
Concept explainers
A.
Single plant-wide factory overhead rate: The rate at which the factory or manufacturing
Formula to compute single plant-wide overhead rate:
To compute: The single plant-wide overhead rate using direct labor hours (DLH) as the allocation base.
A.

Explanation of Solution
Compute single plant-wide overhead rate using DLH as the allocation base.
Step 1: Compute the total number of direct labor hours (DLH) budgeted.
Types of Products | Number of Budgeted Units | × | Number of DLH Per Unit | = | Total Number of Budgeted DLH |
Pistons | 5,000 units | × | 0.50 DLH | = | 2,500 DLH |
Valves | 12,500 units | × | 0.30 DLH | = | 3,750 DLH |
Cams | 1,500 units | × | 0.20 DLH | = | 300 DLH |
Total number of budgeted DLH | 6,550 DLH |
Table (1)
Step 2: Compute single plant-wide overhead rate using DLH as the allocation base.
Note: Refer to Table (1) for value and computation of total number of budgeted DLH.
B.
To compute: The factory overhead allocated per unit of each product, and direct labor cost per unit
B.

Explanation of Solution
Compute the factory overhead allocated per unit for each product.
Types of Products | Single Plant-Wide Overhead Rate | × | Number of DLH Per Unit of Each Product | = | Factory Overhead Per Unit |
Pistons | $25 per DLH | × | 0.50 DLH | = | $12.50 per unit |
Valves | $25 per DLH | × | 0.30 DLH | = | $7.50 per unit |
Cams | $25 per DLH | × | 0.20 DLH | = | $5.00 per unit |
Table (2)
Note: Refer to Step 2 of part (A) for value and computation of single plant-wide overhead rate.
Compute direct labor cost per unit for each product.
Types of Products | Estimated Direct Labor Rate | × | Number of DLH Per Unit of Each Product | = | Direct Labor Cost Per Unit |
Pistons | $30 per DLH | × | 0.50 DLH | = | $15 per unit |
Valves | $30 per DLH | × | 0.30 DLH | = | $9 per unit |
Cams | $30 per DLH | × | 0.20 DLH | = | $60 per unit |
Table (3)
C.
To draft: Budgeted gross profit report of E Engines for the year ended December 31, 20Y2
C.

Explanation of Solution
Prepare a budgeted gross profit report of E Engines, by product line, for the year ended December 31, 20Y2.
E Engines | |||
Budgeted Gross Profit Report | |||
December 31, 20Y2 | |||
Pistons | Valves | Cams | |
Revenues | $225,000 | $212,500 | $90,000 |
Direct materials cost | 40,000 | 37,500 | 60,000 |
Direct labor cost | 75,000 | 112,500 | 9,000 |
Factory overhead | 62,500 | 93,750 | 7,500 |
Total product costs | 177,500 | 243,750 | 76,500 |
Gross profit | $47,500 | $(31,250) | $13,500 |
Gross profit as a percent of sales | 21.1% | (14.7)% | 15.0% |
Table (4)
Working Notes:
Compute sales revenues for each product.
Types of Products | Number of Budgeted Units | × | Price Per Unit | = | Sales Revenue |
Pistons | 5,000 units | × | $45 | = | $225,000 |
Valves | 12,500 units | × | 17 | = | 212,500 |
Cams | 1,500 units | × | 60 | = | 90,000 |
Table (5)
Compute direct material cost for each product.
Types of Products | Number of Budgeted Units | × | Cost Per Unit | = | Direct Material Cost |
Pistons | 5,000 units | × | $8 | = | $40,000 |
Valves | 12,500 units | × | 3 | = | 37,500 |
Cams | 1,500 units | × | 40 | = | 60,000 |
Table (6)
Compute direct labor cost for each product.
Types of Products | Number of Budgeted Units | × | Cost Per Unit | = | Direct Labor Cost |
Pistons | 5,000 units | × | $30 | = | $150,000 |
Valves | 12,500 units | × | 30 | = | 375,000 |
Cams | 1,500 units | × | 30 | = | 45,000 |
Table (7)
Compute total factory overhead allocated for each product.
Types of Products | Number of Budgeted Units | × | Factory Overhead Per Unit | = | Total Factory Overhead |
Pistons | 5,000 units | × | $12.50 per unit | = | $62,500 |
Valves | 12,500 units | × | 7.50 per unit | = | 93,750 |
Cams | 1,500 units | × | 5.00 per unit | = | 7,500 |
Table (8)
Note: Refer to Table (2) for value and computation of factory overhead per unit.
Compute gross profit as a percent of sales for each product.
Types of Products | Gross Profit | ÷ | Sales Revenues | × | 100 | = | Gross Profit Percentage |
Pistons | $47,500 | ÷ | $225,000 | × | 100 | = | 21.1% |
Valves | (31,250) | ÷ | 212,500 | × | 100 | = | (14.7)% |
Cams | 13,500 | ÷ | 90,000 | × | 100 | = | 15% |
Table (9)
Note: Refer to Table (5) for value and computation of sales revenues.
D.
To discuss: The inferences from the gross profit report
D.

Explanation of Solution
Of the three products, pistons are highly profitable, and cams are also profitable as well. But valves are at loss. The sales price per unit should be increased or the cost price should be cut down to increase the profitability of valves.
Want to see more full solutions like this?
Chapter 4 Solutions
Bundle: Managerial Accounting, 14th + Cengagenowv2, 1 Term Printed Access Card
- Please explain the solution to this Financial accounting problem with accurate principles.arrow_forwardKaiser Industries earned an operating income of $35,500 with a contribution margin ratio of 0.40. Actual revenue was $320,000. Calculate the total fixed cost. Round your answer to the nearest dollar, if required.arrow_forwardWhat is the amount of the ending merchandise inventory ?arrow_forward
- Kenneth Manufacturing produces two models of its kitchen tables, the Classic and the Royal. The Classic model requires 5,000 direct labor hours, and the Royal model requires 25,000 direct labor hours. The company produces 4,000 units of the Classic model and 1,500 units of the Royal model each year. The company produces the Classic model in batch sizes of 200, while it produces the Royal model in batch sizes of 150. The company expects to incur $180,000 of total setup costs this year. How much of the setup costs are allocated to the Classic model using ABC costing? A. $80,000 B. $100,000 C. $160,000 D. $120,000arrow_forwardI am looking for the correct answer to this general accounting question with appropriate explanations.arrow_forwardPlease explain how to solve this financial accounting question with valid financial principles.arrow_forward
- Provide correct solution and accountingarrow_forwardWalnut Corporation produces a product that sells for $78.00. Fixed costs are $325,000, and variable costs are $32.00 per unit. Walnut can buy a new production machine that will increase fixed costs by $18,500 per year but will decrease variable costs by $5.50 per unit. Compute the contribution margin per unit if the machine is purchased. a) $46.00 b) $48.50 c) $51.50 d) $52.00 e) $54.00arrow_forward4 POINTSarrow_forward
- Managerial AccountingAccountingISBN:9781337912020Author:Carl Warren, Ph.d. Cma William B. TaylerPublisher:South-Western College PubCornerstones of Cost Management (Cornerstones Ser...AccountingISBN:9781305970663Author:Don R. Hansen, Maryanne M. MowenPublisher:Cengage LearningPrinciples of Accounting Volume 2AccountingISBN:9781947172609Author:OpenStaxPublisher:OpenStax College
- Managerial Accounting: The Cornerstone of Busines...AccountingISBN:9781337115773Author:Maryanne M. Mowen, Don R. Hansen, Dan L. HeitgerPublisher:Cengage LearningFinancial And Managerial AccountingAccountingISBN:9781337902663Author:WARREN, Carl S.Publisher:Cengage Learning,Principles of Cost AccountingAccountingISBN:9781305087408Author:Edward J. Vanderbeck, Maria R. MitchellPublisher:Cengage Learning
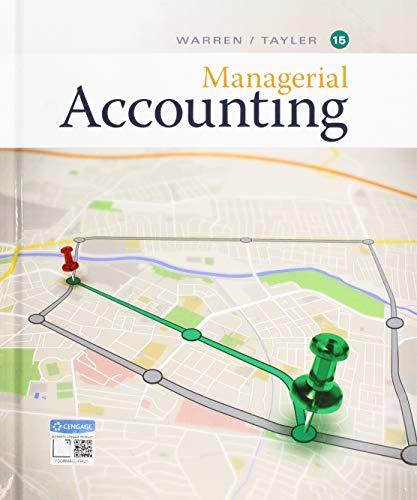
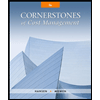
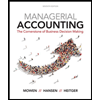
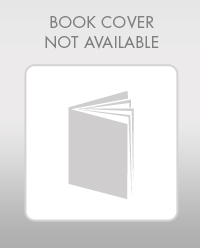
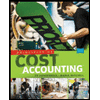