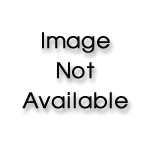
MyLab Operations Management with Pearson eText -- Access Card -- for Operations Management: Processes and Supply Chains
12th Edition
ISBN: 9780134742366
Author: Lee J. Krajewski, Manoj K. Malhotra, Larry P. Ritzman
Publisher: PEARSON
expand_more
expand_more
format_list_bulleted
Concept explainers
Question
Chapter C, Problem 3P
Summary Introduction
Interpretation: The economic production lot size (ELS) should be calculated.
Concept Introduction: Economic production of a lot is the quantity produced at lowest stock value. It is the minimum of total cost that requires for output.
Expert Solution & Answer

Want to see the full answer?
Check out a sample textbook solution
Students have asked these similar questions
A practical application in real life to the Critical Path Method is the construction of a bridge
with references, give a detailed essay on the stages involved in constructing a bridge
Please assist in writing a complete reasearch project of the following title:
Title of research: Study on the impact of Technology in the Work Place.
Intuition is both an emotional experience and a nonconscious analytic process. One problem, however, is that not all emotions signaling that there is a problem or opportunity represent intuition. Please in your Personal opinion how we would know if our “gut feelings” are intuition or not, and if not intuition, suggest what might be causing them.
Chapter C Solutions
MyLab Operations Management with Pearson eText -- Access Card -- for Operations Management: Processes and Supply Chains
Knowledge Booster
Learn more about
Need a deep-dive on the concept behind this application? Look no further. Learn more about this topic, operations-management and related others by exploring similar questions and additional content below.Similar questions
- A coworker suggests that the company where you both work would be much more effective if there were no organizational politics. Please in your personal and detailed opinion, What would you say to this person in reply?arrow_forwardWhat is a bottleneck? Would you try to reduce a bottleneck? Why or why not? Please provide a referencearrow_forwardYour firm has been the auditor of Caribild Products, a listed company, for a number of years. The engagement partner has asked you to describe the matters you would consider when planning the audit for the year ended 31January 2022. During recent visit to the company you obtained the following information: (a) The management accounts for the 10 months to 30 November 2021 show a revenue of $260 million and profit before tax of $8 million. Assume sales and profits accrue evenly throughout the year. In the year ended 31 January 2021 Caribild Products had sales of $220 million and profit before tax of $16 million. (b) The company installed a new computerised inventory control system which has operated from 1 June 2021. As the inventory control system records inventory movements and current inventory quantities, the company is proposing: (i) To use the inventory quantities on the computer to value the inventory at the year-end (ii) Not to carry out an inventory count at the year-end (c)…arrow_forward
- Develop and implement a complex and scientific project for an organisation of your choice. please include report include the following: Introduction Background research to the project The 5 basic phases in the project management process Project Initiation Project Planning Project Execution Project Monitoring and Controlling Project Closing Conclusionarrow_forwardNot use ai pleasearrow_forwardSam's Pet Hotel operates 51 weeks per year, 6 days per week, and uses a continuous review inventory system. It purchases kitty litter for $11.00 per bag. The following information is available about these bags: > Demand 95 bags/week > Order cost $52.00/order > Annual holding cost = 25 percent of cost > Desired cycle-service level = 80 percent >Lead time 4 weeks (24 working days) > Standard deviation of weekly demand = 15 bags > Current on-hand inventory is 320 bags, with no open orders or backorders. a. Suppose that the weekly demand forecast of 95 bags is incorrect and actual demand averages only 75 bags per week. How much higher will total costs be, owing to the distorted EOQ caused by this forecast error? The costs will be $ higher owing to the error in EOQ. (Enter your response rounded to two decimal places.)arrow_forward
- Sam's Pet Hotel operates 50 weeks per year, 6 days per week, and uses a continuous review inventory system. It purchases kitty litter for $10.50 per bag. The following information is available about these bags: > Demand = 95 bags/week > Order cost = $55.00/order > Annual holding cost = 35 percent of cost > Desired cycle-service level = 80 percent > Lead time = 4 weeks (24 working days) > Standard deviation of weekly demand = 15 bags > Current on-hand inventory is 320 bags, with no open orders or backorders. a. Suppose that the weekly demand forecast of 95 bags is incorrect and actual demand averages only 75 bags per week. How much higher will total costs be, owing to the distorted EOQ caused by this forecast error? The costs will be $ 10.64 higher owing to the error in EOQ. (Enter your response rounded to two decimal places.) b. Suppose that actual demand is 75 bags but that ordering costs are cut to only $13.00 by using the internet to automate order placing. However, the buyer does…arrow_forwardBUS-660 Topic 4: Intege... W Midterm Exam - BUS-66... webassign.net b Answered: The binding c... × W Topic 4 Assignment - BU... how to get more chegg... b My Questions | bartleby + macbook screenshot - G... C Consider the following m... As discussed in Section 8.3, the Markowitz model uses the variance of the portfolio as the measure of risk. However, variance includes deviations both below and above the mean return. Semivariance includes only deviations below the mean and is considered by many to be a better measure of risk. (a) Develop a model that minimizes semivariance for the Hauck Financial data given in the file HauckData with a required return of 10%. Assume that the five planning scenarios in the Hauck Financial Services model are equally likely to occur. Hint: Modify model (8.10)-(8.19). Define a variable d for each 5 - scenario and let d≥ Ŕ – R¸ with d¸ ≥ 0. Then make the objective function: Min 1 5 Σας Let Min s.t. 15 FS = proportion of portfolio invested in the foreign…arrow_forwardOn a daily basis, the van is dispatched from Maplewood Hospital to pickup blood and platelet donations made at its local donation centers. The distances in miles between all locations may be found in the table below. Click the icon to view mileage data for Vampire Van. a. The van travels from the Hospital (A) to (B) to (C) to (D) to (E) and then returns to the Hospital (A). What is the total number of miles that the van must travel using this route? Route ABCDEA requires a total distance of miles. (Enter your response rounded to one decimal place.) More Info Maplewood City Center Westbrook Hospital (A) Donation Site (B) Donation Site (C) Municipal Park Donation Site (D) Valley Hills Donation Site (E) Maplewood 3.1 5.3 3.2 4.4 Hospital (A) City Center 3.1 6.7 2.2 4.3 Donation Site (B) Westbrook 5.3 Donation Site (C) 19 6.7 | 6.2 2.5 Municipal Park 3.2 2.2 6.2 | 4.6 Donation Site (D) Valley Hills 4.4 4.3 2.5 4.6 Donation Site (E) - ☑arrow_forward
- The Harvey Motorcycle Company produces three models: the Tiger, a sure-footed dirt bike; the LX2000, a nimble cafe racer; and the Golden, a large interstate tourer. The month's master production schedule calls for the production of 32 Goldens, 31 LX2000s, and 38 Tigers per 10-hour shift. What average cycle time is required for the assembly line to achieve the production quota in 10 hours? 0.099 hours per motorcycle. (Enter your response rounded to three decimal places.) If mixed-model scheduling is used, how many of each model will be produced before the production cycle is repeated? The greatest common divisor of the production requirements is Therefore, the Harvey Motorcycle Company will produce Goldens, LX2000s, and Tigers. (Enter your responses as integers.)arrow_forwardThe Harvey Motorcycle Company produces three models: the Tiger, a sure-footed dirt bike; the LX2000, a nimble cafe racer; and the Golden, a large interstate tourer. The month's master production schedule calls for the production of 32 Goldens, 31 LX2000s, and 38 Tigers per 10-hour shift. What average cycle time is required for the assembly line to achieve the production quota in 10 hours? hours per motorcycle. (Enter your response rounded to three decimal places.)arrow_forwardThe binding constraints for this problem are the second and third constraints are binding. Min x1 + 2x2 s.t. x1 + x2 ≤ 300 2x1 + x2 ≥ 400 2x1 + 5x2 ≥750 X1, X220 (a) Keeping the second objective function coefficient fixed at 2, over what range can the first objective function coefficient vary before there is a change in the optimal solution point? The first objective coefficient can from a low of to a high of (b) Keeping the first objective function coefficient fixed at 1, over what range can the second objective function coefficient vary before there is a change in the optimal solution point? The second objective coefficient can from a low of to a high of (c) If the objective function becomes Min 1.5x₁ + 2x2, what will be the optimal values of x1 and x2? x1 = X2 = What is the value of the objective function at the minimum? (d) If the objective function becomes Min 7x₁ + 6x2, what constraints will be binding? (Select all that apply.) First Constraint Second Constraint Third Constraint…arrow_forward
arrow_back_ios
SEE MORE QUESTIONS
arrow_forward_ios
Recommended textbooks for you
- Purchasing and Supply Chain ManagementOperations ManagementISBN:9781285869681Author:Robert M. Monczka, Robert B. Handfield, Larry C. Giunipero, James L. PattersonPublisher:Cengage LearningMarketingMarketingISBN:9780357033791Author:Pride, William MPublisher:South Western Educational Publishing
- Foundations of Business (MindTap Course List)MarketingISBN:9781337386920Author:William M. Pride, Robert J. Hughes, Jack R. KapoorPublisher:Cengage LearningFoundations of Business - Standalone book (MindTa...MarketingISBN:9781285193946Author:William M. Pride, Robert J. Hughes, Jack R. KapoorPublisher:Cengage LearningPractical Management ScienceOperations ManagementISBN:9781337406659Author:WINSTON, Wayne L.Publisher:Cengage,
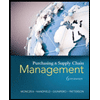
Purchasing and Supply Chain Management
Operations Management
ISBN:9781285869681
Author:Robert M. Monczka, Robert B. Handfield, Larry C. Giunipero, James L. Patterson
Publisher:Cengage Learning
Marketing
Marketing
ISBN:9780357033791
Author:Pride, William M
Publisher:South Western Educational Publishing
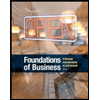
Foundations of Business (MindTap Course List)
Marketing
ISBN:9781337386920
Author:William M. Pride, Robert J. Hughes, Jack R. Kapoor
Publisher:Cengage Learning
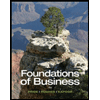
Foundations of Business - Standalone book (MindTa...
Marketing
ISBN:9781285193946
Author:William M. Pride, Robert J. Hughes, Jack R. Kapoor
Publisher:Cengage Learning
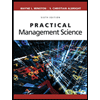
Practical Management Science
Operations Management
ISBN:9781337406659
Author:WINSTON, Wayne L.
Publisher:Cengage,
Inventory Management | Concepts, Examples and Solved Problems; Author: Dr. Bharatendra Rai;https://www.youtube.com/watch?v=2n9NLZTIlz8;License: Standard YouTube License, CC-BY