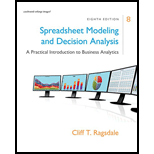
Spreadsheet Modeling & Decision Analysis: A Practical Introduction to Business Analytics (MindTap Course List)
8th Edition
ISBN: 9781305947412
Author: Cliff Ragsdale
Publisher: Cengage Learning
expand_more
expand_more
format_list_bulleted
Concept explainers
Question
Chapter 2, Problem 15QP
a)
Summary Introduction
To formulate: An LP model for the problem.
b)
Summary Introduction
To sketch: The feasible region for the problem.
c)
Summary Introduction
To calculate: The optimal solution using level
Expert Solution & Answer

Want to see the full answer?
Check out a sample textbook solution
Students have asked these similar questions
Geert Hofstede's cultural dimensions theory is a framework for cross-cultural communication, which describes the effects of a society's culture on the values of its members, and how these values relate to behavior. The four dimensions that Hofstede identified are: power distance, uncertainty avoidance, masculinity vs. femininity, and individualism vs. collectivism.
According to Hofstede's research, the Philippines scores high on the Power Distance Index (PDI), which means that the society accepts an unequal distribution of power and people understand their place in the system. The Uncertainty Avoidance Index (UAI) is also high, indicating that the society does not tolerate uncertainty and ambiguity, and tries to minimize the possibility of such situations by strict laws and rules, safety and security measures.
The country scores low on the Individualism (IDV) dimension, which means that the society is Collectivist as compared to Individualist. This is manifest in a close…
How would you monitor the strategy process to ensure that your strategic initiative succeeds? What should be monitored and why? Which Key Performance Indicators (KPIs) needed to be measured and monitored?
Compare and contrast descriptive statistics and inferential statistics. Explain the relationship of population, sampling frame, sampling design, and generalization.
Chapter 2 Solutions
Spreadsheet Modeling & Decision Analysis: A Practical Introduction to Business Analytics (MindTap Course List)
Ch. 2 - Prob. 1QPCh. 2 - Prob. 2QPCh. 2 - Prob. 3QPCh. 2 - Prob. 4QPCh. 2 - Prob. 5QPCh. 2 - Prob. 6QPCh. 2 - Prob. 7QPCh. 2 - Prob. 8QPCh. 2 - Prob. 9QPCh. 2 - Prob. 10QP
Ch. 2 - Prob. 11QPCh. 2 - Prob. 12QPCh. 2 - Prob. 13QPCh. 2 - Prob. 14QPCh. 2 - Prob. 15QPCh. 2 - Prob. 16QPCh. 2 - Prob. 17QPCh. 2 - Prob. 18QPCh. 2 - American Auto is evaluating their marketing plan...Ch. 2 - Prob. 20QPCh. 2 - Prob. 21QPCh. 2 - Prob. 22QPCh. 2 - Prob. 23QPCh. 2 - Prob. 24QPCh. 2 - Prob. 25QPCh. 2 - Prob. 26QPCh. 2 - Prob. 1.1CCh. 2 - Prob. 1.2CCh. 2 - Prob. 1.3CCh. 2 - Prob. 1.4CCh. 2 - Prob. 1.5CCh. 2 - Prob. 1.6CCh. 2 - Prob. 1.7CCh. 2 - Prob. 1.8CCh. 2 - Prob. 1.9CCh. 2 - Prob. 1.10C
Knowledge Booster
Learn more about
Need a deep-dive on the concept behind this application? Look no further. Learn more about this topic, management and related others by exploring similar questions and additional content below.Similar questions
- The research methods used to collect data are Qualitative and Quantitative. If True, discuss. If False, discuss.arrow_forwardIs it important to define the research problem before we collect the data?arrow_forwardContext: I'm a Business Management major in my senior year at University Question: What do you think is your strongest ability and how did you end up being good at it?arrow_forward
- I'm a Business Management major in my senior year at University Question: What would you and others say are five of your personality pluses? And Why?arrow_forwardI'm a Business Management major in my senior year at University Question: What new skills have you learned in the last year? And why were they worth learning?arrow_forwardof the various structures in place today, what do you see as the most beneficial to a technology-laden, forward-thinking organization, and why?arrow_forward
- Sarah Anderson, the Marketing Manager at Exeter Township's Cultural Center, is conducting research on the attendance history for cultural events in the area over the past ten years. The following data has been collected on the number of attendees who registered for events at the cultural center. Year Number of Attendees 1 700 2 248 3 633 4 458 5 1410 6 1588 7 1629 8 1301 9 1455 10 1989 You have been hired as a consultant to assist in implementing a forecasting system that utilizes various forecasting techniques to predict attendance for Year 11. a) Calculate the Three-Period Simple Moving Average b) Calculate the Three-Period Weighted Moving Average (weights: 50%, 30%, and 20%; use 50% for the most recent period, 30% for the next most recent, and 20% for the oldest) c) Apply Exponential Smoothing with the smoothing constant alpha = 0.2. d) Perform a Simple Linear Regression analysis and provide the adjusted…arrow_forwardWhat tend to be the strengths and weaknesses of a group project in university? Describe.arrow_forwardCapsim Team PowerPoint Presentations - Slide Title: Final Results What were your Final Results with Broad Differentiation, R&D, Marketing, Awareness, and Accessibility strategies on your Capsim simulation?arrow_forward
- Capsim Team PowerPoint Presentations - Slide Title: Strategy Overview Make bullet points about your achievements with Broad Differentiation, R&D, Marketing, Awareness, and Accessibility strategies on Capsim.arrow_forwardCapsim Team PowerPoint Presentations - Slide Title: Strengths and Weaknesses of Your Team Describe the strengths and weaknesses of your team through your Capsim simulation.arrow_forwardCapsim Team PowerPoint Presentations - Slide Title: Major Decision PointWhat were your major decision points with Broad Differentiation, R&D, Marketing, Awareness, and Accessibility strategies on Capsim?arrow_forward
arrow_back_ios
SEE MORE QUESTIONS
arrow_forward_ios
Recommended textbooks for you
- Practical Management ScienceOperations ManagementISBN:9781337406659Author:WINSTON, Wayne L.Publisher:Cengage,Purchasing and Supply Chain ManagementOperations ManagementISBN:9781285869681Author:Robert M. Monczka, Robert B. Handfield, Larry C. Giunipero, James L. PattersonPublisher:Cengage Learning
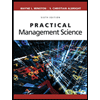
Practical Management Science
Operations Management
ISBN:9781337406659
Author:WINSTON, Wayne L.
Publisher:Cengage,
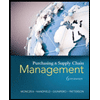
Purchasing and Supply Chain Management
Operations Management
ISBN:9781285869681
Author:Robert M. Monczka, Robert B. Handfield, Larry C. Giunipero, James L. Patterson
Publisher:Cengage Learning