COST ACCOUNTING
16th Edition
ISBN: 9781323169261
Author: Horngren
Publisher: PEARSON C
expand_more
expand_more
format_list_bulleted
Textbook Question
Chapter 20, Problem 20.19MCQ
Lyle Co. has only one product line. For that line, the reorder point is 500 units, the lead time for production is three weeks, and the sales volume is estimated at 50 units per week. Lyle has established which of the following amounts as its safety stock?
- a. 150
- b. 350
- c. 500
- d. 650
Expert Solution & Answer

Want to see the full answer?
Check out a sample textbook solution
Students have asked these similar questions
What is the role of the accounting equation in the analysis of business transactions?
Explain how this theory can help individuals in at least two fields (business, medical, education, etc.) better work in intercultural settings.
Define the theory based on credible sources.
Discuss the development of the theory: how it originated and came to its current status.
Evaluate your scholarly sources, providing a brief comment on the theoretical aspects of each.
Discuss the link(s) between your chosen theory and career field.
Discuss the implications of your case on individuals, society, and the public. How does an increased intercultural understanding affect these different groups?
In 8-10 pages in length. The paper should include support for the topic, your analyses and position(s) by citing course readings, and include at least five credible sources that you chose for your annotated bibliography. A credible source is defined as:
a scholarly or peer-reviewed journal article
which one is correct option?
Chapter 20 Solutions
COST ACCOUNTING
Ch. 20 - Why do better decisions regarding the purchasing...Ch. 20 - Name six cost categories that are important in...Ch. 20 - What assumptions are made when using the simplest...Ch. 20 - Give examples of costs included in annual carrying...Ch. 20 - Give three examples of opportunity costs that...Ch. 20 - What are the steps in computing the cost of a...Ch. 20 - Why might goal-congruence issues arise when...Ch. 20 - JIT purchasing has many benefits but also some...Ch. 20 - What are three factors causing reductions in the...Ch. 20 - You should always choose the supplier who offers...
Ch. 20 - Prob. 20.11QCh. 20 - What are the main features of JIT production, and...Ch. 20 - Distinguish inventory-costing systems using...Ch. 20 - Describe three different versions of backflush...Ch. 20 - Discuss the differences between lean accounting...Ch. 20 - The order size associated with the...Ch. 20 - Prob. 20.17MCQCh. 20 - Prob. 20.18MCQCh. 20 - Lyle Co. has only one product line. For that line,...Ch. 20 - Just-in-time inventory assumes all of the...Ch. 20 - Economic order quantity for retailer. Wonder Line...Ch. 20 - Economic order quantity, effect of parameter...Ch. 20 - EOQ for a retailer. The Fabric World sells fabrics...Ch. 20 - EOQ for manufacturer. Sk8 Company produces...Ch. 20 - Sensitivity of EOQ to changes in relevant ordering...Ch. 20 - JIT production, relevant benefits, relevant costs....Ch. 20 - Backflush costing and JIT production. Grand...Ch. 20 - Backflush costing, two trigger points, materials...Ch. 20 - Backflush costing, two trigger points, completion...Ch. 20 - Prob. 20.30PCh. 20 - Prob. 20.31PCh. 20 - Prob. 20.32PCh. 20 - Prob. 20.33PCh. 20 - JIT purchasing, relevant benefits, relevant costs....Ch. 20 - Supply-chain effects on total relevant inventory...Ch. 20 - Supply-chain effects on total relevant inventory...Ch. 20 - Backflush costing and JIT production. The Acton...Ch. 20 - Backflush, two trigger points, materials purchase...Ch. 20 - Backflush, two trigger points, completion of...Ch. 20 - Lean accounting. Reliable Security Devices (RSD)...Ch. 20 - JIT production, relevant benefits, relevant costs,...
Knowledge Booster
Learn more about
Need a deep-dive on the concept behind this application? Look no further. Learn more about this topic, accounting and related others by exploring similar questions and additional content below.Similar questions
- Net sales total $438,000. Beginning and ending accounts receivable are $35,000 and $37,000, respectively. Calculate days' sales in receivables. A.27 days B.30 days C.36 days D.31 daysarrow_forwardProvide correct answerarrow_forwardFor the system shown in figure below, the per unit values of different quantities are E-1.2, V 1, X X2-0.4. Xa-0.2 Determine whether the system is stable for a sustained fault. The fault is cleared at 8-60°. Is the system stable? If so find the maximum rotor swing. Find the critical clearing angle. E25 G X'd 08 CB X2 F CB V28 Infinite busarrow_forward
- Geisner Inc. has total assets of $1,000,000 and total liabilities of $600,000. The industry average debt-to-equity ratio is 1.20. Calculate Geisner's debt-to-equity ratio and indicate whether the company's default risk is higher or lower than the average of other companies in the industry.arrow_forwardHy expert give me solution this questionarrow_forwardBaker's Market began the current month with inventory costing $35,250, then purchased additional inventory at a cost of $78,400. The perpetual inventory system indicates that inventory costing $82,500 was sold during the month for $88,250. An inventory count at month-end shows that inventory costing $29,000 is actually on hand. What amount of shrinkage occurred during the month? a) $350 b) $1,150 c) $1,750 d) $2,150arrow_forward
- A pet store sells a pet waste disposal system for $60 each. The cost per unit, including the system and enzyme digester, is $42.50. What is the contribution margin per unit? A. $15.00 B. $17.50 C. $12.25 D. $19.00arrow_forwardNarchie sells a single product for $40. Variable costs are 80% of the selling price, and the company has fixed costs that amount to $152,000. Current sales total 16,000 units. What is the break-even point in units?arrow_forwardA company sells 32,000 units at $25 per unit. The variable cost per unit is $20.50, and fixed costs are $52,000. (a) Determine the contribution margin ratio. (b) Determine the unit contribution margin. (c) Determine the income from operations.arrow_forward
arrow_back_ios
SEE MORE QUESTIONS
arrow_forward_ios
Recommended textbooks for you
- EBK CONTEMPORARY FINANCIAL MANAGEMENTFinanceISBN:9781337514835Author:MOYERPublisher:CENGAGE LEARNING - CONSIGNMENTExcel Applications for Accounting PrinciplesAccountingISBN:9781111581565Author:Gaylord N. SmithPublisher:Cengage Learning
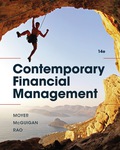
EBK CONTEMPORARY FINANCIAL MANAGEMENT
Finance
ISBN:9781337514835
Author:MOYER
Publisher:CENGAGE LEARNING - CONSIGNMENT
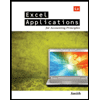
Excel Applications for Accounting Principles
Accounting
ISBN:9781111581565
Author:Gaylord N. Smith
Publisher:Cengage Learning
Inventory management; Author: The Finance Storyteller;https://www.youtube.com/watch?v=DZhHSR4_9B4;License: Standard Youtube License