CM 3502 Exam Notes
docx
keyboard_arrow_up
School
Louisiana State University *
*We aren’t endorsed by this school
Course
3502
Subject
Mechanical Engineering
Date
Dec 6, 2023
Type
docx
Pages
30
Uploaded by CommodoreRam830
CM 3502 Cheat Sheet
CM 3502 Cheat Sheet
How many lives were lost in the Teton Dam Failure? 14
CM 3502 Cheat Sheet
When considered over long periods of time, operations and maintenance costs, ____________ the initial cost of construction of a typical building. Exceed
A material that experiences large deformation before failure
is called Ductile
A
material that fails with very little deformation is called Brittle
Precision refers to the variability of repeat measurements under carefully controlled conditions.
Accuracy is the conformity of results to the true value or the absence of bias.
The ________________ rating system is used to evaluate the sustainability of a project. LEED
The _________________ is a measure of the dispersion or spread of the results. Standard deviation
Stress and Strain
Strain is a physical change in the size or shape of the material. Total strain refers to the total change in size due to a load, its units are any dimensional units, inches, feet, meters, millimeters. Unit strain is the change per unit length, this variable is unitless, it is a ratio but is often represented as inches per inch for clarity. Axial strain is a strain in the direction along a linear member or perpendicular to the cross-section. Tensile strain results in a lengthening of the member, compressive strain, such as in a column, is a shortening or contraction of the member. Shear Stress is stress across a linear member or parallel to the cross-section. Shear strain can be visualized in the previous bolt example or by thinking of the opposing forces at
the edge of the support of a beam, with the support acting upward and the beam acting downward.
Your preview ends here
Eager to read complete document? Join bartleby learn and gain access to the full version
- Access to all documents
- Unlimited textbook solutions
- 24/7 expert homework help
CM 3502 Cheat Sheet
Bending strain is strain due to bending forces, this strain results in the vertical deflection of a horizontal beam. Horizontal shearing strain is due to shear stress from beam loads, it also contributes to beam deflection.
Axial Strain Example
A linear member 33.3 feet long elongates by 2 inches due to a tensile load. Determine the unit strain. Total change equals unit strain times the original length, or unit strain equals total change divided by the original length. Unit strain equals 2 inches divided by 33.3 feet, however, we must have matching units, so we will multiply by 12 inches per 1 foot. Unit strain equals .005.
Example
A linear member 33.3 ft long elongates by 2 inches due to a tensile load
Determine the unit strain, ε
δ = εL
O → ε = δ/L
O
δ = Total Strain, Lengthening or Shortening, in, ft, m
ε = Unit Strain in/in, ft/ft, m/m, unitless
L
O = Original Length, in, ft, m
ε = δ/L
O = 2in/(33.3ft x (12in/1ft))
ε = .005 in/in → ε = .005
Stress-Strain diagram
The following graph shows a typical stress strain diagram for mild steel in tension. Stress strain diagrams exist for multiple materials and all types of stress. The first part of the diagram is the elastic range. A material stressed within this range will return to its original size and shape when the load is removed. The stress at the end
CM 3502 Cheat Sheet
of the elastic range is called the yield stress, a material stressed beyond this point will deform or yield. When we go beyond the elastic range into the plastic range a material will experience permanent deformation. Next is the strain hardening range where material becomes stronger, up to the point of Fu, the ultimate stress. The final section is the failure range, in this range, the material weakens until the failure point, with x denoting the failure point.
Modulus of Elasticity(Young’s Modulus)
The measure of the stiffness of the material is the modulus of elasticity or Young’s modulus. It is represented by E and has units similar to stress, pounds per inch square, kips per inch square, kilopascals, megapascals. The modulus of elasticity defines the relationship between stress and strain, it is the material factor in deformation and deflection calculations. It defines the stiffness of the material, not
CM 3502 Cheat Sheet
the strength. The modulus of elasticity is the change in stress divided by the change
in unit strain within the elastic range of material.
Modulus of Elasticity(Young’s Modulus), E, lbs/in
2
, k/in
2
, kPa, MPa
Modulus of Elasticity defines the relationship between stress and strain
Material Factor in deformation and deflection calculations
Defines the Stiffness, not the strength of a material
E = Δf/Δε
Valid within a materials elastic range
Some materials have nonlinear behavior, we can however estimate a modulus of elasticity within the working range of that material.
E = Δf/Δε
Below is an example problem using test data to determine the modulus of elasticity.
Test data from within the elastic range of an unknown material is given. Data point 1, stress equals 7400 pounds per inch square, unit strain equals .00025. Data point 2, stress equals 22,200 pounds per inch square, unit strain equals .00075. Determine the modulus of elasticity. The modulus of elasticity equals the change in stress divided by the change in unit strain, the modulus of elasticity equals 22,200 pounds per inch square -7400 pounds per inch square divided by .00075-.00025. Modulus of elasticity equals 29.6×10 to the 6th pounds per inch square. Referring to
appendix E we see that this material may be steel. The typical value for the modulus of elasticity of steel that we will use in all our calculations is 29×10 to the 6th pounds per inch square or 29×10 to the third, kips per inch square.
Example
Test data from within the elastic range of an unknown material is given.
Data point 1: f = 7400 lbs/in
2
, ε = .00025
Data point 2: f = 22,200 lbs/in
2
, ε = .00075
Determine the Modulus of Elasticity
E = Δf/Δε
E = (22,200 lbs/in
2
- 7400 lbs/in
2
)/(.00075 - .00025)
E = 29.6(10)
6
lbs/in
2
Refer to Appendix E to determine what material this may be
E
STEEL
= 29(10)
6
lbs/in
2
or 29(10)
3
k/in
2
Your preview ends here
Eager to read complete document? Join bartleby learn and gain access to the full version
- Access to all documents
- Unlimited textbook solutions
- 24/7 expert homework help
CM 3502 Cheat Sheet
Stiffness and Strength
The strength of a material is that materials highest stress in testing. We can have multiple values for the strength of the material. We have the yield stress, labeled F subscript y, which is the stress at which permanent deformation begins. The ultimate stress, labeled F subscript u, is the maximum stress that the material can resist. Notations for stress include both f and F, f denotes a calculated value from actual loading conditions, F denotes a reference or allowable value. Stiffness, on the
other hand, is the slope of the stress strain curve or a measure of the rate of deformation due to stress.
Strength of a material is that material’s highest stress in testing
F
y
– Yield Stress
F
u
– Ultimate Stress
ƒ – denotes a calculated value from actual loading conditions
F – denotes a reference or allowable value
Materials
Need for Quality Materials
Materials are used in a vast range of applications in the construction industry. Here is a simple comparison of different material needs for different applications. These are just a few of the many considerations that go into deciding which materials are used.
Comparison of different material needs for different applications
Roof
Basement
Lightweight
Waterproof
Reflective to thermal load
Strong enough to carry snow load
Insulate against
noise and heat
Weight not important
Waterproof against ground water
Strong enough to resist soil settlement
Resist corrosion
CM 3502 Cheat Sheet
Construction Materials
This course will provide practical insight into the fundamentals involved in designing, evaluating, testing, and construction using:
Aggregates and Soils
Asphalt
Concrete
Masonry
Wood
Steel
Failure and Damage
The Leaning Tower of Pisa (Italy) – 1173
Leaning Tower of Pisa is a medieval structure located in Pisa, Italy, that is famous for
the settling of its foundation which caused it to lean about 15 feet from the perpendicular by the late 20th century. When the leaning tower of Pisa was built, little was known of soil exploration or soil strength. Buildings were typically built based on prior experience. Those prior references were not always valid because soil conditions and soil strengths vary widely even within a small area. Soil is a material that is used on almost all construction jobs, but the layperson often does not think of it as a material. The Leaning Tower of Pisa has tilted in several directions until leaning to the south. A weak clay layer exists at 11m depth from the surface.
Landslides
When a mass of rock, debris, or earth slides down a slope, it is called a landslide. The term "landslide" refers to any downward movement of soil and rock under the influence of gravity. A slope's natural stability is disturbed by landslides. Landslides can accompany heavy rains or follow droughts, earthquakes, or volcanic eruptions. Mudslides occur when water rapidly accumulates in the ground and causes a surge of wet rock, earth, and debris. Landslides can happen due to:
Inadequate slope stability
Erosion by water
Vibrations by traffic and blasting
Excess load by structure and rocks
Teton Dam
CM 3502 Cheat Sheet
The Teton Dam was an earthen dam on the Teton River in Idaho
, United States. It was built by the Bureau of Reclamation, one of eight federal agencies authorized to construct dams.
Dam Failure – 1976
The Teton Dam Failure is built on the Teton River, Idaho, in 1975. It is designed to provide flood control, power generation, and irrigation of farmland. This large earthen dam has a reservoir capacity of 356 million cubic meters. The dam failed suddenly killing 14 people and causing more than $1 billion in damage. The reasons
for failure were based on a combination of geological factors
Those factors include:
Poor compaction of the fill material at less than the optimum moisture content causing:
Erosion channels (Piping)
Highly erodible silts
Highly permeable volcanic rocks
Selection of Materials
Much of this course is dedicated to the study of mechanical properties of materials along with non-mechanical properties of materials. We will also look at economic factors, aesthetic factors, and the production and use of those materials in construction.
Some materials may have a lower cost initially, but the upkeep and maintenance may cause that material to be a more costly choice when considered over the entire
life of a structure.
Analysis of the problem:
Performance required
Useful life required
Allowable cost
Maintenance expense
Your preview ends here
Eager to read complete document? Join bartleby learn and gain access to the full version
- Access to all documents
- Unlimited textbook solutions
- 24/7 expert homework help
CM 3502 Cheat Sheet
Design of selected material:
Size, shape, finish, and method of construction
When considered over long periods of time, operations and maintenance costs, outweigh by far, the initial cost of construction.
Life Cycle Cost of Buildings
5-10% Design and construction “first costs”
60-80% Operations and maintenance
5-35% Land acquisition, conceptual planning, renewal or revitalization, and disposal
Materials
Choosing Materials
The following provides a list of things to consider when choosing materials.
Environmental Impact
Durability
End of Life
Materials Use in Construction
Keep in mind that this chart indicates the use of materials in construction, not all uses of those materials. An interesting point is the sharp drop in the usage of aluminum and the start of the usage of plastic during World War II.
Properties of Materials
The following provides a list of the properties of materials. Each property will be expanded upon in the subsequent pages of the resource book.
Thermal expansion
Thermal conductivity
Strength and stress
Modulus of Elasticity
Elastic and Plastic Properties
CM 3502 Cheat Sheet
Thermal Expansion
Building materials become smaller when cooler and larger when hotter
The amount of expansion and contraction is different with each material type
Described in terms of the coefficient of thermal expansion
Materials may be used together if they have similar thermal characteristics (e.g., steel and concrete)
Coefficient of expansion (α): the increase in length per unit length per degree increase in temperature
Units: in. per in. per °F or cm per cm per °C
To calculate change in length due to temperature variation:
δ = αLΔT
where δ = total change in length (in)
α = linear coefficient of thermal expansion
L = original length
Method of heat propagation:
Convection through air
Conduction through solid (building materials)
Radiation through emission from a surface
Insulation:
A material that can prevent or delay the transmission of heat through any part of the structural frame
Insulating Materials
Insulating materials are rated based on their thermal conductivity expressed in terms of U factor
U-factor
: heat transmitted per square foot of cross-section per hour per oF difference in temperature between the two sides of the material.
The U-factor measures how well a product prevents heat from escaping. The lower the U-factor, the greater the resistance to heat flow and the better its insulating value (0.2 and 1.2)
The reciprocal of the U-factor is the R-value
(thermal resistance)
The R value is what we will typically see when buying insulation.
CM 3502 Cheat Sheet
Thermal Mass
Thermal mass refers to materials that have the capacity to store thermal energy for extended periods. Thermal mass can be used effectively to absorb daytime heat gains (reducing cooling load) and release the heat during the night (reducing heat load).
This can explain why some buildings experience the highest cooling load times of the day, hours after the highest heat of the day.
Stress and Strength
In CM2501 we sometimes used a different symbol for stress. We used the lower-
case italicized f where this slide is using a lower-case Sigma. The lower-case Sigma is used more often. You may recall that we also often used P in place of F.
All construction materials must resist loads:
Dead load (weight of the structural element)
Live load (external load imposed on the structure – e.g., furniture, wind, earthquake, etc.)
Stress is a force applied over an area:
F = force (load) applied in pound (Newton)
A = cross-sectional area in in
2
σ or s = stress (force per unit area), lb/in
2
(psi)
Stress and Strain
Ratio of elongation of a material to the original length
unit deformation
Here unit strain is expressed in units of inches per inch. Unit strain is actually unitless, a ratio, but the notation helps in understanding what is being expressed. Unit strain is how many inches of change we have per inches of length. This value is
typically very small.
Your preview ends here
Eager to read complete document? Join bartleby learn and gain access to the full version
- Access to all documents
- Unlimited textbook solutions
- 24/7 expert homework help
CM 3502 Cheat Sheet
e or δ: elongation or total strain (in or ft)
Lo : (original) length of a material (in or ft)
: unit strain (in/in) or (ft/ft)
Elongation
e = L - L
o
L: loaded length of a material (ft)
Strength
Strength: the largest value of stress a material can resist – Same units as stress (lbs/in2)psi, (kips/in2)ksi, Pa [N/m2], MPa
Fracture (Failure): If the applied stress is increased beyond the strength of the material, failure occurs
Type of loading:
Tensile
Compressive
Shear
The lbs/in
2
and kips/in
2
unit notations are preferred over psi and ksi when used in calculations.
Toughness is the ability of the material to absorb energy while a force is applied to it.
Toughness is the product of stress and strain up to the point of fracture (area under the curve). Impact toughness can be measured by the Charpy test
Charpy test measures energy absorbed by the sample.
All samples will fail.
If a material is brittle, less energy will be absorbed in the materials failure and the hammer will swing farther.
If a material is ductile and tough more energy will be absorbed in breaking the sample and the hammer will not swing as far.
Creep
Development of deformations with time. Materials will have permanent deformation when loaded over long periods of time, although the plastic deformation range on the stress-strain diagram has not been reached. This is called Creep. It happens in most materials but is not always significant. This list goes from more significant to less significance of creep by material. Plastic, Wood, Concrete, Steel.
CM 3502 Cheat Sheet
Fatigue
The repeated application of stress typically produced by an oscillating load such as vibration.
Example: bridge vibration with traffic load or vibration from machinery.
Fatigue failure can occur at stresses well below the static failure stresses.
Iron and Steel
Iron and steel are the most important metals used in construction. All forms of iron and steel are termed ferrous metals:
Finished products delivered to the site (no quality control needed)
Abundant raw materials
Relatively low production cost
Useful range of properties (heat, ductility, etc.)
100% recyclable with no loss of properties
Structure and Composition
You will see later that steel can have very different properties while having the same
chemical makeup. Production methods for steel and heat treatment are very important in determining what properties a steel will have.
Small variations in the content of impurities also cause significant changes in the properties of steel.
Similar to Asphalt Concrete and Portland Cement Concrete, steel is formed from grains that are held together by:
Adhesive strength that comes from atomic bonds
Grains consist of symmetrical patterns of atoms.
Internal atomic structure depends on the rate of cooling during production and content of impurities (carbon, manganese, etc.)
Ferrous Metals
Impurities
Carbon:
Up to 0.9%: increases hardness and tensile strength
Over 0.9%: increases hardness and brittleness
Manganese (0.5 to 2.0%): promotes hardness and uniformity
Silicon (up to 2.5%): same as manganese
Sulfur (up to 0.05%): maintain malleability
CM 3502 Cheat Sheet
Phosphorous (up to 0.05%): increases strength and corrosion resistance
Production
Pure Iron is not found in the earth’s crust. It is mixed with rock or soil (iron ore). The
first step is to produce low-grade iron in a blast furnace:
Load iron ore, coke (coal), and limestone in the furnace
Heat above 1600°C (3000°F) with a strong blast of hot air
◄
Previous:
Iron and Steel
Next:
Blast Furnace
►
Blast Furnace Slag floats to the top of the molten iron. Fluxes can be used to help remove additional impurities. Flux is a material added that bonds with the impurities then floats to the top where they can be separated from the iron. Slag removed from iron is used as an aggregate and in mineral admixtures for concrete. Iron produced from a blast furnace is known as pig iron and is poured into molds.
Pig iron composition is not accurately controlled:
Weak and brittle (4 to 5% carbon)
Rarely used without further processing
Slag floats to the top of the molten iron. Fluxes can be used to help remove additional impurities. A flux is a material added that bonds with the impurities then floats to the top where they can be separated from the iron.
Pig iron may be refined to pure iron. It is rarely used due to its high cost. Pig iron is remelted in small furnaces to produce cast metals and steel.
Molten metal is poured into molds with desired shapes (casting).
Chemical composition is controlled by adding:
Scrap iron and steel
Silicon and manganese
Scrap steel is very important in today’s production of new steel. Using recycled scrap metal in place of virgin iron ore can yield:
75% savings in energy.
86% reduction in air pollution.
76% reduction in water pollution.
90% savings in raw materials used.
40% reduction in water use.
Your preview ends here
Eager to read complete document? Join bartleby learn and gain access to the full version
- Access to all documents
- Unlimited textbook solutions
- 24/7 expert homework help
CM 3502 Cheat Sheet
97% reduction in mining wastes.
Casting
Casting is performed with several different types of molds:
Molding sand
Loam
Shell mold
Metal dies
Centrifugal mold
Cast Iron
Types of iron used as construction materials:
Wrought iron
Gray cast iron
White cast iron
Chilled iron
Malleable iron
Wrought Iron
Wrought iron:
Highly refined iron – rarely used
Have a very small carbon content (not more than 0.15 percent)
Contains some slag as a one-directional fiber – grains-like surface
Properties are different parallel and perpendicular to the fibers.
Ductile and tough – very brittle when cold
Resists corrosion better than steel
Unlike most iron and steel, which have the same properties in all directions.
Gray Cast Iron
Gray cast iron is the most widely used type of cast iron. It has a high content of carbon. Graphite flakes give it a gray appearance.
Properties include:
Excellent machinability
High resistance to wear
Poor ductility and toughness
White Cast Iron
White cast iron is the only cast iron in which the carbon is combined with iron as cementite (Fe
3
C). It is:
CM 3502 Cheat Sheet
Hard and more resistant to wear than gray cast iron
Difficult to machine, less resistant to corrosion, brittle, difficult to cast
Used in crushers, grinders, mixers
Chilled cast iron is preferred: cores of gray iron and surface of white iron
Used in railway-car wheels
Malleable cast iron: white iron made tough and ductile
Steel is poured into ingot molds for further processing.
Most civil engineering steels are hot-rolled sections:
The ingot is squeezed into a smaller cross-section by passing through rollers that exert very high pressure
The changing shape is passed and repassed through rollers until the desired shape is achieved
Mechanical testing
The following are mechanical testing:
Tension (Strength / Ductility)
Torsion
Impact
Hardness
Fatigue
Torsion
t
max
= maximum shear stress
T = torque
r = radius
J = polar moment of inertia = γ = shear strain
= angle of twist in radians
L = gauge length
CM 3502 Cheat Sheet
G = shear modulus
Example
A rod of high-strength steel is given
Length = 1m
Radius = 20mm
The rod is subjected to a torque by rotating the cross-section at one end 45° in relation to the other end. The shear modulus of the material is 90GPa.
What is the applied torque?
Solution
L = 1m R = 20mm = 0.02m G=90GPa = 90*10
9
Pa Rotation = 45°
Impact
The impacts include:
The behavior of materials under dynamic loads which are applied suddenly.
It is useful to study the ductile-to-brittle fracture transition that occurs in some metals
Study of impact involves:
1.
Induced stresses
2.
Energy transfer
3.
Energy absorption and dissipation
Hardness
Hardness is a measure of a material’s resistance to localized plastic deformation (small dent or scratch).
Measured hardness is relative. It is:
Force small indenter into the surface
Measure depth or size of the indentation
Hardness number
Your preview ends here
Eager to read complete document? Join bartleby learn and gain access to the full version
- Access to all documents
- Unlimited textbook solutions
- 24/7 expert homework help
CM 3502 Cheat Sheet
o
softer material = lower hardness number
Cannot always compare values determined by different techniques
Hardness Measurements
There are no units for hardness. All scales are relative. Different testing procedures work better with some materials than others. Different indenters, loading criteria, and scales have been developed for various materials and industries. Relative comparison across scales can be difficult. In the next few subchapters, you will see various testing apparatus and scales.
Different Procedures
Mohs Scale
Rockwell
Brinell
Knoop and Vickers
Correlations
Between different hardness scales
With tensile strength (roughly proportional)
Fatigue
Fatigue occurs in structures that are subjected to dynamic cyclic stresses. Failure occurs at a stress level considerably lower than the tensile or yield strength for a static load. Fatigue is the single largest cause of failure in metals (approximately 90%).
Tests
Test apparatus is designed to duplicate as nearly as possible the service stress conditions.
The subject specimen to stress cycling at a maximum stress amplitude (
)
equal to or less than the tensile (or other) strength.
Count number of stress cycles to failure
The procedure is repeated at progressively decreasing maximum stress amplitudes.
Stress to N-cycles Diagram
For many materials, as the stress is lowered there is a point reached at which an infinite number of cycles will not cause a fatigue failure. This is called the endurance
limit. Aluminum does not have an endurance limit.
Fatigue test results are presented as a plot of stress (S) versus the logarithm of the number of cycles to failure (N) for each of the specimens.
CM 3502 Cheat Sheet
Fatigue strength
The stress level at which failure is likely to occur for some given number of cycles.
Endurance limit
Maximum stress level below which a material can endure an essentially infinite number of stress cycles and doesn't fail
Most steels have an endurance limit that is approximately 40-50% of the tensile strength
Some alloys do not have an endurance limit; fatigue will eventually occur
Microcrack is initiated
At some small internal or surface flaw (magnitude of the applied stress is concentrated)
Crack propagation
Crack grows longer because of cyclic stress
Rapid crack growth
Intact portion of the cross-section is no longer capable of sustaining the load; crack grows very rapidly, and failure is usually sudden
Fatigue life of a structure
Time to crack initiation + time to growth to point of failure
Fatigue Life Improvement Techniques
Smooth surface finish eliminating surface flaws
Refined processing and fabrication methods to reduce internal defects
Design modifications to reduce stress amplification
Surface hardening techniques
Heat treatments include:
Annealing
Normalizing
Quenching or Hardening
Tempering
Annealing
Annealing is a hot-rolled steel section that is reheated and allowed to cool slowly. This relieves residual internal stresses.
CM 3502 Cheat Sheet
The objectives of annealing include:
soften steel
remove internal stresses
remove gases
increase ductility and toughness
Normalizing
Normalizing is similar to annealing. Steel is heated to a higher temperature, held at a high temperature, and then cooled slowly at room temperature. It is considerably cheaper than annealing. Normalizing improves ductility and produces high fracture toughness. Hardening or Quenching
Steel is heated and then is “quenched” or cooled rapidly (in water, oil, or brine). It hardens the steel, leaving it in a state of strain. It “fixes” the crystalline structure and hardens the steel. Martensite (resulting material) is extremely brittle.
Tempering
Quenched steel is reheated to some temperature between 200°C and 550oC, followed by either rapid or slow cooling. Resulting steel is softer but much tougher than quenched steel. It is used to further improve quenched steel.
Many elements can be added to impart certain properties of steel:
Nickel (up to 12%): increases corrosion resistance and hardness
Tungsten (up to 20%): promotes hardness – assures strength retention at high
temperatures
Cobalt (17 to 36%): increases magnetic properties of alloy steels
Copper (up to 0.25%): increases strength and corrosion resistance
Molybdenum (0.1 to 0.4%): increases toughness and hardenability
Each steel type is designated by a group of numbers:
The first number indicates the class of steel:
o
1 is carbon steel, 2 is nickel steel, 4 is molybdenum steel
The next one or two digits indicate the major percentage of the major alloying element
The last two or three digits indicate the carbon content in hundredths of a percent
Examples
1040 steel:
o
Carbon steel
o
0.40 % carbon
o
no alloy
2515 steel:
o
Nickel steel
Your preview ends here
Eager to read complete document? Join bartleby learn and gain access to the full version
- Access to all documents
- Unlimited textbook solutions
- 24/7 expert homework help
CM 3502 Cheat Sheet
o
5% nickel
o
0.15% carbon
Structural Steel
Composition
< 0.25% Carbon by weight (i.e., austenitic steel)
Up to 1.6% Manganese (Mn)
0.2 - 0.5% Copper (Cu) alloy
Types
Plates, beams (T, I), hollow sections, angles, rebar (plain or deformed), wire (mesh)
Specifications
Chemistry (metallurgy), Treatment, Strength, and Deformability (ductility)
Four major categories
1.
Structural steel (carbon steel):
o
Yield strength from 32 to 42ksi
o
A36: all-purpose steel widely used for buildings and bridges
o
Cheapest type – used unless corrosion resistance or heat resistance is of great importance
2.
High-strength low alloy (alloys such as columbium, vanadium, or copper are added)
o
Yield strength from 40 to 65ksi
3.
Corrosion resistant, high-strength, low-alloys (alloys such as chromium, nickel, copper are added): o
Four times the corrosion resistance of structural carbon steel
o
Yield strength from 42 to 50ksi
4.
Quenched and Tempered alloy (alloys such as nickel, silicon, molybdenum are
added):
o
Yield strength from 90 to 100ksi
o
Used in welded structures
Your preview ends here
Eager to read complete document? Join bartleby learn and gain access to the full version
- Access to all documents
- Unlimited textbook solutions
- 24/7 expert homework help
CM 3502 Cheat Sheet
Your preview ends here
Eager to read complete document? Join bartleby learn and gain access to the full version
- Access to all documents
- Unlimited textbook solutions
- 24/7 expert homework help
CM 3502 Cheat Sheet
Your preview ends here
Eager to read complete document? Join bartleby learn and gain access to the full version
- Access to all documents
- Unlimited textbook solutions
- 24/7 expert homework help
CM 3502 Cheat Sheet
Your preview ends here
Eager to read complete document? Join bartleby learn and gain access to the full version
- Access to all documents
- Unlimited textbook solutions
- 24/7 expert homework help
CM 3502 Cheat Sheet
Your preview ends here
Eager to read complete document? Join bartleby learn and gain access to the full version
- Access to all documents
- Unlimited textbook solutions
- 24/7 expert homework help
CM 3502 Cheat Sheet
Your preview ends here
Eager to read complete document? Join bartleby learn and gain access to the full version
- Access to all documents
- Unlimited textbook solutions
- 24/7 expert homework help
CM 3502 Cheat Sheet
Your preview ends here
Eager to read complete document? Join bartleby learn and gain access to the full version
- Access to all documents
- Unlimited textbook solutions
- 24/7 expert homework help
CM 3502 Cheat Sheet
Concrete is required for an exterior column located above ground where substantial freezing and thawing is not a concern. The 28-day compressive strength should be 4,000 lb/in2 . The column dimensions are 12” by 12” with rebar spaced with 2” clear spacing and 1.5” cover.
The properties of the materials are as follows:
Your preview ends here
Eager to read complete document? Join bartleby learn and gain access to the full version
- Access to all documents
- Unlimited textbook solutions
- 24/7 expert homework help
CM 3502 Cheat Sheet
Cement : Type I, specific gravity = 3.15 Coarse Aggregate: Bulk specific gravity (SSD) = 2.80; absorption capacity = 2%; dry-rodded unit weight = 115 lb/ft3 ; moisture content = 1% Maximum coarse aggregate size availability: 1/2in, 3/4in, 1in or 1.5in Fine Aggregate: Bulk specific gravity (SSD) = 2.7; absorption capacity = 1.3%; fineness modulus = 2.80; moisture content = 3.7%
Indicate range of slump recommended but use between 1 and 2in for your mix design. Calculate the weights of cement, moist gravel, moist sand, and water to be added to the batch per yd3 of
concrete.
Your preview ends here
Eager to read complete document? Join bartleby learn and gain access to the full version
- Access to all documents
- Unlimited textbook solutions
- 24/7 expert homework help
Related Documents
Related Questions
Hi can you please help me with the attached question?
arrow_forward
Don’t use ai
arrow_forward
True or False
a) “If the most conservative fatigue criterion were used for infinite life design, the first cycle yield check is not needed.”
b) If an accurate value for the notch sensitivity is hard to find, I should consider the fatigue stress concentration factor higher than the stress concentration factor under static loading condition in design.
c) It is easier to find the asymptotic value of fatigue strength as the endurance limit on the S-N curve for a brass alloy (Cu70Zn30) than that of endurance limit on the S-N curve for an AISI 1045 steel.
arrow_forward
Calculate the average fall time and standard deviation using the data above.
Average - 1.5s
Stdev- 1.85s
Use the average fall time and one of the kinematic equations to determine the height of the building.
Add the standard deviation from step 1 to the average fall time from step 2. This represents a “maximum fall time.” Use this time to calculate the “maximum” height of the building.
arrow_forward
Test Specimen
4140 CF steel
6061 T6 Al
Gray Cast iron 40
FC Brass 360
Impact Energy (J or ft-lb)
48.5 ft-lb
25 ft-lb
12 ft-lb
27 ft-lb
Impact Strength (J/m
or ft-lb/in)
123.096 ft-lb/in
63.452 ft-lb/in
What is the final analysis/ overall observation from the data?
30.457 ft-lb/in
68.528 ft-lb/in
arrow_forward
on-the-job conditions.
9 ±0.2-
0.5
M
Application questions 1-7 refer to the drawing above.
1. What does the flatness tolerance labeled "G" apply to?
Surface F
A.
B.
Surfaces E and F
C. Surfaces D, E, H, and I
D.
The derived median plane of 12 +0.2
0.5
0.5
CF) 20 ±0.2
0.1
7.
O
12 ±0.2-
H
0.3
ASME Y14.5-2009
arrow_forward
3 TRUE & 1 FALSE:
__________a. Two different materials can have the same moduli of elasticity and rigidity but different values of Poisson’s ratio
__________b. If a material has a Poisson’s ratio of 0, it is still possible to relate its moduli of elasticity and rigidity
__________c. The ratio between the modulus of rigidity and modulus of elasticity is constant
__________d. For most materials, the maximum ratio for the modulus of elasticity to modulus of rigidity is 3.
arrow_forward
SEE MORE QUESTIONS
Recommended textbooks for you
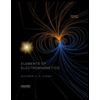
Elements Of Electromagnetics
Mechanical Engineering
ISBN:9780190698614
Author:Sadiku, Matthew N. O.
Publisher:Oxford University Press
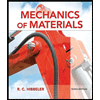
Mechanics of Materials (10th Edition)
Mechanical Engineering
ISBN:9780134319650
Author:Russell C. Hibbeler
Publisher:PEARSON
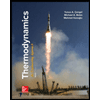
Thermodynamics: An Engineering Approach
Mechanical Engineering
ISBN:9781259822674
Author:Yunus A. Cengel Dr., Michael A. Boles
Publisher:McGraw-Hill Education
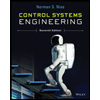
Control Systems Engineering
Mechanical Engineering
ISBN:9781118170519
Author:Norman S. Nise
Publisher:WILEY
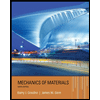
Mechanics of Materials (MindTap Course List)
Mechanical Engineering
ISBN:9781337093347
Author:Barry J. Goodno, James M. Gere
Publisher:Cengage Learning
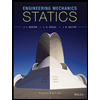
Engineering Mechanics: Statics
Mechanical Engineering
ISBN:9781118807330
Author:James L. Meriam, L. G. Kraige, J. N. Bolton
Publisher:WILEY
Related Questions
- Hi can you please help me with the attached question?arrow_forwardDon’t use aiarrow_forwardTrue or False a) “If the most conservative fatigue criterion were used for infinite life design, the first cycle yield check is not needed.” b) If an accurate value for the notch sensitivity is hard to find, I should consider the fatigue stress concentration factor higher than the stress concentration factor under static loading condition in design. c) It is easier to find the asymptotic value of fatigue strength as the endurance limit on the S-N curve for a brass alloy (Cu70Zn30) than that of endurance limit on the S-N curve for an AISI 1045 steel.arrow_forward
- Calculate the average fall time and standard deviation using the data above. Average - 1.5s Stdev- 1.85s Use the average fall time and one of the kinematic equations to determine the height of the building. Add the standard deviation from step 1 to the average fall time from step 2. This represents a “maximum fall time.” Use this time to calculate the “maximum” height of the building.arrow_forwardTest Specimen 4140 CF steel 6061 T6 Al Gray Cast iron 40 FC Brass 360 Impact Energy (J or ft-lb) 48.5 ft-lb 25 ft-lb 12 ft-lb 27 ft-lb Impact Strength (J/m or ft-lb/in) 123.096 ft-lb/in 63.452 ft-lb/in What is the final analysis/ overall observation from the data? 30.457 ft-lb/in 68.528 ft-lb/inarrow_forwardon-the-job conditions. 9 ±0.2- 0.5 M Application questions 1-7 refer to the drawing above. 1. What does the flatness tolerance labeled "G" apply to? Surface F A. B. Surfaces E and F C. Surfaces D, E, H, and I D. The derived median plane of 12 +0.2 0.5 0.5 CF) 20 ±0.2 0.1 7. O 12 ±0.2- H 0.3 ASME Y14.5-2009arrow_forward
arrow_back_ios
arrow_forward_ios
Recommended textbooks for you
- Elements Of ElectromagneticsMechanical EngineeringISBN:9780190698614Author:Sadiku, Matthew N. O.Publisher:Oxford University PressMechanics of Materials (10th Edition)Mechanical EngineeringISBN:9780134319650Author:Russell C. HibbelerPublisher:PEARSONThermodynamics: An Engineering ApproachMechanical EngineeringISBN:9781259822674Author:Yunus A. Cengel Dr., Michael A. BolesPublisher:McGraw-Hill Education
- Control Systems EngineeringMechanical EngineeringISBN:9781118170519Author:Norman S. NisePublisher:WILEYMechanics of Materials (MindTap Course List)Mechanical EngineeringISBN:9781337093347Author:Barry J. Goodno, James M. GerePublisher:Cengage LearningEngineering Mechanics: StaticsMechanical EngineeringISBN:9781118807330Author:James L. Meriam, L. G. Kraige, J. N. BoltonPublisher:WILEY
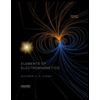
Elements Of Electromagnetics
Mechanical Engineering
ISBN:9780190698614
Author:Sadiku, Matthew N. O.
Publisher:Oxford University Press
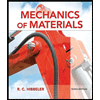
Mechanics of Materials (10th Edition)
Mechanical Engineering
ISBN:9780134319650
Author:Russell C. Hibbeler
Publisher:PEARSON
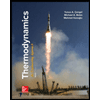
Thermodynamics: An Engineering Approach
Mechanical Engineering
ISBN:9781259822674
Author:Yunus A. Cengel Dr., Michael A. Boles
Publisher:McGraw-Hill Education
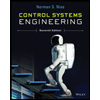
Control Systems Engineering
Mechanical Engineering
ISBN:9781118170519
Author:Norman S. Nise
Publisher:WILEY
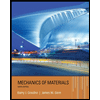
Mechanics of Materials (MindTap Course List)
Mechanical Engineering
ISBN:9781337093347
Author:Barry J. Goodno, James M. Gere
Publisher:Cengage Learning
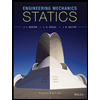
Engineering Mechanics: Statics
Mechanical Engineering
ISBN:9781118807330
Author:James L. Meriam, L. G. Kraige, J. N. Bolton
Publisher:WILEY