Chapter 20 - homework questions template Solutions (1)
xlsx
keyboard_arrow_up
School
York University *
*We aren’t endorsed by this school
Course
2700
Subject
Accounting
Date
Apr 3, 2024
Type
xlsx
Pages
27
Uploaded by CountPenguinMaster907
20-19 EOQ for manufacturer. (LO 1) Lakeland Company, which produces lawn mowers, purchases 18,000 units of a rotor blade part each year at a cost of $60 per unit. Lakeland requires a 15% annual rate of return on investment. In addition, the relevant carrying cost (for insurance, materials handling, breakage, and so on) is $6 per unit per year. The relevant ordering cost per purchase order is $150. Required 1. Calculate Lakeland’s EOQ for the rotor blade part. 2. Calculate Lakeland’s annual relevant ordering costs for the EOQ calculated in requirement 1. 3. Calculate Lakeland’s annual relevant carrying costs for the EOQ calculated in requirement 1. 4. Assume that demand is uniform throughout the year and known with certainty so that there is no need for safety stocks. The purchase-order lead time is half a month. Calculate Lakeland’s reorder point for the rotor blade part. 1000 10 1500
500 1500
20-19 (20min) EOQ for manufacturer. 1. Relevant carrying costs per part per year: Required annual return on investment 15% x $60 = $9 Relevant insurance, materials handling, breakage, etc. costs per year Relevant carrying costs per part per year With D = 18,000; P = $150; C = $15, EOQ for manufacturer is: 2 2 2DP _ [2x18.000x8150 _ (o c $15 , Totalrelevant _ (D, ordering costs ~ | q [wmoxsm] 00 =$4,500 where Q = 600 units, the EOQ. 3. At the EOQ, total relevant ordering costs and total relevant carrying cos equal. Therefore, total relevant carrying costs at the EOQ = $4,500 (from r¢ can also confirm this with direct calculation Total relevant carrying costs = (% x c) :(@xus] 2 =$4,500 where Q = 600 units, the EOQ. 4. Purchase order lead time is half a month. Monthly demand is 18,000 units = 12 months = 1,500 units per month. Demand in half a month is 4 x 1,500 units or 750 units. Lakeland should reorder when the inventory of rotor blades falls to 750 unit
Your preview ends here
Eager to read complete document? Join bartleby learn and gain access to the full version
- Access to all documents
- Unlimited textbook solutions
- 24/7 expert homework help
its will be exactly 2quirement 2). We
20-22 JIT production, relevant benefits, relevant costs. (LO 3) The | Hardware Company manufactures specialty brass door handles at i Lynchburg plant. Colonial is considering implementing a JIT produ system. The following are the estimated costs and benefits of JIT prc¢ a. Annual additional tooling costs would be $200,000. b. Average inventory would decline by 80% from the current lev $2,000,000. c. Insurance, space, materials-handling, and setup costs, which total $600,000 annually, would decline by 25%. d. The emphasis on quality inherent in JIT production would re rework costs by 30%. Colonial currently incurs $400,000 in an rework costs. e. Improved product quality under JIT production would enabl to raise the price of its product by $8 per unit. Colonial sells 4 each year. Colonial's required rate of return on inventory investment is 15% p¢ Required 1. Calculate the net benefit or cost to Colonial if it adopts JIT produr the Lynchburg plant. 2. What nonfinancial and qualitative factors should Colonial consid making the decision to adopt JIT production? 3. Suppose Colonial implements JIT production at its Lynchburg pli
Give examples of performance measures Colonial could use to ev and control JIT production. What would be the benefit of Colonia implementing an enterprise resource planning (ERP) system?
Your preview ends here
Eager to read complete document? Join bartleby learn and gain access to the full version
- Access to all documents
- Unlimited textbook solutions
- 24/7 expert homework help
Colonial ts iction oduction: vel of currently duce nual e Colonial 10,000 units er year. ction at ler when ant. 20-22 (20min) JIT production, relevant benefits, re 1. Solution Exhibit 20-22 presents the annual net benei Company of implementing a JIT production system o Other nonfinancial and qualitative factors that Coloni¢ 1t should implement a JIT system include: a. The possibility of developing and implementing sequential operations of the manufacturing proce: needed for each subassembly so that the productior b. The ability to design products that use standardized c. The ease of obtaining reliable vendors who can d with minimum lead time. d. Willingness of suppliers to deliver smaller and mor e. The confidence of being able to deliver quality prc result in customer dissatisfaction. £ The skill levels of workers to perform multiple tas! quality testing and inspection. 3. Personal observation by production line workers and o than 1n traditional plants. A JIT plant’s production prc are not obscured by piles of inventory or rework. s evaluate by personal observation than are cluttered pla logically laid out. Besides personal observation, nonfinancial pe methods of control. Nonfinancial performance meast understand measures of plant performance. Examples of time, inventory, and quality include the following: Manufacturing lead time Units produced per hour Machine setup time + manufacturing time Number of defective units ~ number of units compl In addition to personal observation and nonfit performance measures are also used. Examples o the following: Cost of rework Ordering costs Stockout costs Inventory tumover (cost of goods sold + avera The success of a JIT system depends on the <
raluate il to manufacturers to suppliers. The Enterprise Res database and gives lower-level managers, work operating information. This benefit, accompanie functions, enables the ERP system to rapidly trans supply and demand so that manufacturing and distr SOLUTION EXHIBIT 20-22 Annual Relevant Costs of Current Production System ¢ for Colonial Hardware Company Relevant Items “Annual tooling costs Required return on investment 15% per year x $2,000,000 of average inventory per y 15% per year x $400,000° of average inventory per yes Insurance, space, materials handling. and setup costs Rework costs Incremental revenues from higher selling prices Total net incremental costs Annual difference in favour of JIT production 52,000,000 x (1 - 80%) = $400,000 $$600,000 x (1 - 0.25) = $450,000 °$400,000 (1 - 0.30) = $280,000 8 x 40,000 units = $320,000
Jdevant costs. fit of $630,000 to Colonial Hardware al should consider in deciding whether a detailed system for integrating the ss. Direct materials must arrive when 1 process functions smoothly. 1 parts and reduce manufacturing time. leliver quality direct materials on time ‘e frequent orders aducts on time. Failure to do so would ks such as minor repairs, maintenance, 1anagers is more effective in JIT plants xcess layout is streamlined. Operations As a result, such plants are easier to ats where the flow of production is not rformance measures are the dominant ares provide most timely and easy to of nonfinancial performance measures leted nancial performance measures, financial £ financial performance measures include ge inventory) speed of information flows from customers
Your preview ends here
Eager to read complete document? Join bartleby learn and gain access to the full version
- Access to all documents
- Unlimited textbook solutions
- 24/7 expert homework help
ource Planning (ERP) system has a single ers, customers, and suppliers access to «d by tight coordination across business smit information 1n response to changes in ibution plans may be revised accordingly and JIT Production System Relevant Relevant Costs under Costs under Current T Production Production System System —$200,000 war $ 300,000 r 60,000 600,000 450,000° 400,000 280,000° (320,000 $1.300000 $670,000 4 $630,000 4
20-24 Backflush costing, two trigger points, materials purchase and sale (continuation of Exercise 20-23). (LO 5) Assume the same facts as in Exer 20-23, except that Road Warrior now uses a backflush costing system witl following two trigger points: « Purchase of direct materials « Sale of finished goods The Inventory Control account will include direct materials purchased bt yet in production, materials in work-in-process, and materials in finished goods but not sold. No conversion costs are inventoried. Any under- or overallocated conversion costs are written off monthly to Cost of Goods ¢ Required 1. Prepare summary journal entries for August, including the disposi under- or overallocated conversion costs. 2. Post the entries in requirement 1 to T-accounts for Inventory Contr Conversion Costs Control, Conversion Costs Allocated, and Cost o Goods Sold.
itnot Sold. tion of 20-24 (20min) Backflush costing, two trigger point 1 (@) Purchases of direct materials (b) Incur conversion costs Inventory Contr Accounts Pay: Conversion Cos Various Acco (¢) Completion of finished goods No entry (d) Sale of finished goods (e) Underallocated or overallocated conversion costs Direct Materials [ Conversion costs [* - - Cost of Goods § Inventory Cor Conversion Ci Conversion Cos Costs of Good Conversion C Inveatory Control (2754000 _[(d)2.692.800 — Bal. 61,200 Conversion Costs Allocated ©739200 | (@739200 — Conversion Costs Control ©)723.600 | (€ 723,600
Your preview ends here
Eager to read complete document? Join bartleby learn and gain access to the full version
- Access to all documents
- Unlimited textbook solutions
- 24/7 expert homework help
ts, materials purchase and sale. ol able Control its Control unts sold atrol osts Allocated its Allocated is Sold osts Control 2,754,000 723,600 3,432,000 739,200 Cost of Goods Sold ()3.432,000 | (&) 15.600 2,754,000 723,600 2,692,800 739,200 15,600 723,600
Your preview ends here
Eager to read complete document? Join bartleby learn and gain access to the full version
- Access to all documents
- Unlimited textbook solutions
- 24/7 expert homework help
20-26 Effect of different order quantities on ordering costs and carrying EOQ. [Excel template] (LO 1) Koala Blue, a retailer of bed and bath linen, 234,000 packages of Mona Lisa designer sheets each year. Koala Blue incu ordering cost of $81 per purchase order placed with Mona Lisa Enterprise: an annual carrying cost of $11.70 per package. Liv Carrol, purchasing man at Koala Blue, seeks your help: She wants to understand how ordering anc carrying costs vary with order quantity. Scenario 1 2 3 4 Annual demand (packages) 234,000 234,000 234,000 234,000 2 Cost per purchase order § 8 s 8 s 8 § 8 S Carrying cost per package per year $ 170 §$ 10 § N0 § 10 S Quantity (packages) per purchase order 900 1,500 1,800 2,100 Number of purchase orders per year Annual relevant ordering costs Annual relevant carrying costs Annual total relevant costs of ordering and carrying inventory Required 1. Complete the preceding table for Liv Carrol. What is the EOQ? Con on your results. 2. Mona Lisa is about to introduce a web-based ordering system for it customers. Liv Carrol estimates that Koala Blue’s ordering costs wil reduced to $49 per purchase order. Calculate the new EOQ and the annual relevant costs of ordering and carrying inventory. 3. Liv Carrol estimates that Koala Blue will incur a cost of $2,000 to tre turn muiechacine accictante 4 siea tha naur Mana Tica cuctam ala T
LU PULLIEOLIG G99151EILD W UST LIS AIEYY VAL LG 2y SLCHLL 4Cp L Carrol present a case to upper management showing that Koala Blu be able to recoup its training costs within the first year of adoption.
nment ain its ©20-26 (30min) Effect of different order quan costs, EOQ. 1 1 Demand (units) (D) 234,000 Cost per purchase order (P) $ 8100 Anmual carrying cost per package (C) $ 1170 Order quantity per purchase order (units) (Q) 900 Number of purchase orders per year (D+ Q) 260.00 Annual ordering costs (D+Q) XP $21,060 Anmual carrying costs (QC + 2) $ 5265 Total relevant costs of ordering and canrying inveatory 526325 The economic order quantity is 1,800 packages. It is t equal ordering costs and total relevant ordering and cart ‘We can also confirm this from direct calculation. Using 2% 234,000 % $81 FoQ = [ZEEA0I 600 packs Q 1170 packages 1t is interesting to note that Koala Blue faces a situ carrying costs do not vary significantly when order qua packages 2. ‘When the ordering cost per purchase order is reduce 2 x 234,000 x $49 EOQ= 2 Q 1170 The EOQ drops from 1,800 packages to 1,400 pack purchase order decreases from $81 to $49. = 1,400 packages And the new relevant costs of ordering inventory = and the new relevant costs or carrying inventory = ‘The total new costs of ordering and carrying inventc 3. As summarized below, the new Mona Lisa we to 1,400 packages, will lower the carrying & spend $2,000 to train its purchasing assistants still save $2,680 i the first year alone. Total relevant costs at EOQ (from Reg
Your preview ends here
Eager to read complete document? Join bartleby learn and gain access to the full version
- Access to all documents
- Unlimited textbook solutions
- 24/7 expert homework help
Annual cost benefit over old system (§ 1e will Training costs Net benefit in first year alone
tities on ordering costs and carrying Scenario 2 3 4 5 234000 234000 234000 234,000 $8100 $8100 $800 8100 $1170 $1170 $1170 $ 1170 1,500 1,800 2,100 2,700 15600 13000 11143 86.67 $12636 $10530 $9026 $ 7020 $8775 $10530 $12285 $15795 $21411 $21060 21311 $22815 he order quantity at which carrying costs rying costs are minimized. D =234,000; P=$81 and C=$11.70 uation where total relevant ordering and ntity ranges from 1,500 packages to 2,700 :d to $49: ages when Koala Blue’s ordering cost per Dop| =B g0 -s8190 Q 1400 gxc) :(l‘mxsu 70)::3,190 2 2 ory =$8,190 x 2 =$16,380 b-based ordering system, by lowering the EOQ nd ordering costs by $4.680. Koala Blue will 5 on the new system. Overall, Koala Blue will |uirement 2) $16.380
521,060 - $16,380) $4.,680 2.000 $2.680
Your preview ends here
Eager to read complete document? Join bartleby learn and gain access to the full version
- Access to all documents
- Unlimited textbook solutions
- 24/7 expert homework help
20-40 Backflush costing and JIT production. (LO 5) The Grand Meter Corporation manufactures electrical meters. For August, there were no beginning inventories of direct materials and no beginning or ending work-in- process. Grand Meter uses a JIT production system and backflush costing with three trigger points for making entries in the accounting system: + Purchase of direct materials and incurring of conversion costs + Completion of good finished wnits of product + sale of finished goods Grand Meter's August standard cost per meter is direct materials, $25, and conversion cost, $20. Grand Meter has no direct materials variances. The following data apply to August manufacturing: Direct materials purchased ~ $650,000 Number of finished units manufactured 21,000 Conversion costs incurred ~ $440,000 Number of finished units sold 20,000 Required 1. Prepare summary journal entries for August (without disposing of under- or overallocated conversion costs). Assume no direct materials variances. 2. Post the entries in requirement 1 to T-accounts for Materials and In- Process Inventory Control, Finished Goods Control, Conversion Costs Control, Conversion Costs Allocated, and Cost of Goods Sold.
Your preview ends here
Eager to read complete document? Join bartleby learn and gain access to the full version
- Access to all documents
- Unlimited textbook solutions
- 24/7 expert homework help
20-40 (20min) Backflush costing and JIT production. 1 (a) Record purchases of direct materials (b) Record conversion costs. incurred () Record cost of good finished units completed (@) Record cost of finished goods sold #20,000 x ($20 + $15 Materials and In-Process Inventory Control Accounts Payable Control Conversion Costs Control Various Accounts (such as Wages Payable Control) Finished Goods Control® Materials and In-Process Tnventory Control* Conversion Costs Allocated” Cost of Goods Sold” i Finished Goods Control 700,000; 20,000 * $20 = $400,000; 20,000 x $15 = $300,000 19,000 x ($20 + $15) = $663.000 Coutrol Finished Goods Control Materials | 4 Conversion Costs 9 () 400000 () 700000 | (d) 665000 — Bal 35,000 (" __Conversion Costs Allocated (© 300000 Conversion Costs Control ® 425000
Your preview ends here
Eager to read complete document? Join bartleby learn and gain access to the full version
- Access to all documents
- Unlimited textbook solutions
- 24/7 expert homework help
500.000 500.000 425,000 425.000 700,000 400.000 300,000 665.000 665.000 0 Cost of Goods Sold (@ 665000
Your preview ends here
Eager to read complete document? Join bartleby learn and gain access to the full version
- Access to all documents
- Unlimited textbook solutions
- 24/7 expert homework help
pois diages ayp Burzed 101503 ap s1IEYAL P damuenb 3p30a2 pue 3utod 33p1033 213 1933% ST [[1 MOH ¢POY O SSROYTEM PINOYs Y2015 33785 YDA MO ‘23] PUEWIaP AUE 32100 03 303 39785 YBNOUS UREIUTRW PINOUS TO 1B PAPRSP SeY VOSYIE]D ‘Purwap Ut vonerzes sy 3[Ry O] %01 0} din Aq aSesaae s wozy dres fews 0007 11) s20ysjosared 0056 st puewap Appuow afesane 5,110 YSNOWIY °¢ ‘o ypea puewap (syjuom 7] + {s20ys 13p1083 O BsnOYRIEM POy Jutod JeUM 38 33P0 e 2a1a3a1 03 Yaa | Sael 11 J] ‘Hfean § Afewewixoidde 7O SISISU0D YIUO YPER PUE S30YS 00’6 ST PUEWSP ANPUOW WSSy T s3pi0 3ad saoys jo s11ed Jo Jaquin [ewndo B AUNIEIAP 01 (PO DOT A 3571 °T painbay syed 3ad g'¢s st s30ys 7o 37ed ¥ J0 3500 Bur1ze> enuue Y[ *3apo 12d 081§ 511500 BursapIo YL ‘Sa0ys Jos310d 000'F11 Aferewrxosdde st O asMOYAIEM 307 PUEWEP [enuuY *A01e] 9173 103 3SOYPIEM e 10f 930 01 S30Ys 30 Sired JO JBQUIN BN FURTIAIP 01 [3pows DO UE 535 UosyIe] “wordas si1 Uy sas0ts 0] Ajerewrxosdde S351A195 3STIOATEM UPT RN S} PUROTE S3STIOYATEM (7 O) PAIMGIISIp 35E saoys a3 ‘wonanposd iy s30ys BunfTesm Arenb ua[eoxa s[pes pue saonposd “0) 30YS U0sIE]D (Z O7) Juted JapI0az “ojs Ajajes ‘Aurepsadun ‘DOT L7-07
Your preview ends here
Eager to read complete document? Join bartleby learn and gain access to the full version
- Access to all documents
- Unlimited textbook solutions
- 24/7 expert homework help
20-27 (30mmn.) EOQ, uncertainty, safetv stock, reords 1. EOQ =((2DP)/C) = V((2 x 114,000 x 180)/3.60) = 3,376 pairs of shoes 2 Weekly demand = Monthly demand + 4 =9,500 = 4 = 2,375 pars of shoes per w Purchasing lead time = 1 week Reorder point = 2,375 pairs of shoes per week x 1 week : 3. Safety stock = 10% x 9,500 = 950 paurs of shoes Reorder point and quantity = Weekly demand + Safety si = 2,375 + 950 = 3,325 pairs of shoes 4. Safety stock cost = 950 shoes x $3.60 = $3,420
Your preview ends here
Eager to read complete document? Join bartleby learn and gain access to the full version
- Access to all documents
- Unlimited textbook solutions
- 24/7 expert homework help
o point. reek =2,375 pairs of shoes tock
Your preview ends here
Eager to read complete document? Join bartleby learn and gain access to the full version
- Access to all documents
- Unlimited textbook solutions
- 24/7 expert homework help
Related Documents
Related Questions
Sk8 Company produces skateboards and purchases 20,000 units of a wheel bearing each year at a cost of $1 per unit. Sk8 requires a 15% annual rate of return on investment. In addition, the relevant carrying cost (for insurance, materials handling, breakage, etc.) is $0.17 per unit per year. The relevant ordering cost per purchase order is $38.40.
Q. Calculate Sk8’s EOQ for the wheel bearing.
arrow_forward
Sk8 Company produces skateboards and purchases 20,000 units of a wheel bearing each year at a cost of $1 per unit. Sk8 requires a 15% annual rate of return on investment. In addition, the relevant carrying cost (for insurance, materials handling, breakage, etc.) is $0.17 per unit per year. The relevant ordering cost per purchase order is $38.40.
Q. Assume that demand is uniform throughout the year and known with certainty so there is no need for safety stocks. The purchase-order lead time is half a month. Calculate Sk8’s reorder point for the wheel bearing.
arrow_forward
15. ERD Company manufactures and sells
two types of beach towels, standard and
deluxe. ERD expects the following operating
results next year for each type of towel:
Standard
Deluxe
Sales
P450,000
P50,000
Variable expenses (total)
P360,000
P20,000
If ERD expects to incur P57,600 in fixed expenses next year, its break-even point must be:
arrow_forward
A plastic manufacturing company that makes four major products seeks to expand its operationsin the coming year. At the beginning of the financial year, the company must decide on which offour new machines A, B, or C to purchase to be able to meet total annual demand. Each machineoperates 14 hours a day, 360 days a year. Machine A costs GH¢43,000, machine B costsGH¢37,500 and machine C costs GH¢75,000. The following product forecasts and processing times have been projected: Demand, units/year Processing times per Unit (Minutes) Product Machine A Machine B Machine CPenholders 16,000 5 3 6Bowls 14,000 4 3 5Cups 6,000 6 5 7Carrier Bags 24,000 3…
arrow_forward
Required:
If ERD expects to incur P57,600 in fixed expenses next year, its break-even point must be?
arrow_forward
35. A large producer of household products purchases a glyceride used in one of its
deodorant soaps from outside of the company. It uses the glyceride at a fairly steady
rate of 40 pounds per month, and the company uses a 23 percent annual interest rate to
compute holding costs. The chemical can be purchased from two suppliers, A and B.
A offers the following all-units discount schedule:
Order Size
Price per Pound
$1.30
0sQ< 500
500 < Q< 1,000
1,000 < Q
1.20
1.10
whereas B offers the following incremental discount schedule: $1.25 per pound for all
orders less than or equal to 700 pounds, and $1.05 per pound for all incremental
amounts over 700 pounds. Assume that the cost of order processing for each case is
$150. Which supplier should be used?
arrow_forward
Porter's Paints produces high-end industrial paint primer and sells the primer for $45
per gallon. The company's variable cost is $21.60 per gallon of primer. Annual fixed
costs related to the primer are $197,145. Porter expects to sell 18,000 gallons of
primer in 2021. What is 2021 expected profit?
$618,345
$224,055
$421,200
$810,000
arrow_forward
A plastic manufacturing company that makes four major products seeks to expand its operations in the coming year. At the beginning of the financial year, the company must decide on which of four new machines A, B, or C to purchase to be able to meet total annual demand. Each machine operates 14 hours a day, 360 days a year. Machine A costs GH¢43,000, machine B costs GH¢37,500 and machine C costs GH¢75,000. The following product forecasts and processing times have been projected: Demand, units/year Processing times per Unit (Minutes) Product Machine A Machine B Machine CPenholders 16,000 5 3 6Bowls 14,000 4 3 5Cups 6,000 6 5 7Carrier Bags 24,000 3…
arrow_forward
16.
Race Corporation manufactures batons. Race can manufacture 300,000 batons a year at a variable cost of $750,000 and a fixed cost of $450,000. Based on Race's predictions for next year, 240,000 batons will be sold at the regular price of $5.00 each. In addition, a special order was placed for 60,000 batons to be sold at a 40% discount off the regular price. Total fixed costs would be unaffected by this order. By what amount would the company's operating income be increased or decreased as a result of the special order?
Select one:
a. $180,000 increase.
b. $60,000 decrease.
c. $36,000 increase.
d. $30,000 increase.
arrow_forward
(D) Delta Company produces mobiles and purchases batteries at $30 per unit. The management proposes producing the batteries instead of purchasing them. The annual quantity of batteries is 50,000 units. The costs of producing the batteries are: $20 variable cost per unit, The company will pay an annual rent of $250,000 to rent a new machine to produce the batteries. The general (old) fixed cost for the company is $500,000. Do you advise the company to produce the batteries or to purchase it? Justify? (E) Nile Co. can produce 2 products, � & B; the following data is estimated to help in preparing the production plan for the coming period to maximize the profit: \table[[,A,B],[Price,$30,$50
arrow_forward
ACME Company purchases for resale 1,000 widgets for $64 each. At year-
end, the replacement cost is $63 per widget, the estimated selling price is
$68 per widget, the disposal cost is $7 per widget, and the estimated
markup is $10 per widget.[General Account]
If ACME uses LCM costing by item, at what amount will the widgets be
reported on the balance sheet?
a. $63,000
b. $51,000
c. $64,000
d. $62,500
e. $61,000
arrow_forward
Sheffield Corp. sells indoor high-resolution security cameras with a unit selling price of $80, a unit contribution margin of $64, and a
contribution margin ratio of 80%. The company projects total fixed costs for the next year to be $3336000. How many units must the
company sell to break-even?
O 41700
O 4170
O 64000
O 52125
arrow_forward
1. Party Co. produces 1,000 parts per year, which are used in the assembly of one of its products. The unit product cost of these parts are: Variable manufacturing cost, P12.00; fixed manufacturing cost, P9.00. The part can be purchased from an outside supplier at P20.00. If the part is purchased from the outside supplier, two thirds of the fixed manufacturing costs can be eliminated. What would be the annual impact on the company’s net operating income as a result of buying the part from the outside supplier?
2.Division A produces a part that it sells to outside customers. Data concerning this part follows: Selling price to outside customers, P60; Variable cost per unit, P40; Total fixed costs, P100,000; Capacity in units, 20,000 units. Division B of the same company purchases 5,000 units of similar part from an outside supplier at a price of P58 per unit. If Division B wants to purchase 5,000 units from Division A instead, and Division A has no idle capacity, what should be the…
arrow_forward
A machine manufacturer sells each machine for $7,300. The fixed costs are $279,550 per annum, variable costs are $1,500 per machine, and the production capacity is 58 machines in a year.
What is break-even as a percent of capacity per annum?
arrow_forward
A manufacturer of ovens sells them for $1,370.00 each. The variable costs are $1,020.00 per unit. The manufacturer's factory has annual fixed costs of $2,460,000.00.
Given the expected sales volume of 3,700 units for this year, what will be this year's net income?
Round to two decimal places
arrow_forward
SEE MORE QUESTIONS
Recommended textbooks for you
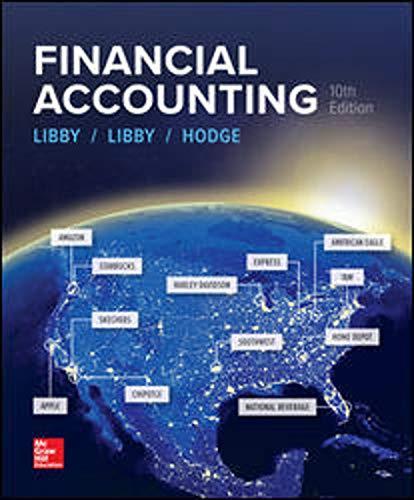
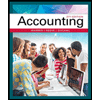
Accounting
Accounting
ISBN:9781337272094
Author:WARREN, Carl S., Reeve, James M., Duchac, Jonathan E.
Publisher:Cengage Learning,
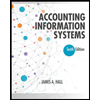
Accounting Information Systems
Accounting
ISBN:9781337619202
Author:Hall, James A.
Publisher:Cengage Learning,
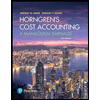
Horngren's Cost Accounting: A Managerial Emphasis...
Accounting
ISBN:9780134475585
Author:Srikant M. Datar, Madhav V. Rajan
Publisher:PEARSON
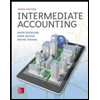
Intermediate Accounting
Accounting
ISBN:9781259722660
Author:J. David Spiceland, Mark W. Nelson, Wayne M Thomas
Publisher:McGraw-Hill Education
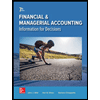
Financial and Managerial Accounting
Accounting
ISBN:9781259726705
Author:John J Wild, Ken W. Shaw, Barbara Chiappetta Fundamental Accounting Principles
Publisher:McGraw-Hill Education
Related Questions
- Sk8 Company produces skateboards and purchases 20,000 units of a wheel bearing each year at a cost of $1 per unit. Sk8 requires a 15% annual rate of return on investment. In addition, the relevant carrying cost (for insurance, materials handling, breakage, etc.) is $0.17 per unit per year. The relevant ordering cost per purchase order is $38.40. Q. Calculate Sk8’s EOQ for the wheel bearing.arrow_forwardSk8 Company produces skateboards and purchases 20,000 units of a wheel bearing each year at a cost of $1 per unit. Sk8 requires a 15% annual rate of return on investment. In addition, the relevant carrying cost (for insurance, materials handling, breakage, etc.) is $0.17 per unit per year. The relevant ordering cost per purchase order is $38.40. Q. Assume that demand is uniform throughout the year and known with certainty so there is no need for safety stocks. The purchase-order lead time is half a month. Calculate Sk8’s reorder point for the wheel bearing.arrow_forward15. ERD Company manufactures and sells two types of beach towels, standard and deluxe. ERD expects the following operating results next year for each type of towel: Standard Deluxe Sales P450,000 P50,000 Variable expenses (total) P360,000 P20,000 If ERD expects to incur P57,600 in fixed expenses next year, its break-even point must be:arrow_forward
- A plastic manufacturing company that makes four major products seeks to expand its operationsin the coming year. At the beginning of the financial year, the company must decide on which offour new machines A, B, or C to purchase to be able to meet total annual demand. Each machineoperates 14 hours a day, 360 days a year. Machine A costs GH¢43,000, machine B costsGH¢37,500 and machine C costs GH¢75,000. The following product forecasts and processing times have been projected: Demand, units/year Processing times per Unit (Minutes) Product Machine A Machine B Machine CPenholders 16,000 5 3 6Bowls 14,000 4 3 5Cups 6,000 6 5 7Carrier Bags 24,000 3…arrow_forwardRequired: If ERD expects to incur P57,600 in fixed expenses next year, its break-even point must be?arrow_forward35. A large producer of household products purchases a glyceride used in one of its deodorant soaps from outside of the company. It uses the glyceride at a fairly steady rate of 40 pounds per month, and the company uses a 23 percent annual interest rate to compute holding costs. The chemical can be purchased from two suppliers, A and B. A offers the following all-units discount schedule: Order Size Price per Pound $1.30 0sQ< 500 500 < Q< 1,000 1,000 < Q 1.20 1.10 whereas B offers the following incremental discount schedule: $1.25 per pound for all orders less than or equal to 700 pounds, and $1.05 per pound for all incremental amounts over 700 pounds. Assume that the cost of order processing for each case is $150. Which supplier should be used?arrow_forward
- Porter's Paints produces high-end industrial paint primer and sells the primer for $45 per gallon. The company's variable cost is $21.60 per gallon of primer. Annual fixed costs related to the primer are $197,145. Porter expects to sell 18,000 gallons of primer in 2021. What is 2021 expected profit? $618,345 $224,055 $421,200 $810,000arrow_forwardA plastic manufacturing company that makes four major products seeks to expand its operations in the coming year. At the beginning of the financial year, the company must decide on which of four new machines A, B, or C to purchase to be able to meet total annual demand. Each machine operates 14 hours a day, 360 days a year. Machine A costs GH¢43,000, machine B costs GH¢37,500 and machine C costs GH¢75,000. The following product forecasts and processing times have been projected: Demand, units/year Processing times per Unit (Minutes) Product Machine A Machine B Machine CPenholders 16,000 5 3 6Bowls 14,000 4 3 5Cups 6,000 6 5 7Carrier Bags 24,000 3…arrow_forward16. Race Corporation manufactures batons. Race can manufacture 300,000 batons a year at a variable cost of $750,000 and a fixed cost of $450,000. Based on Race's predictions for next year, 240,000 batons will be sold at the regular price of $5.00 each. In addition, a special order was placed for 60,000 batons to be sold at a 40% discount off the regular price. Total fixed costs would be unaffected by this order. By what amount would the company's operating income be increased or decreased as a result of the special order? Select one: a. $180,000 increase. b. $60,000 decrease. c. $36,000 increase. d. $30,000 increase.arrow_forward
- (D) Delta Company produces mobiles and purchases batteries at $30 per unit. The management proposes producing the batteries instead of purchasing them. The annual quantity of batteries is 50,000 units. The costs of producing the batteries are: $20 variable cost per unit, The company will pay an annual rent of $250,000 to rent a new machine to produce the batteries. The general (old) fixed cost for the company is $500,000. Do you advise the company to produce the batteries or to purchase it? Justify? (E) Nile Co. can produce 2 products, � & B; the following data is estimated to help in preparing the production plan for the coming period to maximize the profit: \table[[,A,B],[Price,$30,$50arrow_forwardACME Company purchases for resale 1,000 widgets for $64 each. At year- end, the replacement cost is $63 per widget, the estimated selling price is $68 per widget, the disposal cost is $7 per widget, and the estimated markup is $10 per widget.[General Account] If ACME uses LCM costing by item, at what amount will the widgets be reported on the balance sheet? a. $63,000 b. $51,000 c. $64,000 d. $62,500 e. $61,000arrow_forwardSheffield Corp. sells indoor high-resolution security cameras with a unit selling price of $80, a unit contribution margin of $64, and a contribution margin ratio of 80%. The company projects total fixed costs for the next year to be $3336000. How many units must the company sell to break-even? O 41700 O 4170 O 64000 O 52125arrow_forward
arrow_back_ios
SEE MORE QUESTIONS
arrow_forward_ios
Recommended textbooks for you
- AccountingAccountingISBN:9781337272094Author:WARREN, Carl S., Reeve, James M., Duchac, Jonathan E.Publisher:Cengage Learning,Accounting Information SystemsAccountingISBN:9781337619202Author:Hall, James A.Publisher:Cengage Learning,
- Horngren's Cost Accounting: A Managerial Emphasis...AccountingISBN:9780134475585Author:Srikant M. Datar, Madhav V. RajanPublisher:PEARSONIntermediate AccountingAccountingISBN:9781259722660Author:J. David Spiceland, Mark W. Nelson, Wayne M ThomasPublisher:McGraw-Hill EducationFinancial and Managerial AccountingAccountingISBN:9781259726705Author:John J Wild, Ken W. Shaw, Barbara Chiappetta Fundamental Accounting PrinciplesPublisher:McGraw-Hill Education
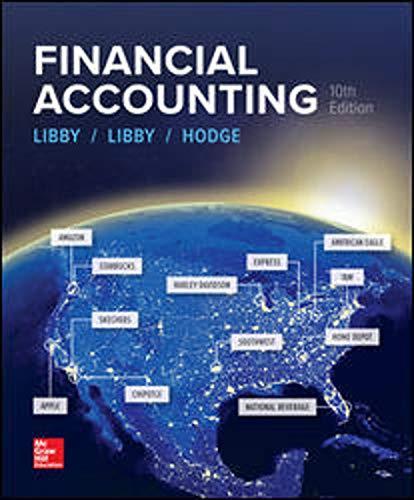
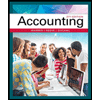
Accounting
Accounting
ISBN:9781337272094
Author:WARREN, Carl S., Reeve, James M., Duchac, Jonathan E.
Publisher:Cengage Learning,
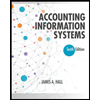
Accounting Information Systems
Accounting
ISBN:9781337619202
Author:Hall, James A.
Publisher:Cengage Learning,
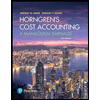
Horngren's Cost Accounting: A Managerial Emphasis...
Accounting
ISBN:9780134475585
Author:Srikant M. Datar, Madhav V. Rajan
Publisher:PEARSON
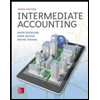
Intermediate Accounting
Accounting
ISBN:9781259722660
Author:J. David Spiceland, Mark W. Nelson, Wayne M Thomas
Publisher:McGraw-Hill Education
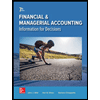
Financial and Managerial Accounting
Accounting
ISBN:9781259726705
Author:John J Wild, Ken W. Shaw, Barbara Chiappetta Fundamental Accounting Principles
Publisher:McGraw-Hill Education