MEM07032 - THEORY - Use workshop machines for basic operations - PRE LEARNING: Attempt review
pdf
keyboard_arrow_up
School
Baxter Institute *
*We aren’t endorsed by this school
Course
07032
Subject
Computer Science
Date
Dec 6, 2023
Type
Pages
58
Uploaded by UltraJackal3870
2/4/2023, 2
:
02 p. m.
MEM07032 - THEORY - Use workshop machines for basic operations - PRE LEARNING: Attempt review
Página 1 de 58
https://baxter.edfibre.com/gradejet/mod/quiz/review.php
?
attempt=147249&cmid=18279
Dashboard
Courses
Engineering
MEM40119 - Certificate IV in Engineering
MEM40119-PRELEARN
MEM07032 - Use workshop machines for basic operations
MEM07032 - THEORY - Use workshop machines for basic operations - PRE LEARNING
Information
Started on
Started on
Sunday, 17 April 2022, 12:23 PM
State
State
Finished
Completed on
Completed on
Sunday, 17 April 2022, 11:51 PM
Time taken
Time taken
11 hours 27 mins
Grade
Grade
Not yet graded
SECTION 1 DETERMINE JOB REQUIREMENTS
SECTION 1 DETERMINE JOB REQUIREMENTS
1.1
Follow standard operating procedures (SOPs)
1.1
Follow standard operating procedures (SOPs)
What is Standard Operating Procedure
What is Standard Operating Procedure
Standard operating procedures are written, step-by-step instructions that describe how to perform a
routine activity. Employees should complete them in the exact same way every time so that the business
can remain consistent. Standard operating procedures help maintain safety and efficiency for
departments such as:
Production/operations
Sales and customer service
Employee training
Legal
Financial
A standing operating procedure should never be difficult to read or vaguely worded. It should be brief, easy
to understand and contain actions steps that are simple follow. A good standard operating procedure
should clearly outline the steps and inform the employee of any safety concerns.
The standing operating procedures should be the basis for training any new employees. They should also
be updated every year to ensure they stay relevant to the current needs of the organization.
Why Do You Need Standard Operating Procedures?
Why Do You Need Standard Operating Procedures?
Some business owners have a hard time grasping why standard operating procedures are necessary. They
already trained their employees so why do they need a written document outlining the process as well?
They save time and money
They save time and money
When the same task is completed in many ways, it will always take longer to complete. Having a standard
operating procedure in place streamlines the process so employees can accomplish more in less time.
They provide consistency
They provide consistency
Having a standard operating procedure in place ensures that regardless of who is working, business
processes are being completed the correct way.
They improve communication
They improve communication
Standard operating procedures make your employees’ jobs easier because no longer do they have to
guess as to how they should be performing their jobs. And they don’t have to try to rack their brains to
remember what you told them when they were first hired.
They allow you to hold your employees accountable
They allow you to hold your employees accountable
How can you evaluate your employees if you don’t have written standards in place? Without standard
operating procedures, employee evaluations become a matter of personal opinion, which is hardly fair to
your employees.
They create a safer work environment
They create a safer work environment
2/4/2023, 2
:
02 p. m.
MEM07032 - THEORY - Use workshop machines for basic operations - PRE LEARNING: Attempt review
Página 2 de 58
https://baxter.edfibre.com/gradejet/mod/quiz/review.php
?
attempt=147249&cmid=18279
When employees perform the same tasks in completely different ways, it is not only inefficient it is a liability
for your business. Standard operating procedures ensure that employees perform their job functions in a
safe and consistent manner.
One of the biggest misconceptions about standard operating procedures is that they will cause businesses
to become rigid and inflexible.
This article in the Harvard Business Review
does a great job of explaining how
systems in place for employees having to follow makes businesses more flexible.
How to Write a Standard Operating Procedure
How to Write a Standard Operating Procedure
Now you know what a standard operating procedure is and why you need one. However, you may be
wondering how you can actually go about creating your own. Standard operating procedures require a lot
of planning and preparation before you can even begin writing the document.
Here are five steps to follow when creating your own standard operating procedure:
Develop a list of your
Develop a list of your
business processes
business processes
To get started, have the managers talk to your employees about the duties they perform in their jobs every
day. This will allow them to begin creating a detailed list of processes that need standard operating
procedures.
From there, you can review the list with your managers and look for any redundancies. This list will serve as
a starting point for creating your standard operating procedure.
Plan the process
Plan the process
In this step, you will need to decide on a format for your process. Do you want it to be a step-by-step guide
or a
workflow diagram
? From there you can create a template. You will also need to decide how your
standard operating procedure will be made visible to your employees. Will you have a written copy posted
or will a copy be available online?
Talk with employees
Talk with employees
Now that you have your list of processes and you have created your template; you need to talk to your
employees. This is important because you can’t fully understand the process unless you have spoken with
the people who actually perform it on a daily basis. Only speaking with management is not enough.
Write and review the process
Write and review the process
Once you have spoken with your employees, immediately add your notes to the template. From there you
can review your standard operating procedure with employees once again and obtain input from your
managers. You should also determine who will be responsible for oversight and maintenance of the
standard operating procedure.
Keep in mind that all your standard operating procedures should read the same way while still distinctly
describing the functions of each area of your business.
Maintain the process
Maintain the process
Your work is not finished once the standard operating procedure is written! In order for it to remain relevant
and useful, you must maintain and update it at least once per year.
A written standard operating procedure not only lets your employee know how they should be doing their
job; it lets them know why. When you explain to employees why tasks are performed in a certain way, they
will be more likely to complete them.
Standard operating procedures are time-consuming to create at first, but the benefits are worth it. They will
save you a lot of time and frustration down the road.
Standard operating procedures are detailed, written instructions on how to perform a routine business
activity. They are easy to read and they explain every detail of the process being described. It is important
to keep in mind that a good standard operating procedure does not focus on what needs to be done but
rather how it should be done. A standard operating procedure is an effective tool that every business
should have.
Standard operating procedures will give you a better understanding of your business processes and help
you decide how to move forward. They will ensure that all employees are performing the business
processes in the same way.
Advantages to have SOP
Advantages to have SOP
Standard Operating Procedure (SOP)
Standard Operating Procedure (SOP) is a great tool for organisations to document and streamline their
business processes. SOPs are equally beneficial for start-ups, small, medium, and large organisations. It is a
great low-cost tool to transform an organisation from being a person-driven one to a process-driven one.
The purpose of this article is to highlight some of the unique benefits of developing SOPs for the
organisation.
Be it a new employee or an experienced employee, training with the aid of an SOP will sharpen their skills
and reduce defects or errors in their day-to- day activities
.
SOP conveys an organisation’s intention in a court-of-law. A well-developed SOP with supporting
documentations showing that the necessary trainings were imparted to the employee will only speak in
favour of the organisation in case of accidents.
SOPs clearly establish the roles and responsibilities of the staff working in various functions such as
manufacturing, procurement, sales, marketing, accounts, finance, legal, customer service, human
resources, administration etc. SOP introduces immense clarity in understanding one’s own job, eliminates
confusion among colleagues and avoids blame- gaming.
Typically, in organisations the employees working on the customer facing side may have less experience
and qualification. A well-crafted SOP will enable such organisations to deliver superior customer service
at low-cost.
2/4/2023, 2
:
02 p. m.
MEM07032 - THEORY - Use workshop machines for basic operations - PRE LEARNING: Attempt review
Página 3 de 58
https://baxter.edfibre.com/gradejet/mod/quiz/review.php
?
attempt=147249&cmid=18279
In organisations where they have multiple outlets or spread across a wider geography, SOP brings
consistency in their operations and clearly establishes the brand image in the consumer mind.
SOP identifies the process owners who are responsible to maintain the functioning of a process. It
becomes the responsibility of the process owners to continuously improve the SOP with best practices.
SOP helps in auditing a process for its validity and to find out the deviation between the documented and
actual performance.
SOP enables the process owners and process improvement experts to quickly get an understanding of
the current state of the process. SOP establishes the foundation for all process improvement efforts.
While expanding the capacity of an organisation or while commissioning an additional production line,
SOP comes handy to estimate the quantum of work especially the factors of production such as men,
machine, material and money required.
SOP demonstrates a company’s sound process orientation and their commitment towards process
improvement, which is appreciated by the clients and boost your credibility, especially in a B2B
environment.
SOP is a tool for communicating the organisations expectation in terms of the standards of performance
with reference to functions, processes and activities.
When employees follow SOP, which is thoroughly evaluated for its best practices and safe operation, it
tremendously increases the safety and security of not only the employees who are performing the
activities, but also others in the vicinity.
Organisations that establish sound SOPs for their functions and processes can have a good negotiation
with the insurance companies as it mitigates the exposed risk and its degree.
SOP provides a global view of processes helpful in identifying opportunities for small or large
automations in processes.
A good document to capture and consolidate the business rules that need to be followed while
performing a transaction or operation.
For public safety and national security, companies in industries such as pharma, healthcare, insurance,
banking etc. are mandated by the respective national governments or regulatory bodies to establish
and follow SOPs.
In case of a long-repeated processes, human memory is limited and there is a possibility of missing
certain activities. SOP along with a check list will be of immense help in these situations.
When companies want to implement an ERP system or to move from a legacy system to a new system,
SOP will help the software implementers to understand the organisations processes with greater
accuracy. In the absence of SOPs, the software implementers must go through a phase of numerous
meetings with the stakeholders and eventually create such documents that represent the organisational
processes.
1.1
Comply with work health and safety (WHS) requirements at all times
1.1
Comply with work health and safety (WHS) requirements at all times
Workplace health and safety management system
Workplace health and safety management system
A workplace health and safety management system are a set of policies, procedures and plans that
systematically manages health and safety at work and can help to minimise the risk of injury and illness
from workplace operations.
A systems-based approach
A systems-based approach
As an employer, you can choose to establish a health and safety management system to help meet your
duties and responsibilities under the Work Health and Safety Act 2011
Well-designed policies and procedures help organisations comply with work health and safety legislation
and regulations.
However, a workplace health and safety management system is much more than simply having safety-
related forms and policies in place and documented procedures. Rather, it is about achieving the
measures and contents of the safety documentation in an ongoing and managed way.
A systems-based approach is far more effective in protecting people from harm and meeting safety goals
than a system which relies on documentation alone. This is because a workplace health and safety
management system:
is evolving and continuously improving
uses feedback to manage and improve safety related outcomes
builds on existing health and safety processes
integrates with other management systems
provides for more informed decision making
strengthens corporate culture and demonstrates due diligence.
The Australian standard
The Australian standard
The Australian standard, AS/NZS ISO 45001:2018 (Occupational health and safety management systems -
Requirements with guidance for use):
specifies the conditions for a workplace health and safety management system
gives guidance on its use.
The standard aims to enable organisations to provide safe and healthy workplaces by preventing work-
related injury and illness, and proactively improve its work health and safety performance. Like some other
Australian standards dealing with management systems, AS/NZS ISO 45001:2018 is closely aligned with the
relevant international standards, ISO 9000 series, dealing with similar issues.
How to develop a health and safety system
How to develop a health and safety system
Every organisation will find that it has some elements of a workplace health and safety management
system in place.
What is less common is the linking of these elements into a coordinated overall system to improve work
health and safety performance.
Your preview ends here
Eager to read complete document? Join bartleby learn and gain access to the full version
- Access to all documents
- Unlimited textbook solutions
- 24/7 expert homework help
2/4/2023, 2
:
02 p. m.
MEM07032 - THEORY - Use workshop machines for basic operations - PRE LEARNING: Attempt review
Página 4 de 58
https://baxter.edfibre.com/gradejet/mod/quiz/review.php
?
attempt=147249&cmid=18279
1.
Start by comparing the intent behind each element in the Australian standard AS/NZS ISO 45001:2018
with the management practices and procedures your organisation currently uses
2.
Think about what a mature work health and safety management system looks like and consider your
organisation—it should be risk focused, fit for purpose, improved through learning and review, and be
sensitive to the way people behave.
Commitment and accountabilities
Commitment and accountabilities
Senior management is visibly involved and committed.
Organisational structures and accountabilities for health and safety are in place.
There are clearly assigned work health and safety responsibilities at various management levels.
Robust worker consultative arrangements are an essential element.
Consultation occurs with affected workers on work health and safety matters.
Consultation
Consultation
Work Health and Safety Consultation, Cooperation and Coordination Code of Practice
– practical
guidance for employers on how to effectively consult with workers.
Health and safety aspects are considered in the design of work and throughout the product and service
life cycle.
Design of work
Design of work
Good work design
is put into practice.
A program of workplace inspections is in place.
Incidents are investigated and reported.
Identification and monitoring of hazards and emerging risk are in place.
First aid arrangements and health monitoring appropriate to the health risks at the workplace
Hazard and risk management
Hazard and risk management
How to Manage Work Health and Safety Risks Code of Practice
– practical guidance for people who have
duties under the Work Health and Safety Act 2011 and Regulations 2011 to manage risks to health and
safety.
Risk Management: A Snapshot (PDF, 126.0 KB)
– key things to consider when managing work health and
safety risks.
Preventing harm and injury at work
– includes information on biological, chemical, ergonomic and
physical hazards and how to manage risks in the workplace.
A continuing mechanism for work health and safety management system monitoring and evaluation.
Safety performance criteria are identified and monitored, and data is collected and analysed.
Health and safety committees
Health and safety committees
Under the Work Health and Safety Act 2011 (WHS Act) a health and safety committee bring together workers
and management to develop and review health and safety policies and procedures for the workplace.
When a health and safety representative, or five or more workers, at a workplace request a health and
safety committee be created, the 'person conducting a business or undertaking' (
PCBU
), who is usually the
employer, must create one within two months of the request.
Functions of a health and safety committee are:
facilitate cooperation between the PCBU and workers in instigating, developing and carrying out
measures designed to ensure the workers’ health and safety at work
assist in developing standards, rules and procedures relating to health and safety
comply with functions prescribed by regulations
carry out any other functions agreed between the PCBU and the health and safety committee.
Monitoring and evaluation
Monitoring and evaluation
Work Health and Safety Barriers and Remedies checklist (PDF, 169.5 KB)
– includes likely barriers affecting
safe and healthy work and some suggested remedies.
National Audit tool (PDF, 322.2 KB)
– provides a review of the elements that are considered during a work
health and safety management system audit.
Proof that health and safety policies and procedures are documented, implemented and maintained.
A policy which focuses on workplace health and safety is central to all operations and suits the nature
and scale of your organisation’s risks.
Procedures are in place which set out the steps workers should follow to perform specific work activities
safely and meet organisational policies and legislation.
Emergency management and response procedures are in place.
Policies and procedures are available to all staff, such as on staff noticeboards and intranet site.
Policies and procedures
Policies and procedures
A policy is a course or principle of action. Common features of good policy are it:
states matter of principle
has a focus on action, stating what is to be done and by who
is an authoritative statement, made by a person or body with the power to do so.
A procedure sets out the steps to be followed for work activities. You must consult with affected workers
when developing procedures for resolving work health and safety issues, consulting with workers on work
health and safety, monitoring worker health and workplace conditions, and providing information and
training.
AS/NZS ISO 45001:2018 Occupational health and safety management systems – requirements with
guidance for use. Australian Standards may be purchased through selected bookstores and online.
Writing a Health and Safety Policy
– guidelines to writing a work health and safety policy, prepared by
Health and Safety Executive UK though laws mentioned do not relate to Australia.
Safe Work Procedures advice sheet
– examples and guidance by Worksafe Queensland on preparing
safe work procedures.
Manage risks in the workplace
Manage risks in the workplace
2/4/2023, 2
:
02 p. m.
MEM07032 - THEORY - Use workshop machines for basic operations - PRE LEARNING: Attempt review
Página 5 de 58
https://baxter.edfibre.com/gradejet/mod/quiz/review.php
?
attempt=147249&cmid=18279
The ‘person conducting a business or undertaking’ (
PCBU
), who is usually the employer, must manage risks
to health and safety by eliminating risks as much as is reasonably practicable.
Those responsible for preventing and managing risks include:
employers
the self-employed
principal contractorsanyone who manages or controls a workplace
designers
manufacturers
importers and suppliers of plant, substances or structures that are used at work.
This applies to all types of work and all workplaces that are covered by the Work Health and Safety Act 2011
(WHS Act).
Managing work health and safety risks within a workplace involves the elements of governance, prevention,
response, and recovery.
Governance
Governance
Governance is the framework, procedures, policies and processes that organisations use to manage work
health and safety duties, functions and operations.
One of the primary duties of a PCBU is to:
develop organisational work health and safety policies
define key work health and safety roles and responsibilities
address obligations to consult
define arrangements for working with Comcare.
Developing a culture that promotes workplace health and safety also belongs in this category.
Prevention
Prevention
Prevention is always better than cure! At the centre of an effective preventative system is compliance with
work health and safety obligations and stopping hazards entering the workplace. Having policies and
procedures to effectively manage risks and hazards allows an organisation to identify and resolve hazards
before they cause injury or illness to workers.
Strategies to prevent
physical hazards
and
ergonomic hazards
include:
promoting health and safety in
workplace design
conducting work health and safety audits
analysing safety data
providing or attending
work health and safety training and education
setting up mandatory internal hazard reporting
developing and following hazard specific policies and procedures.
Organisations should consider
psychosocial hazards
in the same way as other health and safety hazards
and risks. A commitment to preventing psychosocial hazards in the workplace should be included in health
and safety policies.
Response
Response
If a safety incident takes place, the organisation must take steps to remove the hazard that caused the
incident. It should also implement changes to stop the incident from happening again.
The organization’s response documentation must include information on:
incident investigation
incident notification requirements
emergency preparedness and response
first aid policies and procedures.
Recovery
Recovery
When a worker is ill or injured, the employer has responsibilities under both the
Safety
Rehabilitation and
Compensation Act 1988
and
Work Health and Safety Act 2011
.
These responsibilities are usually addressed by a
rehabilitation management system
that manages
workplace injury or illness.
Employees and other workers
Employees and other workers
Workers play an important role in helping keep the workplace safe and setting the workplace health and
safety standards.
The role of workers
The role of workers
Definition of a worker
Definition of a worker
Under the
Work Health and Safety Act 2011
(WHS Act), a worker includes any person who works, in any
capacity, in or as part of the business or undertaking.
You are a worker under health and safety legislation if you are an:
employee
independent contractor or subcontractor (or their employee)
employee of a labour hire company
outworker, such as a home-based worker
apprentice or trainee
a student gaining work experience
volunteer.
Duties of a worker
Duties of a worker
As a worker, you have duties and responsibilities under the
Work Health and Safety Act
2011
(WHS Act).
Duties and responsibilities include:
taking reasonable care for your own health and safety
taking reasonable care that your actions or omissions do not harm the health and safety of others
2/4/2023, 2
:
02 p. m.
MEM07032 - THEORY - Use workshop machines for basic operations - PRE LEARNING: Attempt review
Página 6 de 58
https://baxter.edfibre.com/gradejet/mod/quiz/review.php
?
attempt=147249&cmid=18279
reporting any hazards or work practices you feel may be unsafe
complying with any reasonable instruction, policy or procedure relating to health and safety in the
workplace, such as
o
follow safety manuals and procedures
o
participate in safety training
o
wear personal protective equipment
o
exercise a level of care and responsibility in your work
reinforcing and influencing safety behaviours in your workplace
working with management to identify safety problems and find solutions
understanding and following internal incident reporting processes
acting upon health and safety matters where you have control or influence
working with colleagues to promote health and safety so that it becomes a part of your daily work
contributing to quality data and information which measures health and safety compliance over time –
this can be used to identify trends and target preventative actions and improvements.
Liabilities
Liabilities
If you do not follow the required procedures, you could face non-compliances under the
Work
Health and
Safety Act 2011
(WHS Act).
This may include penalties such as criminal prosecution, fines and jail sentences.
Communicating and consulting effectively
Communicating and consulting effectively
Importance of communication and consultation
Importance of communication and consultation
Communication and consultation are vital to building a strong health and safety culture and minimizing
injury and illness in the workplace.
This process involves:
talking about issues
listening to and raising concerns
understanding your role
seeking information and sharing views
discussing issues in a timely manner
considering what is being said before decisions are made
attending scheduled meetings.
Contributing to consultation as a worker
Contributing to consultation as a worker
You can contribute by:
speaking at team meetings
talking with your work group
giving feedback on policy and procedures when asked.
Participation in consultation provides you with an opportunity to:
think constructively about health and safety issues that affect you
contribute ideas for improvement
work as a team in implementing good workplace safety practices.
When you should be consulted
When you should be consulted
The ‘person conducting business or undertaking’ (PCBU) is required to consult with you on any matters that
may directly affect your health and safety. If you are a HSR or represented by an HSR, then you or your HSR,
must also be included in the consultation.
There are number of situations when your manager and senior leaders are required to consult with you.
They include:
identifying hazards and assessing risks arising from work
making decisions about ways to eliminate or minimise those risks
making decisions about the adequacy of facilities for the welfare of workers
proposing changes that may affect the health and safety of workers
making decisions about the procedures for resolving health and safety issues
monitoring the health of workers or workplace conditions, information and training or consultation with
workers
carrying out any other activity prescribed by the WHS Regulations.
When the PCBU consults with you on a health and safety issue, you need to consider the information
provided and give feedback through your HSR.
Barriers to effective consultation
There are many barriers to how we communicate and consult with each other in the workplace. Finding the
right time and delivering messages in the right way can be a challenge. Workers and HSRs should establish
a relationship with their manager that encourages open and honest discussion and mutual trust.
Consultation often fails due to:
lack of clarity of message
absence of emotional resonance in your message
inaccurate targeting
poor timing
no genuine feedback process.
Improving and promoting communication
Improving and promoting communication
To ensure that communication is effective in your workplace, you should use all the available and
established channels to provide your ideas and concerns about health and safety.
Ways to contribute to effective communication include:
contribute at meetings
seek information from your intranet
use emails to clarify, and provide a two-way communication approach
establish an open and constructive approach to talking to your colleagues and managers
Your preview ends here
Eager to read complete document? Join bartleby learn and gain access to the full version
- Access to all documents
- Unlimited textbook solutions
- 24/7 expert homework help
2/4/2023, 2
:
02 p. m.
MEM07032 - THEORY - Use workshop machines for basic operations - PRE LEARNING: Attempt review
Página 7 de 58
https://baxter.edfibre.com/gradejet/mod/quiz/review.php
?
attempt=147249&cmid=18279
consider the barriers to communication in remote and isolated work locations (e.g shift work, working on
your own, isolated by distance or team support, working from home)
make contact daily where possible.
Talking to the health and safety representative (HSR)
Talking to the health and safety representative (HSR)
Your
health and safety representative
(HSR) is your main point of contact regarding health and safety
matters, so inform them of any concerns or safety issues you may have. HSRs represent workers in relation
to health and safety matters affecting workers.
Having your HSR represent your work group can help because:
a HSR is likely to understand your views and concerns
HSRs can be trained in work health and safety and in how to represent you
a coordinated and formal approach to raising ideas and concerns with your ‘person conducting
business or undertaking’
(PCBU)
can have greater impact
HSRs have rights and powers to take action on your behalf.
Right to cease unsafe work
Right to cease unsafe work
You may cease, or refuse to carry out, any work that you believe poses a serious risk to your health or safety.
This is your right and responsibility as a worker.
If you cease or refuse to carry out any work for this reason, you must notify the relevant ‘person conducting
a business or undertaking’
(PCBU)
as soon as possible.
A PCBU can redirect you to carry out suitable alternative work at the same or another workplace. The
suitable alternative work must be safe and appropriate for you until you can resume normal duties.
Rehabilitation and return to work
Rehabilitation and return to work
If you sustain a work-related injury or illness, you should:
find out about your organisation’s rehabilitation policy
let your supervisor or rehabilitation case manager know if you are going to be away from work for an
extended period because of your work-related injury
undergo an assessment for rehabilitation if required
talk to your rehabilitation case manager about your obligations and rights regarding rehabilitation
participate in your rehabilitation program
talk to your rehabilitation case manager or rehabilitation provider if you have any concerns about your
return to work plan.
Understanding WHS and your responsibilities
Understanding WHS and your responsibilities
All employees have certain responsibilities to ensure the provision and maintenance of a workplace that is
without risk to the health and safety of workers, other people at the workplace or those impacted by the
work everyone do
As part of this, all employees must ensure the provision and maintenance of:
1.
a work environment without risk to health and safety
2.
safe plant and structures
3.
safe systems of work
4.
safe use, handling and storage of plant, structures, and substances
5.
adequate facilities for the welfare of workers at work
6.
information, training, instruction, or supervision that is necessary to protect all persons from risks to
their health and safety arising from work carried out by the organization, and
7.
regular monitoring of workplace conditions and the health of workers for the purpose of preventing
illness or injury.
All employees must also ensure:
that all the workers they engage to perform duties on behalf of organization
report all WHS Incidents or concerns occurring
comply with all reasonable requests for WHS information from personnel, including the provision of
documents that demonstrate how you manage risks while on the job and evidence that you are meeting
your WHS responsibilities, and
understand that if at any time organization are concerned you or your workers are not implementing a
safe system of work or the health and safety of workers or others is at risk, Organization may require the
job site or activity to be closed.
Safety Precautions:
Safety Precautions:
General Machine Shop:
General Machine Shop:
1: Be sure that all lathe and milling machine or the machines have effective and properly working guards
that are always in place where machines are operating.
2: Replace lathe or milling machine’s guards immediately after any repair.
3: Before using lathe or milling machine, do not attempt to oil, clean, adjust or repair any machine while it is
running, stop the machine and lock the power switch in the off position.
4: Even after the power is off, do not leave any machine until it has stopped running. Someone else may
notice that it is still in motion and be injured.
5: Do not operate any machine unless authorized, to do so by the instructor or under his supervision. 6: Do
not try to stop the machine with your hand or body.
7: Always see that work and cutting tools on any machine are clamped securely before starting.
8: Keep the floor clean of metal chips or curls and waste pieces, put them in container provided for such
things.
9: Do not operate machinery when the instructor is not in the workshop.
10: When working with another worker only one should operate machine or switches. 11: Do not rest against
the machine.
12: Concentrate on the work and do not talk unnecessary while operating machine. 13: Do not talk to others
when they are operating a machine.
14: Get first aid immediately for any injury.
2/4/2023, 2
:
02 p. m.
MEM07032 - THEORY - Use workshop machines for basic operations - PRE LEARNING: Attempt review
Página 8 de 58
https://baxter.edfibre.com/gradejet/mod/quiz/review.php
?
attempt=147249&cmid=18279
15: Be sure you have sufficient light to see clearly check with the supervisor if you do not enough.
Clothing and Safety Equipment:
Clothing and Safety Equipment:
1: Always wear safety glasses, or face shields designed for the type of the work operating any machine
2: Wear safety shoes if heavy work is being done.
3: Wear clothing suited for the job, wear shoes with thick soles.
4: Do not wear rings, watches, bracelets or other jewelry that could get caught in moving machinery.
5: Do not wear neck ties or loose turn clothing of any kind.
6: Wear shirts or uppers with sleaves cut off or rolled above the elbows.
7: Always remove gloves before turning on or operating a machine. If material is rough and sharp, then
gloves must be workplace or handle material with machine turned off.
House Keeping:
House Keeping:
1: Keeping floor free of oil, grease, or any other liquid. Clean up spilled liquid immediately they are sleeping
hazards.
2: Aisles should be clear, at all time to avoid tripping of other accident.
3: Store materials in such a way that they cannot become tripping hazards.
4: Do not leave tools or work on the table of a machine even if the machine in not turning. Tools or work may
fall off and cause the fact of injury.
5: Put tools always when not in use. 6: Place the scrap box.
1.1
1.1
Use appropriate personal protective equipment (PPE) in accordance
Use appropriate personal protective equipment (PPE) in accordance
with SOPs
with SOPs
A Safe Work Procedure (SWP) or Standard Operating Procedure (SOP)
documents
the risks associated
with a work task and lists the appropriate risk control measures into a sequence of steps for performing the
task or activity safely. SWP's are most effective when developed in consultation with your workers.
SOP’s provide information to assist your workers to perform tasks safely. These procedures can also assist in
the training and orientation of new workers in the hazards of the task being performed, as well as providing
your workers with the preferred way to safely perform the task/activity. They are also a useful tool when
training and supervising your workers, and when responding to incident reports and changes in the
workplace.
SAFETY AND PERSONAL PROTECTIVE EQUIPMENT
SAFETY AND PERSONAL PROTECTIVE EQUIPMENT
All safety equipment and personal protective equipment must meet an approved standard, generally an
Australian Standard. The clothing and personal protective equipment must be heat resistant.
If you receive a workplace injury, seek treatment straight away and report the incident to you supervisor
immediately. You may think that the injury is not that important, but it may lead to complications further
down the track.
Apparel
Apparel
When working in the welding and fabrication industry, you need to wear either coveralls or work- shirt and
pants. Wearing the incorrect apparel will result in arc burn (explained later). Wearing short sleeved apparel
and short pants will expose the body to these and other types of burns.
Coveralls
Coveralls
Work shirts and pants
Work shirts and pants
Gloves
Gloves
Long leather gloves are used y-fuel gas welding manual and riggers gloves are used for handling material.
Many people use riggers gloves for oxy-fuel gas welding, this is an incorrect technique as riggers gloves are
shorter than the long leather gloves and do not provide protection against burns on the wrist area of the
arm
Short rubber gloves is good for use in the activities that involved with sharp material
Welding gloves
Thin workshop gloves
Welding gloves
Thin workshop gloves
Two photos below show burns from radiant welding, one is of burns to the neck and the other is to the arm
due to not wearing gloves.
2/4/2023, 2
:
02 p. m.
MEM07032 - THEORY - Use workshop machines for basic operations - PRE LEARNING: Attempt review
Página 9 de 58
https://baxter.edfibre.com/gradejet/mod/quiz/review.php
?
attempt=147249&cmid=18279
Eye protection
Eye protection
Eye protection is critical to ensure that your eyes are protected from foreign bodies entering your eyes and
to protect them from harmful rays. Oxy-fuel gas goggles must be worn to protect the eyes from, heat, rays
and foreign objects from entering the eyes while welding. A clear face shield adds extra protection.
Clear safety glasses
Oxy-fuel gas cutting and welding goggles
Full face shield
Clear safety glasses
Clear safety glasses
These glasses are as a rule generally worn in the workshop to protect the eyes from foreign bodies entering
them. They will also help reduce the effects of welding rays on the eyes.
Shown below is a small piece of iron has lodged near the margin of the cornea, this accident was the result
of not wearing proper eye protection
Leather jackets and leather aprons
Leather jackets and leather aprons
Leather jackets and aprons provide additional protection when welding, particularly a leather jacket when
welding over head
Work boots
Work boots
In the welding and fabrication industry there is the chance that you will drop something heavy on your toes,
so it is important to protect them. Your work boots should have toe protection made either of steel or a
composite material to protect them.
Slip on boots
Lace up boots
Hearing protection
Hearing protection
It is important that hearing protection is worn when working in the welding and fabrication industry. The
noise level is generally above what is acceptable as safe for normal noise that will not affect you hearing.
Shown above are the two type of hearing protection, ear plugs and muffs. Ear plugs and muffs come in a
variety of shapes and sizes, choose the one that feel most comfortable for you.
The major problem with hearing loss is that it slowly creeps up on you; you do not notice it until the damage
has been done and you hearing has been irreversibly damaged.
Ear plugs
Ear muffs
Others PPE at workshop
Others PPE at workshop
Shown below is a list of additional personal protective equipment that may be useful when performing your
work tasks
Safety Glasses
Steel cap boots
Close fitting clothing
Your preview ends here
Eager to read complete document? Join bartleby learn and gain access to the full version
- Access to all documents
- Unlimited textbook solutions
- 24/7 expert homework help
2/4/2023, 2
:
02 p. m.
MEM07032 - THEORY - Use workshop machines for basic operations - PRE LEARNING: Attempt review
Página 10 de 58
https://baxter.edfibre.com/gradejet/mod/quiz/review.php
?
attempt=147249&cmid=18279
Keep long hair protected
Keep your work area clean
Clean up spills immediately
Leather sleeves
Leather spats
Visible safety vest
Hard hat
Face mask
Respirator
1.1
Identify job requirements from specifications, sketches, job sheets or
1.1
Identify job requirements from specifications, sketches, job sheets or
work instructions
work instructions Specification
Specification
A specification often refers to a set of documented requirements to be satisfied by a material, design,
product, or service.
Engineering standards and specifications
Engineering standards and specifications
Standards, codes, specifications are extremely important - often essential - technical documents in
engineering and related technical fields. It is usually a formal document that establishes
uniform engineering or technical criteria, methods, processes and practices.
Standards and Codes
Standards and Codes
Standards, codes, specifications are extremely important - often essential - technical documents in
engineering and related technical fields.
STANDARDS
STANDARDS: a technical standard is an established norm or requirement. It is usually a formal document
that establishes uniform engineering or technical criteria, methods, processes, and practices. The
documents prepared by a professional group or committee which are believed to be good and proper
engineering practices, and which contain mandatory requirement.
CODES
CODES: a code is a set of rules and specifications or systematic procedures for design, fabrication,
installation, and inspection methods prepared in such a manner that it can be adopted by legal
jurisdiction. Codes can be approved by local, state, or federal governments and can carry the force of law.
The main purpose of codes is to protect the public by setting up the minimum acceptable level of safety for
buildings, products, and processes.
Purpose
Purpose
The purpose of this introduction to specifications for design is
(1)
to make users aware of various standards which may be considered during the design process and
(2)
to assist users in finding the standards needed for a specific design project.
Specifications are agreed upon defined requirements for a product
Specifications are a type of Standard defined by a governing body
Specifications may have embedded drawings but may focus more on text
There are effectively two types of specifications.
Design or Product Specifications (what is wanted)
Application Specifications (how something is to be done to achieve a specific goal)
Data sheets share some common points with specifications sheets
Where do Specifications appear on a drawing?
Where do Specifications appear on a drawing?
2/4/2023, 2
:
02 p. m.
MEM07032 - THEORY - Use workshop machines for basic operations - PRE LEARNING: Attempt review
Página 11 de 58
https://baxter.edfibre.com/gradejet/mod/quiz/review.php
?
attempt=147249&cmid=18279
The treatment or coating that the component is finished to is stated in the title block. If the process is a
company or military standard that is often followed e.g. the aircraft industry, NASA, The Australian Army,
then reference to a standard data sheet is made. This slide shows an open ended and overly basic material
and finish specification that are both prone to misinterpretation.
Design or Product Specification
Design or Product Specification
A design or product specification describes the key points or requirements for a final design not how to
achieve it.
Application Specifications provide a sequential presentation of functions that need to be carried out to
achieve a goal. The key difference between Performance and Application Specifications is that
Performance specifications define a goal with no guidance on how this is achieved. Whereas Application
Specifications define a step by step set of instructions which lead to a common goal.
Data Sheets
Data Sheets
A data sheet provides a summary of the typical performance a component. Popular in the Electronics
Industry for defining components.
Sketch (drawing)
Sketch (drawing)
A sketch is a rapidly executed freehand
drawing
that is not usually intended as a finished work. A sketch
may serve a number of purposes: it might record something that the artist sees, it might record or develop
an idea for later use or it might be used as a quick way of graphically demonstrating an image, idea or
principle.
Sketches can be made in any drawing medium. The term is most often applied to graphic work executed in
a dry medium such as silverpoint, graphite, pencil, charcoal or pastel.
Engineering Drawing and Sketching
Engineering Drawing and Sketching
One of the best ways to communicate one's ideas is through some form of picture or sketch. This is
especially true for the engineer. The purpose of this guide is to give the basics of engineering sketching and
drawing.
We will treat "sketching" and "drawing" as one. "Sketching" generally means freehand drawing. "Drawing"
usually means using drawing instruments, from compasses to computers to bring precision to the
drawings. Below Figure is a Machined Block. When manufacturer wants to product this product, then needs
to create different types of Sketches or drawings
The representation of the object in figure below is called an isometric drawing. This is one of a family of
three-dimensional views called pictorial drawings. In an isometric drawing, the object's vertical lines are
drawn vertically, and the horizontal lines in the width and depth planes are shown at 30 degrees to the
horizontal. When drawn under these guidelines, the lines parallel to these three axes are at their true (scale)
lengths. Lines that are not parallel to these axes will not be of their true length.
Any engineering drawing should show everything: a complete understanding of the object should be
possible from the drawing. If the isometric drawing can show all details and all dimensions on one drawing,
it is ideal. One can pack a great deal of information into an isometric drawing. However, if the object in
figure 2 had a hole on the back side, it would not be visible using a single isometric drawing. To get a more
complete view of the object, an orthographic projection may be used.
Orthographic or Multiview Drawing
Orthographic or Multiview Drawing
Imagine that having an object suspended by transparent threads inside a glass box, as in figure below.
2/4/2023, 2
:
02 p. m.
MEM07032 - THEORY - Use workshop machines for basic operations - PRE LEARNING: Attempt review
Página 12 de 58
https://baxter.edfibre.com/gradejet/mod/quiz/review.php
?
attempt=147249&cmid=18279
Then draw the object on each of three faces as seen from that direction. Unfold the box (figure 4) and have
the three views. We call this an "orthographic" or "multiview" drawing. Figure below shows the creation of an
orthographic multiview drawing.
Which views should one choose for a Multiview drawing? The views that reveal every detail about the
object. Three views are not always necessary; we need only as many views as are required to describe the
object fully. For example, some objects need only two views, while others need four. The circular object in
figure below requires only two views.
Dimensioning
Dimensioning
We have "dimensioned" the object in the isometric drawing in figure below. As a general guideline to
dimensioning, try to think that would make an object and dimension it in the most useful way.
Put in exactly as many dimensions as are necessary for the craftsperson to make it -no more, no less. Do
not put in redundant dimensions. Not only will these clutter the drawing, but if "tolerances" or accuracy
levels have been included, the redundant dimensions often lead to conflicts when the tolerance allowances
can be added in different ways.
Repeatedly measuring from one point to another will lead to inaccuracies. It is often better to measure from
one end to various points. This gives the dimensions a reference standard. It is helpful to choose the
placement of the dimension in the order in which a machinist would create the part. This convention may
take some experience.
Sectioning
Sectioning
There are many times when the interior details of an object cannot be seen from the outside.
An isometric drawing that does not show all details.
Your preview ends here
Eager to read complete document? Join bartleby learn and gain access to the full version
- Access to all documents
- Unlimited textbook solutions
- 24/7 expert homework help
2/4/2023, 2
:
02 p. m.
MEM07032 - THEORY - Use workshop machines for basic operations - PRE LEARNING: Attempt review
Página 13 de 58
https://baxter.edfibre.com/gradejet/mod/quiz/review.php
?
attempt=147249&cmid=18279
We can get around this by pretending to cut the object on a plane and showing the "sectional view". The
sectional view is applicable to objects like engine blocks, where the interior details are intricate and would
be very difficult to understand through the use of "hidden" lines (hidden lines are, by convention, dotted) on
an orthographic or isometric drawing.
Imagine slicing the object in the middle:
"Sectioning" an object.
Sectioning the object in figure 8.
Take away the front half and what have is a full section view.
Sectioned isometric and orthogonal views.
The cross-section looks like figure when it is viewed from straight ahead.
Drawing Tools
Drawing Tools
To prepare a drawing, one can use manual drafting instruments or computer-aided drafting or design, or
CAD. The basic drawing standards and conventions are the same regardless of what design tool use to
make the drawings. In learning drafting, we will approach it from the perspective of manual drafting. If the
drawing is made without either instruments or CAD, it is called a freehand sketch.
Drawing Tools.
"Assembly" Drawings
"Assembly" Drawings
An isometric view of an "assembled" pillow-block bearing system is shown in figure. It corresponds closely
to what see when viewing the object from a particular angle. We cannot tell what the inside of the part
looks like from this view.
We can also show isometric views of the pillow-block being taken apart or "disassembled”. This allows
everyone to see the inner components of the bearing system. Isometric drawings can show overall
arrangement clearly, but not the details and the dimensions.
Pillow-block (Freehand sketch).
2/4/2023, 2
:
02 p. m.
MEM07032 - THEORY - Use workshop machines for basic operations - PRE LEARNING: Attempt review
Página 14 de 58
https://baxter.edfibre.com/gradejet/mod/quiz/review.php
?
attempt=147249&cmid=18279
Disassembled Pillow-block.
Cross-Sectional Views
Cross-Sectional Views
A cross-sectional view portrays a cut-away portion of the object and is another way to show hidden
components in a device.
Imagine a plane that cuts vertically through the center of the pillow block as shown in figure. Then imagine
removing the material from the front of this plane, as shown in figure.
Pillow Block.
Pillow Block.
This is how the remaining rear section would look. Diagonal lines (cross-hatches) show regions where
materials have been cut by the cutting plane.
This cross-sectional view (section A-A, figure), one that is orthogonal to the viewing direction, shows the
relationships of lengths and diameters better. These drawings are easier to make than isometric drawings.
Seasoned engineers can interpret orthogonal drawings without needing an isometric drawing, but this
takes a bit of practice.
The top "outside" view of the bearing is shown in figure 18. It is an orthogonal (perpendicular) projection.
Notice the direction of the arrows for the "A-A" cutting plane.
The top "outside" view of the bearing.
Half-Sections
Half-Sections
A half-section is a view of an object showing one-half of the view in section, as in figures below.
2/4/2023, 2
:
02 p. m.
MEM07032 - THEORY - Use workshop machines for basic operations - PRE LEARNING: Attempt review
Página 15 de 58
https://baxter.edfibre.com/gradejet/mod/quiz/review.php
?
attempt=147249&cmid=18279
Full and sectioned isometric views.
Front view and half section.
The diagonal lines on the section drawing are used to indicate the area that has been theoretically cut.
These lines are called
section lining
or
cross-hatching
. The lines are thin and are usually drawn at a 45-
degree angle to the major outline of the object. The spacing between lines should be uniform.
A second, rarer, use of cross-hatching is to indicate the material of the object. One form of cross- hatching
may be used for cast iron, another for bronze, and so forth. More usually, the type of material is indicated
elsewhere on the drawing, making the use of different types of cross-hatching unnecessary.
Half section without hidden lines.
Usually hidden (dotted) lines are not used on the cross-section unless they are needed for dimensioning
purposes. Also, some hidden lines on the non-sectioned part of the drawings are not needed (figure) since
they become redundant information and may clutter the drawing.
Sectioning Objects with Holes, Ribs, Etc.
Sectioning Objects with Holes, Ribs, Etc.
The cross-section on the right of figure is technically correct. However, the convention in a drawing is to
show the view on the left as the preferred method for sectioning this type of object.
Cross section.
Dimensioning
Dimensioning
The purpose of dimensioning is to provide a clear and complete description of an object. A complete set of
dimensions will permit only one interpretation needed to construct the part. Dimensioning should follow
these guidelines.
1.
Accuracy: correct values must be given.
2.
Clearness: dimensions must be placed in appropriate positions.
3.
Completeness: nothing must be left out, and nothing duplicated.
4.
Readability: the appropriate line quality must be used for legibility.
The Basics: Definitions and Dimensions
The Basics: Definitions and Dimensions
The dimension line is a thin line, broken in the middle to allow the placement of the dimension value, with
arrowheads at each end (figure).
Your preview ends here
Eager to read complete document? Join bartleby learn and gain access to the full version
- Access to all documents
- Unlimited textbook solutions
- 24/7 expert homework help
2/4/2023, 2
:
02 p. m.
MEM07032 - THEORY - Use workshop machines for basic operations - PRE LEARNING: Attempt review
Página 16 de 58
https://baxter.edfibre.com/gradejet/mod/quiz/review.php
?
attempt=147249&cmid=18279
Dimensioned Drawing.
Dimensioned Drawing.
An arrowhead is approximately 3 mm long and 1 mm wide. That is, the length is roughly three times the
width. An extension line extends a line on the object to the dimension line. The first- dimension line should
be approximately 12 mm (0.6 in) from the object. Extension lines begin 1.5 mm from the object and extend 3
mm from the last dimension line.
A leader is a thin line used to connect a dimension with a particular area (figure).
Example drawing with a leader.
A leader may also be used to indicate a note or comment about a specific area. When there is limited
space, a heavy black dot may be substituted for the arrows, as in figure. Also in this drawing, two holes are
identical, allowing the "2x" notation to be used and the dimension to point to only one of the circles.
Where To Put Dimensions
Where To Put Dimensions
The dimensions should be placed on the face that describes the feature most clearly. Examples of
appropriate and inappropriate placing of dimensions are shown in figure.
Example of appropriate and inappropriate dimensioning.
To get the feel of what dimensioning is all about, we can start with a simple rectangular block. With this
simple object, only three dimensions are needed to describe it completely (figure). There is little choice on
where to put its dimensions.
Simple Object.
Simple Object.
We must make some choices when we dimension a block with a notch or cut out (figure). It is usually best
to dimension from a common line or surface. This can be called the datum line of surface. This eliminates
the addition of measurement or machining inaccuracies that would come from "chain" or "series"
dimensioning. Notice how the dimensions originate on the datum surfaces. We chose one datum surface in
figure, and another in figure. If we are consistent, it makes no difference. (We are just showing the top view).
Surface datum example.
2/4/2023, 2
:
02 p. m.
MEM07032 - THEORY - Use workshop machines for basic operations - PRE LEARNING: Attempt review
Página 17 de 58
https://baxter.edfibre.com/gradejet/mod/quiz/review.php
?
attempt=147249&cmid=18279
Surface datum example.
In figure we have shown a hole that we have chosen to dimension on the left side of the object. The Ø
stands for "diameter".
Exampled of a dimensioned hole.
When the left side of the block is "radiuses" as in figure, we break our rule that we should not duplicate
dimensions. The total length is known because the radius of the curve on the left side is
given. Then, for clarity, we add the overall length of 60 and we note that it is a reference (REF) dimension.
This means that it is not really required.
Example of a directly dimensioned hole.
Somewhere on the paper, usually the bottom, there should be placed information on what measuring
system is being used (e.g. inches and millimeters) and also the scale of the drawing.
Example of a directly dimensioned hole.
This drawing is symmetric about the horizontal centerline. Centerlines (chain-dotted) are used for
symmetric objects, and for the centre of circles and holes. We can dimension directly to the centreline, as in
figure. In some cases, this method can be clearer than just dimensioning between surfaces.
2/4/2023, 2
:
02 p. m.
MEM07032 - THEORY - Use workshop machines for basic operations - PRE LEARNING: Attempt review
Página 18 de 58
https://baxter.edfibre.com/gradejet/mod/quiz/review.php
?
attempt=147249&cmid=18279
Question
1
Complete
Marked out of
1.00
Question
2
Complete
Marked out of
1.00
Produce an isometric drawing
Produce an isometric drawing
Produce on A3 paper using drawing equipment, apply the ordinate method of construction to produce an
isometric drawing.
Accuracy, line work, lettering, dimensions, and cleanliness must be shown.
This is a 12 mm mild steel 250 plate. The rectangle and the square are to be spaced evenly on the drawing
sheet and the circle is to be placed centrally inside the rectangle.
Please upload photo (minimum-1 and maximum-3) of your work.
MEM07032 Q1.pdf
Review questions
Write detailed responses to the following questions
Write detailed responses to the following questions
1.
What does WHS stand for?
Work Health and Safety
2.
List some of the duties of the workers in the language (minimum 8)
As a worker, you have duties and responsibilities under the Work Health and Safety Act 2011 (WHS Act).
Duties and responsibilities include:
Taking reasonable care for your own health and safety
Taking reasonable care that your actions or omissions do not harm the health and safety of others
Reporting any hazards or work practices you feel may be unsafe complying with any
Reinforcing and influencing safety behaviours in your workplace
Working with management to identify safety problems and find solutions
Understanding and following internal incident reporting processes
Acting upon health and safety matters where you have control or influence
3.
Under the
Work Health and Safety Act 2011
(WHS Act), what is the Definition of a worker?
The role of workers Definition of a worker Under the Work Health and Safety Act 2011 (WHS Act), a worker
includes any person who works, in any capacity, in or as part of the business or undertaking. You are a
worker under health and safety legislation if you are an: employee independent contractor or
subcontractor (or their employee) employee of a labour hire company outworker, such as a home-based
worker apprentice or trainee a student gaining work experience volunteer.
4.
State three (3) safety precautions, relating to machine safety, which should be observed when using a
lathe.
Safety precautions, related to machine safety, when using a lathe are as follows:
1: Make sure all lathes and mills or machines have effective and properly functioning guards that are
always in place where the machines are operating.
2: Replace lathe or mill guards immediately after any repair.
3: Before using the lathe or milling machine, do not attempt to oil, clean, adjust or repair any machine while
it is running, stop the machine and lock the power switch in the off position.
Your preview ends here
Eager to read complete document? Join bartleby learn and gain access to the full version
- Access to all documents
- Unlimited textbook solutions
- 24/7 expert homework help
2/4/2023, 2
:
02 p. m.
MEM07032 - THEORY - Use workshop machines for basic operations - PRE LEARNING: Attempt review
Página 19 de 58
https://baxter.edfibre.com/gradejet/mod/quiz/review.php
?
attempt=147249&cmid=18279
Question
3
Complete
Marked out of
1.00
Information
Review questions
Write detailed responses to the following questions
Write detailed responses to the following questions
5.
List some PPE for mechanical shop (minimum 3)
Some PPE for mechanical shop is follows:
Apparel
Apparel:
When working in the welding and fabrication industry, you need to wear either coveralls or work- shirt and
pants. Wearing the incorrect apparel will result in arc burn (explained later). Wearing short sleeved apparel
and short pants will expose the body to these and other types of burns
Gloves
Gloves:
Long leather gloves are used y-fuel gas welding manual and riggers gloves are used for handling material.
Many people use riggers gloves for oxy-fuel gas welding, this is an incorrect technique as riggers gloves
are shorter than the long leather gloves and do not provide protection against burns on the wrist area of
the arm
Short rubber gloves is good for use in the activities that involved with sharp material
Work boots
Work boots:
In the welding and fabrication industry there is the chance that you will drop something heavy on your
toes, so it is important to protect them. Your work boots should have toe protection made either of steel or
a composite material to protect them.
6.
What is the Purpose of Job sheet or Work Instructions?
A specification often refers to a set of documented requirements to be satisfied by a material, design,
product, or service.
The purpose of this introduction to specifications for design is:
(1) to make users aware of various standards which may be considered during the design process and
(2) to assist users in finding the standards needed for a specific design project.
7.
What does a Job sheet or Work instructions describe?
A worksheet or work instructions describe the specifications about the requirements defined for a product,
these can have embedded drawings. A design or product specification describes the key points or
requirements for a final design, not how to achieve it. Application specifications provide a sequential
presentation of the functions that must be carried out to achieve an objective. The key difference between
performance and application specifications is that performance specifications define a goal without
guidance on how to achieve it. Whereas application specifications define a set of step-by-step
instructions leading to a common goal.
8.
What is the relationship between Processes, Procedures and Work Instructions?
The relationship between process, procedure and work instructions is that the Processes will be supported
if necessary by Procedures for mandatory legislative or regulatory compliance or company policies. And it
will be supported by Work Instructions to document the mandatory steps to follow in those activities that
require it.
9.
What are the 9 basic steps of writing Work Instructions?
The 9 basic steps of writing Work Instructions are follows:
1. Know exactly how to do the task.
2. Plan how to write steps in order.
3. Write instructions beginning with a verb.
4. Write each step as a small piece.
5. Include warnings as pre-steps.
6. Write the steps in logical order.
7. Review and edit instructions carefully.
8. Express steps in the positive.
9. Avoid expressing opinions, preferences, or choices.
Job sheets and work instructions
Job sheets and work instructions
A Job sheet can be defined as a document or a page that contains instructions to help an employee do
his/her job in the best way possible. It has details of what would be the time taken to perform the task and
the materials needed to do so.
Job sheets will save time invoicing customers. Completed jobs can be easily converted into invoices for
easy billing and emailed to the customer.
A Job sheet can also call work instruction.
A job sheet or Work Instruction usually is a document that provides specific instructions to carry out an
Activity. A job sheet or Work Instruction is a step by step guide to perform a single instruction. job sheet or
Work Instruction contains more detail than a Procedure and is only created if detailed step-by-step
instructions are needed.
Work Instructions are the “how you address satisfying the SOP” documents.
2/4/2023, 2
:
02 p. m.
MEM07032 - THEORY - Use workshop machines for basic operations - PRE LEARNING: Attempt review
Página 20 de 58
https://baxter.edfibre.com/gradejet/mod/quiz/review.php
?
attempt=147249&cmid=18279
Job sheet or Work instructions describe:
1. What is the activity is
2. Who performs it
3. When it is performed
4. How the activity is performed.
5. How safe the activity can be (include the risk control)
Purpose of Job sheet or Work Instructions
Purpose of Job sheet or Work Instructions
A work instruction is a tool provided to help someone to do a job correctly. This simple statement implies
that the purpose of the work instruction is quality and that the target user is the worker.
Unfortunately, in many workplaces, today’s work instructions have little connection with this fundamental
focus. Factories have encumbered work instructions with content that has been added to satisfy auditors,
lawyers, engineers, accountants and yes, even quality managers. We’ve piled on so much extraneous
material that we’ve lost sight of the intended purpose of work instructions.
ISO 9001 Processes, Procedures and Work Instructions
ISO 9001 Processes, Procedures and Work Instructions
ISO 9001:2015 has relaxed the strict requirement for quality management documentation. However, to
satisfy the remaining documentation requirements and to properly implement the Quality Management
System (QMS), ISO 9001 Processes, Procedures and Work Instructions are typically still employed.
Section 4.4 of the standard, titled Quality Management System and its Processes covers the general
requirements for work processes. Unfortunately, within the QMS planning and documentation realm, the
terms are often confused. Below we can find definitions of each of these terms with examples and links to
resources to help improving creation of the ISO 9001:2015 documentation.
The Relationship Between Processes, Procedures and Work Instructions
The Relationship Between Processes, Procedures and Work Instructions
When a company documents its QMS, it is an effective practice to identify their processes, procedures, and
work instructions clearly and concisely to explain and control how it meets the requirements of ISO
9001:2015. This begins with a basic understanding of the hierarchy of these terms and how to efficiently
categorize the workings of a management system within them. Simply put:
1. A process states what needs to be done and why
2. A procedure states how the process needs to be done
3. A work instruction explains how to carry out the procedure.
Consider a process as a high level, strategic method of control, in effect a summary of objectives,
specifications, and broad resources needed. The procedure adds more specifics such as responsibilities,
specific tools, methods, and measurement. And a work instruction is a step-by-step guideline to implement
the process and procedure, often segmented in some way to focus those who are doing the actual work.
How to Write Work Instructions
How to Write Work Instructions
Triggers
Triggers- identify any triggers required to start the activity.
Inputs
Inputs- describe any inputs required from other procedures/processes, department, etc.
Outputs
Outputs- describe the outputs generated by the Work Instruction.
Describe the detailed instructions for the work. Identify roles and responsibilities.
Give each activity its own title. One role activity. Do not combine two roles in the same step. Number each
step. Use consistent formatting. Document control-Version#, Date, Doc name, Detail of change, Review
date, etc.
9 basic steps of writing Work Instructions
9 basic steps of writing Work Instructions
1. Know exactly how to do the task.
2. Plan how to write steps in order.
3. Write instructions beginning with a verb.
4. Write each step as a small piece.
5. Include warnings as pre-steps.
6. Write the steps in logical order.
7. Review and edit instructions carefully.
8. Express steps in the positive.
9. Avoid expressing opinions, preferences, or choices.
Below are the samples of work instruction
2/4/2023, 2
:
02 p. m.
MEM07032 - THEORY - Use workshop machines for basic operations - PRE LEARNING: Attempt review
Página 21 de 58
https://baxter.edfibre.com/gradejet/mod/quiz/review.php
?
attempt=147249&cmid=18279
Information
SECTION 2 SET UP MACHINE
SECTION 2 SET UP MACHINE
2.1
2.1 Select appropriate machine and tools to meet work requirements
Select appropriate machine and tools to meet work requirements
Work requirements are the job qualifications and skills necessary for a certain position. Work requirements
are usually written in the form of a list that contains the most
important job qualifications, skills, and qualities that a candidate must possess in order to be able to
perform certain job duties.
The basic meaning of a job description is a list that manpower, machines and tools have which can be
used by for maintaining certain tasks along with some functions and responsibilities pertaining to a certain
position or machines to making the products.
Why is it Important to Understand and Review Job Description?
Why is it Important to Understand and Review Job Description?
In a company every employee always like to know what is really expected by them working in that
company from the management. Knowing a job description is a great way for the person to really
understand what the management wants them to do and how they are being evaluated in the company.
They also come to know how important and critical the job they are doing in the firm now is for the benefit
of the company and what are the characteristics required for the employees who are new. The second step
is to know what equipment and tools need to be selected for the job requirement. In most of the case the
company only take the job order based on what equipment and tools they currently have. Then the only
task for process worker is to select the available equipment and tools.
Some of the most used criteria when choosing a machine tool include the following:
production quantity,
machining type,
geometrical features of the machine,
complexity of the workpiece,
productivity
etc.
Mechanical Workshop: Equipment
Mechanical Workshop: Equipment
CNC Machining centre
Manual Lathe
CNC Lathe
Milling machines
Surface grinding
Welding facilities
3D Printing and Scanning
Your preview ends here
Eager to read complete document? Join bartleby learn and gain access to the full version
- Access to all documents
- Unlimited textbook solutions
- 24/7 expert homework help
2/4/2023, 2
:
02 p. m.
MEM07032 - THEORY - Use workshop machines for basic operations - PRE LEARNING: Attempt review
Página 22 de 58
https://baxter.edfibre.com/gradejet/mod/quiz/review.php
?
attempt=147249&cmid=18279
Vacuum forming
CNC Machining Centres
CNC Machining Centres
Used for the manufacture of fixtures and rigs for undergraduate and research projects these machine tools
are the workhorses of the mechanical workshop. These machine tools can be programmed by the following
means to machine most materials.
Conversational programming – Hurco have their own conversational programming feature called WinMax
which allows programming in a question and answer format using multiple choice and fill in the blank
questions. Operator prompts in plain English. No codes or computer languages are used.
DXF Transfer – this feature allows to quickly import the 2D data from a dxf file. This feature enables the
operator to select holes and machining operations, thereby creating a conversational program at the
control.
CAD/CAM – the mechanical workshop uses Alphacam software for milling. Part files can be imported into
our Alphacam system which enables the operator to generate tool paths for contouring, pocketing,
engraving and hole-drilling complex parts.
Manual lathes
Manual lathes
manual lathes are regularly used in the manufacture of prototype equipment used in undergraduate and
research projects.
CNC Lathe
CNC Lathe
This 5 – axis machine tool is complete with twin chucks and turrets. Each turret consists of 12 stations which
can carry live tooling with speeds of between 100-4500rpm. The machine uses a Fanuc based CNC control
system, OSP 7000L and programming is carried out manually at the console.
Conventional milling machines
Conventional milling machines
conventional milling machines are regularly used where a considerable amount of user interaction with the
work piece is required. They are also used where larger, more awkward work pieces need modification or
re-work or where the head of the machine needs to be tilted off to one side to machine an angle.
Your preview ends here
Eager to read complete document? Join bartleby learn and gain access to the full version
- Access to all documents
- Unlimited textbook solutions
- 24/7 expert homework help
2/4/2023, 2
:
02 p. m.
MEM07032 - THEORY - Use workshop machines for basic operations - PRE LEARNING: Attempt review
Página 23 de 58
https://baxter.edfibre.com/gradejet/mod/quiz/review.php
?
attempt=147249&cmid=18279
Surface grinding
Surface grinding
Used to produce ultra-flat surfaces on metallic materials, our Jones & Shipman surface grinder can
achieve surface finishes of 0.2
µ
m Ra. It is used for a wide variety of engineering projects such as;
The precision grinding of syringes used in electro-spraying
The precision grinding of parallel surfaces in press tooling
To achieve ultra- flat surfaces prior to the application of strain gauges used in undergraduate teaching
laboratories
Welding facilities
Welding facilities
The Dept. of Mechanical & Manufacturing Engineering has a dedicated welding bay where the following
types of welding are carried out.
MIG – Metal Inert Gas
TIG – Tungsten Inert Gas
Arc welding or Stick welding
Gas welding
3D Printing and Scanning
3D Printing and Scanning
Dimension 3D Printer and Roland 3D Laser Scanner
Dimension 3D Printer and Roland 3D Laser Scanner
The mechanical workshop staff have been providing a 3D prototyping service for over 15 years
and have a wealth of experience in this process. Situated in the “Build Base” our Dimension 3D Printer uses
the fusion deposition modelling process (FDM) to manufacture prototypes for research and undergraduate
projects. We also have Roland Picza 3D Laser Scanner which is particularly suitable for the reverse
engineering of components and models.
Vacuum forming
Vacuum forming
Your preview ends here
Eager to read complete document? Join bartleby learn and gain access to the full version
- Access to all documents
- Unlimited textbook solutions
- 24/7 expert homework help
2/4/2023, 2
:
02 p. m.
MEM07032 - THEORY - Use workshop machines for basic operations - PRE LEARNING: Attempt review
Página 24 de 58
https://baxter.edfibre.com/gradejet/mod/quiz/review.php
?
attempt=147249&cmid=18279
A vacuum forming machine is available for use in the mechanical workshop.
2.1
2.1
Sharpen cutting tools, as required
Sharpen cutting tools, as required
Cutting tools
Cutting tools
Cutting tools. A cutting tool is a type of cutting tool with a blade at the end of the shank. ...
Reamer. A reamer is a tool to finish the hole opened by a drill according to the required accuracy.
...
Drill. ...
Milling tools. ...
Endmill. ...
Broach. ...
Tap/thread cutting die
Main Types of Lathe Tooling
Main Types of Lathe Tooling
Understanding lathe tooling, what it does and how it works is a big part of refining finishing and maximizing
tool wear and tear. There are a lot of options, so it can seem confusing, but it really is not once understand
the basics.
There are five types of lathe tooling: External turning tools,
Boring bars,
Drills,
Threading tools,
Parting tools.
First, about external turning tools. They are great at just what the name implies, cutting away the exterior of
the piece. This include roughing or finishing work. Second on our list was boring bars. All these can
recognize these by their circular, bar design. They come in a bunch of different sizes, with one main purpose
– to make an already existing hole bigger or to refine the finish of hole.
To make that initial hole, it will need a drill. If the operator is new to lathe work, it can picture this as a power
tool drill, but instead of the machine spinning the cutting tool into the workpiece, it is the exact opposite. The
workpiece is moving fast, and the drill is secured in a stationary position. The holes boring bars make have
a rougher finish, but if to thread it later, that is perfect.
Threading tools can add threads to both the interior and exterior of the workpiece.
Lastly – we have parting tools. Parting tools are also very important and do much more than their name
imply. These tools can part, groove, and cut off workpieces while offering a consistent, smooth finish.
There are also the left hand, right hand, and neutral hand tooling. That describes how the cutting tool faces
the workpiece and what direction the lathe is spinning he work piece. Normally our lathe will be spinning
clockwise. It’s easy to differentiate the left handed tools from right handed tools, because if lay the tools
with the insert up, left handed tools curve to the right, and right handed tools curve into the left, kind of like
the finders do if making ‘c’s with them. This is also always included in the lathe tooling designation, which
can find engraved into the side of the tool.
Lathe cutting tools
Lathe cutting tools
According to the process of using the lathe cutting tools
lathe cutting tools. Following are the 14 different types of lathe
lathe
cutting tools used in lathe:
cutting tools used in lathe:
1.
Turning tool.
2.
Chamfering tool.
3.
Thread cutting tool.
4.
Internal thread cutting tool.
5.
Facing tool.
6.
Grooving tool.
7.
Forming tool.
8.
Boring tool.
9.
Parting-off tool.
10. Counterboring tool
11. Undercutting tool
12. According to the method of applying feed
Right-hand tool
Left-hand tool
Your preview ends here
Eager to read complete document? Join bartleby learn and gain access to the full version
- Access to all documents
- Unlimited textbook solutions
- 24/7 expert homework help
2/4/2023, 2
:
02 p. m.
MEM07032 - THEORY - Use workshop machines for basic operations - PRE LEARNING: Attempt review
Página 25 de 58
https://baxter.edfibre.com/gradejet/mod/quiz/review.php
?
attempt=147249&cmid=18279
Round Nose
13. According to the method of using the tool
Turning Tool
The lathe cutting tool geometry for H.S.S. as indicated on the diagram.
NOTE: Do not state the values of the angles.
A
Side Rake
B
B
Side Clearance
Side Clearance
C
C
Front Clearance
Front Clearance
D
D
Top Rake
Top Rake
There are mainly two classes of turning tool:
Rough turning tool. Finish turning tool.
Rough Turning Tool
The main function of a rough turning tool is to remove the maximum amount of metal in minimum time
that the tool, work, and the machine will permit. The cutting angle is so ground that it can withstand
maximum cutting pressure.
1.2 Finish Turning Tool
1.2 Finish Turning Tool
Turning tool is used to remove the very small amount of metal. A tool angle is so ground that it can produce
a very smooth and accurate surface.
Chamfering Tool
Chamfering Tool
Straight turning tools are also used as a chamfering tool when the cutting edges are set at an angle of the
chamfer.
Where a large number of chamfer works are to be performed a special chamfering tool with its side cutting
edge angle ground to the angle of the chamfer is used.
Shoulder Turning Tool
Shoulder Turning Tool
Your preview ends here
Eager to read complete document? Join bartleby learn and gain access to the full version
- Access to all documents
- Unlimited textbook solutions
- 24/7 expert homework help
2/4/2023, 2
:
02 p. m.
MEM07032 - THEORY - Use workshop machines for basic operations - PRE LEARNING: Attempt review
Página 26 de 58
https://baxter.edfibre.com/gradejet/mod/quiz/review.php
?
attempt=147249&cmid=18279
A square shoulder is turned by a knife-edge turning tool or facing tool. A bevelled shoulder may be turned
by a straight turning tool having a side cutting edge angle and zero nose radius. A filleted shoulder is turned
by a straight turning tool with a nose radius corresponding to the fillet radius of the work.
Thread Cutting Tool
Thread Cutting Tool
External Thread Cutting Tool
External Thread Cutting Tool
Metric, B.S.W
or American “V” thread are formed by a single point thread cutting tool. Its cutting edges
sharpened to the shape and size of the thread to be cut.
The shape of the tool is determined by the included angle at the nose of the tool which should correspond
to the angle of the thread. It may be 60° for metric threads or 55° for
B.S.W threads.
The included angle at the nose of the tool which should correspond to the angle of the thread. It may be 60°
for metric threads or 55° for
B.S.W threads.
The size or cross-section of the cutting edges of the tool depends upon the pitch of the thread. Below figure
illustrates an H.S.S. thread cutting tool.
So for machining
different screw threads
having different pitches separates tools are used to produce
accurate threads. The nose of the tool is pointed, flat or rounded according to the shape of the root of the
thread.
A thread tool gauge is used to check the shape and size of the tool after it has been ground.
Tool for cutting square threads
Tool for cutting square threads
The side clearance of the tool for cutting square thread is of prime importance in order to prevent the tool
from interfering or rubbing against the vertical flank of the thread.
As a rule, the forward side clearance angle is determined by adding 5° to the helix angle of the thread and
trailing side clearance is obtained by subtracting 5° from the helix angle, if ø be the forward side clearance
angle and
θ
be the trailing side clearance angle, then from the formula:
The width of the cutting edge should be equal to half the pitch of the thread.
Small clearance angle of 1° to 2° are provided at the side of the tool to prevent the surface from ribbing with
the work.
Internal Thread Cutting Tool
Internal Thread Cutting Tool
The cutting edge of the tool is exactly similar to an external thread cutting tool but the front clearance
angle is sufficiently increased as in a boring tool.
The tool is a forged type orbit type and held on a boring bar. The point of the tool must be set square with
the work.
Read also:
22 Different Types of Operations used in Lathe Machine
Facing Tool
Facing Tool
Your preview ends here
Eager to read complete document? Join bartleby learn and gain access to the full version
- Access to all documents
- Unlimited textbook solutions
- 24/7 expert homework help
2/4/2023, 2
:
02 p. m.
MEM07032 - THEORY - Use workshop machines for basic operations - PRE LEARNING: Attempt review
Página 27 de 58
https://baxter.edfibre.com/gradejet/mod/quiz/review.php
?
attempt=147249&cmid=18279
A facing tool removes metal by its side cutting edges. So no top rake in necessary in a facing tool. The
figure shows H.S.S. facing tool intended for finishing operations.
The tool has 2° side cutting edge angle and 34° end cutting edge angle can be accommodated in the
space between the end of the work and 60° dead centre leaving a clearance of 2° on both sides.
The standard shank section is 20
Χ
20, 25
Χ
25, 32
Χ
32, 40
Χ
40, and 50
Χ
55 all expressed in mm. The length of
the tool is 125, 140,170, 200 and 240 mm and the nose radius varies from 0.5 to 1.6 mm.
Grooving Tool
Grooving Tool
Grooving tool is similar to a parting-off tool illustrated in the figure. The cutting edges are made square,
rounded or “V” shape according to the shape of the groove to be cut.
Forming Tool
Forming Tool
Turning curved profiles may be affected by using
1.
Ordinary lathe tools,
2.
Flat forming tools,
3.
Circular forming tools.
An ordinary lathe turning tool may sever the purpose where a copying attachment is used to reproduce the
form of a template. Flat forming tools are made of two types:
1.
Simple forming tools
2.
Flat dovetail forming tools.
Simple forming tools
Simple forming tools
These tools have their cutting edges ground to the shape of the groove, undercut, or thread to be cut.
Flat dovetail forming tools have a wider cutting edge corresponding to the shape desired. Dovetail end of
the tool is fitted in a special tool holder. No front rake is provided but sufficient front clearance angle is given
and it ranges from 10° to 15°.
Regrinding is always done on the top face of the tool which does not alter the form of the tool.
Circular Form Tools
Circular Form Tools
These tools are preferred in production work as a very long cutting surface can be used resulting in longer
tool life.
Your preview ends here
Eager to read complete document? Join bartleby learn and gain access to the full version
- Access to all documents
- Unlimited textbook solutions
- 24/7 expert homework help
2/4/2023, 2
:
02 p. m.
MEM07032 - THEORY - Use workshop machines for basic operations - PRE LEARNING: Attempt review
Página 28 de 58
https://baxter.edfibre.com/gradejet/mod/quiz/review.php
?
attempt=147249&cmid=18279
The centre of the tool is set slightly above the centre line of the work to provide an effective front clearance
angle on the tool. The tool will rub against the work if the centres are of the same height.
The tool centre is usually higher than the centre line of the lathe by 1/20 to 1/10 of the tool diameter. This
height is termed ‘offset’. Regrinding is done by grinding the flat only.
Boring Tool
Boring Tool
A boring tool is similar to a left-hand external turning tool so far its cutting edge is concerned.
The tool may be a bit type inserted in a boring bar or holder, or forged type having a tool shank.
The figure shows an H.S.S. tool bit inserted in a boring bar.
A boring bar is made of mild steel with slots or holes cut into it to accommodate the tool bit which is locked
by an Allen screw. The amount of projection of the cutting edge of the tool from the centre of the bar
determines the finished hole diameter of the work.
The bit is generally inserted at right angles to the centre line of the bar for boring a continuous hole passing
from one end to the other end.
Different Design of The Boring Tool
Different Design of The Boring Tool
The bit is set at a single to the axis projecting beyond the end of the bar for boring a blind hole.
A tool bit having two cutting edges at it two ends is used for quick machining.
A wide double-bladed cutter is inserted in the boring bar to finish the boring operation.
Two or more bits may be inserted in a boring bar for different diameters in one setting.
Boring Bars:
Boring Bars:
Boring bars are held in the tailstock for boring small holes ranging from 12 to 100 mm.
For boring larger hole diameters, boring bars are gripped by two clamp blocks and held in the tool post.
For precision boring or boring in odd size work that is supported on cross-slide, the bar is supported on
centres and is made to revolve.
Clearance for Boring Tool
Clearance for Boring Tool
In a boring tool, the tool cutting edge most have sufficient front clearance to clear the work. To strengthen
the tool point double clearance, primary and secondary, is provided.
The smaller be the hole diameter the larger should be the front clearance. Larger clearance angle
necessitates the reduction in rake angle in a boring tool.
The nose of the tool is straight or round according to the type of finish desired.
Counterboring Tool
Counterboring Tool
The counterboring operation can be performed by an ordinary boring tool. The tool cutting edge is so
ground that it can leave a shoulder after turning. A counterbore having multiple cutting edges is commonly
used.
Your preview ends here
Eager to read complete document? Join bartleby learn and gain access to the full version
- Access to all documents
- Unlimited textbook solutions
- 24/7 expert homework help
2/4/2023, 2
:
02 p. m.
MEM07032 - THEORY - Use workshop machines for basic operations - PRE LEARNING: Attempt review
Página 29 de 58
https://baxter.edfibre.com/gradejet/mod/quiz/review.php
?
attempt=147249&cmid=18279
Undercutting Tool
Undercutting Tool
Undercutting or grooving tool has a point and form of the cutting edge exactly similar to the form of the
required groove.
Clearance angle is given at all the sides of the tool. For the recessing groove cutting edge, the longitudinal
feed is employed. The front clearance angle depends upon the bore of the work.
Parting Off Tool
Parting Off Tool
A parting off tool is normally forged and used as bits for cemented carbide tipped tools. Parting off tool is
made as narrow as possible to remove the minimum of metal.
The width of the cutting-edge ranges from 3 to 12 mm only. The length of the cutting tool which inserts into
the work should be slightly longer than the radius of the bar stock being machined.
As the tool penetrates deep into the work, clearance is provided all around the tool cutting edge to prevent
it from rubbing against the work surface.
As the tool is purely ended cutting it has no side rake slight back rake is provided on the tool to promote an
easy flow of the ships.
According to The Method of Applying Feed
According to The Method of Applying Feed
Right-hand tool
Left-hand tool
Round Nose
Right-Hand Tool
Right-Hand Tool
A right-hand tool is shown in the figure. Is that which is fed from lathe bed, i.e. from the tailstock to the
headstock end when operations like turning, thread cutting, etc are performed.
A right-hand tool is formed on its left-hand end when viewed from the top with its nose pointing away from
the operator.
Left-Hand Tool
Left-Hand Tool
The left-hand tool is shown in the figure. Is that which is fed from the Left to the right-hand end of the lathe
bed, i.e. from the headstock to the tailstock end.
The left-hand tool is used for left-hand thread cutting operation or turning operation which leaves a
shoulder on the right-hand end of the workpiece.
A left-hand tool has its cutting edge formed on its right-hand end when viewed from the top with its nose
pointing away from the operator.
A left-hand tool may also be used for facing operation.
Round Nose Tool
Round Nose Tool
A round nose turning tool sown in the figure. Maybe fed from left to the right or from right to the left- hand
end of the lathe bed away. For this reason, they have no back rake and side rake.
In some cases, a small back rake is provided on the tool. A round nose turning tool is usually used for finish
turning operation.
Tool sharpening safety
Tool sharpening safety
When using any type of power tool in this section, the following safety equipment should be worn:
Your preview ends here
Eager to read complete document? Join bartleby learn and gain access to the full version
- Access to all documents
- Unlimited textbook solutions
- 24/7 expert homework help
2/4/2023, 2
:
02 p. m.
MEM07032 - THEORY - Use workshop machines for basic operations - PRE LEARNING: Attempt review
Página 30 de 58
https://baxter.edfibre.com/gradejet/mod/quiz/review.php
?
attempt=147249&cmid=18279
Eyes protection
Hearing protection
Coveralls, shirt/pants (cotton)
Steel cap boots
Hair protection
Dust mask (masonry)
Gloves
Always disconnect the power on a portable power tool before changing or adjusting attachments such
as drill bits and saw blades.
Never operate a power tool with the guard removed or when it is improperly adjusted
Sharpening cutting edges- lathe cutting tools
Sharpening cutting edges- lathe cutting tools
Cutting edges do not stay sharp forever.
In fact, tools that are designed to be razor sharp - such as knives and chisels - tend to go blunt very quickly
while using them, especially if cutting hard materials.
Lathe Tools
Lathe Tools
Dressing the grinding wheel is a part of maintaining the bench grinder. Grinding wheels should be
considered cutting tools and must be sharpened. A wheel dresser sharpens by “breaking off” the outer layer
of abrasive grit from the wheel with star shaped rotating cutters which also must be replaced from time to
time. This leaves the cutting edges of the grit sharp and clean.
A sharp wheel will cut quickly with a “hissing” sound and with very little heat by comparison to a dull wheel.
A dull wheel produces a “rapping” sound created by a “loaded up” area on the cutting surface. Compare
what happens to grinding wheels to a piece of sandpaper that is being used to sand a painted surface; the
paper loads up, stops cutting, and has to be replaced.
As with any machining operation, grinding requires the utmost attention to “Eye Protection.” Be sure to use it
when attempting the following instructions.
Grinding lathe tools is easy, and the only reason we sell them is to help a beginner get started.
Consider a carpenter who did not have the confidence to drive a nail because he was worried about
missing the nail and hitting his thumb. He/she would not be in the trade very long! It should not take but a
few minutes to make simple cutting tools and only a few seconds to re-sharpen them.
A bench grinder does not have to be expensive to work well, but it does require good “wheels” for high-
speed steels. Try to find a source for grinding wheels from an industrial supplier. Some of the wheels that
come with inexpensive grinders would not sharpen a butter knife. Sixty grit is a good place to start. A wheel
dresser is also a necessity. They are relatively inexpensive and are readily available from good hardware
stores and on-line resources.
FIGURE—A Wheel Dressing Tool and spare “star wheel” sharpening insert.
For safety, a bench grinder should be mounted to something heavy enough so it will not move while being
used. The tool support must be used and should be set at approximately 7°. Few
people have the skill to make tools without a tool support and in essence it is wasted effort. Tool supports
are usually made up of two pieces that allow an operator to set the tool rest above or below center. It really
does not matter whether its above or below if the support is at 7°.
FIGURE—Set tool rest at any height, but at 7° angle from centerline of wheel.
The reason tool supports are designed like this is so they can be used for a variety of uses, not just tool bits.
What this means is that if the tool support is above or below center it must be adjusted as the wheel
diameter changes.
When working around grinders it is an absolute necessity to wear EYE PROTECTION. Grinding debris is thrown
out at high velocities and can damage not only eyes, but also expensive glasses. Wear safety glasses or a
full-face shield.
If an operator never sharpened a tool, take a close look at how ours are sharpened. Let us duplicate the
right-hand tool on the opposite end of the blank.
First dress the wheel by taking the dresser and setting it on the tool support square with the wheel and while
applying a light pressure move the dresser back and forth with the grinder running. Unless the wheel is in
bad shape, it should be ready to use in a few passes.
Grinding Side 1 of the Tool
Grinding Side 1 of the Tool
Turn off the grinder and set the tool support for approximately 7°. If it is not good at guessing at angles use
a pre-sharpened Sherline tool to set the angle. Metal cutting tools are very tolerant on angles
Heel
FIGURE 3—Heel of the tool.
Have a cup of water handy to cool the tool with and set the blank on the tool rest and start grinding side 1.
Your preview ends here
Eager to read complete document? Join bartleby learn and gain access to the full version
- Access to all documents
- Unlimited textbook solutions
- 24/7 expert homework help
2/4/2023, 2
:
02 p. m.
MEM07032 - THEORY - Use workshop machines for basic operations - PRE LEARNING: Attempt review
Página 31 de 58
https://baxter.edfibre.com/gradejet/mod/quiz/review.php
?
attempt=147249&cmid=18279
Move the blank back and forth across the face of the wheel until have ground a 10° angle on approximately
3/16" (4 mm) of side 1.
This is where the “positive approach” comes in. Unless pushing the tool into the wheel with enough pressure,
the tool will bounce around and will never get a good flat cutting surface. It is not necessary to worry about
getting the tool too hot. Modern day tool steels do not anneal, and a little discoloration does not affect the
tool life in tool room use. Concentrate on holding the 10° angle while moving back and forth. We’ll give this
edge a final sharpening later; it’s time for side 2.
Grinding side 2 of the tool
Grinding side 2 of the tool
FIGURE —Grinding side 2.
The reason angle B is ground less than 90° is to allow the tool to get into corners.
FIGURE 7—Properly ground tool cutting into a corner
Side 2 is ground the same way as side 1, moving the tool back and forth until have a point. After getting side
2 ground, cool the tool in the cup of water.
The next step is to learn another aspect of tool grinding. It is important to know when have ground the
surface up to the cutting edge, especially when re-sharpening lathe tools. Take the tool just ground and
bring it up to the wheel at a slightly different angle than ground for this experiment.
Watch the point that touches the wheel first and will notice that the sparks will bounce off the cutting edge
only where the wheel has ground from top to bottom.
FIGURES —Tip not yet ground flat and 8B, Tool ground flat all the way to the tip.
This tells when the tool has been sharpened without taking it away to look which allows to grind flat and
true surfaces. If sharpen a tool for a Sherline lathe, use a 1/4" square tool blank and keep the cutting edge
up to the top of the blank; the tool will come out on center without shims.
Grind until sparks just reach tip of tool
FIGURE —Grinding the “Hook” into side 3. When grinding tools by hand, on average, the cutting- tip surface
of the tool is going to be .005” to .0010” below the top of the tool. This will leave a .010” to .020” tit on the end
of the tool when facing off the part.
Use the skill have developed grinding the second side now. Set the blank on the support with the 10° (side 1)
up. The tool must be brought up to the grinding wheel with a slight angle so do not grind the tip below
center. With the tool setting on the rest, move the tool in and grind until seeing sparks bouncing off the
cutting edge where the corner of the wheel is lined up with the back part of the 10° face. When this happens,
slowly decrease the angle without pushing the tool in any more until sparks bounce all the way to the tip.
Stop as soon as this happens. On most of our tool holders can adjust the tool tip height to compensate for
the amount that have ground off the top of the tool (generally .005" to .010"). However, there is no
adjustment on our compound slide.
Therefore, on the compound slide, the cutting tip of the tool needs to be at the same height as the top of
the tool blank. It must be inspected, and the surface should be entirely ground. The recommended way is to
put more “hook” on the tool than previously suggested, but have found that the slight increase in
performance is offset by the problems encountered re-sharpening these tools.
Your preview ends here
Eager to read complete document? Join bartleby learn and gain access to the full version
- Access to all documents
- Unlimited textbook solutions
- 24/7 expert homework help
2/4/2023, 2
:
02 p. m.
MEM07032 - THEORY - Use workshop machines for basic operations - PRE LEARNING: Attempt review
Página 32 de 58
https://baxter.edfibre.com/gradejet/mod/quiz/review.php
?
attempt=147249&cmid=18279
FIGURES —Normally recommended “hook” ground into tool and 10B, Simpler method suggested for Sherline
tools.
To put the finishing touches on the tool, it has to “kiss off” sides 1 and 2 again. Carefully line up side 1 with the
wheel and bring it to the wheel in a positive manner with very little pressure; watch
for the sparks on the cutting edge. What trying to accomplish is to make the tool set against the wheel on
the same plane as when first ground side 1. If the tool is held too rigid, it will not align itself, too loose and it
will bounce around. “Breaking” the Point
Use the same method on side 2. The tool should be ready to use except for the point. It is recommend
putting about a .010 (.2 mm) “break” on the point by holding the tool with the point aimed at the wheel face.
Because two angles converge at the point, the angle in relation to the sides is greater. Think about it!
FIGURE —Putting a .010" “Break” on the tip of the tool.
Top of Tool
Angles approximately equal
Angles approximately equal
This means that if setting the tool flat on the tool rest the tool rest angle would have to be increased to get
an even flat. This would not be worth the effort, so the easy way is to free hand it. Start by touching the heel
of the tool first, and then change the angle until a slight flat is put on the tip. The angle for holding it at has
to be close when starting to get desired results.
FIGURE 12—Hand holding the tool to “Break” the point saves resetting the angle on the tool rest.
The purpose of this flat is to improve finish and tool life. That is not recommend a large radius on the tip of
tools used on small machines. These machines are not rigid enough to get the desired results from this
practice and cause “chatter” problems.
The finished product should be a right-handed tool, have flat cutting surfaces (except for the radius caused
by the wheel), have a slight flat on the tip, and a tip angle of less than 90°.
Tools used on lathes such as the shearline will do all their cutting at the tip of the tool because they don’t
have the horsepower for 1/4" (6 mm) cuts.
That is not recommend using oil stones to improve the edges. After a few minutes use with an occasional
dab of cutting oil a properly sharpened tool will hone itself in.
The final sharpening to a tool should take place with the wheel cutting the cutting edge of the tool from the
top of the tool to the bottom when using bench grinders.
These instructions include a great deal of information about how to do what should be a simple operation,
but these are very complex instructions to write because we are trying to how to control the hands, not a
simple machine.
Incidentally, the reason we call a tool a right-handed tool when the cutting edge is on the left is because it
is designated by which way the chip leaves the cutting tool. Cutting tools such as left or right-handed tin
snips are also designated in this manner because the cut-off falls to the left or right.
The left-hand tools are ground the same as right, in the same order with the angles reversed. Boring Tools
FIGURE 13—Typical boring tool.
Boring tools are the most difficult to grind. They should always be made as rigid as possible. Tool angles
around the “tip” can be the same as any cutting tool, but clearances of the tool body must be considered
carefully. A tool ground with enough clearance for a finished hole may not have enough clearance to start
with when the hole has a smaller diameter. If it must bore a hole in a part that has a lot of work in it, have a
tool ready to use that has been checked out on a piece of scrap.
Form Tools
Form Tools
Form tools are used to create a shape the same as the tool. To grind form tools, a pattern of the finished
shape should be at hand and there should be some possibility of success with what work with. However, it
cannot grind a 1/8" (3 mm) groove into the tool 1/4" (6 mm) deep with a 1/2" (12 mm) wide wheel.
FIGURES 14A—A typical form tool made by a custom toolmaking shop, and 14B, a home shop method of
achieving the same finished shape in two steps with a tool that can be ground on a bench grinder.
This type of tool is usually made by Tool and Cutter specialists that have high shop rates using precision
grinders, diamond dressers, and a large variety of wheels available to them.
Your preview ends here
Eager to read complete document? Join bartleby learn and gain access to the full version
- Access to all documents
- Unlimited textbook solutions
- 24/7 expert homework help
2/4/2023, 2
:
02 p. m.
MEM07032 - THEORY - Use workshop machines for basic operations - PRE LEARNING: Attempt review
Página 33 de 58
https://baxter.edfibre.com/gradejet/mod/quiz/review.php
?
attempt=147249&cmid=18279
Like any skill, tool grinding is one that must develop with time. It is also the skill that allows to go one step
beyond the average hacker.
Sharpen Used and Dull Drill Bits (By Hand)
Well before head over to the hardware store to buy a brand-new box of drill bits, try this simple technique
first and save a lot of time and money!
Follow these steps and it can transform the used, dull, chipped, broken, or otherwise useless drill bit, into a
prime hole blasting instrument.
Sharpening bits is a tricky task.—sharpening by hand on a belt sander or bench grinder.
Materials:
Materials:
1.
A dull or chipped drill bit
2.
A bench grinder or belt sander
WARNING!
WARNING! The hands will be very close to the sharpening device, and dangerously at risk with losing some
skin.
DO NOT wear gloves
DO NOT wear gloves as they can get caught into the sharpening device and pull operator in. Be mindful
and deliberate about where position on the sharpening device. The operator should probably wear safety
glasses too.
Step 1: Know the Drill Bit
Step 1: Know the Drill Bit
There are many features on a drill bit that can be defined. For speed sake, were only worried about 3 basic
features on the bit: the lip, land, and chisel.
Your preview ends here
Eager to read complete document? Join bartleby learn and gain access to the full version
- Access to all documents
- Unlimited textbook solutions
- 24/7 expert homework help
2/4/2023, 2
:
02 p. m.
MEM07032 - THEORY - Use workshop machines for basic operations - PRE LEARNING: Attempt review
Página 34 de 58
https://baxter.edfibre.com/gradejet/mod/quiz/review.php
?
attempt=147249&cmid=18279
The "lip" is what does the actual cutting. The two lips on the twist drill should be symmetric if an equal
cutting is to be done while drilling. If one lip is favoured while sharpening, it will become bigger than the
other and most of the cutting will be performed on one side of the bit. This is bad as it makes non-straight
holes.
The "land" or "landing" is what follows the lip and will support the sharp edge while the bit is cutting. The
landing must be angled in such a way that it leaves clearance between the part trying
to drill and the lip. However, too much angle subtracts support from the lip, and will cause the bit to chip
more often, especially on the corners.
The "chisel" is the line which is created when the landing from both sides of the twist drill intersect. In truth,
this area does no cutting motion. Don't think of it as a true chisel. In fact, while the drill is turning and being
forced down into the work-piece, the chisel smears the wood or metal drilling into the lips. For this reason, it
is especially important to create a very small chisel.
Step 2: Understand Why Drills Chip and Dull
Step 2: Understand Why Drills Chip and Dull
To know how to better sharpen the bit, should know the reason for doing this.
Chipped bits are caused because the landing force behind them cannot support the forces exerted by the
drilling operation. So, make sure the landing has a curved shape to it. Curved shapes add support to the lip.
Dull bits are caused when either the chisel is having trouble smearing the material to the lip and needs to
be re-defined on the face of the bit. Or the lip is rolling over and needs to be re-sharpened so that it pushes
directly into the workpiece.
Step 3: Prepare the Bit
Step 3: Prepare the Bit
Run a file across any burrs that bay be on the shank of the drill bit. If anything were to go wrong, and the bit
were to slip in the fingers, would not want these nasty burrs cutting into the skin.
Step 4: Choose the Sharpening Tool
Step 4: Choose the Sharpening Tool
Either a bench grinder or a belt sander will work for sharpening bits. Just make sure that the guards on
either one of these machines is less than 1/8" away from the belt or wheel so that the bit does not get
caught between the guard!
Step 5: Practice Holding the Bit
Step 5: Practice Holding the Bit
Your preview ends here
Eager to read complete document? Join bartleby learn and gain access to the full version
- Access to all documents
- Unlimited textbook solutions
- 24/7 expert homework help
2/4/2023, 2
:
02 p. m.
MEM07032 - THEORY - Use workshop machines for basic operations - PRE LEARNING: Attempt review
Página 35 de 58
https://baxter.edfibre.com/gradejet/mod/quiz/review.php
?
attempt=147249&cmid=18279
Start in a comfortable position with the hand against the machine support and take the drill bit into both
hands. Hold the bit at a 60-degree angle to the face of the belt sander. Place the end of the landing so that
it is directly against the belt. Use steps 5-7 to move the bit across the belt into the finish position. Notice in
these two pictures how little difference there is between the start and finish sharpening positions. Steps 5-7
are simultaneous steps to get to that finish position but notice how the only hand that moves is the left
hand. The right hand stays stationary, with only the fingers guiding the drill bit.
Step 6: Cut the Landing
Step 6: Cut the Landing
Cut the landing by raising the left hand while applying pressure to the sharpening device.
Step 7: Shape the Chisel
Step 7: Shape the Chisel
By moving the left hand towards the right, creating the chisel angle. Practice a few times until the chisel
angle is 45 degrees from the lip.
Step 8: Shape the Landing
Step 8: Shape the Landing
By rotating or rolling the bit counter clockwise, creating a rounded landing that gives more support to the
lip.
Step 9: Combine Cutting, Shaping, and Rotating
Step 9: Combine Cutting, Shaping, and Rotating
Combine all three movements while sharpening to make the perfect cut on the drill face.
Repeat this step a couple of times and rotate the drill bit 180 degrees in the hand to sharpen the other lip.
WARNING:
WARNING: this procedure will heat up the drill bit face. Have a cup of cool water by the belt sander or
bench grinder to dip the tip of the drill bit into to cool it off.
Step 10: Repetition
Step 10: Repetition
It may take a couple dozen times to get the two lips of the drill bit symmetric. That is normal and requires a
lot of patience. But keep on trying! Often rotate which side of the bit is working on so that do not favour one
side over the other. Always make deliberate cuts, do not try to "feather" a sharp tip by pressing the drill bit
lightly into the sander or grinder. This almost always leads to uneven lips or will cause to roll the lip so that it
no longer cuts.
2.3
2.3
Install tools according to procedures
Install tools according to procedures
Correct Lathe Cutter Setup
Correct Lathe Cutter Setup
Using a Lathe is one of the first skills learned by a beginning Machinist. There are a lot of tips and tricks that
are not readily available to everybody. Here is one simple trick that is fundamental to getting a part
properly turned. Setting the outside cutter to the proper height is something rather elusive to a good many
aspiring lathe users.
Step 1: Get the Right Tool
Step 1: Get the Right Tool
All the Setup steps are done with the lathe powered off. Make sure there is no chance of accidentally
turning on the machine.
All is needed is a simple metallic ruler, about 6 inches long. They are only a couple of dollars. They are
available at any hardware store or home improvement chain in the measuring tool isle. In a pinch any
metallic straight flat "Ruler-Like" object would do.
Step 2: Chuck the Part
Step 2: Chuck the Part
Load the cylindrical part in the lathe. Here is an extra tip: as tighten the chuck rotate the part with the hand
lightly, as the friction just grips the part, keep tightening with the key, until it does not move any more. This
helps centering the part and gives a truer alignment along the axis of the lathe spindle. It will be less wobbly
as it turns...Also it will be less waste as the truing cut taken is less.
Step 3: Load Cuter Tool
Step 3: Load Cuter Tool
Install a regular cutting bit in the tool post. Make sure it is the tool that intend to use for the first cut. This tool
height procedure needs to be repeated for every tool that will be used in outside turning. Install the tool
tight in the holder and set the holder perpendicular to the part. Make sure the tool seat is clean of debris
otherwise will get a false setup that is not repeatable.
Your preview ends here
Eager to read complete document? Join bartleby learn and gain access to the full version
- Access to all documents
- Unlimited textbook solutions
- 24/7 expert homework help
2/4/2023, 2
:
02 p. m.
MEM07032 - THEORY - Use workshop machines for basic operations - PRE LEARNING: Attempt review
Página 36 de 58
https://baxter.edfibre.com/gradejet/mod/quiz/review.php
?
attempt=147249&cmid=18279
Step 4: Set Ruler in Position
Step 4: Set Ruler in Position
Lock the cam on the tool post
Bring the lathe Carriage close to the chuck end of lathe and using the cross-feed wheel get the tool closer
to the part until can pinch the ruler against the part to be turned. Do not tighten too much as
it will damage the ruler. Just tight enough so that the ruler does not fall off and stays pinched between the
tool and the surface of the part.
Step 5: Reading the Ruler
Step 5: Reading the Ruler
If the tool height is set correctly, the ruler will be vertical. Just as in the first picture.
If the ruler is tilting to the right, then the cutter is sitting too low. Release tool post cam and Adjust the height
wheel on the tool post to get it to the right height. See second picture
If the ruler is tilted to the left toward the back of the lathe the tip of the cutter is above the centre line of the
part. Release cam, and Again spin the knurled wheel to drop the tool just slightly.
Adjusting might take a few tries until the ruler is apparently straight up and down (vertical) as viewed from
the back of the lathe. In time the operator will develop a real knack for setting the tool straight in just one or
two tries.
If the ruler is vertical, set tight the locking nut sitting over the adjusting knurled wheel. The setting will be
preserved
Step 6: Take First Test Cut
Step 6: Take First Test Cut
Release cam and remove cutter. Install it again longitudinally along the lathe axis and flip it around to take
a facing cut. Take a light facing cut. If the tool is not exactly on centre it will leave a little nib on the part, see
photo.
If the nib is left because the tool is too low or too high. Stop lathe, back off the carriage and repeated the
above steps. Use small increments while adjusting the Knurled wheel on the tool holder.
Step 7: Final Adjustments
Step 7: Final Adjustments
The setup is repeatable. Make sure all the surfaces are clean...
Do this for all the tools that plan to use turning the part. It is useful to have multiple holders that once set
can be just dropped in place.
This procedure should be followed any time there is a tool change done.
Having several holders with the tools already set at the right height will save the time. The picture above
illustrates a perfectly turned part that is about to be milled.
Your preview ends here
Eager to read complete document? Join bartleby learn and gain access to the full version
- Access to all documents
- Unlimited textbook solutions
- 24/7 expert homework help
2/4/2023, 2
:
02 p. m.
MEM07032 - THEORY - Use workshop machines for basic operations - PRE LEARNING: Attempt review
Página 37 de 58
https://baxter.edfibre.com/gradejet/mod/quiz/review.php
?
attempt=147249&cmid=18279
How to Set up a Lathe Cutting Tool
How to Set up a Lathe Cutting Tool
Positioning the cutting point correctly and setting up a lathe cutting tool are critical to
CNC
turning
process,
greatly affects the removal rate, cutting efficiency and surface finish.
Watch the video: Working with a Lathe
Essential Machining Skills: Working with a Lathe, Part One
Boring Bar secured in gang tool holding set up.
Drill secured in gang tool holding set up.
Threading tool secured in gang tool holding set up.
Parting tool secured in turret tool holding set up.
2.3
2.3
Set guards and adjust, as required
Set guards and adjust, as required
Your preview ends here
Eager to read complete document? Join bartleby learn and gain access to the full version
- Access to all documents
- Unlimited textbook solutions
- 24/7 expert homework help
2/4/2023, 2
:
02 p. m.
MEM07032 - THEORY - Use workshop machines for basic operations - PRE LEARNING: Attempt review
Página 38 de 58
https://baxter.edfibre.com/gradejet/mod/quiz/review.php
?
attempt=147249&cmid=18279
By using the machine in a workshop, we must understand What some good safety principles are to follow
when using a lathe.
What are some good safety principles to follow when using a lathe?
Wear appropriate CSA-certified safety glasses. It may be necessary for others in the area to wear safety
glasses too as objects will fly off the work.
Make sure entanglement hazards are removed (e.g. loose clothing, jewellery, etc.). Tie back and confine
long hair.
Keep the floor free from obstructions, or slip hazards.
Make sure the lathe has a start/stop button within easy reach of the operator.
Make sure the lathe has an emergency stop button (e-stop).
Follow job specifications for the speed, feed, and depth of cut for materials being turned. Make sure all
work runs true and cantered.
Centre-drill work deeply enough to provide support for the piece while it is turning
Secure and clamp the piece being worked.
Adjust tool and tool rest so that they are slightly above the centre of the work.
Use a lifting device to handle heavy chucks or work. Refer to
Materials Handling
for additional
information.
Inspect chucks for wear or damage. Flying pieces can be very dangerous.
Remove chuck wrench immediately after adjusting chuck.
Use a barrier guard when operating the lathe in semi-automatic or automatic mode
Guard all power transmission parts.
Remove all tools, measuring instruments and other objects from saddle or lathe bed before starting
machine.
Keep all lathe cutting tools sharp.
Ensure that the chip and coolant shields are in place.
Shut off the power supply to the motor before mounting or removing accessories.
Stop lathe before taking measurements of any kind.
Use a vacuum, brush or rake to remove cuttings only after the lathe has stopped moving.
Keep working surface clean of scraps, tools and materials.
Keep floor around lathe clean and free of oil and grease.
Less than 50 per cent of industrial machines are properly safeguarded. The unfortunate result is thousands
of reported amputations, lacerations, crushing injuries, and abrasions, and hundreds of accidents that
result in deaths each year. The number of moving parts and motions involved in producing components on
lathes and grinders and the proximity of operators during setup and operation can create particularly
precarious situations.
Hazards to the operator and other employees in the machine area exist at the point of operation because
of the very nature of the process; numerous rotating parts can create in-going nip points, pulling in
clothing, hair, or fingers; chips and parts can fly off during production, endangering vision and creating a
trip hazard around the machine; and coolant can spatter, causing slip hazards.
To provide a safe work environment, a company needs to keep current on—and follow—codes regarding
proper machine guarding and personal protection equipment. All employees should be aware of the safety
requirements for each machine and receive frequent reminders that safety procedures are expected to be
followed at all times.
Shield Shop Employees
Shield Shop Employees
Shields secured to the lathe, probably the most common safety practice, can protect operators from
several dangers, including the rotating chuck and tool, cross-slide movements, and the operation of the
magnetic base.
A hinged chuck can prevent items from inadvertently getting entangled with the chuck. Some chuck shields
are constructed entirely of steel; some have a steel frame with a visibility window to allow viewing during
operation; and others are constructed of transparent, high-impact polycarbonate, providing a full view of
the operation.
Chip/coolant shields can stop flying chips or parts from reaching the operator’s upper body or
accumulating on the floor where they can create a slip hazard along with coolant overspray. Cross- slide
travel shields travel along with the sliding carriage to provide continuous protection. Even if the operator is
wearing proper personal protective equipment flying chips and coolant can create hazards, and the
additional protection is recommended.
Most shields can be interlocked with the machine’s electrical system to prevent operation when they are
not in place. Swinging a shield from its protective position will break its electrical connection and cut the
power, forcing a quick coast down.
Lathe components like lead screws, cam shafts, and traverse rods that rotate slowly may appear to be
harmless but they can hold a lot of torque, and their rotational energy can capture, pull-in, and crush items
that get too close.
Your preview ends here
Eager to read complete document? Join bartleby learn and gain access to the full version
- Access to all documents
- Unlimited textbook solutions
- 24/7 expert homework help
2/4/2023, 2
:
02 p. m.
MEM07032 - THEORY - Use workshop machines for basic operations - PRE LEARNING: Attempt review
Página 39 de 58
https://baxter.edfibre.com/gradejet/mod/quiz/review.php
?
attempt=147249&cmid=18279
Telescopic stainless-steel sleeves can cover these types of rotating components allowing them to function
while providing a safety barrier between the action and employees. A small amount of carriage travel will
be lost, and the sleeves will need to be cleaned and lubricated occasionally.
Boost the Power of ‘Stop’
Boost the Power of ‘Stop’
Electrical updates for lathes can include the addition of emergency stop (e-stop) buttons that are main
power disconnect switches to stop all machine activity.
American National Standards Institute (ANSI) standards say that an e-stop is required on any machine that
will tolerate a quick stop. Some lathes have a true emergency stop built into halt operation in less than a
second, but most require several seconds to cease functions. An electronic motor brake can improve
coast-down time, in some cases from 15 seconds to 3 seconds, which can make a significant difference in
an emergency.
The red, mushroom-shaped button should have a manual latch that keeps it down once it is pushed to
prevent machine operation by the regular controls. Once the e-stop is engaged, the latch keeps it down
until a manual quarter-turn releases the latch and allows the machine’s controls to again command the
machine’s actions. Kick plates or grab-wires that go across a machine can facilitate an emergency shut-
down if there is potential for an operator’s hands to be caught.
E-stops need to be readily accessible. An e-stop button should be within easy reach at each location on
the machine that requires operator interaction. When more than one individual is involved, each person
should have his or her own e-stop.
A spring-loaded button indicates that there is a magnetic motor start or anti-restart, also known as drop-
out protection, to prevent a machine from unexpectedly resuming operation after shutting down because
of power loss.
Avoid Flying Wrench Risks
Avoid Flying Wrench Risks
Misuse of a standard chuck wrench is a common source of lathe accidents. When a lathe is not in use, a
seemingly logical and typical but unsafe storage place for the chuck wrench is in the chuck. The danger is
that an operator may turn on the lathe without checking to see where the wrench is located. It can fly out of
the chuck, and across the shop, causing a serious injury to anyone in the area.
Spring-loaded, self-ejecting chuck wrenches, available in several sizes, can eliminate this hazard by not
allowing the wrench to remain in the chuck. They are available in several sizes.
Onsite risk assessments and machine surveys can help a company get and stay up to code. Based on ANSI
B11.0-2015, a risk assessment provides a hazard score with the risk level for each machine, suggestions to
lower the hazard level, and detailed documentation to outline the results. A machine safeguarding
assessment audits each machine for code compliance and provides customized proposals that suggest
specific products and services to bring the machine into compliance.
Safety principles when working with a lathe, according to the Canadian Centre for Occupational Health and
safety (CCOHS), include:
Wear appropriate safety glasses during operation.
Remove entanglement hazards such as loose clothing and jewelry.
Keep the floor should be clear of obstructions and slip hazards.
Ensure the e-stop button is within easy reach of the operator.
Follow job specifications for speed, feed, and depth of cut for the material being turned and take all
necessary steps to ensure that work is run true and centered.
Centre drill work deeply enough to provide support for the piece while it is turning.
Secure and clamp the workpiece.
Adjust the tool and tool rest so they are slightly above the centre of the work.
Use a lifting device to handle heavy chucks or work.
Inspect chucks for wear or damage to help prevent flying workpieces.
Use a barrier guard when operating a lathe in a semi-automatic or automatic mode.
Your preview ends here
Eager to read complete document? Join bartleby learn and gain access to the full version
- Access to all documents
- Unlimited textbook solutions
- 24/7 expert homework help
2/4/2023, 2
:
02 p. m.
MEM07032 - THEORY - Use workshop machines for basic operations - PRE LEARNING: Attempt review
Página 40 de 58
https://baxter.edfibre.com/gradejet/mod/quiz/review.php
?
attempt=147249&cmid=18279
Guard all power transmission parts.
Remove all tools, measuring instruments, and other objects from the saddle or lathe bed before starting
the machine.
Keep all cutting tools sharp.
Ensure that the clip and coolant shields are in place.
Shut off the power supply to the motor before mounting or removing accessories.
Stop the lathe before taking measurements of any kind.
Use a vacuum, brush, or rake to remove cuttings only after the lathe has stopped moving.
Keep working surfaces clean of scrap, tools, and materials.
Keep the floor around the lathe clean and free of oil and grease.
A metal lathe is a precision turning machine that rotates a metal rod or irregular-shaped material while a
tool cuts into the material at a preset position. Similar to the wood lathe, the metal lathe normally consists
of a headstock and base that houses one or more spindles on which a work holding device (chuck) can
drive the stock and the cutting tools can remove metal, producing mainly cylindrical and conical shapes.
There are basically two main types of metal lathes: Lathes for shaft work (material supported at two or
more locations) and lathes for bar (bar stock introduced through the spindle) or chucking work (individual
pieces secured at the chuck). Shaft lathes include engine lathes, vertical-shaft lathes, and turning centers.
Bar and chucking lathes include turret lathes (vertical and horizontal) and vertical boring mills.
Hazard Severe injuries and death can occur primarily from being caught in or struck by rotating parts. An
operator can be pulled into the lathe from working perilously close (e.g., polishing a
slotted shaft with emery cloth) or wearing gloves, loose clothing, loose hair, jewelry, etc. Trapping spaces
are also created between the cutting tool, its mounting, and the work piece or chuck.
Projected parts or material such as chuck keys or unsecured work pieces can also strike nearby operators.
Flying chips and coolant also present hazards to the operator. Solution Avoid wearing gloves, loose clothing,
long hair, jewelry, or other dangling objects near lathe operations. Pay close attention to work pieces that
have keyway slots or other surface profiles that may increase the risk of entanglement. Assess the need to
manually polish (e.g., emery cloth) rotating material. If necessary, consider milling keyways or other profiles
after polishing or use emery cloth with the aid of a tool or backing boards. Always use a brush or tool to
remove chips. Cover work-holding devices (chucks) and tool trapping space hazards (especially in
automatic or semiautomatic modes) with secured fixed or movable guards or shields. Vertical lathes and
controlled turning centers are normally provided with fixed or interlocked guarding that prevents access
during the automatic cycle. Make sure all work pieces and work-holding devices are secure and free from
defects. Remove the chuck key from the chuck after securing the material. A good rule is to never take the
hand off the chuck key until set it back onto a table. Consider using a spring-loaded wrench. Provide a
chip/coolant shield unless another guard or shield already provides protection. This does not replace the
need for eye and face protection, however. Note: Guards or shields used to protect lathe operators from
projected parts must either be from the manufacturer or, if fabricated in-house, meet or exceed the same
impact-resistance specifications as the original manufactured part. Various materials (such as
polycarbonates) may possess different and less- effective impact-resistance characteristics than the
original materials used by the manufacturer
In one case, an operator was killed when the bell casting on a lathe came loose while the lathe was turning
and was propelled through two, 1/2-inch-thick Plexiglas windows. The Plexiglas was installed as a
replacement for the manufacturer’s original composite window on the machine’s door frame. The operator
was fatally struck in the head and neck as he was looking through the window. The manufacturer’s original
observation window was made of a 1/4-inch-thick laminated glass plate with a 1/2-inch-thick
polycarbonate window, separated by an approximately 1/4-inch air space. The original window was
replaced with Plexiglas material that had a lower impact resistance than the polycarbonate shield
originally supplied by the machine manufacturer.
Polycarbonates are a family of various polymers that includes Macrolux, Lexan, Relex, Replex, Dynaglass,
Exolite, Verolite, Cyrolon, and Makrolon. These materials have different impact- resistance characteristics
for different thicknesses and surface areas. It is important to note that increasing the thickness beyond a
certain level does not always improve or increase the impact resistance. Some studies have shown
polycarbonate degrades due to age and prolonged contact with metalworking fluids and lubricants.
Milling machine A milling machine removes material from a work piece by rotating a cutting tool (cutter)
and moving it into the work piece. Milling machines, either vertical or horizontal, are usually
used to machine flat and irregularly shaped surfaces of metal and other tough materials, and can be used
to drill, bore, and cut gears, threads, and slots. The vertical mill, or “column and knee” mill, is the most
common milling machine found in machine shops today. The general construction of this mill includes the
quill, which moves vertically in the head and contains the spindle and cutting tools. The knee moves up and
down by sliding parallel to the column. The column holds the turret, which allows the milling head to be
positioned anywhere above the table. Hand wheels move the work table to the left and right (X axis), in and
out (Y axis), in addition to moving the knee, saddle, and worktable up and down (Z axis).
Hazard
Hazard
Serious injuries and entanglement can occur if the operator contacts the rotating cutter. Metal shavings
and lubricating/cooling fluids might also present a risk from the point of operation area. Material might spin
and strike an operator if the material is not secured to the table. Injuries can also occur from a projected
wrench if it is left in the spindle. Solution Secure the work piece, either by clamping it onto the work table or
by clamping it securely in a vise that is clamped tightly to the table. Note: Computer numerical controlled
(CNC) mills are rapidly replacing manually fed machines, mainly for versatility and production reasons. The
increased automation does not normally require the operator to move the hand wheels (like the traditional
machines), so operators must always keep their hands away from the point of operation. A guard or shield
that encloses the cutter head or milling bed may be considered to protect the operator from the cutting
area, flying metal shavings, and lubricating or cooling fluids. Make sure the tightening wrench is removed
from the mill.
Your preview ends here
Eager to read complete document? Join bartleby learn and gain access to the full version
- Access to all documents
- Unlimited textbook solutions
- 24/7 expert homework help
2/4/2023, 2
:
02 p. m.
MEM07032 - THEORY - Use workshop machines for basic operations - PRE LEARNING: Attempt review
Página 41 de 58
https://baxter.edfibre.com/gradejet/mod/quiz/review.php
?
attempt=147249&cmid=18279
CNC router and cutting tables
CNC router and cutting tables
Computer numerical controlled (CNC) routers remove material from a work piece by rotating a cutting tool
(cutter) and moving it into the work piece, but operate at higher speeds than milling machines. CNC routers
are usually used to cut or shape more ornate designs into thinner and softer materials such as wood,
plastic, and soft metals like aluminum. CNC cutting tables use plasma, lasers, or high-powered waterjets
instead of a rotating tool, to cut and engrave metal, and other hard or soft materials. CNC routers and
cutting tables, either vertical or horizontal, are commonly found in wood shops and metal fabrication shops,
and vary in size to accommodate smaller work pieces, or large sheet stock. The general construction of
these highly automated machines consists of a stationary table or bed featuring a turret (Z axis) with a
spindle or cutting tip that moves back and forth on the rails (X axis) of a moving gantry (Y axis) above the
work piece.
Depending on size and application, CNC routers and cutting tables can be completely open, or partially or
totally enclosed by interlocked metal enclosures equipped with thermoplastic vision panels. Operators
initiate start/stop sequences from a control console that is usually a safe distance away from the point of
operation.
Hazard Serious lacerations, fractures, burns, and amputations can occur if an operator contacts the
rotating cutting tool, or cutting tip/nozzle during operation. Fractures, lacerations, and even death can
occur to the operator and others in the area from being struck by ejected material, parts,
and tooling. Metal shavings and lubricating/cooling fluids might also present a risk from the point of
operation area. Plasma and laser cutting produces toxic fumes and particulates, and also produces intense
light and/or radiation that can cause eye damage and skin burns. Sparks and hot slag from these hot
processes can ignite nearby combustibles. A potential for shock and electrocution hazards exists due to the
high operating voltages of plasma and laser cutters. Dust accumulation from the laser cutting of titanium,
aluminum, zinc, and their alloys can cause a thermite reaction when mixed with the dust of oxidized iron or
copper and cause a combustible dust explosion.
Water used in high-powered jet cutting is compressible at the pressures involved and can store energy just
as compressed air does. The use of pool/ spa chemicals to control bacteria in the water tanks of waterjet
cutters can cause eye injuries. Crushing injuries can occur if an operator, or any part of the body is caught
between the stationary and moving parts of the machine. The operator, or others in the area, can be struck
by the traveling gantry. Unexpected movement or startup caused by faults in the control system can also
cause serious injury when changing tools and moving material and parts. Solution When CNC routers are
not fully or partially enclosed, fixed barrier guards can protect the operator and others in the area from
point of operation hazards at the cutting tool and from ejected parts. Automatic loading and unloading
methods, automatic tool changing, light curtains, or pressure sensitive mats that shut off the machine can
further reduce the exposure to the point of operation from unexpected movement or startup. Safe distance,
barrier guards, or electronic safety devices can prevent others in the area from getting to close to the
moving gantry, and other moving parts of the machine. Ensure adequate ventilation is provided to exhaust
hazardous fumes and particulates.
Keep dust collectors clean. Do not allow the accumulation of flammable or combustible materials and
debris such as metal dust, baled paper, bulk sulfur, and oily rags. Keep a fire extinguisher readily available
in the immediate area. Use proper personal protective equipment to protect operators and others from
hazards caused by hot processes such as hearing protection, safety glasses and/or face shields, shock
resistant gloves, and welding curtains. Establish a laser safety program and appoint a Laser Safety Officer in
accordance with ANSI Z 136.1 when workers use or are exposed to Class IIIB or Class IV lasers.
What are some things should avoid doing?
What are some things should avoid doing?
Do not wear gloves, rings, watches or loose clothing. Tie back and confine long hair.
Do not lean on machine. Stand erect. Keep the face and eyes away from flying chips.
Do not make adjustments while the machine is operating. Wait until the machine has come to a
complete stop.
Do not place hands on work turning in the lathe.
Do not use calipers or gauges on a workpiece while machine is moving.
Do not make heavy cuts on long slender pieces because the work could bend and fly out of the lathe.
Do not leave lathe unattended while it is running.
The procedure when equipment safety guard not functioning or removed
The procedure when equipment safety guard not functioning or removed
Mechanical equipment (plant, machinery and hand-held power tools) can cause serious injuries, including
open wounds, fractures and amputations. Some injuries can result in death. Sprains and strains often result
when mechanical equipment is used incorrectly. Bad working posture contributes to many such injuries.
The most common mechanical equipment injuries are to hands and fingers, which may be cut, sprained,
dislocated, broken, crushed, or cut off by machinery or tools. Eye injuries can be caused by heat or radiation
or by objects thrown from moving mechanical parts.
Key point
Key point
The workplace must have a maintenance program to ensure that all equipment and machines are in safe
working order.
Mechanical equipment injuries can cause long periods of time off work, and sometimes permanent
disability. Many injuries happen in the construction, agricultural and manufacturing industries.
When working with mechanical equipment, personal protective equipment may include protective gloves,
arm guards, safety glasses, hard hats, and safety boots.
Guards
Guards
Guards attached to mechanical equipment protect from the moving parts of machines. Machine guards
must never be removed and if a guard is damaged or missing, the machine must not be used until it can
be repaired or replaced. A missing or damaged guard must be reported at once.
If guards are removed during cleaning, make sure they are replaced and checked by an authorized person
before the machine is used. Never start machinery during cleaning.
Your preview ends here
Eager to read complete document? Join bartleby learn and gain access to the full version
- Access to all documents
- Unlimited textbook solutions
- 24/7 expert homework help
2/4/2023, 2
:
02 p. m.
MEM07032 - THEORY - Use workshop machines for basic operations - PRE LEARNING: Attempt review
Página 42 de 58
https://baxter.edfibre.com/gradejet/mod/quiz/review.php
?
attempt=147249&cmid=18279
Question
4
Complete
Marked out of
1.00
'Locking out' equipment
'Locking out' equipment
Locking out is one way of stopping electrically powered machinery from starting during maintenance. A
lock is attached to the machine switch so it cannot be turned on.
The person working with the machine should hold the only key to the lock. A lock must only be removed by
the person who attached it to the equipment or machinery. Procedures must be put in place for the
removal of the lock should that person not be available (for example, if there has been a change of shift
workers, or if the person authorized to remove the lock has been called away).
'Danger' and 'Out of Service' tags
'Danger' and 'Out of Service' tags
Red and black 'DANGER' tags are designed for the protection of individual people. The only person permitted
to remove a personal 'DANGER' tag is the person whose name is on the tag.
Yellow and black 'OUT OF SERVICE' tags are used to prevent accidents or damage to machinery that is out
of service for repairs.
All faulty equipment should be tagged so that it cannot be used until it is replaced or repaired.
The safe work procedures for removal of 'DANGER' and 'OUT OF SERVICE' tags at all workplace must be
followed.
Review questions
Write detailed responses to the following questions
Write detailed responses to the following questions
1.
State three (3) safety precautions, relating to machine safety
machine safety, which should be observed when using a
lathe.
NOTE:
NOTE:
Do not state any safety precautions relating to personal safety equipment. E.g. safety glasses,
etc.
1. Make sure the lathe has an emergency stop button (e-stop).
2. Centre-drill work deeply enough to provide support for the piece while it is turning
3. Secure and clamp the piece being worked.
2.
Name three measuring tools that you would use when machining?
The measurement tools that we are going to use in machining are numerous, although depending on the
work that we are doing, we will use more than others, for example squares, templates and gauges,
goniometer, dial indicator, feeler gauge, alexometer, vernier. calibrate. , micrometer, gauge or height
gauge, pattern blocks among others. 3 tools and how to use them are described below.
1) A micrometer is a tool that measures the size of an object by enclosing it. Some models can even
perform measurements in units of 1
μ
m. Unlike manual calipers, micrometers adhere to the Abbe principle,
allowing them to make more precise measurements.
In general, the term "micrometer" refers to outside micrometers.
2) Vernier caliper, an instrument for making very precise linear measurements introduced in 1631 by Pierre
Vernier of France. It uses two graduated scales: a ruler-like main scale and a specially graduated auxiliary
scale, the vernier, which slides parallel to the main scale and allows readings of a division fraction on the
main scale. Vernier calipers are widely used in scientific laboratories and manufacturing for quality control
measurements.
3) A goniometer is a device in the form of a semicircle or circle graduated at 180º or 360º, used to measure
or construct angles. This instrument allows you to measure angles between two objects, such as two
points on a coast, or a star, usually the Sun, and the horizon. With this instrument, if the observer knows the
elevation of the Sun and the time of day, he can determine his latitude quite precisely by means of simple
mathematical calculations.
3.
State three reasons for using coolant when using workshop machines?
Coolants are an instrumental part of machining, including grinding, milling, and turning. They help extend
tool life and provide an improved surface finish of the parts being machined. Understanding the role and
types of coolant help you select a coolant that is the right fit for your machine and operation. By properly
maintaining the concentration levels of your coolant, you extend not only the life of the coolant but also
your tools and machine.
The critical functions of coolant in the machining process include:
1. Reducing and removing the heat build-up in the cutting zone and workpiece
2. Provides lubrication to reduce friction between the tool and removal of the chips
3. Flushes away chips and small abrasive particles from the work area and protects against corrosion.
4.
Why is it necessary to thin the web of a drill after the drill has been shortened by repeated sharpening?
The rake angle of the cutting edge of a drill reduces toward the centre, and it changes into a negative
angle at the chisel edge. During drilling, the centre of a drill crushes the work, generating 50–70% of the
cutting resistance. Web thinning is very effective for reduction in the cutting resistance of a drill, early
removal of cut chips at the chisel edge, and better biting.
Your preview ends here
Eager to read complete document? Join bartleby learn and gain access to the full version
- Access to all documents
- Unlimited textbook solutions
- 24/7 expert homework help
2/4/2023, 2
:
02 p. m.
MEM07032 - THEORY - Use workshop machines for basic operations - PRE LEARNING: Attempt review
Página 43 de 58
https://baxter.edfibre.com/gradejet/mod/quiz/review.php
?
attempt=147249&cmid=18279
Question
5
Correct
Mark 1.00 out
of 1.00
Question
6
Complete
Marked out of
1.00
Information
Clearly label the following features of the twist drill shown below.
Flute
La
Your answer is correct.
Review questions
Write detailed responses to the following questions
Write detailed responses to the following questions
6.
Why when a lathe is not in use, does a seemingly logical and typical but unsafe storage place for the
chuck wrench is in the chuck?
Misuse of a standard chuck wrench is a common source of lathe accidents.When a lathe is not in use, a
seemingly logical and typical but unsafe storage place for the chuck wrench is in the chuck. The danger is
that an operator may turn on the lathe without checking to see where the wrench is located. It can fly out
of the chuck, and across the shop, causing a serious injury to anyone in the area.
Spring-loaded, self-ejecting chuck wrenches, available in several sizes, can eliminate this hazard by not
allowing the wrench to remain in the chuck. They are available in several sizes.
7.
Fill in the missing words:
When machine guards removed and if a guard is damaged or missing, the machine must
not be used until it can be
repaired or
replaced .
8.
What are the correct Lathe cutter setup 7 steps?
Step 1: Get the Right Too: All the Setup steps are done with the lathe powered off. Make sure there is no
chance of accidentally turning on the machine.
Step 2: Chuck the Part: Load the cylindrical part in the lathe.
Step 3: Load Cuter Tool: Install a regular cutting bit in the tool post. Make sure it is the tool that intend to use
for the first cut.
Step 4: Set Ruler in Position: Lock the cam on the tool post.
Step 5: Reading the Ruler: If the tool height is set correctly, the ruler will be vertical.
Step 6: Take First Test Cut: Release cam and remove cutter. Install it again longitudinally along the lathe
axis, and flip it around to take a facing cut.
Step 7: Final Adjustments: If you wanted to take a facing cut only, then you are done, if not and you need to
turn a part along its axis, you need to take the tool out and set it up again perpendicular to the part.
9.
What are some good safety principles to follow when using a lathe?
- Do not wear gloves, rings, watches or loose clothing. Tie back and confine long hair.
- Do not lean on machine. Stand erect. Keep the face and eyes away from flying chips.
- Do not make adjustments while the machine is operating. Wait until the machine has come to a
complete stop.
- Do not place hands on work turning in the lathe.
- Do not use calipers or gauges on a workpiece while machine is moving.
- Do not make heavy cuts on long slender pieces because the work could bend and fly out of the lathe.
- Do not leave lathe unattended while it is running.
SECTION 3 OPERATE MACHINE
SECTION 3 OPERATE MACHINE
3.1
Mount material to be machined and secure using clamping device/
3.1
Mount material to be machined and secure using clamping device/
Your preview ends here
Eager to read complete document? Join bartleby learn and gain access to the full version
- Access to all documents
- Unlimited textbook solutions
- 24/7 expert homework help
2/4/2023, 2
:
02 p. m.
MEM07032 - THEORY - Use workshop machines for basic operations - PRE LEARNING: Attempt review
Página 44 de 58
https://baxter.edfibre.com/gradejet/mod/quiz/review.php
?
attempt=147249&cmid=18279
appropriate to the material and work requirements
appropriate to the material and work requirements
Lathe Accessories
Lathe Accessories
a. Chucks. (1) General. Workpieces are held to the headstock spindle of the lathe with chucks, faceplates, or
lathe centers. A lathe chuck is a device that exerts pressure on the workpiece to hold it secure to the
headstock spindle or tailstock spindle. Commonly used with the lathe are the independent chuck, the
universal scroll chuck, the combination chuck, the hollow headstock spindle chuck, the lathe tailstock
chuck, the collet chuck, and the step chuck. (2) Independent Chuck. (a) The independent chuck (figure 14)
generally has four jaws which are adjusted individually on the chuck face by means of adjusting screws.
The chuck face is scribed with concentric circles which are used for rough alignment of the jaws when
chucking round workpieces. The final adjustment is made by turning the workpiece slowly and using gages
to determine its concentricity. The jaws are then readjusted as necessary to align the workpiece to desired
tolerances. (b) The jaws of the independent chuck may be used as in figure 14, or may be reversed so that
the steps face in the opposite direction; thus, workpieces can be gripped either externally or internally. The
independent chuck can he used to hold square, round, octagonal, or irregular shaped workpieces in either
a concentric or eccentric position due to the independent operation of each jaw. (c) Because of its
versatility and capacity for fine adjustment, the independent chuck is commonly used for mounting
workpieces that require extreme accuracy. (3) Universal Scroll Chuck. (a) The universal scroll chuck (figure
14 on the previous page) usually has three jaws which move in unison as an adjusting pinion is rotated. The
advantage of the universal scroll chuck is its ease of operation in centering the work for concentric turning.
This chuck is not as accurate as the independent chuck but, when in good condition, it will center the work
automatically within 0.003 of an inches of complete accuracy.
(b) The jaws are moved simultaneously within the chuck by means of a scroll or spiral threaded plate. The
jaws are threaded to the plate and move an equal distance inward or outward as the scroll is rotated by
means of the adjusting pinion. Since the jaws are individually aligned on the scroll, the jaws cannot be
reversed. However, the chuck is usually supplied with two sets of jaws which can be interchanged. (c) The
universal scroll chuck can be used to hold and automatically center round or hexagonal workpieces.
Having only three jaws, the chuck cannot be used effectively to hold square, octagonal, or irregular shapes.
(4) Combination Chuck. A combination chuck combines the features of the independent chuck and the
universal scroll chuck and can have either three or four jaws. The jaws can be moved in unison on a scroll
for automatic centering or can be moved individually if desired by separate adjusting screws. (5) Drill
Chuck. The drill chuck is a small universal-type chuck which can be used in either the headstock spindle or
in the tailstock for holding straight-shank drills, reamers, taps, or small- diameter workpieces. The drill
chuck has three or four hardened steel jaws which are moved together or apart by adjusting a tapered
sleeve within which they are contained. The drill chuck is capable of centering tools and small-diameter
workpieces to within 0.002 or 0.003 of an inch when firmly tightened. (6) Hollow Headstock Spindle Chuck.
The hollow headstock spindle chuck is similar to a drill chuck but is hollow. It is provided with threads to
screw it onto the headstock spindle nose. This chuck can be used to hold rods, tubes, or bars which are
passed through the headstock spindle. It is generally capable of centering workpieces to an accuracy of
0.002 of an inch. (7) Collet Chuck. (a) The collet chuck is the most accurate means of holding small
workpieces in the lathe. The collet chuck consists of a spring machine collet and a collet attachment which
secures and regulates the collet on the headstock spindle of the lathe. (b) The spring machine collet (figure
15 on the following page) is a thin metal bushing with an accurately machined bore and a tapered exterior.
The collet has three lengthwise slots to permit its sides to be sprung slightly inward to grip the workpiece. To
grip the workpiece accurately, the collet must be no more than 0.001 inch larger or smaller than the
diameter of the piece to be chucked. For this reason, spring machine collets are generally supplied in sets
with various capabilities in 1/16, 1/32, or 1/64 inch increments. For general purposes, the spring machine
collets are limited in capacity to 1 inch in diameter. (c) The collet attachment which, with the spring
machine collet, forms the collet chuck and consists of a collet sleeve, a draw bar, and a handwheel or hand
lever to move the draw bar. The collet is fitted to the right end of the headstock spindle. The draw bar
passes through the headstock spindle and is threaded to the spring machine collet. When the draw bar is
rotated by means of the handwheel, the collet is pulled inward and the collet walls are cammed together
by contact with the collet sleeve,
(d) Collet chucks are usually standard equipment on toolroom-type engine lathes and on horizontal turret
lathes. Spring machine collets are available in different shapes in order to chuck square and hexagonal
workpieces of small dimensions as well as round workpieces. (8) Jacobs Rubber-Flex Collets. The rubber
flex collet (figure 16 on the following page) is comprised of hardened alloy steel jaws bonded together with
oil-resistant Hycar synthetic rubber. The collets have a range of 1/8 inch per collet and the gripping power
and accuracy remain constant throughout the entire collet capacity. These collets are designed for heavy-
duty turning and possess 2 to 4 times the grip of conventional split steel type collets sleeve, tightening the
chuck to the workpiece.
Your preview ends here
Eager to read complete document? Join bartleby learn and gain access to the full version
- Access to all documents
- Unlimited textbook solutions
- 24/7 expert homework help
2/4/2023, 2
:
02 p. m.
MEM07032 - THEORY - Use workshop machines for basic operations - PRE LEARNING: Attempt review
Página 45 de 58
https://baxter.edfibre.com/gradejet/mod/quiz/review.php
?
attempt=147249&cmid=18279
(9) Step Chuck. The step chuck is a variation of the collet chuck, but is intended for accurate holding of
workpieces larger than 1 inch in diameter. The step chuck consists of the handwheel or hand lever collet
attachment and a step chuck machine collet in place of the regular spring machine collet. The step chuck
machine collet, which is split into three sections like the spring machine collet, is threaded to the draw bar
of the collet attachment. As the step chuck machine collet is drawn into the collet sleeve, the three sections
of the collet are cammed against the workpiece by an inside taper in the collet sleeve. The step chuck is
supplied in 2, 3, 4, and 5-inch sizes, the size indicating the maximum diameter of the workpieces that can
be supported. The step chuck machine collets are furnished blank and machined on the lathe to the
desired step diameter.
(10) Lathe Tailstock Chuck. The lathe tailstock chuck is a device designed to support the ends of the
workpieces in the tailstock when a lathe center cannot be conveniently used. The chuck has a taper arbor
that fits the lathe tailstock spindle. The three bronze self-centering jaws of the chuck will accurately close
upon the workpieces that are between 1/4 and 1 inch in diameter. The bronze jaws provide a good bearing
surface for the workpiece. The jaws are adjusted to the diameter of the workpiece and then locked in place.
b. Lathe Faceplates. (1) A lathe faceplate (figure 17 on the following page) is a flat, round plate that threads
to the headstock spindle of the lathe. The faceplate is used for clamping and machining irregularly shaped
workpieces that cannot be successfully held by chucks or mounted between centers. The workpiece is
either attached to the faceplate using angle plates or brackets or is bolted directly to the plate. Radial T-
slots in the faceplate surface facilitate mounting workpieces. The faceplate is valuable for mounting
workpieces in which an eccentric hole or projection is to be machined. The number of applications of the
faceplate depends upon the ingenuity of the machinist. (2) A small faceplate, known as a driving faceplate,
is used to drive the lathe dog for workpieces mounted between centers. The driving faceplate usually has
fewer T-slots than the larger faceplates. When the workpiece is supported between centers, a lathe dog is
fastened to the workpiece and engaged in a slot of the driving faceplate. c. Lathe Centers. (1) General. Lathe
centers (figure 18 on page 39) are the most common devices for supporting workpieces in a lathe. Most
lathe centers have a tapered point with a 600 included angle to fit the workpiece holes with the same
angle. The workpiece is supported between two centers, one in the headstock spindle and one in the
tailstock spindle. Centers for lathe work have standard tapered shanks that fit into the tailstock directly and
into the headstock spindle, using a center sleeve to convert the larger bore of the spindle to the smaller
taper size of the lathe center. The centers are referred to as live centers or dead centers, depending upon
whether they move with the workpiece or remain stationary. The most common types of centers are
described below. (2) Male Center. The male center or plain center is the type used in pairs for most general
lathe turning operations. The point is ground to a 60° cone angle. When used in the headstock spindle,
where it revolves with the workpiece, it is commonly called a live center. When used in the tailstock spindle,
where it remains stationary when the workpiece is turning, it is called a dead center. Dead centers are
always hard and must be lubricated very often to prevent overheating.
(3) Pipe Center. The pipe center is very similar to the male center, but its cone is ground to a greater angle
and is larger in size. It is used for holding pipe and tubing in the lathe while they are being machined. (4)
Female Center. The female center is conically bored at the tip and is used to support workpieces that are
pointed at the end. (5) Half-Male Center. The half-male center is a male center that has a portion of the 60°
cone cut away. The half-male center is used as a dead center in the tailstock where complete facing is to
be performed. The cutaway portion of the center faces the cutting tool and provides the necessary
clearance for the tool when facing the surface immediately around the drilled center in the workpiece. (6)
V-Center. The V-center is used to support round workpieces at right angles to the lathe axis for special
operations such as drilling or reaming. d. Lathe Dogs. (1) Lathe dogs (figure 19 on page 39) are cast metal
devices used in conjunction with a driving plate or a faceplate to provide a firm connection between the
headstock spindle and the workpiece that is mounted between centers. This firm connection permits the
workpiece to be driven at the same speed as the spindle under the strain of cutting. Frictional contact
alone, between the live center and the workpiece, is not sufficient to drive the workpiece. Three common
types of lathe dogs are illustrated in figure 19. Lathe dogs may have bent tails or straight tails. When the
bent tail dogs are used, the tail fits into a slot of the driving face plate. When straight tail dogs are used, the
tail bears against a stud projecting from the faceplate. (2) The bent tail lathe dog with a headless setscrew
is considered safer than the dog with the square head screw because the headless setscrew reduces the
danger of the dog catching in the operator's clothing and causing an accident.
Your preview ends here
Eager to read complete document? Join bartleby learn and gain access to the full version
- Access to all documents
- Unlimited textbook solutions
- 24/7 expert homework help
2/4/2023, 2
:
02 p. m.
MEM07032 - THEORY - Use workshop machines for basic operations - PRE LEARNING: Attempt review
Página 46 de 58
https://baxter.edfibre.com/gradejet/mod/quiz/review.php
?
attempt=147249&cmid=18279
Between Centres
Between Centres
Advantages
Advantages
Work may be removed and replaced accurately in position without any additional resetting.
Can be easily transferred to milling machine or cylindrical grinder.
Work can be turned at each end and the diameters will be concentric
3.2
Operate machine to suit work and material requirements
3.2
Operate machine to suit work and material requirements
Functions of the Centre Lathe
Functions of the Centre Lathe
The purpose of the Centre Lathe is to produce:
Cylindrical shapes (turning), form flat surfaces (facing).
Angles/bevels
To cut threads
Lathes vary considerably in size. The size of the lathe is determined by the swing (largest
diameter of work) and the distance between centers (longest work that can be held)
Common engineering materials
Common engineering materials
Introduction:
Introduction:
This unit refers to selecting the correct materials for the application in which the engineered part is being
used. This selection process includes choosing the material, paying attention to its specific type or grade
based on the required properties. Engineers will select a grade of material based on its properties such as
malleability or tensile strength. Composites comprise two materials, such as a metallic mesh and a resin,
the combination of which also depends on the properties required.
Materials from which the item is to be manufactured are noted on the engineering drawing using standard
material and grade codes. It is important that manufacturers do not interchange materials because the
switch may make the products susceptible to failures.
Classification of materials:
Classification of materials:
Metals and non-metals
Ferrous and non-ferrous metals
Polymers (thermoplastics, thermosetting and elastomers) Ceramics and glasses Composite materials
Properties of materials:
Properties of materials:
Ferrous materials
Ferrous materials
Contain iron in their internal structure, i.e. tool steel, cast iron, carbon and alloy steels, coated
steel, etc.
Contain small amounts of other metals or elements to give them the required properties,
Are magnetic and give little resistant to corrosion.
·Stainless steel, magnetic state is called ferritic stainless steel.
Non-ferrous materials
Non-ferrous materials
Aluminum: lightweight, low strength, easily shaped,
Cooper: Highly malleable, with high electrical conductivity,
Lead: heavy, soft, malleable metal, low melting point, low strength,
Tin: Soft, malleable, low tensile strength, used to coat steel to prevent corrosion,
Refractory metals,
Silver, platinum and gold
Nickel: is a metal magnetic at or near room temperature, high electrical and thermal
conductivity.
Bulk nickel is non-magnetic.
Polymer materials:
Polymer materials:
Polyethylene (low density), polyethylene (high density), polyvinyl chloride, polytetrafluoroethylene,
polypropylene, polystyrene, polymethyl methacrylate, phenol formaldehyde, nylon (6,6), polyester (PET),
polycarbonate.
Your preview ends here
Eager to read complete document? Join bartleby learn and gain access to the full version
- Access to all documents
- Unlimited textbook solutions
- 24/7 expert homework help
2/4/2023, 2
:
02 p. m.
MEM07032 - THEORY - Use workshop machines for basic operations - PRE LEARNING: Attempt review
Página 47 de 58
https://baxter.edfibre.com/gradejet/mod/quiz/review.php
?
attempt=147249&cmid=18279
Composite materials:
Composite materials:
Reinforced concrete (concrete alone will not compress or shatter, will not survive tensile loading
it will quickly break, steel bars added to became reinforced concrete) and masonry,
Cob or mud bricks using clay and straw,
Composite wood such plywood,
Reinforced plastics, such as fibre-reinforced polymer i.e. fiberglass (strong and stiff but also
brittle, flexible and ductile);
Ceramic matrix composites (composite ceramic and metal matrices)
Metal matrix composites,
Advanced composite materials like carbon fibers and silicon carbide,
Fiber reinforced used in swimming pools are non-corrosive.
Thermosetting materials:
Thermosetting materials:
RIM thermosetting: (pDCPD) (polydicyclopentadiene), polyurethanes, polyureas, structural foams, RTM
Thermosetting (Fiberglass reinforced): polyester, vinyl Ester, polyimides,
Other types of thermosets and thermoset resins:
Epoxy (e.g. carbon fiber epoxy resin), phenolics, bismaleimide (BMI), fluoropolymers, polytetrafluoroethylene
(PTFE), polyvinylidene fluoride (PVDF), melamine silicone, formaldehyde, polyester and urea formaldehyde
are:
Available moulded-in tolerances,
Choice of color and surface finishes,
High strength-to-weight ratio and performance,
Outstanding dielectric strength,
Low thermal conductivity and microwave transparency,
Resistance to corrosion effects and water,
Low tooling/set-up costs
Reduced production costs over fabrication using metals.
Good electrical insulator, hard, brittle unless reinforced, resists chemicals well,
Used for casting and encapsulation, adhesives, bonding of other materials,
Thermoplastic:
Thermoplastic:
PVC or CPVC, polypropylene, PDVF, ABS, nylon and polyethylene, polyamide,
Polyethylene gas thanks used to transport natural gas. High pressure polyethylene to encapsulate rigid
objects like electrical equipment, low pressure polyethylene is very elastic ideal for insulating electrical
cables. Polyamide is associated with the production of ropes and belts.
Thermoplastics can withstand corrosive materials and corrosive environments, Being able to carry
materials of extreme temperatures (hot or cold),
Their capacity to handle virtually any type of fluid transport application.
Ceramics:
Ceramics:
High melting points (they are heat resistant) Great hardness and strength,
Considerable durability (they are long-lasting and hard-wearing) Low electrical and thermal conductivity
(good insulators), Chemical inertness (they are unreactive with other chemicals), Ferrites (iron-based
ceramics) happen to make great magnets (because of their iron content), but most ceramics are
nonmagnetic materials,
They are fragile and brittle like glass and porcelain.
Composite materials:
Composite materials:
Not isotropic (independent of direction of applied force) in nature, but they are anisotropic (different
depending on the direction of the applied force or load).
The stiffness of a composite panel will often depend upon of the applied forces and/or moments. Three
Three
different types of cutting tool materials used for cutting material in a workshop machine
different types of cutting tool materials used for cutting material in a workshop machine
High Speed Steel (HSS)
Tungsten Carbide
Sintered Inserts Ceramics
Basic Operations of a Lathe
Basic Operations of a Lathe
Facing
Facing
Parallel Turning
Parallel Turning
Taper Turning
Taper Turning
Form Turning
Form Turning
Boring
Boring
Thread Turning
Thread Turning
Knurling
Knurling
Drilling
Drilling
Facing
Facing in machining can be used in two different areas: facing on a milling machine and facing on a lathe.
Facing on the milling machine involves various
milling
operations, but primarily
face milling
. On the lathe,
facing is commonly used in
turning
and
boring
operations. Other operations remove material in ways
similar to facing, for example,
planning,
shaping
, and
grinding
, but these processes are not labeled by the
term "facing."
Facing on the lathe uses a facing tool to cut a flat surface perpendicular to the work piece's rotational axis.
A facing tool is mounted into a tool holder that rests on the carriage of the
lathe
. The tool will then feed
perpendicularly across the part's rotational axis as it spins in the jaws of the chuck. A user will have the
option to hand feed the machine while facing or use the power feed option. For a smoother surface, using
the power feed option is optimal due to a constant
feed rate
. Facing will take the work piece down to its
finished length very accurately. Depending on how much material needs to be taken off, a
machinist
can
choose to take roughing or finishing cuts.
[1]
Factors that affect the quality and effectiveness of facing
operations on the lathe are
speeds and feeds
, material
hardness
, cutter size, and how the part is being
clamped down.
Your preview ends here
Eager to read complete document? Join bartleby learn and gain access to the full version
- Access to all documents
- Unlimited textbook solutions
- 24/7 expert homework help
2/4/2023, 2
:
02 p. m.
MEM07032 - THEORY - Use workshop machines for basic operations - PRE LEARNING: Attempt review
Página 48 de 58
https://baxter.edfibre.com/gradejet/mod/quiz/review.php
?
attempt=147249&cmid=18279
Parallel machining (or turning)
Parallel machining (or turning) on a lathe refers to a cut taken on a workpiece along its outside or
inside diameter on the longitudinal axis, which is parallel to the bed of the lathe.
This really could apply to Metal or Wood lathes, but it is the sense of achieving a purely PARALLEL object, that
is the basic premise of a Horizontal Lathe. Which is the most common version and perception of the
machines. VERTICAL LATHES also exist in great numbers. Parallel turning on them is Vertical.
We Parallel Turn the giant objects of our time, as VERTICAL is not really an option when things are 25 to 100+
feet long. Things like Gun Barrels and Propeller shafts for Battleships and most all other Naval vessels and
commercial ships.
The most common companion operation, turning in the PERPENDICULAR sense, is generally referred to as
“Facing”. Often the same general tooling, but the “Cross Slide” moves 90 degrees from the parallel. This
process can be at other angles, but this is most common. This allows Cylinders, Tubes, Discs, and most
other variations to be a practical process.
Taper turning
Taper turning as a machining operation is the gradual reduction in diameter from one part of a
cylindrical workpiece to another part. Tapers
Tapers can be either external or internal.
A Drift
A Drift is used to remove a Morse taper drill from the spindle of a drilling machine
Form Turning
Form Turning
Turning
Turning is a form
form of machining, a material removal process, which is used to create rotational parts by
cutting away unwanted material. The turning
turning process requires a turning
turning machine or lathe
lathe, workpiece,
fixture, and cutting tool.
Lathe boring
Lathe boring
Lathe boring
Lathe boring is a cutting operation that uses a single point cutting tool or a boring
boring head to produce
conical or cylindrical surfaces by enlarging an existing opening in a workpiece. For nontape red holes, the
cutting tool moves parallel to the axis of rotation.
Thread turning
Thread turning
Both inch and metric screw threads
threads can be cut using the lathe
lathe. A thread
thread is a uniform helical groove cut
inside of a cylindrical workpiece, or on the outside of a tube or shaft
........
Hand coordination, lathe
lathe
mechanisms, and cutting tool angles are all interrelated during the thread
thread cutting process.
Your preview ends here
Eager to read complete document? Join bartleby learn and gain access to the full version
- Access to all documents
- Unlimited textbook solutions
- 24/7 expert homework help
2/4/2023, 2
:
02 p. m.
MEM07032 - THEORY - Use workshop machines for basic operations - PRE LEARNING: Attempt review
Página 49 de 58
https://baxter.edfibre.com/gradejet/mod/quiz/review.php
?
attempt=147249&cmid=18279
Knurling
Knurling is a manufacturing process and technique of creating concave and bumps on the surface of
workpiece, presented as the pattern of straight, angled or crossed lines is rolled into the material, the
knurling
knurling operation is usually performed on the lathe
lathe machine, including CNC turning lathes
lathes.
Drilling
Drilling
The tailstock of a lathe
lathe can be used for drilling
drilling, with the aid of a drill
drill chuck attachment.
The drill
drill chuck has a morse taper shaft which can be push into the shaft of the tailstock, locking it in
position. The usual starting point for drilling
drilling with a centre lathe
lathe is to use a countersink bit.
The two most common shanks found on twist drills
The two most common shanks found on twist drills
1.
1.
Taper
Taper
2.
2.
Straight
Straight
Types of drills shown below.
Types of drills shown below.
Your preview ends here
Eager to read complete document? Join bartleby learn and gain access to the full version
- Access to all documents
- Unlimited textbook solutions
- 24/7 expert homework help
2/4/2023, 2
:
02 p. m.
MEM07032 - THEORY - Use workshop machines for basic operations - PRE LEARNING: Attempt review
Página 50 de 58
https://baxter.edfibre.com/gradejet/mod/quiz/review.php
?
attempt=147249&cmid=18279
Cutting Speed
Cutting Speed
This is the rate, expressed in metres per minute(m/min), at which a point on the circumference of the
rotating work passes the tool bit.
If it were possible to measure the length of the chip removed in one minute, this length in metres would be
the cutting speed.
Feed
Feed
Feed is the distance that the tool advances along the work during each revolution. It is usually expressed in
millimetres per revolution (mm/rev).
Finishing feed rate 0.05 mm/rev (0.002”/rev) Roughing feed rate 0.25 mm/rev (0.010”/rev)
Factors Affecting Cutting Speed
Factors Affecting Cutting Speed
Type of material being cut
Cutting speed is determined by type of material being cut (from chart)
Cutting tool material
HSS (high speed steel)
Tungsten carbide inserts
Ceramics
Depth of cut
Finishing cuts, the speed may be increased to improve the finish
Rate of feed
Roughing cut, where course feeds are used, the speed should be reduced.
Rigidity of the work
Short work held in four jaw chuck maybe turned faster than long work supported by steadies.
Power, strength, and condition of the lathe
larger more powerful lathes can handle higher cutting speeds.
Coolant or lubricant used.
Cutting speeds for most materials can be increased by using the correct lubricant.
Shape of tool
In general, the cutting speed should vary inversely with the width of the cutting edge in contact with the
work.
RPM FORMULA
RPM FORMULA
REVS PER MINUTE =
E.G
E.G
Calculate the RPM for a diameter 80 job if the cutting speed is 30 m/min? RPM
=
3.1
Check machined component
against work
requirements
and
3.1
Check machined component
against work
requirements
and
predetermined finish
predetermined finish
Parts of a Lathe
Parts of a Lathe
Your preview ends here
Eager to read complete document? Join bartleby learn and gain access to the full version
- Access to all documents
- Unlimited textbook solutions
- 24/7 expert homework help
2/4/2023, 2
:
02 p. m.
MEM07032 - THEORY - Use workshop machines for basic operations - PRE LEARNING: Attempt review
Página 51 de 58
https://baxter.edfibre.com/gradejet/mod/quiz/review.php
?
attempt=147249&cmid=18279
The Carriage
The Carriage
The Carriage and Saddle provide the mechanisms and tool holding to allow the Lathe to machine
accurately.
Most centre lathes have some form of power feed mechanism to provide automatic movement to the
cutting tool. Power feed can be applied to both the saddle and cross slide.
Feed and Lead Screw
Feed and Lead Screw
When the feed lever is engaged power is connected from the feed shaft to the saddle and cross slide. This
provides automatic feeding for facing and turning.
Centre lathes equipped with power feed also have provision for screw-cutting. When the Leadscrew lever is
engaged threads can be cut.
The Tailstock
The Tailstock
The tailstock is used mainly to support the right-hand end of the work. It may be moved and clamped in
position along the bed.
Lathe Size
Lathe Size
r - Radius of work (Centre height of lathe)
d -Diameter of work (Swing of lathe)
Lc - Length between centres
Your preview ends here
Eager to read complete document? Join bartleby learn and gain access to the full version
- Access to all documents
- Unlimited textbook solutions
- 24/7 expert homework help
2/4/2023, 2
:
02 p. m.
MEM07032 - THEORY - Use workshop machines for basic operations - PRE LEARNING: Attempt review
Página 52 de 58
https://baxter.edfibre.com/gradejet/mod/quiz/review.php
?
attempt=147249&cmid=18279
Lb - Length of the bed
Centre Lathe work holding
Centre Lathe work holding
Reference
Fitting & Machining (Culley) pp247 – 261 (TJ1185 .f3 2003)
Types of spindles
Types of spindles
Jaws are adjusted one at a time to hold regular and irregular work
Much greater gripping force
Jaws can be reversed for holding larger work
Disadvantages
Disadvantages
Longer to setup
Three Jaw Self-cantering Chuck
Three Jaw Self-cantering Chuck
Advantages
Advantages
Less time to setup
Disadvantages
Disadvantages
Work must be accurately
Machined round or hexagonal in section Less gripping force than four jaw
Jaws cannot be reversed,
there is a second set of reversed jaws
Your preview ends here
Eager to read complete document? Join bartleby learn and gain access to the full version
- Access to all documents
- Unlimited textbook solutions
- 24/7 expert homework help
2/4/2023, 2
:
02 p. m.
MEM07032 - THEORY - Use workshop machines for basic operations - PRE LEARNING: Attempt review
Página 53 de 58
https://baxter.edfibre.com/gradejet/mod/quiz/review.php
?
attempt=147249&cmid=18279
Between Centres
Between Centres
Advantages
Advantages
Work may be removed and replaced accurately in position without any additional resetting
Can be easily transferred to milling machine or cylindrical grinder.
Work can be turned at each end and the diameters will be concentric.
Face Plate
Face Plate
Faceplates are used for holding work that cannot be conveniently held in a chuck.
Types of Centres
Types of Centres
Plain centres
Plain centres
Used in the tail stock and head stock.
Must be lubricated if used in tail stock.
There are two types
Hard centres which have an inserted tip and are held in tail stock.
Soft centres which are held in head stock and rotate with workpiece.
Live centres use taper roller and ball bearings. This allows them to run at higher speeds.
Your preview ends here
Eager to read complete document? Join bartleby learn and gain access to the full version
- Access to all documents
- Unlimited textbook solutions
- 24/7 expert homework help
2/4/2023, 2
:
02 p. m.
MEM07032 - THEORY - Use workshop machines for basic operations - PRE LEARNING: Attempt review
Página 54 de 58
https://baxter.edfibre.com/gradejet/mod/quiz/review.php
?
attempt=147249&cmid=18279
Pipe centre has various cone centres to suit diameters of pipe.
Driving centres are used to turn along the entire length of job without stopping. This eliminates the need for
a lathe carrier.
3.4
Make adjustments, as required
3.4
Make adjustments, as required
7 major Problems with Lathe
7 major Problems with Lathe
Lathe machine is the most common and oldest equipment to be used in industries to cut, groove, drill, and
do other machine-related operations. As it is a machine, from time to time, there can be problems.
Metal lathe chattering
Weird vibration on a wood lathe
Carriage problem
Threads cutting issues
Improper metal cuts
Tailstock slipping
Lathe machine fails
Some solutions and adjustment as below:
Some solutions and adjustment as below:
1. Metal lathe chattering
1. Metal lathe chattering
Chattering is the enemy of every machinist that will face it sooner or later unless a CNC machinist and
familiar with the HAAS Automation’s SSV technique.
However, for the regular machinists who are using general lathes like a small-sized lathe, it can get tricky.
Therefor will create a rough-cut surface and leave the chatter mark in the metal piece. It is like a car tire
leaving its mark on the dessert. And the sound it makes is the chattering noise.
The golden rule to stop chattering is to “reduce the speed and increase the feed.” Chatter frequently
originates if going too high in speed or not hitting it strong enough.
Though some operations are destined to chatter, there are few things can always do to win over.
Step 1: Make sure the rigidity is higher
Chatter occurs when the cutting pressure is too high than the rigidity of the setup. Rigidly is critical in
overcoming chatter. Always make the setup as ridge as possible.
Check all the slides are tight enough, nothing is loose. Remove compound if it is not using it. Make sure
everything is locked firmly before starting
Using tailstock every time possible is a good practice.
Just keep everything close and tight is the key to maintain rigidity. Step 2: Decrease Tool Pressure
Check out the tool bit how it is shaped, how the operator wants the finishes. If for deeper cuts, using a
rounded nose tool for a more delicate finish, the tool pressure will be higher.
But we want to lower the pressure.
Step 3: Some other tricks that work
Flip the tool upside down and machine on the other side of the hole. It will make the springy tool post/top
slide/carriage act in a completely different way and might be the one trick to get away from chatter.
Sharpen the tool bit and then try to do a pass that is deeper than the chatter area.
·Wrapping elastic bands or sticking plasticine around the work can be a good trick.
The Harding demo where they turn a 1
″
bar down to 0.5mm in one hit with a knife tool.
Check if the tool is well above the centreline when boring.
Make sure the top slide is locked in place if having a tool post on the top slide.
Put a bolt & nut under the tool against the carriage top and tighten it to provide more support for the
tool.
Using chatter grease or spray does help.
2. Vibration Problem in Lathe:
2. Vibration Problem in Lathe:
The vibrating issues occur in a lathe for numerous reasons. It could be a balancing problem. Maybe the
turning object is not cantered well, or the machine itself could have mechanical issues, and so on.
It is coming from an imbalance situation of the lathe attached to the ground.
The problem is between the workpiece and the cutting tool.
Priority 1
Priority 1
Run the lathe without attaching anything. Then it indeed is a mechanical problem.
The more solid and robust the attachment of the chunk is with the faceplate, the more it will reduce the
vibration.
Irregular large bowl blanks produce the vibration often. Run the lathe and increase the speed gradually in
this case. See at what point the chunk is turning smoothly.
Checking leg extension if it is settled with the floor in a proper flat situation is critical. If any imbalanced
surface contact, either move the whole lathe to a new place or just use a flat rubber piece or a chunk of
paper folded. Put it right beneath the leg where the surface is not contacting smoothly.
Put some extra weight on lathe if it is possible to ground it more firmly. It will absorb the movement more to
the ground. It is not recommended but still effective.
Priority 2
Priority 2
If working with small object and experiencing vibrations, this is where steady rests are a must-try option, no
matter if turning spindle or bowl. There are steady rests specially designed for bowl turners now.
Check if motor, drive belt, or headstock bearings are making any noises. May need to change them if
possible or at least repair it.
Your preview ends here
Eager to read complete document? Join bartleby learn and gain access to the full version
- Access to all documents
- Unlimited textbook solutions
- 24/7 expert homework help
2/4/2023, 2
:
02 p. m.
MEM07032 - THEORY - Use workshop machines for basic operations - PRE LEARNING: Attempt review
Página 55 de 58
https://baxter.edfibre.com/gradejet/mod/quiz/review.php
?
attempt=147249&cmid=18279
Try to use the tailstock almost every time. Tailstock is all about the support. The workpiece to be mounted
firmly between the centres. It is evident that it dramatically reduces the vibration.
If the motor does not have the vibration, then trying to mount the motor rigidly will not help that much.
Check out the leg again and try to isolate the motor entirely from the stand.
3. Carriage Problem
3. Carriage Problem
Getting a ‘stuck carriage’ in lathe machine. Not only the carriage but also the handles need to be working
perfectly for the machine to move and run efficiently.
Carriage helps the cutting tools to move in between headstock and tailstock.
At the top of the carriage, it is the Tool post that holds the cutting tools.
Compound rest holds the tool post and has a handle to rotate it to any angle for making different cutting
angles with the tools.
Cross slide holds the tool rest, and the compound rest together. Has a handle that helps to perform the
up-side movements of the tool post and compound rest together.
Then comes the saddle that holds all the components mentioned above. It moves right to the left also by
a handle.
4. Threads Cutting Problem: 2 Steps
4. Threads Cutting Problem: 2 Steps
Step 1: setting up the lathe for threading
Step 1: setting up the lathe for threading
The compound and toolpost must be clean and steady. Check that first before running the project. It
should be fine if that is a new lathe.
Always use the manual from the manufacturer of the machine to select the right gear need to cut the
thread. Look for the gear table in the book.
Then set the threading tool to the diameter of the part to be threaded. It will be the starting depth.
The scale should be set to zero both for the cross slide and the compound.
Step 2: Start cutting the thread
Step 2: Start cutting the thread
Start with aluminium instead if it is the first project. It will make life a bit easier.
Run the lathe at a slower speed and start cutting a scratch pass.
Stop the machine whenever running the tool at the end of the cut. Do the cut one at a time to avoid any
damage.
Use a thread gauge to double-check the pitch after one scratch pass.
Back the carriage away to clear the tool. Run the lathe again, but in reverse, to track the tool back to the
start point.
The tool will not touch the material while backing off the carriage. Then go for the next pass.
Turn the carriage to scale zero again. The compound and the cross slide.
5. Improper Metal Cuts
5. Improper Metal Cuts
If the lathe cutting tool has not been installed properly or ignoring the proper tool height settings, then likely
to have improper metal cuts.
It will ruin the projects and will never be satisfied. The trick for perfect installation is to remember to get an
accurate and immaculate cut.
Before start working, do not forget to centre the lathe tool correctly.
Getting the right cutting tools for the lathe is a fundamental thing to start cutting.
Select the cutting tools that can sharpen easily. Take HSS tools for example. They are easy to repair and
sharpen if gets worn.
Do not forget to set the “tool height” correctly. Because if the centre rotation of the chuck is interrupted.
The piece will loosen up very easily during operation.
Pause the machine frequently. Let it cool down and then start again.
6. Tailstock Is Slipping from The Centres
6. Tailstock Is Slipping from The Centres
It is common in turning lathe. The tailstock is slipping while trying to tighten the work-piece between the
centers.
This can happen even with the new lathe when the tailstock is not fixed properly before working. Lock it
down firmly before start cutting or turning.
7. Fails
7. Fails
Lathe machines can lead to accidents as well. Safety is a crucial key while working with any machine.
Nothing can be better than using safety goggles to protect the operator’s eyes from the dust.
The clothes can get caught within the machine; the proper workshop clothes must be worn.
The best way is clean the carriage on a regular basis to avoid metal dust on it. Use a brush to take off metal
particles but be in the distance as much possible.
This distance can help to avoid the direct contact of metal particles with the operator’s skin. These particles
may cause scrapes and bruises.
Your preview ends here
Eager to read complete document? Join bartleby learn and gain access to the full version
- Access to all documents
- Unlimited textbook solutions
- 24/7 expert homework help
2/4/2023, 2
:
02 p. m.
MEM07032 - THEORY - Use workshop machines for basic operations - PRE LEARNING: Attempt review
Página 56 de 58
https://baxter.edfibre.com/gradejet/mod/quiz/review.php
?
attempt=147249&cmid=18279
Question
7
Correct
Mark 1.00 out
of 1.00
Question
8
Complete
Marked out of
1.00
Question
9
Correct
Mark 1.00 out
of 1.00
REVIEW QUESTIONS
REVIEW QUESTIONS
Drag and drop the names from below and put them on the diagram in the best place to
Drag and drop the names from below and put them on the diagram in the best place to
describe each part of the lathe.
describe each part of the lathe.
Headstock
Feedshaft
Feed mechanism
Tailstock
Lead Screw
Compound slide
Your answer is correct.
- Review questions
Write detailed responses to the following questions
Write detailed responses to the following questions
2.
What is the purpose of the slideways?
The slides and slideways of a machined tool locate and guide members which move relative to each
other, usually changing the position of the tool relative to the workpiece. the movement generally takes the
form of translation in a straight line, but is sometimes angular rotation, e.g. tilting the wheelhead of a
universal thread grinding machine to an angle corresponding with the helix angle of the workpiece thread.
3.
If a live centre was to be used while turning on a lathe, where would the live centre be located?
Live centres use taper roller and ball bearings. This allows them to run at higher speeds. Pipe centre has
various cone centres to suit diameters of pipe. Driving centres are used to turn along the entire length of
job without stopping. This eliminates the need for a lathe carrier. This firm connection permits the
workpiece to be driven at the same speed as the spindle under the strain of cutting. Frictional contact
alone, between the live center and the workpiece, is not sufficient to drive the workpiece.
If a machine is fitted with a safety guard or shield can you remove these
If a machine is fitted with a safety guard or shield can you remove these
guards once you become familiar with that machine?
guards once you become familiar with that machine?
Select one:
True
False
!
Your preview ends here
Eager to read complete document? Join bartleby learn and gain access to the full version
- Access to all documents
- Unlimited textbook solutions
- 24/7 expert homework help
2/4/2023, 2
:
02 p. m.
MEM07032 - THEORY - Use workshop machines for basic operations - PRE LEARNING: Attempt review
Página 57 de 58
https://baxter.edfibre.com/gradejet/mod/quiz/review.php
?
attempt=147249&cmid=18279
Question
10
10
Complete
Marked out of
1.00
Question
11
11
Complete
Marked out of
1.00
Learning Activity 3
Write detailed responses to the following questions
Write detailed responses to the following questions
5.
Name three different types of cutting tool materials used for cutting material in a workshop machine.
Here are many types of cutting process done in different conditions. In such conditions along with the
general requirements of the cutting tool, they need some unique properties. To achieve this properties the
cutting tools are made up of different material. The material chosen for a particular application depends
on the material to be machined, type of machining, quantity and quality of production.
According to the material used the tools are classified into:
Carbon tool steel
High speed steel tool (HSS)
Cemented carbide
Ceramics tool
Cubic boron nitride Tool (CBN)
Diamond tool
6.
Give an advantage of using correctly sharpened cutting tools?
Smooth Cut Sharpening saves you both time and money. With regular precision sharpening, you’ll have
clean and smooth-edged tools, clear of chips and burrs. Sharpening will also prolong the life of your
blades.
7.
What is the name of the chuck shown?
Four Jaw independent chuck
8.
Name the two (2) most common shanks found on twist drills.
The two most common shanks found on twist drills
1. Taper
2. Straight
- Review questions
Write detailed responses to the following questions
Write detailed responses to the following questions
9.
Name the two (2) types of drills shown below.
1. Counterbore. 2. Countersink
10. Calculate the RPM for a diameter 40 brass job, with a cutting speed of 60 m/min?
(320* cutting speed)/ diameter of work piece
(320*60)/40 =RPM 480
11.
Calculate the RPM for a diameter 10 cast iron job, with a cutting speed of 18m/min?
(320* cutting speed)/ diameter of work piece
(320*18)/10 =RPM 576
12. Calculate the RPM for a diameter 25 mild steel job, with a cutting speed of 30m/min?
(320* cutting speed)/ diameter of work piece
(320*30)/25 =RPM 384
13.
What is the name of the tool that is used to remove a Morse taper drill from the spindle of a drilling
machine?
A Drift is used to remove a Morse taper drill from the spindle of a drilling machine.
Your preview ends here
Eager to read complete document? Join bartleby learn and gain access to the full version
- Access to all documents
- Unlimited textbook solutions
- 24/7 expert homework help
2/4/2023, 2
:
02 p. m.
MEM07032 - THEORY - Use workshop machines for basic operations - PRE LEARNING: Attempt review
Página 58 de 58
https://baxter.edfibre.com/gradejet/mod/quiz/review.php
?
attempt=147249&cmid=18279
Stay in touch
Baxter Institute
RTO No: 7030
CRICOS Provider No. 02233M
!
http://www.baxter.vic.edu.au
"
03 9650 0367
#
mail@baxter.vic.edu.au
$
%
&
'
Data retention summ
(
Get the mobile ap
Your preview ends here
Eager to read complete document? Join bartleby learn and gain access to the full version
- Access to all documents
- Unlimited textbook solutions
- 24/7 expert homework help
Related Documents
Recommended textbooks for you
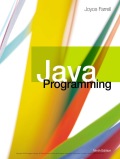
EBK JAVA PROGRAMMING
Computer Science
ISBN:9781337671385
Author:FARRELL
Publisher:CENGAGE LEARNING - CONSIGNMENT
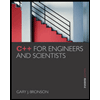
C++ for Engineers and Scientists
Computer Science
ISBN:9781133187844
Author:Bronson, Gary J.
Publisher:Course Technology Ptr

Principles of Information Systems (MindTap Course...
Computer Science
ISBN:9781285867168
Author:Ralph Stair, George Reynolds
Publisher:Cengage Learning
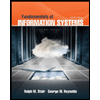
Fundamentals of Information Systems
Computer Science
ISBN:9781305082168
Author:Ralph Stair, George Reynolds
Publisher:Cengage Learning
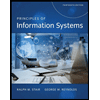
Principles of Information Systems (MindTap Course...
Computer Science
ISBN:9781305971776
Author:Ralph Stair, George Reynolds
Publisher:Cengage Learning
Recommended textbooks for you
- EBK JAVA PROGRAMMINGComputer ScienceISBN:9781337671385Author:FARRELLPublisher:CENGAGE LEARNING - CONSIGNMENTC++ for Engineers and ScientistsComputer ScienceISBN:9781133187844Author:Bronson, Gary J.Publisher:Course Technology PtrPrinciples of Information Systems (MindTap Course...Computer ScienceISBN:9781285867168Author:Ralph Stair, George ReynoldsPublisher:Cengage Learning
- Fundamentals of Information SystemsComputer ScienceISBN:9781305082168Author:Ralph Stair, George ReynoldsPublisher:Cengage LearningPrinciples of Information Systems (MindTap Course...Computer ScienceISBN:9781305971776Author:Ralph Stair, George ReynoldsPublisher:Cengage Learning
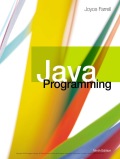
EBK JAVA PROGRAMMING
Computer Science
ISBN:9781337671385
Author:FARRELL
Publisher:CENGAGE LEARNING - CONSIGNMENT
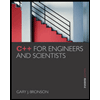
C++ for Engineers and Scientists
Computer Science
ISBN:9781133187844
Author:Bronson, Gary J.
Publisher:Course Technology Ptr

Principles of Information Systems (MindTap Course...
Computer Science
ISBN:9781285867168
Author:Ralph Stair, George Reynolds
Publisher:Cengage Learning
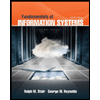
Fundamentals of Information Systems
Computer Science
ISBN:9781305082168
Author:Ralph Stair, George Reynolds
Publisher:Cengage Learning
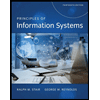
Principles of Information Systems (MindTap Course...
Computer Science
ISBN:9781305971776
Author:Ralph Stair, George Reynolds
Publisher:Cengage Learning