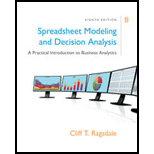
Spreadsheet Modeling & Decision Analysis: A Practical Introduction To Business Analytics, Loose-leaf Version
8th Edition
ISBN: 9781337274852
Author: Ragsdale, Cliff
Publisher: South-Western College Pub
expand_more
expand_more
format_list_bulleted
Concept explainers
Question
thumb_up100%
Chapter 2, Problem 25QP
a)
Summary Introduction
To formulate: An LP model for the problem.
b)
Summary Introduction
To sketch: The feasible region for the problem.
c)
Summary Introduction
To calculate: The optimal solution using corner points.
Expert Solution & Answer

Trending nowThis is a popular solution!

Students have asked these similar questions
For PurrTech’s expansion into Germany, I’ve decided to use a polycentric staffing approach—meaning we’ll hire German professionals to run our operations there. I believe this is the most respectful and effective choice. After all, no one knows how to do business in Germany better than those who live and work there. I want to build something that fits the local culture, not just transplant our way of doing things. Germany is home to a highly skilled and well-educated workforce, especially in technical fields. Their strong focus on vocational training and quality makes this a great opportunity to learn and grow alongside our team there. By working with local talent, we can adapt our products and operations to meet the expectations of German consumers and regulators without missing a beat. When it comes to hiring for leadership roles, my top priority is finding people who combine a solid understanding of local laws and regulations with a forward-thinking, solution-focused mindset. I’m…
What is a good response to this post?
The cultural nuances and education levels in Italy for our new operations, a hybrid staffing approach leaning towards a regiocentric model is most strategic. While initially, a few key global-strategy-aligned individuals might be placed in top leadership an ethnocentric element the primary focus will be on recruiting Italian talent for managerial, administrative, and plant worker roles. Italian managers bring invaluable local market understanding and cultural intelligence crucial for navigating business practices and building relationships. A well-educated local workforce is available for administrative tasks, ensuring smooth daily operations. For plant workers, local hiring is practical and fosters community goodwill. However, my paramount hiring requirement across all levels is adaptability, a growth mindset, and particularly, cultural intelligence. Success in Italy demands individuals who can not only perform their duties but also navigate the…
What is a good response to this post?
A hybrid staffing approach would be the most effective for Nike's expansion into China. This approach allows for Nike to place local professionals in China in key roles, which respect local customs, cultural norms and consumer preferences. Also, it ensures Nike maintains its global standards, innovation mindset and unified brand culture across markets.
When selecting staff for the expansion I would recommend the top requirement to be adaptability and a growth mindset. While technical knowledge and experience is important, the ability to adjust to change, work across cultural boundaries, and have continuous learning is vital in the fast-evolving environment. Having this mindset supports long-term success, fosters innovation, and helps employees navigate challenges naturally.
Chapter 2 Solutions
Spreadsheet Modeling & Decision Analysis: A Practical Introduction To Business Analytics, Loose-leaf Version
Ch. 2 - Prob. 1QPCh. 2 - Prob. 2QPCh. 2 - Prob. 3QPCh. 2 - Prob. 4QPCh. 2 - Prob. 5QPCh. 2 - Prob. 6QPCh. 2 - Prob. 7QPCh. 2 - Prob. 8QPCh. 2 - Prob. 9QPCh. 2 - Prob. 10QP
Ch. 2 - Prob. 11QPCh. 2 - Prob. 12QPCh. 2 - Prob. 13QPCh. 2 - Prob. 14QPCh. 2 - Prob. 15QPCh. 2 - Prob. 16QPCh. 2 - Prob. 17QPCh. 2 - Prob. 18QPCh. 2 - American Auto is evaluating their marketing plan...Ch. 2 - Prob. 20QPCh. 2 - Prob. 21QPCh. 2 - Prob. 22QPCh. 2 - Prob. 23QPCh. 2 - Prob. 24QPCh. 2 - Prob. 25QPCh. 2 - Prob. 26QPCh. 2 - Prob. 1.1CCh. 2 - Prob. 1.2CCh. 2 - Prob. 1.3CCh. 2 - Prob. 1.4CCh. 2 - Prob. 1.5CCh. 2 - Prob. 1.6CCh. 2 - Prob. 1.7CCh. 2 - Prob. 1.8CCh. 2 - Prob. 1.9CCh. 2 - Prob. 1.10C
Knowledge Booster
Learn more about
Need a deep-dive on the concept behind this application? Look no further. Learn more about this topic, management and related others by exploring similar questions and additional content below.Similar questions
- What is a good response to this post? Formal leaders play a critical role in the successful implementation of strategy within an organization. Their authority allows them to make key decisions, allocate necessary resources, and hold individuals accountable for performance. This clear decision-making power and influence can foster alignment across teams, facilitate collaboration, and ensure the strategy’s goals are prioritized. Additionally, their position lends them legitimacy and the ability to inspire others, motivating staff to embrace and execute the plan. With ownership over resources, formal leaders are well-equipped to ensure the necessary infrastructure is in place, and their accountability often drives a strong commitment to achieving success. However, being a formal leader in strategy implementation also presents challenges. Leaders can become overwhelmed by the sheer responsibility of managing both high-level strategy and daily operations, leading to burnout or decision…arrow_forwardCreate an expanded outline for InnovateTech an AI powered healthcare platform to the North American market. Use the bold headings listed below as organizational headers for the main sections of the policy manual. Outline three to five short, relevant commentary sentences supported by any necessary citations. This is an opportunity to organize your ideas for your company and to integrate citations from required sources. Strategy Formation Describe InnovateTech. Comment 1 Comment 2 Comment 3 Describe the value chain analysis of InnovateTech. Description of the strategic initiative (goals to be achieved). Strategy Execution–Policies Potential for process re-engineering to achieve the goal more efficiently. Resource allocation policies to support the initiative’s implementation. Human resource management policies to support the initiative’s implementation. Human resource policies to empower people in supporting organizational success. Incentive policies to support the…arrow_forwardCreate an expanded outline for InnovateTech an AI powered healthcare platform to the North American market. Use the bold headings listed below as organizational headers for the main sections of the policy manual. Outline three to five short, relevant commentary sentences supported by any necessary citations. This is an opportunity to organize your ideas for your company and to integrate citations from required sources. Strategy Formation Description of InnovateTech. Example: Comment 1 (citation, if needed). Example: Comment 2 (citation, if needed). Example: Comment 3 (citation, if needed). Value chain analysis of InnovateTech. Description of the strategic initiative (goals to be achieved). Strategy Execution–Policies Potential for process re-engineering to achieve the goal more efficiently. Resource allocation policies to support the initiative’s implementation. Human resource management policies to support the initiative’s implementation. Human resource policies to empower…arrow_forward
- Create an expanded outline for InnovateTech an AI powered healthcare platform to the North American market. Use the bold headings listed below as organizational headers for the main sections of the policy manual. Outline three to five short, relevant commentary sentences supported by any necessary citations. This is an opportunity to organize your ideas for your company and to integrate citations from required sources. Strategy Formation Description of InnovateTech. Example: Comment 1 (citation, if needed). Example: Comment 2 (citation, if needed). Example: Comment 3 (citation, if needed). Value chain analysis of InnovateTech. Description of the strategic initiative (goals to be achieved). Strategy Execution–Policies Potential for process re-engineering to achieve the goal more efficiently. Resource allocation policies to support the initiative’s implementation. Human resource management policies to support the initiative’s implementation. Human resource policies to empower…arrow_forwardFor this Portfolio Milestone, you will create an expanded outline for InnovateTech an AI powered healthcare platform to the North American market. Use the bold headings listed below as organizational headers for the main sections of the policy manual. These headings do not require additional comment. For each subheading, outline three to five short, relevant commentary sentences supported by any necessary citations. This is an opportunity to organize your ideas for your Portfolio Project and to integrate citations from required sources. The Policy Manual Strategy Formation Description of InnovateTech. Example: Comment 1 (citation, if needed). Example: Comment 2 (citation, if needed). Example: Comment 3 (citation, if needed). Value chain analysis of InnovateTech. Description of the strategic initiative (goals to be achieved). Strategy Execution–Policies Potential for process re-engineering to achieve the goal more efficiently. Resource allocation policies to support the…arrow_forwardWhat is a good response to this post? In this week's lecture, one piece that stuck with me is that "informal leaders are only leaders when others recognize them as such...[because] a leader without followers is not a leader" (Module 5 Lecture). When implementing a strategy, I find that there is great success. with execution when leaders get buy-in from informal leaders. Formal leaders "earned their status by developing strong relationships with the people around them and proving themselves, through actions, to be reliable and trustworthy" (Indeed Editorial Team, 2025). Getting teams onboard a strategy will likely yield the best outcome by collaborating often and openly with informal leaders. Without informal leadership buy-in, strategy implementation could be difficult, as these leaders often set the tone for the people within their team. If an informal leader perhaps disagrees with or dislikes a strategy, an informal leader could even negatively influence the team.arrow_forward
- Drawing on ABC's experience in expanding into Mauritania, discuss the significance of the Experience Curve and Learning Effects for firms expanding internationally, and analyse their long-term benefits in a competitive global market. Demonstrates a clear and thorough understanding of both the Experience Curve and Learning Effects, with detailed examples related to ABC’s expansion. Applies the concepts effectively to ABC’s expansion into Mauritania, with clear examples of how these effects manifest in the new market. Effectively incorporates relevant theories and models to support the analysis. Response should be well-organised, with clear and logical arguments that flow seamlessly. The language is concise and appropriate.arrow_forwardEntering foreign markets presents firms with various strategic options. Using the case of ABC's expansion into Mauritania, discuss the key factors influencing a firm's choice of market entry strategy. Demonstrates a clear and detailed understanding of market entry strategies, providing a strong evaluation of the factors affecting ABC’s choice of entry strategy in Mauritania. Applies relevant theories and concepts effectively to ABC’s entry into Mauritania, with strong, context specific examples and explanations. Provides a comprehensive evaluation of the key factors affecting market entry, explaining how each factor influences the choice. Response should be well-organised, with clear and logical arguments that flow seamlessly. The language is concise and appropriate.arrow_forwardExplain with the help of diagram(s) (a) how the producer's and consumer's risks are related to the natural tolerance set at ±30 in a control chart, and (b) how the two risks are involved in the typical OC-curve?arrow_forward
- for University of wales trinity saint david,uk , give me a image with source for see immage as new brand extention. only immage with source.no need to any writing.arrow_forwardfor university of wales trinity saint david give me a conceptual model as follow new brand extention as immage instruction?arrow_forwardmy boss is considering transferring a member of the international staff, a Training Manager , from Mexico City to the US office in Chicago. She has asked me to use the requirements listed below and to make a recommendation regarding pay and benefits to be paid. I need to write her a memo outlining the job requirements and make a recommendation as to the pay and benefits the Training and development specialist should receive. Use the link below to obtain the required information in order to address the boss' questions in the memo she has required. http://www.salary.com/category/salary/# Find a job description for a Training Manager who has full department wide authority and who is considered a lower middle level manager. In order to use this site you will need to compare up to three similar positions. Select the "Free Salary Data" box for the job you will be using. This will bring up a salary bell curve. To determine benefits to be offered and their costs, select the "benefits"…arrow_forward
arrow_back_ios
SEE MORE QUESTIONS
arrow_forward_ios
Recommended textbooks for you
- Practical Management ScienceOperations ManagementISBN:9781337406659Author:WINSTON, Wayne L.Publisher:Cengage,
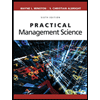
Practical Management Science
Operations Management
ISBN:9781337406659
Author:WINSTON, Wayne L.
Publisher:Cengage,