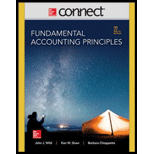
Concept explainers
Concept Introduction:
Manufacturing overhead allocation:
Manufacturing overhead cost is the pool of all indirect costs incurred for the production. These are the costs which are not directly traceable to the product.
Requirement-1:
To determine: Activity overhead rates

Answer to Problem 1APSA
Solution: Activity overhead rates are as follows:
Activity | Activity Rate | |
Grinding | $ 24.62 | Per Machine Hour |
Polishing | $ 10.38 | Per Machine Hour |
Product Modification | $ 40.00 | Per Engineering Hour |
Providing Power | $ 15.00 | Per Direct Labor Hour |
System Calibration | $ 1,250.00 | Per Batch |
Explanation of Solution
Explanation: Activity overhead rates are calculated as follows:
Activity | Overhead Cost | Allocation base | Activity Rate | ||
A | B | = A/B | |||
Grinding | $ 320,000 | 13000 | Machine Hours | $ 24.62 | Per Machine Hour |
Polishing | $ 135,000 | 13000 | Machine Hours | $ 10.38 | Per Machine Hour |
Product Modification | $ 600,000 | 15000 | Engineering Hours | $ 40.00 | Per Engineering Hour |
Providing Power | $ 255,000 | 17000 | Direct Labor Hours | $ 15.00 | Per Direct Labor Hour |
System Calibration | $ 500,000 | 400 | Batches | $ 1,250.00 | Per Batch |
Conclusion: Hence, costs are allocated to the products using the overhead allocation rate.
Requirement-2:
To determine: The overhead Costs assigned to jobs

Answer to Problem 1APSA
Solution: The overhead Costs assigned to jobs are as follows:
• Job 3175 = $74,650
• Job 4286 = $383,425
Explanation of Solution
Explanation: The overhead Costs assigned to jobs are calculated as follows:
Job 3175: | ||||
Activity | Allocation base | Activity Rate | Allocated Overhead Cost | |
A | B | =A*B | ||
Grinding | 550 | Machine Hours | $ 24.62 | $ 13,538.46 |
Polishing | 550 | Machine Hours | $ 10.38 | $ 5,711.54 |
Product Modification | 26 | Engineering Hours | $ 400.00 | $ 10,400.00 |
Providing Power | 500 | Direct Labor Hours | $ 15.00 | $ 7,500.00 |
System Calibration | 30 | Batches | $ 1,250.00 | $ 37,500.00 |
Total Overhead Cost allocated to Job 3175 (C) | $ 74,650.00 |
Job 4286: | ||||
Activity | Allocation base | Activity Rate | Allocated Overhead Cost | |
A | B | =A*B | ||
Grinding | 5500 | Machine Hours | $ 24.62 | $ 135,384.62 |
Polishing | 5500 | Machine Hours | $ 10.38 | $ 57,115.38 |
Product Modification | 32 | Engineering Hours | $ 400.00 | $ 12,800.00 |
Providing Power | 4375 | Direct Labor Hours | $ 15.00 | $ 65,625.00 |
System Calibration | 90 | Batches | $ 1,250.00 | $ 112,500.00 |
Total Overhead Cost allocated to Job 4286 = | $ 383,425.00 |
Conclusion: Hence, costs are allocated to the products using the overhead allocation rate.
Requirement-3:
To determine: The overhead Cost per unit for each job

Answer to Problem 1APSA
Solution: The overhead Cost per unit for each job is as follows:
• Job 3175 = $373.25 Per unit
• Job 4286 = $1543.27 Per unit
Explanation of Solution
Explanation: The overhead Cost per unit for each job is calculated as follows:
Job 3175: | ||||
Activity | Allocation base | Activity Rate | Allocated Overhead Cost | |
A | B | =A*B | ||
Grinding | 550 | Machine Hours | $ 24.62 | $ 13,538.46 |
Polishing | 550 | Machine Hours | $ 10.38 | $ 5,711.54 |
Product Modification | 26 | Engineering Hours | $ 400.00 | $ 10,400.00 |
Providing Power | 500 | Direct Labor Hours | $ 15.00 | $ 7,500.00 |
System Calibration | 30 | Batches | $ 1,250.00 | $ 37,500.00 |
Total Overhead Cost allocated to Job 3175 (C) | $ 74,650.00 | |||
Number of Units (D) | 200 | |||
Overhead Cost per unit = (C/D) | $ 373.25 |
Job 4286: | ||||
Activity | Allocation base | Activity Rate | Allocated Overhead Cost | |
A | B | =A*B | ||
Grinding | 5500 | Machine Hours | $ 24.62 | $ 135,384.62 |
Polishing | 5500 | Machine Hours | $ 10.38 | $ 57,115.38 |
Product Modification | 32 | Engineering Hours | $ 400.00 | $ 12,800.00 |
Providing Power | 4375 | Direct Labor Hours | $ 15.00 | $ 65,625.00 |
System Calibration | 90 | Batches | $ 1,250.00 | $ 112,500.00 |
Total Overhead Cost allocated to Job 4286 = | $ 383,425.00 | |||
Number of Units (D) | 2,500 | |||
Overhead Cost per unit = (C/D) | $ 153.37 |
Conclusion: Hence, costs are allocated to the products using the overhead allocation rate.
Requirement-4:
To determine: The overhead Cost allocated per unit for each job using the plant wide overhead rate

Answer to Problem 1APSA
Solution: The overhead Cost allocated per unit for each job using the plant wide overhead rate is as follows:
• Job 3175 = $382.88 Per unit
• Job 4286 = $306.31 Per unit
Explanation of Solution
Explanation: The overhead Cost allocated per unit for each job using the plant wide overhead rate is as follows:
Total Estimated Overhead Cost (A) | $ 1,810,000 |
Total Machine hours (B) | 13,000 |
Overhead allocation rate (C) = A/B = | $ 139.23 |
For Job 3175: | |
Overhead allocated (D) = (550 MH *C) | $ 76,576.92 |
Number of Units (E) | 200 |
Overhead Cost per unit = (D/E) | $ 382.88 |
For Job 4286: | |
Overhead allocated (D) = (5500 MH *C) | $ 765,769.23 |
Number of Units (E) | 2500 |
Overhead Cost per unit = (D/E) | $ 306.31 |
Conclusion: Hence, all overhead costs are allocated using a single plant wide overhead rate.
Requirement-5:
To Compare: The overhead Cost allocated per unit under both the methods

Answer to Problem 1APSA
Solution: The overhead Cost allocated per unit under both the methods is compared as follows:
Overhead Cost per unit: | ABC Method | Plant wide Method |
Job 3175 | $ 373.25 | $ 382.88 |
Job 4286 | $ 153.37 | $ 306.31 |
Explanation of Solution
Explanation: The overhead Cost allocated per unit under both the methods is compared as follows:
Overhead Cost per unit: | ABC Method | Plant wide Method |
Job 3175 | $ 373.25 | $ 382.88 |
Job 4286 | $ 153.37 | $ 306.31 |
Activity bases costing method is better method to allocated the overhead costs.
Conclusion: Hence, it can be concluded that the Activity bases costing method is better method to allocated the overhead costs.
Want to see more full solutions like this?
- What is the impact of recording depreciation expense on the financial statements?A. Assets increase; Net income increasesB. Assets decrease; Net income decreasesC. Liabilities increase; Net income increasesD. Assets increase; Liabilities increasearrow_forwardWhich financial statement shows a company’s financial position at a specific point in time?A. Income StatementB. Balance SheetC. Statement of Cash FlowsD. Statement of Retained Earningsarrow_forwardWhich account is closed at the end of the accounting period? A. Accumulated Depreciation B. Salaries Payable C. Service Revenue D. Retained Earnings need carrow_forward
- Which account is closed at the end of the accounting period?A. Accumulated DepreciationB. Salaries PayableC. Service RevenueD. Retained Earningsarrow_forward12. Which account is closed at the end of the accounting period?A. Accumulated DepreciationB. Salaries PayableC. Service RevenueD. Retained Earningsneed helparrow_forward12. Which account is closed at the end of the accounting period?A. Accumulated DepreciationB. Salaries PayableC. Service RevenueD. Retained Earningsarrow_forward
- Which account is closed at the end of the accounting period?A. Accumulated DepreciationB. Salaries PayableC. Service RevenueD. Retained Earningsneed helparrow_forwardWhich account is closed at the end of the accounting period?A. Accumulated DepreciationB. Salaries PayableC. Service RevenueD. Retained Earningsarrow_forwardThe principle that requires companies to record expenses in the same period as the revenues they help generate is the:A. Revenue Recognition PrincipleB. Consistency PrincipleC. Matching PrincipleD. Cost Principleneed hekparrow_forward
- No AI The principle that requires companies to record expenses in the same period as the revenues they help generate is the:A. Revenue Recognition PrincipleB. Consistency PrincipleC. Matching PrincipleD. Cost Principlearrow_forwardThe principle that requires companies to record expenses in the same period as the revenues they help generate is the:A. Revenue Recognition PrincipleB. Consistency PrincipleC. Matching PrincipleD. Cost Principlearrow_forwardNo ai 14. A company receives a bill for electricity to be paid next month. What is the journal entry today?A. Debit Utilities Expense; Credit Accounts PayableB. Debit Cash; Credit Utilities ExpenseC. Debit Accounts Payable; Credit Utilities ExpenseD. No entry until payment is madearrow_forward
- AccountingAccountingISBN:9781337272094Author:WARREN, Carl S., Reeve, James M., Duchac, Jonathan E.Publisher:Cengage Learning,Accounting Information SystemsAccountingISBN:9781337619202Author:Hall, James A.Publisher:Cengage Learning,
- Horngren's Cost Accounting: A Managerial Emphasis...AccountingISBN:9780134475585Author:Srikant M. Datar, Madhav V. RajanPublisher:PEARSONIntermediate AccountingAccountingISBN:9781259722660Author:J. David Spiceland, Mark W. Nelson, Wayne M ThomasPublisher:McGraw-Hill EducationFinancial and Managerial AccountingAccountingISBN:9781259726705Author:John J Wild, Ken W. Shaw, Barbara Chiappetta Fundamental Accounting PrinciplesPublisher:McGraw-Hill Education
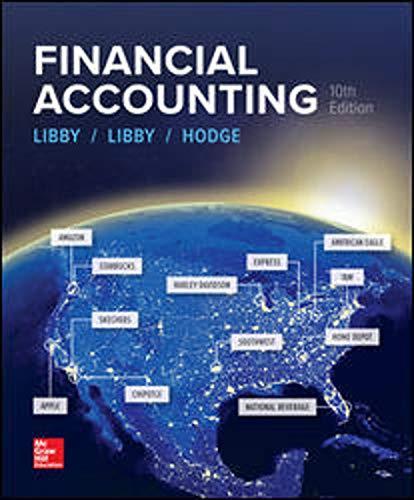
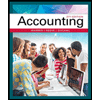
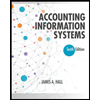
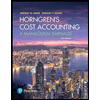
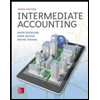
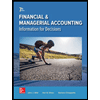