Midterm 1 review topics
docx
keyboard_arrow_up
School
Baruch College, CUNY *
*We aren’t endorsed by this school
Course
3710
Subject
Management
Date
Feb 20, 2024
Type
docx
Pages
13
Uploaded by SuperMusicOryx14
MGT 3710 Midterm Fall 2023
75 minutes exam; 25 questions, 4 points each; all multiple choice
Basic calculations will be required; no spreadsheet work, but a calculating device will be needed
Midterm will be on BlackBoard – bring a device that supports BlackBoard
No phones are permitted to be used during the exam and must be put away.
Areas likely to be on midterm
Supply chain surplus – what it is and how to calculate it
The value (AKA supply chain surplus) = Customer value - Supply chain cost
o
Difference between what the value of the final product is to the customer and the costs the entire supply chain incurs in filling the customer’s request.
The difference between the value of the product and its price remains with the customer as consumer surplus.
The rest of the supply chain surplus becomes supply chain profitability, the difference between the revenue generated from the customer and the overall cost across the supply chain.
Effective supply chain management involves the management of supply chain assets and product, information, and fund flows to grow the total supply chain surplus.
Higher supply chain profitability = more successful
o
Success should be measured in terms of supply chain surplus and not in terms of
the profits at an individual stage
Push, pull, push/pull boundary
Push/Pull View
o
Pull processes are initiated by a customer order
Pull processes operate when customer demand is known
Constrained by inventory and capacity decisions
Minimize excess inventory and waste
Often rely on JIT inventory where products are manufactured only when they are needed.
o
Push processes are initiated in anticipation of customer orders
Push processes operate in an uncertain environment due to unknown customer demand
Approach is often used in industries where demand is relatively stable and predictable
Higher inventory levels to ensure products are readily available.
o
Push/pull boundary
In a supply chain separates push processes from pull processes.
It’s the dividing line that separates the upstream (earlier) and downstream
(later) stages of the supply chain.
What is a supply chain, supply chain evolution and how supply chain fits in the organization?
A supply chain consists of all parties involved, directly or indirectly, in fulfilling a customer request.
Dynamic, constant flow of information, product, and funds among different stages.
Most are networks
o
Consist of:
Customers
Retailers
Wholesalers/distributors
Manufacturers
Component/raw material suppliers
Supply chain evolution refers to the process of transformation and development that supply chains undergo over time
o
Technological advancements, globalization, e-commerce and omnichannel retail,
risk management
Learnings from the paper airplane and Belleza simulations
Belleza Simulation:
Corporate procurement - Centralized group working from headquarters. Corporate procurement buys packaging supplies and works very closely with sales, marketing and advertising. Tend to buy large dollar
items with long term contracts.
Local manufacturing - Work from manufacturing site. Three buyers each buying raw materials for their specific product: Lipstick, shaving cream, nail polish. Tend to buy low cost items with year to year contracts.
External Supply - Centralized group working remotely. Manage third party manufacturers. Must establish long term contracts and assure the third part meets company quality standards as well as all supply requirements.
Marketing
- Centralized group working from headquarters. Responsible for brand growth, revenue and customer experience. Finance
- Centralized group working from headquarters. - Responsible of company financial performance and shareholder value.
Supply chain components – Strategy, planning, operations
Designing a supply chain requires many business considerations
Strategy
o
Months to years
o
Company decides how to structure the supply chain over the next several years
Chain’s configuration, resource allocation, processes for each stage o
Function in-house, location and capabilities of production and warehousing facilities
Planning
o
Weeks to months
o
Establish constraints within which planning must be done
Maximize value given constraints
o
Decisions regarding which markets will be supplied from which locations, subcontracting of manufacturing, inventory policies, timing and size of marketing and price promotions
o
Include uncertainty in demand, exchange rates, and competition
Operations
o
Days to weeks
o
Make decisions regarding individual customer orders
o
Handle incoming customer orders; allocate inventory/production to individual orders, set a date by which orders need to be done, generate pick lists at the warehouse, set delivery schedules, replenishment orders, etc.
Strategy refers to what each process/function will try to do particularly well.
o
Product development strategy specifies the portfolio of new products that a company will try to develop.
o
Marketing and sales strategy specifies how the market will be segmented and how the product will be positioned, priced, and promoted.
o
Supply chain strategy determines the nature of procurement of raw materials, transportation of materials to and from the company, manufacture of the product or operation to provide the service, and distribution of the product to the customer, along with A/S.
Supply chain strategy and Supply Chain fit- Example: Wholefoods vs Aldi
Strategic fit: requires both competitive and supply chain strategies of a company to have aligned goals.
o
Competitive strategy and all functional strategies must fit together to form a coordinated overall strategy. Each functional strategy must support other functional strategies and help a firm reach its competitive strategy goal.
Your preview ends here
Eager to read complete document? Join bartleby learn and gain access to the full version
- Access to all documents
- Unlimited textbook solutions
- 24/7 expert homework help
o
The different functions in a company must appropriately structure their processes
and resources to be able to execute these strategies successfully.
o
The design of the overall supply chain and the role of each stage must be aligned
to support the supply chain strategy.
How is strategic fit achieved
Understanding the customer and supply chain uncertainty
o
Identify needs of the customer segment being served
o
Customer demand from different segments varies along several attributes
Quantity of the product needed in each lot
Response time that customers are willing to tolerate
Variety of products needed
Service level required
Price of the product
Desired rate of innovation in the product
o
Uncertainty from the customer and the supply chain can be combined and mapped on the implied uncertainty spectrum
Understanding the supply chain capabilities
o
Supply chain responsiveness includes a chain’s ability to:
Respond to wide ranges of quantities demanded
Meet short lead times
Handle a large variety of products
Meet a high service level
Build highly innovative products
Handle supply uncertainty
o
Supply chain efficiency is the inverse of the cost of making and delivering a product to the customer. Uncertainty
Demand uncertainty – what are the elements? What is done to increase/decrease demand uncertainty
-
Demand uncertainty reflects uncertainty of customer demand for a product
-
Implied demand uncertainty is the resulting uncertainty for only the portion of the demand that the supply chain plans to satisfy based on the attributes the customer desires.
o
EX: a firm supplying only emergency orders for a product will face a higher implied demand uncertainty than a firm that supplies the same product with a long lead time, as the second firm has an opportunity to fulfill the orders evenly over the long lead time.
Supply uncertainty – what are the elements? What is done to increase/decrease supply uncertainty
-
Elements include demand uncertainy, supply uncertainty (availability and reliability of suppliers, can result from supplier disruptions, quality issues, delays in the supply of raw materials or components), market uncertainty, external factors, regulatory uncertainty.
Supply Chain segmentation Customer demand from different segments varies along several attributes:
• Quantity of the product needed in each lot:
An emergency order for material needed to
repair a production line is likely to be small. An order for material to construct a new production
line is likely to be large.
• Response time that customers are willing to tolerate:
The tolerable response time for
the emergency order is likely to be short, whereas the allowable response time for the construction
order is apt to be long.
• Variety of products needed:
A customer may place a high premium on the availability of
all parts of an emergency repair order from a single supplier. This may not be the case for
the construction order.
• Service level required:
A customer placing an emergency order expects a high level of
product availability. This customer may go elsewhere if all parts of the order are not immediately
available. This is not apt to happen in the case of the construction order, for which
a long lead time is likely.
• Price of the product
: The customer placing the emergency order is apt to be much less
sensitive to price than the customer placing the construction order.
•
Desired rate of innovation in the product:
Customers at a high-end department store
expect a lot of innovation and new designs in the store’s apparel. Customers at Walmart
may be less sensitive to new product innovation.
Characteristics of a Responsive vs efficient supply chain; characteristics of a functional vs innovative supply chain
Supply chain responsiveness includes a chain’s ability to:
o
Respond to wide ranges of quantities demanded
o
Meet short lead times
o
Handle a large variety of products
o
Meet a high service level
o
Build highly innovative products
o
Handle supply uncertainty
Supply chain efficiency is the inverse of the cost of making and delivering a product to the customer.
Your preview ends here
Eager to read complete document? Join bartleby learn and gain access to the full version
- Access to all documents
- Unlimited textbook solutions
- 24/7 expert homework help
Product life cycle and its impact on supply chain
Beginning stages of a product’s life cycle:
-
Demand is very uncertain, and supply is unpredictable
-
Margins are often high, time is crucial to gaining sales
-
Product availability is crucial to capturing the market
-
Cost is often a secondary consideration
Given high demand uncertainty and the need for a high level of product availability, responsiveness is the most important characteristic.
Later stages (when it becomes a commodity): -
Demand becomes more certain, predictable supply
-
Margins are lower as a result of an increase in competitive pressure
-
Price becomes a significant factor in customer choice.
In this situation, efficiency becomes the most important characteristic.
Supply chain financials – Working capital, Cash to cash (Chapter 6)
-
When considering global sourcing decisions, total cost should include the impact of global sourcing on freight, inventories, lead time, quality, on-time delivery, minimum order quantity, working capital, and stockouts.
Companies should evaluate the impact of offshoring on the following key elements of total cost:
o
Supplier price
Link to costs from direct materials, direct labor, indirect labor, management, overhead, capital amortization, local taxes, manufacturing costs, and local regulatory compliance costs.
o
Terms
Costs are affected by net payment terms and any volume discounts
Delivery costs:
o
include in-country transportation, ocean/air freight, destination transport, and packaging.
Inventory and warehousing:
o
include in-plant inventories, in-plant handling, plant ware-house costs, supply chain inventories, and supply chain warehousing costs.
Cost of quality:
o
includes cost of validation, cost of performance drop due to poorer quality, and cost of incremental remedies to combat quality drop.
Customer duties, value-added taxes, local tax incentives.
Cost of risk, procurement staff, broker fees, infrastructure (IT and facilities), and tooling and mold costs.
Exchange rate trends and their impact on cost.
Offshoring to low cost countries are attractive for products with high labor content, large production volumes, relatively low variety, and low transportation costs relative to the product value.
Companies using only an offshore facility often find themselves carrying extra inventory and resorting to air freight because of the long and variable lead times.
Cash-to-cash cycle roughly measures the average amount of time from when cash enters the process as cost to when it returns as collected revenue.
o
– Weeks Payable (1/APT) + Weeks in Inventory (1/INVT) + Weeks Receivable (1/ART)
Supply chain drivers- what are the drivers and when are they used? CHAPTER 3
Performance depends on the interaction between these drivers. The goal is to structure the drivers to achieve the desired level of responsiveness at the lowest possible cost, thus improving the supply chain surplus and the firm’s financial performance.
-
Facilities
o
The actual physical locations where products are stored, assembled, or fabricated.
-
Inventory
o
All raw materials, WIP, and finished goods within a supply chain
-
Transportation
o
Moving inventory from point to point in the supply chain
-
Information
o
Data and analysis concerning facilities, inventory, transportation, costs, prices, and customers throughout the supply chain
-
Sourcing
o
Choice of who will perform a particular supply chain activity, such as production, storage, transportation, or the management of information.
-
Pricing
o
How much a firm will charge for the goods and services that it makes available in the supply chain.
Retail supply chain design – 4 distribution networks to customers; which items fit best? What is Omnichannel and when it is used?
Four distribution networks:
o
Showrooms / Home-Delivery
Low levels of inventory
o
Traditional retail
High level of inventory (changing)
Customer leaves with product o
Online info + pickup
Reduces outbound transportation costs
o
Online info + delivery
Aggregation of inventory
Few locations
Omni-channel retailing o
Provide a seamless and integrated shopping experience to customers across multiple channels, including physical stores, e-commerce websites, mobile apps, social media, etc.
o
Goal is to allow customer to shop through their preferred channel.
o
Three flows
Information
Product
Funds
What is the SCOR model and why is it used
-
The SCOR model provides a description of supply chain processes, a framework for relationships between these processes, and a set of metrics to measure process performance.
-
Used to optimize supply chain operations and achieve better efficiency, effectiveness, and competitiveness.
-
SCOR = supply chain operations reference
Types of data management assurance – Trust, Diversity. Literacy, Complexity
-
Trust
o
Confidence that an organization and its stakeholders have in the accuracy, reliability, and integrity of its data
o
What is the source of the data?
-
Diversity
o
Wide variety of data types, sources, and formats that organizations must manage, ranging from structured to unstructured.
o
Does the data reflect a narrow or broad perspective?
o
Any inherent bias?
-
Literacy
o
What is user’s data maturity?
o
Is the data targeted to the right user?
Your preview ends here
Eager to read complete document? Join bartleby learn and gain access to the full version
- Access to all documents
- Unlimited textbook solutions
- 24/7 expert homework help
-
Complexity
o
How have the analytics been tested?
o
Are the data tools robust and controlled?
Network supply chain design – Factors to consider when building a network.
Six distinct distribution network designs:
o
Manufacturer storage with direct shipping
Shipped directly from manufacturer to the end customer, bypassing the retailer (who takes the order and initiates the delivery request)
Also referred to as drop-shipping
Centralizes inventories at the manufacturer which can aggregate demand across all retailers that it supplies.
Able to provide a high level of product availability with lower levels
of inventory
Benefits are highest for high-value, low-demand items with unpredictable demand.
High transportation costs because manufacturers are farther from customers.
A customer order includening items from several manufacturers will involve multiple shipments to the customer.
o
Manufacturer storage with direct shipping and in-transit merge
Combines pieces of the order coming from different locations so the customer gets a single delivery.
In-transit merge decreases transportation costs relative to drop-shipping by aggregating the final delivery.
Party performing the in-transit merge has higher facility costs
Overall supply chain facility and handling costs are higher than with drop-
shipping.
o
Distributor storage with carrier deliver
Inventory is held not by manufacturers but by distributors/retailers in intermediate warehouses, and package carriers are used to transport products from the intermediate location to the final customer.
Stock only the slow- to fast-moving items at their warehouses, with very- slow-moving items stocked farther upstream.
Information needed is less than what is needed with manufacturer storage.
o
Distributor storage with last-mile delivery
Requires higher levels of inventory than the other options because it has a lower level of aggregation
Suitable for relatively fast moving items that are needed quickly and for which some level of aggregation is beneficial.
Facility costs are somewhat lower than those for a network with retail stores but much higher than for either manufacturer storage or distributor storage with package carrier delivery.
o
Manufacturer/distributor storage with customer pickup
Inventory costs are low, transportation costs low, marginal increase in transportation cost is small b/c trucks are already making delivers to the stores, and their utilization can be improved by including online orders.
Facility costs are high if new pickup sites have to be built.
Processing costs are high because each order must be matched with a specific customer when he/she arrives.
Significant information infrastructure is needed to provide visibility of the order until the customer picks it up.
Order visibility is extremely important as the customer must be informed when the order has arrived, and the order should be easily identified once the customer arrives to pick it up.
o
Retail storage with customer pickup
Customers walk into the retail store or place an online order and pick it up
at the retail store.
Local storage increases inventory costs b/c of lack of aggregation
For fast- to very-fast-moving items, there is marginal increase in inventory, even with local storage.
Lower transportation costs because inexpensive modes of transport can be used to replenish product at the retail store.
High facility costs because many local facilities are required
Minimal information is needed if customers walk into the store and order.
Significant amount is needed if ordered online due to visibility purposes.
Time to market is highest because the new product must penetrate through the entire supply chain before it is available to customers.
Global supply chain design – Financial and non-financial considerations; risks and benefits CHAPTER 6
Forecasting models
-
Forecasting methods
o
Causal o
Qualitative
o
Time series
o
Simulation -
Time-series (static forecasting method)
o
The goal of any forecasting method is to predict the systematic component of demand and estimate the random component.
Systematic component = (Level + Trend) x Seasonal factor
-
Moving Average
o
Used when demand has no observable trend or seasonality
-
Simple exponential smoothing
o
Used when demand has no observable trend or seasonality
-
Adaptive forecasting
o
Used when wanting to incorporate all new data that is observed
Forecast error types and formulas with basic calculations
-
Mean squared error (MSE) o
Related to the variance of the forecast error
o
Penalizes large errors
o
Appropriate to use when forecast error has a distribution that is symmetric about zero.
-
Absolute deviation
o
Absolute value of the error in period t
-
Mean absolute deviation (MAD)
o
Average of the absolute deviation over all periods
o
Can be used to estimate the standard deviation of the random component assuming
that the random component is normally distributed.
o
Better than MSE if there is no symmetric distribution -
Mean absolute percentage error (MAPE)
o
Average absolute error as a percentage of demand
o
Best used when the underlying forecast has significant seasonality and demand varies considerably from one period to the next.
-
Bias
o
Sum of forecast errors
o
Will fluctuate around 0 if the error is truly random
-
Tracking signal
o
The ratio of the bias and the MAD
1.
A supply benefit of global supply chains is
a.
larger markets for sales
b.
lower cost labor
c.
reduced lead times
d.
expanded forecast data
2.
Historical sales can differ from historical demand due to a.
Stockouts
b.
Competitor actions
c.
Promotions
d.
All the above
3.
Forecast is 120 and the demand is 100. The forecast percent error would be closest to
a.
20%
b.
-20%
c.
17%
d.
-17%
4.
For the option to globally source glass, the Belleza purchasing department was expecting to
a.
Increased capacity
b.
Improved quality
c.
Decreased lead time
d.
Improved margins
5.
A well formatted PowerPoint presentation has
a.
Many references
b.
Long sentences
c.
Consistently size fonts
Your preview ends here
Eager to read complete document? Join bartleby learn and gain access to the full version
- Access to all documents
- Unlimited textbook solutions
- 24/7 expert homework help
d.
Many images and charts
6.
Sum of forecast error is the formula for
a.
MAD
b.
Bias
c.
MSE
d.
Tracking Signal
Related Documents
Recommended textbooks for you
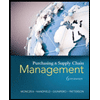
Purchasing and Supply Chain Management
Operations Management
ISBN:9781285869681
Author:Robert M. Monczka, Robert B. Handfield, Larry C. Giunipero, James L. Patterson
Publisher:Cengage Learning
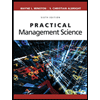
Practical Management Science
Operations Management
ISBN:9781337406659
Author:WINSTON, Wayne L.
Publisher:Cengage,
Marketing
Marketing
ISBN:9780357033791
Author:Pride, William M
Publisher:South Western Educational Publishing
Recommended textbooks for you
- Purchasing and Supply Chain ManagementOperations ManagementISBN:9781285869681Author:Robert M. Monczka, Robert B. Handfield, Larry C. Giunipero, James L. PattersonPublisher:Cengage LearningPractical Management ScienceOperations ManagementISBN:9781337406659Author:WINSTON, Wayne L.Publisher:Cengage,MarketingMarketingISBN:9780357033791Author:Pride, William MPublisher:South Western Educational Publishing
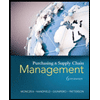
Purchasing and Supply Chain Management
Operations Management
ISBN:9781285869681
Author:Robert M. Monczka, Robert B. Handfield, Larry C. Giunipero, James L. Patterson
Publisher:Cengage Learning
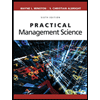
Practical Management Science
Operations Management
ISBN:9781337406659
Author:WINSTON, Wayne L.
Publisher:Cengage,
Marketing
Marketing
ISBN:9780357033791
Author:Pride, William M
Publisher:South Western Educational Publishing