MEC 430 LAB 1.docx
pdf
keyboard_arrow_up
School
Toronto Metropolitan University *
*We aren’t endorsed by this school
Course
430
Subject
Mechanical Engineering
Date
Oct 30, 2023
Type
Pages
15
Uploaded by PresidentMoon265
Your preview ends here
Eager to read complete document? Join bartleby learn and gain access to the full version
- Access to all documents
- Unlimited textbook solutions
- 24/7 expert homework help
Your preview ends here
Eager to read complete document? Join bartleby learn and gain access to the full version
- Access to all documents
- Unlimited textbook solutions
- 24/7 expert homework help
Your preview ends here
Eager to read complete document? Join bartleby learn and gain access to the full version
- Access to all documents
- Unlimited textbook solutions
- 24/7 expert homework help
Your preview ends here
Eager to read complete document? Join bartleby learn and gain access to the full version
- Access to all documents
- Unlimited textbook solutions
- 24/7 expert homework help
Your preview ends here
Eager to read complete document? Join bartleby learn and gain access to the full version
- Access to all documents
- Unlimited textbook solutions
- 24/7 expert homework help
Recommended textbooks for you
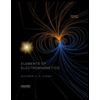
Elements Of Electromagnetics
Mechanical Engineering
ISBN:9780190698614
Author:Sadiku, Matthew N. O.
Publisher:Oxford University Press
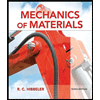
Mechanics of Materials (10th Edition)
Mechanical Engineering
ISBN:9780134319650
Author:Russell C. Hibbeler
Publisher:PEARSON
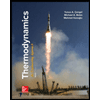
Thermodynamics: An Engineering Approach
Mechanical Engineering
ISBN:9781259822674
Author:Yunus A. Cengel Dr., Michael A. Boles
Publisher:McGraw-Hill Education
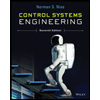
Control Systems Engineering
Mechanical Engineering
ISBN:9781118170519
Author:Norman S. Nise
Publisher:WILEY
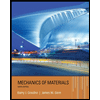
Mechanics of Materials (MindTap Course List)
Mechanical Engineering
ISBN:9781337093347
Author:Barry J. Goodno, James M. Gere
Publisher:Cengage Learning
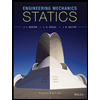
Engineering Mechanics: Statics
Mechanical Engineering
ISBN:9781118807330
Author:James L. Meriam, L. G. Kraige, J. N. Bolton
Publisher:WILEY
Recommended textbooks for you
- Elements Of ElectromagneticsMechanical EngineeringISBN:9780190698614Author:Sadiku, Matthew N. O.Publisher:Oxford University PressMechanics of Materials (10th Edition)Mechanical EngineeringISBN:9780134319650Author:Russell C. HibbelerPublisher:PEARSONThermodynamics: An Engineering ApproachMechanical EngineeringISBN:9781259822674Author:Yunus A. Cengel Dr., Michael A. BolesPublisher:McGraw-Hill Education
- Control Systems EngineeringMechanical EngineeringISBN:9781118170519Author:Norman S. NisePublisher:WILEYMechanics of Materials (MindTap Course List)Mechanical EngineeringISBN:9781337093347Author:Barry J. Goodno, James M. GerePublisher:Cengage LearningEngineering Mechanics: StaticsMechanical EngineeringISBN:9781118807330Author:James L. Meriam, L. G. Kraige, J. N. BoltonPublisher:WILEY
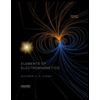
Elements Of Electromagnetics
Mechanical Engineering
ISBN:9780190698614
Author:Sadiku, Matthew N. O.
Publisher:Oxford University Press
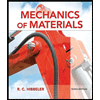
Mechanics of Materials (10th Edition)
Mechanical Engineering
ISBN:9780134319650
Author:Russell C. Hibbeler
Publisher:PEARSON
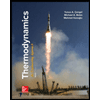
Thermodynamics: An Engineering Approach
Mechanical Engineering
ISBN:9781259822674
Author:Yunus A. Cengel Dr., Michael A. Boles
Publisher:McGraw-Hill Education
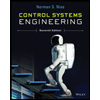
Control Systems Engineering
Mechanical Engineering
ISBN:9781118170519
Author:Norman S. Nise
Publisher:WILEY
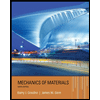
Mechanics of Materials (MindTap Course List)
Mechanical Engineering
ISBN:9781337093347
Author:Barry J. Goodno, James M. Gere
Publisher:Cengage Learning
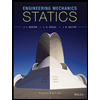
Engineering Mechanics: Statics
Mechanical Engineering
ISBN:9781118807330
Author:James L. Meriam, L. G. Kraige, J. N. Bolton
Publisher:WILEY
Browse Popular Homework Q&A
Q: 2. A jetliner touches down moving horizontally at 288 km/h. The plane then undergoes
acceleration…
Q: 2. (a) Let f(x)
=
4- x²
X-
and find f(2) or explain why it does not exist
(b) Use algebra and other…
Q: 10-
8-
6-
4-
2-
Match the graph of f with the correct sign chart.
-8
-6
-4
-2-2-
-4-
-6-
-8-
-10…
Q: Required information
Problem 08.034 - DEPENDENT MULTI-PART PROBLEM - ASSIGN ALL PARTS - Refrigerant…
Q: How many of the surveyed customers know about the computers because of EXACTLY ONE of these forms of…
Q: A projectile is launched from ground level with an initial velocity of vo feet per second.…
Q: Franklin Training Services (FTS) provides instruction on the use of computer software for the…
Q: Which statement is true?
a. Veins have more muscle and elastic fibers than arteries
b. Arteries…
Q: In some other applications, we might need two stacks with the same type of data. If we implement
the…
Q: E
OSTATES OF MATTER
Using heat of fusion or vaporization to find the heat needed to...
Calculate the…
Q: Question 25 of 30
Current Attempt in Progress
Activity Cost Pools
Ordering and receiving
Food…
Q: The graph of f(x) is given below (click on graph to enlarge):
Determine for which values of x = a…
Q: Write a query that returns the EMP_NUM and Number of ratings he/she earned (based on EARNEDRATING…
Q: A piston-cylinder device initially contains 2 kg of refrigerant-134a at 100 kPa and 20°C. Heat is…
Q: Unethical judges may be removed from the bench through
A: impeachment proceedings.
B: recall…
Q: omplete the following passage from Mary Rowlandson's captivity narrative (HINT: both answers are the…
Q: Complete the sentence below.
2
The x-coordinate of the vertex of f(x) = ax + bx+c, a #0, is
The…
Q: Find the time required for an investment of $3000 to grow to $5000 at an interest rate of 7.5% per…
Q: 1. What are the magnitude and direction of the angular momentum relative to the origin
of the 200 g…
Q: Prove by induction that for any positive.
integer n
2
32 3³ = (n(0₂1) ²
3=1
а
Q: What cellular structures do eukaryotic cells have that prokaryotic cells lack?
Select ALL that apply…
Q: A 1.0 kg ball and a 2.0 kg ball are connected by a 1.0 m long rigid, massless rod. The rod
is…
Q: B
The sum of vectors A and B is
Q: Consider the position vector a shown in the diagram below. a makes an angle with
the positive x…
Q: Can I get help with requirments 4-8 as well please?