Lab4
pdf
keyboard_arrow_up
School
University of Central Oklahoma *
*We aren’t endorsed by this school
Course
2143
Subject
Mechanical Engineering
Date
Dec 6, 2023
Type
Pages
11
Uploaded by HighnessScorpionMaster539
University of Central Oklahoma
Fracture Test - Experiment 4
Dylan Robinson, Joshua Jackson, and Kaleb Paddock Dr. Adnan Al-Ibadi
Thursday 1:00 PM
10/20/22
Abstract
Experiment 4 for the Strength of Materials laboratory covers a fracture test.[1] In this experiment, the slender column specimen is loaded into the testing apparatus (Universal Testing Machine or ZPM) and an axial force is applied to the specimen. In this particular experiment, we are asked to calculate a theoretical value for the fracture toughness that a brittle material can withstand, and then compare the experimental value with a finite element model.[2]
Theory
Equations associated with this experiment are located in the appendix. In aerospace sustainability engineering, structural members in aircraft develop internal stresses throughout their lifespan. Over time these members may develop small fractures, reducing the yield stress of the material. If left unabated, these members may fail. Engineers must use a variety of methods to discover these fractures. The inspection of structural members without disassembling a system oftentimes is the only viable method of determining the true condition of a metal. This type of inspection is called non-destructive inspecting or NDI. The most common type of NDI is a visual test method, where an engineer or technician visually determines the state of the material. Of course this method is least effective. Although there are many methods to perform this type of inspection, one of the most effective for fracture failures specifically, is crack testing with a liquid penetrant. In this test, a spray is applied to a test area that makes fractures more apparent. This test
s’ effectiveness is determined by the experience of the inspector.
These types of tests are also utilized in other fields of engineering, most notably civil engineering. Here engineers might use these methods to see if a structural design is meeting the outlined constraints throughout the lifespan of the structure.[3]
Machines and Instruments
‘Figure 2’ shows the main machine used in this experiment. This machine applies an accurate and measured force onto our test specimen, as well as measures the displacement of the specimen due to the force applied. This ZPM is different from the standard equipment and is the same test stand utilized in the previous experiment, the Tension Test. Using this information, we are able to test our theoretical value for the critical force applied before the specimen that will cause it to break, or more specifically fracture.
Experimental Method
In this experiment, we rely heavily on the concepts of stress, strain, modulus of elasticity, and a few other key concepts specific to strength of materials. In this particular experiment, we employ some of the concepts
associated with determining the critical stress intensity factor, Kc. The critical stress intensity factor of materials has a multitude of applications in the engineering world, as one could imagine. Using the ZPM universal testing machine, and an acrylic test specimen, as well as some provided equations, we are able to calculate values for our fracture toughness.
Figure 1: CT Test Specimen Diagram.
Test Procedure
For this experiment, our acrylic test specimen is loaded into the ZPM universal testing machine. The specimen is secured via three dowels as per the diagram above in figure 1, and shown below in figure 2. After the specimen is secured and the ZPM is calibrated, we begin applying force pulling the specimen apart. The displacement and the applied force is recorded to be employed in our equations for calculating the fracture toughness.
Your preview ends here
Eager to read complete document? Join bartleby learn and gain access to the full version
- Access to all documents
- Unlimited textbook solutions
- 24/7 expert homework help
Figure 2: Acrylic test specimen loaded into the ZPM.
Specimen Specifications
In this experiment, we are performing a critical fracture test on an acrylic specimen. The specimen used was one of the compact tension specimen (CT) variety. In accordance with ASTM standard No. E399, the CT specimen is loaded into the ZPM universal testing machine and connected to it via a couple of dowel pins. The precise dimensions needed for the calculations included in our appendix section are listed below in table 1, and the figure below depicts the specimen loaded into the universal testing machine.
Table 1: Specimen Dimensions
Results
With the results from the ZPM aggregated in combination with the equation listed below, the value of fracture toughness is able to be calculated. The main equation employed to calculate the fracture toughness is:
EQ. 1:Kic=(Pmax)(f)/(B)(W0.5)
Here, ‘Pmax’ is the maximum load applied to the specimen before it breaks, ‘f’ is the shape factor for the crack, ‘B’ is the thickness of the specimen, and ‘W’ is the width. With the data from the ZPM provided (shown below in figure 3) we can calculate a value for our fracture toughness. The ZPM gave a lot of values for a lot of increments, so for the sake of saving space, we will only include the portion that gives us our maximum load applied. Figure 3: Table of Values from ZPM universal testing machine.
From the table listed above, we are able to see that the maximum applied load before the specimen broke was of value 261.745 N. As shown in our appendix section, we have a value of Kic being equal to 4102974.4. Figure 4 shows the acrylic specimen fractured.
Your preview ends here
Eager to read complete document? Join bartleby learn and gain access to the full version
- Access to all documents
- Unlimited textbook solutions
- 24/7 expert homework help
Figure 4: Specimen after testing in ZPM.
Validation and Discussion Given the data shown above in Figure 3, we were able to calculate the fracture toughness (Kic) from the maximum load value. This calculation is shown below in the appendix section. The maximum load value used for the calculation was 261.745 N. This value gave the specimen a fracture toughness of 4102974.4 Pa/m or 4.103 MPa/m.
Conclusion This test is important for understanding a material’
s characteristics. The methods shown in this experiment are the same methods used when determining which materials to use when building aircraft, automobiles, and building structures. This test allows engineers to obtain precise measurements while keeping parts cost low due to the small specimen size. In using these testing methods engineers are able to predict a material
’
s performance characteristics with a high degree of certainty.
References
[1] Khandaker, M. (2021). Laboratory Manual for Strength of Materials Lab. Department of Engineering and Physics (UCO)
[2] Hibbeler, R. C. Mechanics of Materials
. Pearson, 2022. [3] The 6 Most Important Methods for Crack Testing in Non-Destructive ...
https://blog.foerstergroup.com/en/component-testing/the-6-most-important-methods-for-
crack-testing-in-non-destructive-material-testing.
Your preview ends here
Eager to read complete document? Join bartleby learn and gain access to the full version
- Access to all documents
- Unlimited textbook solutions
- 24/7 expert homework help
Appendix
Related Questions
You have been given the following test sample data following mechanical testing of 15
test pieces of a modified Alumina.
What is the Weibull modulus of this material?
Would you advise the use of this material over one with a Weibull Modulus of 19.6 and a
mean failure stress of 270 MPa, if you anticipate that the peak stress on the material
could be 255 MPa?
Sample
1
2
3
4
5
6
7
8
9
10
11
12
13
14
15
Select one or more:
a. 185
b. No
Yes
□d. 49
□e. 28.6
3.7
Failure Stress (MPa)
297
293
270
300
g. 22.8
260
296
265
295
280
288
263
290
298
275
arrow_forward
Flag question
You have been given the following test sample data following mechanical testing of 15 test pieces of a modified Alumina.
What is the Weibull modulus of this material?
Would you advise the use of this material over one with a Weibull Modulus of 19.6 and a mean failure stress of 270 MPa, if you
anticipate that the peak stress on the material could be 255 MPa?
Sample
1
2
3
4
5
6
7
8
9
10
11
12
13
14
15
Select one or more:
Failure Stress (MPa)
297
293
270
300
260
286
265
295
4
293
280
288
263
290
298
275
arrow_forward
1. For the stress-strain curve shown below, please estimate the properties indicated.
(a) Fracture Strain
Please do your work on a separate sheet of paper,
and put your answers in the boxes on the right.
Be sure to include the proper symbol and units.
Stress Strain
70
60
50
Stress (ksi)
240
30
20
10
70
0
0.000
60
50
Stress (ksi)
40
20
10
KULL
0
0.000
0.010
0.050
0.100
Strain (in/in)
Stress Strain
0.020 0.030
Strain (in/in)
0.040
0.150
0.050
(b) Ultimate Tensile Stress
(c) Fracture Stress
(d) Proportional Limit
(e) Elastic Modulus
(1) Yield Stress
(g) Tensile Toughness
(Modulus of Toughness)
(h) Modulus of Resilience
arrow_forward
I need the answer as soon as possible
arrow_forward
Question 1
You are working on a design team at a small orthopaedic firm. You have been asked to select a cobalt-
chrome-molybdenum (CoCr) material that will not experience plastic deformation under a specific mechanical test, as follows...
A tensile stress is applied along the long axis of a solid cylindrical rod that has a diameter of 10 mm. An applied load of some
magnitude F produces a 7x10-³ mm change in diameter (see figure below, original shape is blue, elongated shape is unshaded).
Q1E: Of those two materials (F75 CoCr alloy (as cast) and F90 CoCr alloy (hot forged)), which materials would you select to assure
that the deformation is entirely elastic (No yield!)?
arrow_forward
Question 1
You are working on a design team at a small orthopaedic firm. You have been asked to select a cobalt-
chrome-molybdenum (CoCr) material that will not experience plastic deformation under a specific mechanical test, as follows...
A tensile stress is applied along the long axis of a solid cylindrical rod that has a diameter of 10 mm. An applied load of some
magnitude F produces a 7x10-³ mm change in diameter (see figure below, original shape is blue, elongated shape is unshaded).
Q1G: If your design required using the new material to create a wire, what is the largest diameter that would lead to ductile
behavior while still avoiding plastic deformation when exposed to the above loading conditions?
arrow_forward
please solve part b, this is past paper and just iam studying, mechanical engineering
arrow_forward
Figure 1 shows the tensile testing results for different materials. All specimens have an initial
diameter of 12 mm and an initial gauge length of 50 mm.
300
250
Low carbon steel
Network polymer
200
Crystalline polymer
150
Amorphous polymer
100
50
5
10
15
20
25
30
Strain (%)
Figure 1: Stress-strain curve
b. Determine the following parameters for each material:
• the tensile strength
the 0.2% offset yield strength
the modulus of elasticity
• the ductility
Stress (MPa)
LO
arrow_forward
Question 1
You are working on a design team at a small orthopaedic firm. You have been asked to select a cobalt-
chrome-molybdenum (CoCr) material that will not experience plastic deformation under a specific mechanical test, as follows...
A tensile stress is applied along the long axis of a solid cylindrical rod that has a diameter of 10 mm. An applied load of some
magnitude F produces a 7x10³ mm change in diameter (see figure below, original shape is blue, elongated shape is unshaded).
Q1H: Provide a brief rationale based on calculations used to support your answer. That is, how would you explain the behavior of
the "new alloy" material to your design team?
Table of properties: Assume Poisson's ratio is 0.3 for all materials
Process
Elastic Modulus (GPa)
Material
CoCr F75
As cast/Annealed
210
CoCr F90
Hot forged
New alloy
Z
X
↑ F
df
O
210
110
Yield Strength (MPa)
450-517
900-1200
600
Tensile Strength (MPa)
655-890
1400-1600
700
arrow_forward
Question 1
You are working on a design team at a small orthopaedic firm. You have been asked to select a cobalt-
chrome-molybdenum (CoCr) material that will not experience plastic deformation under a specific mechanical test, as follows...
A tensile stress is applied along the long axis of a solid cylindrical rod that has a diameter of 10 mm. An applied load of some
magnitude F produces a 7x10³ mm change in diameter (see figure below, original shape is blue, elongated shape is unshaded).
Q1C-D: Using the table of material properties below, calculate the magnitude of stress (o) and applied load (F) required to produce
the 7x10-³ mm change in diameter for rods fabricated from F75 CoCr alloy (as cast) and F90 CoCr alloy (hot forged) materials.
arrow_forward
I just can't find The percent elongation at fracture.
arrow_forward
How did temperature affect the toughness of the specimens?
arrow_forward
Hello Good Evening Sir,I have a question in my homework related structural statics lesson. The following below is my question. Please advice. Thank you so much
Regards,Irfan
arrow_forward
Question 2
Figure 2 shows the dependence of fatigue strength on testing cycles (S-N curve) of an acetal
polymer.
60
50
40
30
20
10
104
105
106
107
108
Number of cycles to failure
Figure 2 The S-N fatigue curve for an acetal polymer
a. What is the fatigue strength, or maximum stress amplitude, at one million cycles of
loading?
b. An acetal polymer 30-cm-long bar with a diameter of 20 mm is designed to survive
one million cycles of loading, what is the maximum allowable axial load that can be
applied on one end of the bar?
Magnitude of stress
Reversal, MPa
arrow_forward
SEE MORE QUESTIONS
Recommended textbooks for you
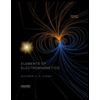
Elements Of Electromagnetics
Mechanical Engineering
ISBN:9780190698614
Author:Sadiku, Matthew N. O.
Publisher:Oxford University Press
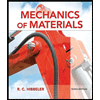
Mechanics of Materials (10th Edition)
Mechanical Engineering
ISBN:9780134319650
Author:Russell C. Hibbeler
Publisher:PEARSON
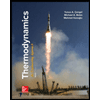
Thermodynamics: An Engineering Approach
Mechanical Engineering
ISBN:9781259822674
Author:Yunus A. Cengel Dr., Michael A. Boles
Publisher:McGraw-Hill Education
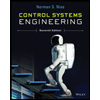
Control Systems Engineering
Mechanical Engineering
ISBN:9781118170519
Author:Norman S. Nise
Publisher:WILEY
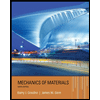
Mechanics of Materials (MindTap Course List)
Mechanical Engineering
ISBN:9781337093347
Author:Barry J. Goodno, James M. Gere
Publisher:Cengage Learning
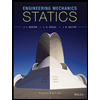
Engineering Mechanics: Statics
Mechanical Engineering
ISBN:9781118807330
Author:James L. Meriam, L. G. Kraige, J. N. Bolton
Publisher:WILEY
Related Questions
- You have been given the following test sample data following mechanical testing of 15 test pieces of a modified Alumina. What is the Weibull modulus of this material? Would you advise the use of this material over one with a Weibull Modulus of 19.6 and a mean failure stress of 270 MPa, if you anticipate that the peak stress on the material could be 255 MPa? Sample 1 2 3 4 5 6 7 8 9 10 11 12 13 14 15 Select one or more: a. 185 b. No Yes □d. 49 □e. 28.6 3.7 Failure Stress (MPa) 297 293 270 300 g. 22.8 260 296 265 295 280 288 263 290 298 275arrow_forwardFlag question You have been given the following test sample data following mechanical testing of 15 test pieces of a modified Alumina. What is the Weibull modulus of this material? Would you advise the use of this material over one with a Weibull Modulus of 19.6 and a mean failure stress of 270 MPa, if you anticipate that the peak stress on the material could be 255 MPa? Sample 1 2 3 4 5 6 7 8 9 10 11 12 13 14 15 Select one or more: Failure Stress (MPa) 297 293 270 300 260 286 265 295 4 293 280 288 263 290 298 275arrow_forward1. For the stress-strain curve shown below, please estimate the properties indicated. (a) Fracture Strain Please do your work on a separate sheet of paper, and put your answers in the boxes on the right. Be sure to include the proper symbol and units. Stress Strain 70 60 50 Stress (ksi) 240 30 20 10 70 0 0.000 60 50 Stress (ksi) 40 20 10 KULL 0 0.000 0.010 0.050 0.100 Strain (in/in) Stress Strain 0.020 0.030 Strain (in/in) 0.040 0.150 0.050 (b) Ultimate Tensile Stress (c) Fracture Stress (d) Proportional Limit (e) Elastic Modulus (1) Yield Stress (g) Tensile Toughness (Modulus of Toughness) (h) Modulus of Resiliencearrow_forward
- I need the answer as soon as possiblearrow_forwardQuestion 1 You are working on a design team at a small orthopaedic firm. You have been asked to select a cobalt- chrome-molybdenum (CoCr) material that will not experience plastic deformation under a specific mechanical test, as follows... A tensile stress is applied along the long axis of a solid cylindrical rod that has a diameter of 10 mm. An applied load of some magnitude F produces a 7x10-³ mm change in diameter (see figure below, original shape is blue, elongated shape is unshaded). Q1E: Of those two materials (F75 CoCr alloy (as cast) and F90 CoCr alloy (hot forged)), which materials would you select to assure that the deformation is entirely elastic (No yield!)?arrow_forwardQuestion 1 You are working on a design team at a small orthopaedic firm. You have been asked to select a cobalt- chrome-molybdenum (CoCr) material that will not experience plastic deformation under a specific mechanical test, as follows... A tensile stress is applied along the long axis of a solid cylindrical rod that has a diameter of 10 mm. An applied load of some magnitude F produces a 7x10-³ mm change in diameter (see figure below, original shape is blue, elongated shape is unshaded). Q1G: If your design required using the new material to create a wire, what is the largest diameter that would lead to ductile behavior while still avoiding plastic deformation when exposed to the above loading conditions?arrow_forward
- please solve part b, this is past paper and just iam studying, mechanical engineeringarrow_forwardFigure 1 shows the tensile testing results for different materials. All specimens have an initial diameter of 12 mm and an initial gauge length of 50 mm. 300 250 Low carbon steel Network polymer 200 Crystalline polymer 150 Amorphous polymer 100 50 5 10 15 20 25 30 Strain (%) Figure 1: Stress-strain curve b. Determine the following parameters for each material: • the tensile strength the 0.2% offset yield strength the modulus of elasticity • the ductility Stress (MPa) LOarrow_forwardQuestion 1 You are working on a design team at a small orthopaedic firm. You have been asked to select a cobalt- chrome-molybdenum (CoCr) material that will not experience plastic deformation under a specific mechanical test, as follows... A tensile stress is applied along the long axis of a solid cylindrical rod that has a diameter of 10 mm. An applied load of some magnitude F produces a 7x10³ mm change in diameter (see figure below, original shape is blue, elongated shape is unshaded). Q1H: Provide a brief rationale based on calculations used to support your answer. That is, how would you explain the behavior of the "new alloy" material to your design team? Table of properties: Assume Poisson's ratio is 0.3 for all materials Process Elastic Modulus (GPa) Material CoCr F75 As cast/Annealed 210 CoCr F90 Hot forged New alloy Z X ↑ F df O 210 110 Yield Strength (MPa) 450-517 900-1200 600 Tensile Strength (MPa) 655-890 1400-1600 700arrow_forward
- Question 1 You are working on a design team at a small orthopaedic firm. You have been asked to select a cobalt- chrome-molybdenum (CoCr) material that will not experience plastic deformation under a specific mechanical test, as follows... A tensile stress is applied along the long axis of a solid cylindrical rod that has a diameter of 10 mm. An applied load of some magnitude F produces a 7x10³ mm change in diameter (see figure below, original shape is blue, elongated shape is unshaded). Q1C-D: Using the table of material properties below, calculate the magnitude of stress (o) and applied load (F) required to produce the 7x10-³ mm change in diameter for rods fabricated from F75 CoCr alloy (as cast) and F90 CoCr alloy (hot forged) materials.arrow_forwardI just can't find The percent elongation at fracture.arrow_forwardHow did temperature affect the toughness of the specimens?arrow_forward
arrow_back_ios
SEE MORE QUESTIONS
arrow_forward_ios
Recommended textbooks for you
- Elements Of ElectromagneticsMechanical EngineeringISBN:9780190698614Author:Sadiku, Matthew N. O.Publisher:Oxford University PressMechanics of Materials (10th Edition)Mechanical EngineeringISBN:9780134319650Author:Russell C. HibbelerPublisher:PEARSONThermodynamics: An Engineering ApproachMechanical EngineeringISBN:9781259822674Author:Yunus A. Cengel Dr., Michael A. BolesPublisher:McGraw-Hill Education
- Control Systems EngineeringMechanical EngineeringISBN:9781118170519Author:Norman S. NisePublisher:WILEYMechanics of Materials (MindTap Course List)Mechanical EngineeringISBN:9781337093347Author:Barry J. Goodno, James M. GerePublisher:Cengage LearningEngineering Mechanics: StaticsMechanical EngineeringISBN:9781118807330Author:James L. Meriam, L. G. Kraige, J. N. BoltonPublisher:WILEY
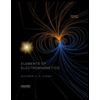
Elements Of Electromagnetics
Mechanical Engineering
ISBN:9780190698614
Author:Sadiku, Matthew N. O.
Publisher:Oxford University Press
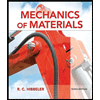
Mechanics of Materials (10th Edition)
Mechanical Engineering
ISBN:9780134319650
Author:Russell C. Hibbeler
Publisher:PEARSON
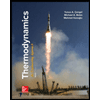
Thermodynamics: An Engineering Approach
Mechanical Engineering
ISBN:9781259822674
Author:Yunus A. Cengel Dr., Michael A. Boles
Publisher:McGraw-Hill Education
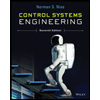
Control Systems Engineering
Mechanical Engineering
ISBN:9781118170519
Author:Norman S. Nise
Publisher:WILEY
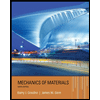
Mechanics of Materials (MindTap Course List)
Mechanical Engineering
ISBN:9781337093347
Author:Barry J. Goodno, James M. Gere
Publisher:Cengage Learning
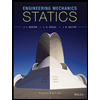
Engineering Mechanics: Statics
Mechanical Engineering
ISBN:9781118807330
Author:James L. Meriam, L. G. Kraige, J. N. Bolton
Publisher:WILEY