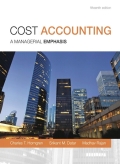
1.
To compute: Manufacturing cycle efficiency
Given information:
Inspection time for 2012 is 4.
Process time for 2012 is 8.
Move time for 2012 is 4.
Order receiving time for 2012 is 15.
Machine setup time for 2012 is 13.
Inspection time for 2013 is 2.
Process time for 2013 is 8.
Move time for 2013 is 4.
Order receiving time for 2013 is 14.
Machine setup time for 2013 is 12.
Calculated values,
Manufacturing time for 2012 is 12.
Manufacturing cycle time for 2012 is 25.
Manufacturing time for 2013 is 10.
Manufacturing cycle time for 2013 is 22.
2.
a.
To compute: Percentage of goods returned
Given information:
Units of finished goods shipped in 2012 are 28,480 units.
Number of units returned in 2012 is 750 units.
Units of finished goods shipped in 2013 are 33,668 units.
Number of units returned in 2013 is 915 units.
b.
To compute: Defective units reworked as a percentage of units shipped.
Given information:
Units of finished goods shipped in 2012 are 28,480 units.
Number of defective units reworked in 2012 is 2,200 units.
Units of finished goods shipped in 2013 are 33,668 units.
Number of defective units reworked in 2013 is 1,640 units.
c.
To compute: Percentage of on-time deliveries.
Given information:
Units of finished goods shipped in 2012 are 28,480 units.
Number of units delivered on time in 2012 is 24,820 units.
Units of finished goods shipped in 2013 are 33,668 units.
Number of units delivered on time in 2013 is 29,935 units
d.
To compute: Percentage of hours spent by each employee in quality training.
Given information:
Average total hours worked per employee in 2012 are 2,000 hours.
Annual hours spent on quality training per employee in 2012 is 38 hours.
Average total hours worked per employee in 2013 are 2,000 hours.
Annual hours spent on quality training per employee in 2013 is 44 hours.
3.
To evaluate: Management’s performance on quality and timeliness.

Want to see the full answer?
Check out a sample textbook solution
Chapter 19 Solutions
Cost Accounting
- Marino Snacks Co. had its highest total cost of $84,000 in July and its lowest total cost of $60,000 in November. The company produces a single product. Production volume was 14,000 units in July and 9,000 units in November. What is the fixed cost per month? HELParrow_forwardWhat is the estimated inventory balance at June 30 ?arrow_forward!!???arrow_forward
- Gable Industries sells its product for $15 per unit. Next year, fixed expenses are expected to be $500,000, and variable expenses are anticipated to be $9 per unit. How many units must the company sell to generate a net operating income of $120,000? Need helparrow_forwardC&L Estates is developing a lakeside community that includes 300 homelots; 140 lots are lakefront lots and will sell for $110,000 each; 160 are interior lots and will sell for $70,000 each. The developer acquired the landfor $2,100,000 and spent another $1,800,000 on road and utility improvements. Compute the amount of joint cost to be allocated to the lakefront lots using a value basis.arrow_forwardCan you help me with General accounting question?arrow_forward
- AccountingAccountingISBN:9781337272094Author:WARREN, Carl S., Reeve, James M., Duchac, Jonathan E.Publisher:Cengage Learning,Accounting Information SystemsAccountingISBN:9781337619202Author:Hall, James A.Publisher:Cengage Learning,
- Horngren's Cost Accounting: A Managerial Emphasis...AccountingISBN:9780134475585Author:Srikant M. Datar, Madhav V. RajanPublisher:PEARSONIntermediate AccountingAccountingISBN:9781259722660Author:J. David Spiceland, Mark W. Nelson, Wayne M ThomasPublisher:McGraw-Hill EducationFinancial and Managerial AccountingAccountingISBN:9781259726705Author:John J Wild, Ken W. Shaw, Barbara Chiappetta Fundamental Accounting PrinciplesPublisher:McGraw-Hill Education
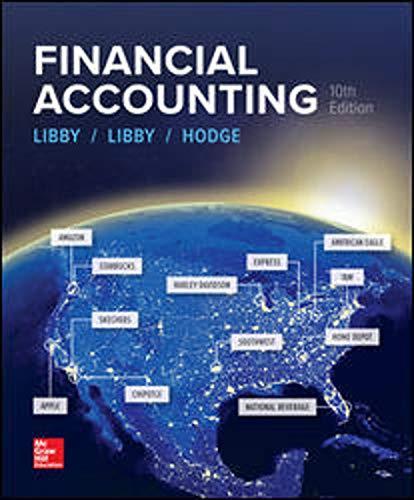
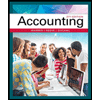
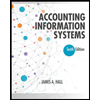
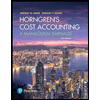
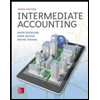
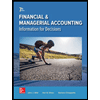