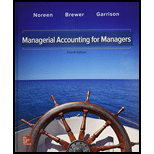
GEN COMBO MANAGERIAL ACCOUNTING FOR MANAGERS; CONNECT 1S ACCESS CARD
4th Edition
ISBN: 9781259911682
Author: Eric Noreen
Publisher: McGraw-Hill Education
expand_more
expand_more
format_list_bulleted
Concept explainers
Question
Chapter 6A, Problem 6A.1E
To determine
Concept introduction:
Activity-based costing is a method of allocation of
To indicate: The classification of each activity.
Expert Solution & Answer

Explanation of Solution
The classification of each activity is as follows:
Activity # | Type | |
a | Batch Level | Raw materials are used for a batch of the product; hence receiving the raw materials is a batch level activity. |
b | Product level | Management of parts inventory is a product-level activity. |
c | Unit level | Milling work on the product is done at the unit level. Hence, it is a unit-level activity. |
d | Organization level | Hiring new employees is an organization level activity. |
e | Organization level | Designing a new product is an organization level activity. |
f | Organization level | Performing preventive maintenance of equipment is an organization level activity. |
g | Organization level | The use of general factory building is an organization level activity. |
h | Batch Level | Issuing purchase orders for a job is a batch level activity. |
Want to see more full solutions like this?
Subscribe now to access step-by-step solutions to millions of textbook problems written by subject matter experts!
Students have asked these similar questions
Work in process inventory account for the month of June
Compute chill spa net income for 2021
No AI
None
Chapter 6A Solutions
GEN COMBO MANAGERIAL ACCOUNTING FOR MANAGERS; CONNECT 1S ACCESS CARD
Knowledge Booster
Learn more about
Need a deep-dive on the concept behind this application? Look no further. Learn more about this topic, accounting and related others by exploring similar questions and additional content below.Similar questions
- I am trying to find the accurate solution to this general accounting problem with appropriate explanations.arrow_forwardThe actual cost of direct labor per hour is $29.75 and the standard cost of direct labor per hour is $31.20. The direct labor hours allowed per finished unit is 0.85 hours. During the current period, 7,500 units of finished goods were produced using 4,100 direct labor hours. How much is the direct labor rate variance?arrow_forwardPlease provide the accurate answer to this general accounting problem using appropriate methods.arrow_forward
- Mia Steel started the year with total assets of $325,000 and total liabilities of $174,000. During the year the business recorded $360,000 in revenues, $190,000 in expenses, and dividends of $99,000. Stockholders' equity at the end of the year was____.arrow_forwardGeneral accounting questionarrow_forwardCanyon Ridge Inc. has the following Contribution Margin Income Statement: Unit Selling Price: $520 • Total Sales: $3,120,000 • Variable Costs: $410 per unit • Total Variable Costs: $2,460,000 Fixed Costs: $540,000 Question: At this level of activity, what is Canyon Ridge Inc.'s operating leverage factor?arrow_forward
arrow_back_ios
SEE MORE QUESTIONS
arrow_forward_ios
Recommended textbooks for you
- Principles of Cost AccountingAccountingISBN:9781305087408Author:Edward J. Vanderbeck, Maria R. MitchellPublisher:Cengage LearningManagerial AccountingAccountingISBN:9781337912020Author:Carl Warren, Ph.d. Cma William B. TaylerPublisher:South-Western College PubManagerial Accounting: The Cornerstone of Busines...AccountingISBN:9781337115773Author:Maryanne M. Mowen, Don R. Hansen, Dan L. HeitgerPublisher:Cengage Learning
- Financial And Managerial AccountingAccountingISBN:9781337902663Author:WARREN, Carl S.Publisher:Cengage Learning,Cornerstones of Cost Management (Cornerstones Ser...AccountingISBN:9781305970663Author:Don R. Hansen, Maryanne M. MowenPublisher:Cengage Learning
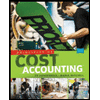
Principles of Cost Accounting
Accounting
ISBN:9781305087408
Author:Edward J. Vanderbeck, Maria R. Mitchell
Publisher:Cengage Learning
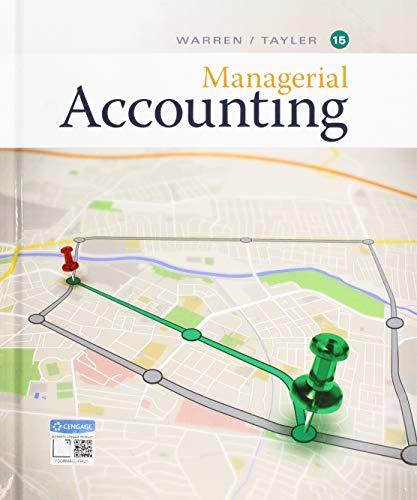
Managerial Accounting
Accounting
ISBN:9781337912020
Author:Carl Warren, Ph.d. Cma William B. Tayler
Publisher:South-Western College Pub
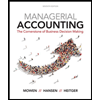
Managerial Accounting: The Cornerstone of Busines...
Accounting
ISBN:9781337115773
Author:Maryanne M. Mowen, Don R. Hansen, Dan L. Heitger
Publisher:Cengage Learning
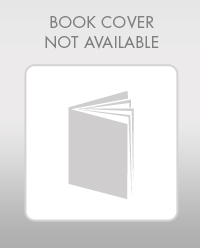
Financial And Managerial Accounting
Accounting
ISBN:9781337902663
Author:WARREN, Carl S.
Publisher:Cengage Learning,
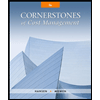
Cornerstones of Cost Management (Cornerstones Ser...
Accounting
ISBN:9781305970663
Author:Don R. Hansen, Maryanne M. Mowen
Publisher:Cengage Learning
Cost Classifications - Managerial Accounting- Fixed Costs Variable Costs Direct & Indirect Costs; Author: Accounting Instruction, Help, & How To;https://www.youtube.com/watch?v=QQd1_gEF1yM;License: Standard Youtube License