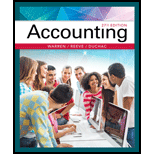
Concept explainers
Variance interpretation
Vanadium Audio Inc. is a small manufacturer of electronic musical instruments. The plant manager received the following variable factory
Actual | Budgeted Variable Factory Overhead at Actual Production | Controllable Variance | |
Supplies | $ 42,000 | $ 39,780 | S 2,220 U |
Power and light | 52,500 | 50,900 | 1,600 U |
Indirect factory wages | 39,100 | 30,600 | 8,500 U |
Total | $133,600 | $121,280 | $12,320 U |
Actual units produced: 15.000 (90% of practical capacity)
The plant manager is not pleased with the $12,320 unfavorable variable factory overhead controllable variance and has come to discuss the matter with the controller. The following discussion occurred:
Plant Manager: I just received this factory report for the latest month of operation. I’m not very pleased with these figures. Before these numbers go to headquarters, you and I need to reach an understanding.
Controller: Go ahead. What’s the problem?
Plant Manager: What's the problem? Well, everything. Look at the variance. It’s too large. If I understand the accounting approach being used here, you are assuming that my costs are variable to the units produced. Thus, as the production volume declines, so should these costs. Well. I don’t believe these costs are variable at all. I think they are fixed costs. As a result when we operate below capacity, the costs really don’t go down. I’m being penalized for costs I have no control over. I need this report to be redone to reflect this fact. If anything, the difference between actual and budget is essentially a volume variance. Listen. I know that you’re a team player. You really need to reconsider your assumptions on this one.
If you were in the controller’s position, how would you respond to the plant manager?

Trending nowThis is a popular solution!

Chapter 23 Solutions
Working Papers, Chapters 18-26 for Warren/Reeve/Duchacâs Accounting, 27E
- I am looking for the correct answer to this financial accounting question with appropriate explanations.arrow_forwardCalculate the current ratio for a company with current assets $200,000 and current liabilities $100,000.arrow_forwardQuincy Electronics common stock is currently selling at $54.75 per share. The company follows a 40% dividend payout ratio and has a P/E ratio of 18. There are 75,000 shares of stock outstanding. What is the amount of the annual net income for the firm?arrow_forward
- Peralta Distillery has estimated budgeted costs of $134,500, $155,000, and $175,500 for the manufacture of 5,000, 7,000, and 9,000 liters of spirits, respectively, next quarter. What are the variable and fixed manufacturing costs in the flexible budget for Peralta Distillery?arrow_forwardIf za company purchases equipment for $50,000, how would this transaction be recorded?arrow_forwardWhat is depreciation, and how is it calculated?arrow_forward
- Managerial AccountingAccountingISBN:9781337912020Author:Carl Warren, Ph.d. Cma William B. TaylerPublisher:South-Western College PubFinancial And Managerial AccountingAccountingISBN:9781337902663Author:WARREN, Carl S.Publisher:Cengage Learning,Principles of Cost AccountingAccountingISBN:9781305087408Author:Edward J. Vanderbeck, Maria R. MitchellPublisher:Cengage Learning
- Principles of Accounting Volume 2AccountingISBN:9781947172609Author:OpenStaxPublisher:OpenStax CollegeManagerial Accounting: The Cornerstone of Busines...AccountingISBN:9781337115773Author:Maryanne M. Mowen, Don R. Hansen, Dan L. HeitgerPublisher:Cengage LearningCornerstones of Cost Management (Cornerstones Ser...AccountingISBN:9781305970663Author:Don R. Hansen, Maryanne M. MowenPublisher:Cengage Learning
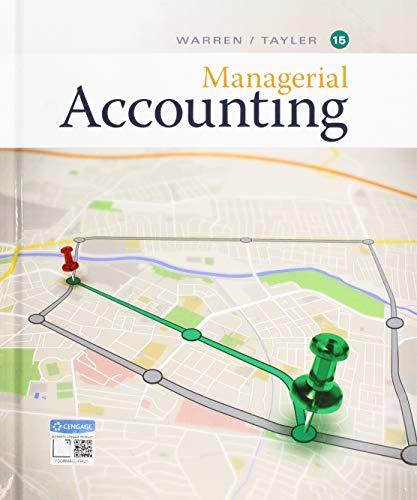
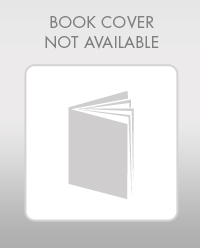
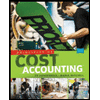
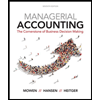
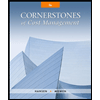