
Eager to read complete document? Join bartleby learn and gain access to the full version
- Access to all documents
- Unlimited textbook solutions
- 24/7 expert homework help
15
Questions 1.
What is the n value when you plot log h
m
versus log V for each size of pipes (h
m
∞V
n
) for all pipe sizes? What value of n you expected? a.
The n values for the various pipe sizes after plotting are as follows. The pipe with the diameter of 5mm had an n value of 0.827
. The following pipe with a diameter of 8mm had a value of 3.026
. Next, the diameter of 17mm had a value of -0.902
. Lastly, the pipe with the same diameter of the previous (17mm) but a non smooth (rough) interior had a n value of 1.422
. The values from each of the pipes align with what we expected.
1.
Comparing between the head loss values computed using Darcy Weisbach’s equation and the corresponding measured values for various pipe sizes we see that the measured values
have an average error of 22% compared to the calculated values.
2.
Darcy Weisbach’s equation can also be utilized to obtain friction losses if fluid velocity and pipe dimensions are known as well as the head loss by manipulating the equation.
3.
The Reynold’s number was significantly higher initially in every step as the flow rate was
at its highest and as that decreased so did the number.
4.
As the Reynold’s number decreased in each trial the measured head loss did as well. The pipe with the highest value of head loss was the 8mm diameter pipe. 5.
Rough pipes will always have greater head loss than their smooth counterparts. Two trials
within the experiment tested pipes of the same 17mm diameter, but one considered smooth and the other considered rough. The rough pipe experienced twice as much head
16
loss with the same flow rate into both. Conclusion
This lab successfully demonstrated the characteristics of major head losses when fluid flows through pipes of various diameters and roughnesses experiencing laminar and turbulent flow. We
observed that frictional head losses in pipes are not dependent on pressure of the fluid flows and the head loss is proportional to the length of the pipe and is inversely to the diameter of the pipe. Each pipe within the experiment had varying diameters and the values for head loss both calculated and measured reflect how as the diameter decreased the head loss values generally increased. It was apparent that turbulent flow is considered more so in rough pipes than in smooth pipes. With various ways to obtain head loss through equations and charts when compared to the measured values throughout the lab there is an average error margin of 22%. However, the ultimate purpose of the experiment was to observe and report the trends between head loss, pipe geometry, and friction factors. These trends were made very apparent while analyzing the data obtained and agree with our understanding of major losses in pipes.
17
References Sultana, Rebeka. “Lab #5 Energy losses in pipes.” Fluid Mechanics Laboratory Student Manual.
2017. Print.
Your preview ends here
Eager to read complete document? Join bartleby learn and gain access to the full version
- Access to all documents
- Unlimited textbook solutions
- 24/7 expert homework help
Related Documents
Related Questions
Problem 7: A small ball bearing is released from rest in a tank of oil at t = 0. The downward
acceleration of the ball bearing is g - kv, where g is the constant acceleration due to gravity,
k is a constant that depends on the viscosity of the oil, and is the downward velocity of the
object. Derive expressions for the velocity and the displacement y as function of the time t
after the ball bearing's release.
Ans (partial): v = g(1 - e-kt)/k
arrow_forward
CHAPTER 5 : DIESEL ENGINE POWER PLANT
A six cylinder, four-stroke CI engine is tested against a water brake dynamometer for which
B.P = WN/17x10' in kW, where W is the brake load in newton and N is the speed of the
engine in the r.p.m. The air consumption was measured by means of a sharp edged orifice.
During the test following observersations were taken :
• Bore
• Stroke
• Speed
• Brake load
Barometer reading
= 10 cm
= 14 cm
= 2500 rpm
= 480 N
= 76 cm Hg
• Orifice diameter
• Co-efficient of discharge of orifice
• Pressure drop across orifice
• Room temperature
Fuel Consumption
= 3.3 cm
= 0.62
= 14 cm of Hg
= 25°C
= 0.32 kg/min
Calculate following :
i.
The volumetric efficiency
The brake mean effective pressure ( b.m.e.p)
The engine torque
The brake specific fuel consumption ( b.s.f.c )
ii.
iv.
arrow_forward
Pressurized eyes Our eyes need a certain amount of internal pressure in order to work properly, with the normal range being between 10 and 20 mm of mercury. The pressure is determined by a balance between the fluid entering and leaving the eye. If the pressure is above the normal level, damage may occur to the optic nerve where it leaves the eye, leading to a loss of the visual field termed glaucoma. Measurement of the pressure within the eye can be done by several different noninvasive types of instruments, all of which measure the slight deformation of the eyeball when a force is put on it. Some methods use a physical probe that makes contact with the front of the eye, applies a known force, and measures the deformation. One non-contact method uses a calibrated “puff” of air that is blown against the eye. The stagnation pressure resulting from the air blowing against the eyeball causes a slight deformation, the magnitude of which is correlated with the pressure within the eyeball.…
arrow_forward
Instrumentation & Measurements
This homework measures your capability to design/analyze various components/variables of ameasurement system based on what you have studied.
Question is Attached in image. Thank you.
arrow_forward
Problems
Chapter 17 of "Physics for Scientists and Engineers", 10th ed. by Serway and Jewet.
Two sound waves arrive at your ear simultaneously; they have slightly different frequencies: wi and
w2 and equal amplitudes. You hear the loudness oscillate sinusoidally; this is what we refer to as
"beats". Show that the total sound wave has the the form:
P(t) = Patm + 28P cos((w1 - w2)/2) cos((w1 + w2)/2).
(1)
e,
bimagination
Cosl lWi-We) +
Cos/ (W,+We)+
Real puth Releiter Reterort
ot above
expussion
Real purts
Coslwit) + Cos (We t)
arrow_forward
Is this Correct?
arrow_forward
Kindly solve this problem with complete solution so that I can Understand.
Correct Final answer: 1400 or 1.4x10^3
arrow_forward
Instrumentation & Measurements
This homework measures your capability to design/analyze various components/variables of ameasurement system based on what you have studied.
Question 1 Attached.
arrow_forward
3. Microfluidic channels will need to be fabricated on a key micro-scale sensor used by aerospace
industries. Before running machining tests and analyzing machined quality, preliminary efforts are needed
to evaluate selected materials and factors affecting machining process¹. Three material candidates have
been selected, including 422SS (stainless steel), IN718 (nickel alloy), and Ti64 (titanium alloy) with their
measured tensile properties and equation of true stress-true strain relationship used listed below. Tref25°C.
Specifically, three factors will need to be evaluated, including different materials, temperature, and size
effect. Please calculate true stress values for true strain ranging between 0-3 for each case listed below.
Material
A (MPa)
& (S-¹)
Tm (°C)
870
0.01
1520
422SS (Peyre et al., 2007)
IN718 (Kobayashi et al., 2008)
Ti64 (Umbrello, 2008)
980
1
1300
782.7
1E-5
1660
Material
422SS (CINDAS, 2011)
IN718 (Davis, 1997)
Ti64 (Fukuhara and Sanpei, 1993)
0 =
X
G (GPa)
1+
B…
arrow_forward
https://pubmed.ncbi.nlm.nih.gov/32521345/
In the literature review, they should present the system installed and the main results obtained. In other words, the enhancement due to the installed system. They have to define the system used in this study. (the report talking about ventilation) pls in briefly
Don’t using chatgpt please urgent
i will give u like
arrow_forward
solve manually
arrow_forward
A used battery was brought to the workshop and the technician noticed that it had
1 litre of distilled water in it but was fully discharged. The specs sheet for this type
of battery states that it is fully charged when the change in distilled water to the
change in charge equals to the difference between twice the amount of charge and
the actual amount of distilled water existing in the battery
For the used battery, derive the differential equation and
state the initial condition for the range x= 0(0.2)1.0, then obtain a numerical solution for
this equation using Euler’s method.
arrow_forward
Q.1
a. Repeatability and reproducibility are ways of measuring precision, particularly in the field of
engineering.
i.
What is an engineer's expectation when performing repeatability or reproducibility?
ii.
State a difference between repeatability and reproducibility in an experiment?
b. Figure Q.1 shows the measurement data of two types of thermal transducers namely thermocouple.
Турe E
Туре К
6.8
4.2
20
40
60
80
100
Temperature Difference (°C)
Voltage Output (mV)
arrow_forward
SEE MORE QUESTIONS
Recommended textbooks for you
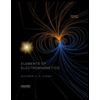
Elements Of Electromagnetics
Mechanical Engineering
ISBN:9780190698614
Author:Sadiku, Matthew N. O.
Publisher:Oxford University Press
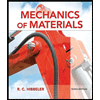
Mechanics of Materials (10th Edition)
Mechanical Engineering
ISBN:9780134319650
Author:Russell C. Hibbeler
Publisher:PEARSON
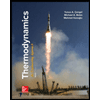
Thermodynamics: An Engineering Approach
Mechanical Engineering
ISBN:9781259822674
Author:Yunus A. Cengel Dr., Michael A. Boles
Publisher:McGraw-Hill Education
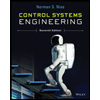
Control Systems Engineering
Mechanical Engineering
ISBN:9781118170519
Author:Norman S. Nise
Publisher:WILEY
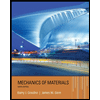
Mechanics of Materials (MindTap Course List)
Mechanical Engineering
ISBN:9781337093347
Author:Barry J. Goodno, James M. Gere
Publisher:Cengage Learning
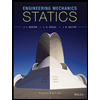
Engineering Mechanics: Statics
Mechanical Engineering
ISBN:9781118807330
Author:James L. Meriam, L. G. Kraige, J. N. Bolton
Publisher:WILEY
Related Questions
- Problem 7: A small ball bearing is released from rest in a tank of oil at t = 0. The downward acceleration of the ball bearing is g - kv, where g is the constant acceleration due to gravity, k is a constant that depends on the viscosity of the oil, and is the downward velocity of the object. Derive expressions for the velocity and the displacement y as function of the time t after the ball bearing's release. Ans (partial): v = g(1 - e-kt)/karrow_forwardCHAPTER 5 : DIESEL ENGINE POWER PLANT A six cylinder, four-stroke CI engine is tested against a water brake dynamometer for which B.P = WN/17x10' in kW, where W is the brake load in newton and N is the speed of the engine in the r.p.m. The air consumption was measured by means of a sharp edged orifice. During the test following observersations were taken : • Bore • Stroke • Speed • Brake load Barometer reading = 10 cm = 14 cm = 2500 rpm = 480 N = 76 cm Hg • Orifice diameter • Co-efficient of discharge of orifice • Pressure drop across orifice • Room temperature Fuel Consumption = 3.3 cm = 0.62 = 14 cm of Hg = 25°C = 0.32 kg/min Calculate following : i. The volumetric efficiency The brake mean effective pressure ( b.m.e.p) The engine torque The brake specific fuel consumption ( b.s.f.c ) ii. iv.arrow_forwardPressurized eyes Our eyes need a certain amount of internal pressure in order to work properly, with the normal range being between 10 and 20 mm of mercury. The pressure is determined by a balance between the fluid entering and leaving the eye. If the pressure is above the normal level, damage may occur to the optic nerve where it leaves the eye, leading to a loss of the visual field termed glaucoma. Measurement of the pressure within the eye can be done by several different noninvasive types of instruments, all of which measure the slight deformation of the eyeball when a force is put on it. Some methods use a physical probe that makes contact with the front of the eye, applies a known force, and measures the deformation. One non-contact method uses a calibrated “puff” of air that is blown against the eye. The stagnation pressure resulting from the air blowing against the eyeball causes a slight deformation, the magnitude of which is correlated with the pressure within the eyeball.…arrow_forward
- Instrumentation & Measurements This homework measures your capability to design/analyze various components/variables of ameasurement system based on what you have studied. Question is Attached in image. Thank you.arrow_forwardProblems Chapter 17 of "Physics for Scientists and Engineers", 10th ed. by Serway and Jewet. Two sound waves arrive at your ear simultaneously; they have slightly different frequencies: wi and w2 and equal amplitudes. You hear the loudness oscillate sinusoidally; this is what we refer to as "beats". Show that the total sound wave has the the form: P(t) = Patm + 28P cos((w1 - w2)/2) cos((w1 + w2)/2). (1) e, bimagination Cosl lWi-We) + Cos/ (W,+We)+ Real puth Releiter Reterort ot above expussion Real purts Coslwit) + Cos (We t)arrow_forwardIs this Correct?arrow_forward
- Kindly solve this problem with complete solution so that I can Understand. Correct Final answer: 1400 or 1.4x10^3arrow_forwardInstrumentation & Measurements This homework measures your capability to design/analyze various components/variables of ameasurement system based on what you have studied. Question 1 Attached.arrow_forward3. Microfluidic channels will need to be fabricated on a key micro-scale sensor used by aerospace industries. Before running machining tests and analyzing machined quality, preliminary efforts are needed to evaluate selected materials and factors affecting machining process¹. Three material candidates have been selected, including 422SS (stainless steel), IN718 (nickel alloy), and Ti64 (titanium alloy) with their measured tensile properties and equation of true stress-true strain relationship used listed below. Tref25°C. Specifically, three factors will need to be evaluated, including different materials, temperature, and size effect. Please calculate true stress values for true strain ranging between 0-3 for each case listed below. Material A (MPa) & (S-¹) Tm (°C) 870 0.01 1520 422SS (Peyre et al., 2007) IN718 (Kobayashi et al., 2008) Ti64 (Umbrello, 2008) 980 1 1300 782.7 1E-5 1660 Material 422SS (CINDAS, 2011) IN718 (Davis, 1997) Ti64 (Fukuhara and Sanpei, 1993) 0 = X G (GPa) 1+ B…arrow_forward
- https://pubmed.ncbi.nlm.nih.gov/32521345/ In the literature review, they should present the system installed and the main results obtained. In other words, the enhancement due to the installed system. They have to define the system used in this study. (the report talking about ventilation) pls in briefly Don’t using chatgpt please urgent i will give u likearrow_forwardsolve manuallyarrow_forwardA used battery was brought to the workshop and the technician noticed that it had 1 litre of distilled water in it but was fully discharged. The specs sheet for this type of battery states that it is fully charged when the change in distilled water to the change in charge equals to the difference between twice the amount of charge and the actual amount of distilled water existing in the battery For the used battery, derive the differential equation and state the initial condition for the range x= 0(0.2)1.0, then obtain a numerical solution for this equation using Euler’s method.arrow_forward
arrow_back_ios
SEE MORE QUESTIONS
arrow_forward_ios
Recommended textbooks for you
- Elements Of ElectromagneticsMechanical EngineeringISBN:9780190698614Author:Sadiku, Matthew N. O.Publisher:Oxford University PressMechanics of Materials (10th Edition)Mechanical EngineeringISBN:9780134319650Author:Russell C. HibbelerPublisher:PEARSONThermodynamics: An Engineering ApproachMechanical EngineeringISBN:9781259822674Author:Yunus A. Cengel Dr., Michael A. BolesPublisher:McGraw-Hill Education
- Control Systems EngineeringMechanical EngineeringISBN:9781118170519Author:Norman S. NisePublisher:WILEYMechanics of Materials (MindTap Course List)Mechanical EngineeringISBN:9781337093347Author:Barry J. Goodno, James M. GerePublisher:Cengage LearningEngineering Mechanics: StaticsMechanical EngineeringISBN:9781118807330Author:James L. Meriam, L. G. Kraige, J. N. BoltonPublisher:WILEY
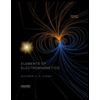
Elements Of Electromagnetics
Mechanical Engineering
ISBN:9780190698614
Author:Sadiku, Matthew N. O.
Publisher:Oxford University Press
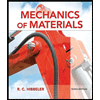
Mechanics of Materials (10th Edition)
Mechanical Engineering
ISBN:9780134319650
Author:Russell C. Hibbeler
Publisher:PEARSON
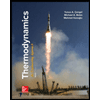
Thermodynamics: An Engineering Approach
Mechanical Engineering
ISBN:9781259822674
Author:Yunus A. Cengel Dr., Michael A. Boles
Publisher:McGraw-Hill Education
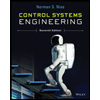
Control Systems Engineering
Mechanical Engineering
ISBN:9781118170519
Author:Norman S. Nise
Publisher:WILEY
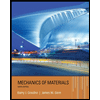
Mechanics of Materials (MindTap Course List)
Mechanical Engineering
ISBN:9781337093347
Author:Barry J. Goodno, James M. Gere
Publisher:Cengage Learning
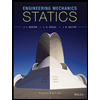
Engineering Mechanics: Statics
Mechanical Engineering
ISBN:9781118807330
Author:James L. Meriam, L. G. Kraige, J. N. Bolton
Publisher:WILEY