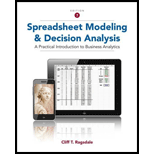
Spreadsheet Modeling and Decision Analysis: A Practical Introduction to Business Analytics
7th Edition
ISBN: 9781285418681
Author: Cliff Ragsdale
Publisher: Cengage Learning
expand_more
expand_more
format_list_bulleted
Concept explainers
Question
Chapter 2, Problem 20QP
a)
Summary Introduction
To formulate: An LP model for the problem.
b)
Summary Introduction
To sketch: The feasible region for the problem.
c)
Summary Introduction
To calculate: The optimal solution using corner points.
Expert Solution & Answer

Trending nowThis is a popular solution!

Students have asked these similar questions
Sarah Anderson, the Marketing Manager at Exeter Township's Cultural Center, is conducting research on the attendance history for cultural events in the area over the past ten years. The following data has been collected on the number of attendees who registered for events at the cultural center.
Year
Number of Attendees
1
700
2
248
3
633
4
458
5
1410
6
1588
7
1629
8
1301
9
1455
10
1989
You have been hired as a consultant to assist in implementing a forecasting system that utilizes various forecasting techniques to predict attendance for Year 11.
a) Calculate the Three-Period Simple Moving Average
b) Calculate the Three-Period Weighted Moving Average (weights: 50%, 30%, and 20%; use 50% for the most recent period, 30% for the next most recent, and 20% for the oldest)
c) Apply Exponential Smoothing with the smoothing constant alpha = 0.2.
d) Perform a Simple Linear Regression analysis and provide the adjusted…
What tend to be the strengths and weaknesses of a group project in university? Describe.
Capsim Team PowerPoint Presentations - Slide Title: Final Results What were your Final Results with Broad Differentiation, R&D, Marketing, Awareness, and Accessibility strategies on your Capsim simulation?
Chapter 2 Solutions
Spreadsheet Modeling and Decision Analysis: A Practical Introduction to Business Analytics
Ch. 2 - Prob. 1QPCh. 2 - Prob. 2QPCh. 2 - Prob. 3QPCh. 2 - Prob. 4QPCh. 2 - Prob. 5QPCh. 2 - Prob. 6QPCh. 2 - Prob. 7QPCh. 2 - Prob. 8QPCh. 2 - Prob. 9QPCh. 2 - Prob. 10QP
Ch. 2 - Prob. 11QPCh. 2 - Prob. 12QPCh. 2 - Prob. 13QPCh. 2 - Prob. 14QPCh. 2 - Prob. 15QPCh. 2 - Prob. 16QPCh. 2 - Prob. 17QPCh. 2 - Prob. 18QPCh. 2 - Prob. 19QPCh. 2 - Prob. 20QPCh. 2 - Prob. 21QPCh. 2 - Prob. 22QPCh. 2 - Prob. 23QPCh. 2 - Prob. 24QPCh. 2 - Prob. 25QPCh. 2 - American Auto is evaluating their marketing plan...Ch. 2 - Prob. 1.1CCh. 2 - Prob. 1.2CCh. 2 - Prob. 1.3CCh. 2 - Prob. 1.4CCh. 2 - Prob. 1.5CCh. 2 - Prob. 1.6CCh. 2 - Prob. 1.7CCh. 2 - Prob. 1.8CCh. 2 - Prob. 1.9CCh. 2 - For the Lines They Are a-Changin (with apologies...
Knowledge Booster
Learn more about
Need a deep-dive on the concept behind this application? Look no further. Learn more about this topic, management and related others by exploring similar questions and additional content below.Similar questions
- Capsim Team PowerPoint Presentations - Slide Title: Strategy Overview Make bullet points about your achievements with Broad Differentiation, R&D, Marketing, Awareness, and Accessibility strategies on Capsim.arrow_forwardCapsim Team PowerPoint Presentations - Slide Title: Strengths and Weaknesses of Your Team Describe the strengths and weaknesses of your team through your Capsim simulation.arrow_forwardCapsim Team PowerPoint Presentations - Slide Title: Major Decision PointWhat were your major decision points with Broad Differentiation, R&D, Marketing, Awareness, and Accessibility strategies on Capsim?arrow_forward
- For PurrTech’s expansion into Germany, I’ve decided to use a polycentric staffing approach—meaning we’ll hire German professionals to run our operations there. I believe this is the most respectful and effective choice. After all, no one knows how to do business in Germany better than those who live and work there. I want to build something that fits the local culture, not just transplant our way of doing things. Germany is home to a highly skilled and well-educated workforce, especially in technical fields. Their strong focus on vocational training and quality makes this a great opportunity to learn and grow alongside our team there. By working with local talent, we can adapt our products and operations to meet the expectations of German consumers and regulators without missing a beat. When it comes to hiring for leadership roles, my top priority is finding people who combine a solid understanding of local laws and regulations with a forward-thinking, solution-focused mindset. I’m…arrow_forwardWhat is a good response to this post? The cultural nuances and education levels in Italy for our new operations, a hybrid staffing approach leaning towards a regiocentric model is most strategic. While initially, a few key global-strategy-aligned individuals might be placed in top leadership an ethnocentric element the primary focus will be on recruiting Italian talent for managerial, administrative, and plant worker roles. Italian managers bring invaluable local market understanding and cultural intelligence crucial for navigating business practices and building relationships. A well-educated local workforce is available for administrative tasks, ensuring smooth daily operations. For plant workers, local hiring is practical and fosters community goodwill. However, my paramount hiring requirement across all levels is adaptability, a growth mindset, and particularly, cultural intelligence. Success in Italy demands individuals who can not only perform their duties but also navigate the…arrow_forwardWhat is a good response to this post? A hybrid staffing approach would be the most effective for Nike's expansion into China. This approach allows for Nike to place local professionals in China in key roles, which respect local customs, cultural norms and consumer preferences. Also, it ensures Nike maintains its global standards, innovation mindset and unified brand culture across markets. When selecting staff for the expansion I would recommend the top requirement to be adaptability and a growth mindset. While technical knowledge and experience is important, the ability to adjust to change, work across cultural boundaries, and have continuous learning is vital in the fast-evolving environment. Having this mindset supports long-term success, fosters innovation, and helps employees navigate challenges naturally.arrow_forward
- What is a good response to this post? Formal leaders play a critical role in the successful implementation of strategy within an organization. Their authority allows them to make key decisions, allocate necessary resources, and hold individuals accountable for performance. This clear decision-making power and influence can foster alignment across teams, facilitate collaboration, and ensure the strategy’s goals are prioritized. Additionally, their position lends them legitimacy and the ability to inspire others, motivating staff to embrace and execute the plan. With ownership over resources, formal leaders are well-equipped to ensure the necessary infrastructure is in place, and their accountability often drives a strong commitment to achieving success. However, being a formal leader in strategy implementation also presents challenges. Leaders can become overwhelmed by the sheer responsibility of managing both high-level strategy and daily operations, leading to burnout or decision…arrow_forwardCreate an expanded outline for InnovateTech an AI powered healthcare platform to the North American market. Use the bold headings listed below as organizational headers for the main sections of the policy manual. Outline three to five short, relevant commentary sentences supported by any necessary citations. This is an opportunity to organize your ideas for your company and to integrate citations from required sources. Strategy Formation Describe InnovateTech. Comment 1 Comment 2 Comment 3 Describe the value chain analysis of InnovateTech. Description of the strategic initiative (goals to be achieved). Strategy Execution–Policies Potential for process re-engineering to achieve the goal more efficiently. Resource allocation policies to support the initiative’s implementation. Human resource management policies to support the initiative’s implementation. Human resource policies to empower people in supporting organizational success. Incentive policies to support the…arrow_forwardCreate an expanded outline for InnovateTech an AI powered healthcare platform to the North American market. Use the bold headings listed below as organizational headers for the main sections of the policy manual. Outline three to five short, relevant commentary sentences supported by any necessary citations. This is an opportunity to organize your ideas for your company and to integrate citations from required sources. Strategy Formation Description of InnovateTech. Example: Comment 1 (citation, if needed). Example: Comment 2 (citation, if needed). Example: Comment 3 (citation, if needed). Value chain analysis of InnovateTech. Description of the strategic initiative (goals to be achieved). Strategy Execution–Policies Potential for process re-engineering to achieve the goal more efficiently. Resource allocation policies to support the initiative’s implementation. Human resource management policies to support the initiative’s implementation. Human resource policies to empower…arrow_forward
- Create an expanded outline for InnovateTech an AI powered healthcare platform to the North American market. Use the bold headings listed below as organizational headers for the main sections of the policy manual. Outline three to five short, relevant commentary sentences supported by any necessary citations. This is an opportunity to organize your ideas for your company and to integrate citations from required sources. Strategy Formation Description of InnovateTech. Example: Comment 1 (citation, if needed). Example: Comment 2 (citation, if needed). Example: Comment 3 (citation, if needed). Value chain analysis of InnovateTech. Description of the strategic initiative (goals to be achieved). Strategy Execution–Policies Potential for process re-engineering to achieve the goal more efficiently. Resource allocation policies to support the initiative’s implementation. Human resource management policies to support the initiative’s implementation. Human resource policies to empower…arrow_forwardFor this Portfolio Milestone, you will create an expanded outline for InnovateTech an AI powered healthcare platform to the North American market. Use the bold headings listed below as organizational headers for the main sections of the policy manual. These headings do not require additional comment. For each subheading, outline three to five short, relevant commentary sentences supported by any necessary citations. This is an opportunity to organize your ideas for your Portfolio Project and to integrate citations from required sources. The Policy Manual Strategy Formation Description of InnovateTech. Example: Comment 1 (citation, if needed). Example: Comment 2 (citation, if needed). Example: Comment 3 (citation, if needed). Value chain analysis of InnovateTech. Description of the strategic initiative (goals to be achieved). Strategy Execution–Policies Potential for process re-engineering to achieve the goal more efficiently. Resource allocation policies to support the…arrow_forwardWhat is a good response to this post? In this week's lecture, one piece that stuck with me is that "informal leaders are only leaders when others recognize them as such...[because] a leader without followers is not a leader" (Module 5 Lecture). When implementing a strategy, I find that there is great success. with execution when leaders get buy-in from informal leaders. Formal leaders "earned their status by developing strong relationships with the people around them and proving themselves, through actions, to be reliable and trustworthy" (Indeed Editorial Team, 2025). Getting teams onboard a strategy will likely yield the best outcome by collaborating often and openly with informal leaders. Without informal leadership buy-in, strategy implementation could be difficult, as these leaders often set the tone for the people within their team. If an informal leader perhaps disagrees with or dislikes a strategy, an informal leader could even negatively influence the team.arrow_forward
arrow_back_ios
SEE MORE QUESTIONS
arrow_forward_ios
Recommended textbooks for you
- Practical Management ScienceOperations ManagementISBN:9781337406659Author:WINSTON, Wayne L.Publisher:Cengage,
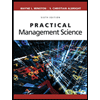
Practical Management Science
Operations Management
ISBN:9781337406659
Author:WINSTON, Wayne L.
Publisher:Cengage,