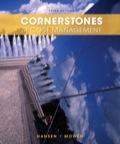
Concept explainers
1 a.
Ascertain the productivity profile for 2014 using actual inputs.
1 a.

Explanation of Solution
Productivity measurement: The productivity measurement refers to the quantitative assessment of the changes in the productivity.
Profile measurement and analysis: The profile measurement and analysis refers to the computation of a set of operational partial productivity measures and their comparison to the corresponding set of base period, for the assessment of the nature of changes in productivity.
Compute the productivity profile for 2014:
Compute the Material Productivity Profile for 2014:
Compute the Labor Productivity Profile for 2014:
The Material Productivity Profile is 1.67 and Labor Productivity Profile is 0.83.
1 b.
Ascertain the productivity profile for 2015 for the proposed process changes.
1 b.

Explanation of Solution
Compute the productivity profile for 2015 Change 1:
Compute the Material Productivity Profile for 2015 Change 1:
Compute the Labor Productivity Profile for 2015 Change 1:
The Material Productivity Profile is 1.43 and Labor Productivity Profile is 1.25.
Compute the productivity profile for 2015 Change 2:
Compute the Material Productivity Profile for 2015 Change 2:
Compute the Labor Productivity Profile for 2015 Change 2:
The Material Productivity Profile is 2.00 and Labor Productivity Profile is 1.00.
There is an overall improvement in the output input ratio from 2014 to 2015.
1 c.
Ascertain the productivity profile for optimal input combination and recommend the most productive profile.
1 c.

Explanation of Solution
Compute the productivity profile for optimal input combination:
Compute the Material Productivity Profile for optimal input combination:
Compute the Labor Productivity Profile for optimal input combination:
The Material Productivity Profile is 2.50 and Labor Productivity Profile is 1.25.
There is an overall improvement in the output input ratio from 2014 to 2015. The change 1 in 2015 has the optimum labor productivity, however the material productivity is very low. In the Change 2 of 2015, both material and labor productivity are good. Now for the decision regarding the implementation of the productivity profile, this depends on the productivity trade-offs of the inputs.
2.
Ascertain the productive inefficiency among the given combinations and compare the improvement along with the changes in the technical and
2.

Explanation of Solution
Total productive efficiency: The total productive efficiency refers to the point where the maximum technical and allocative efficiency is achieved. This is the point where the production of a new product may compromise the production of another product, as the optimum quantity of inputs is being used to get the desired output.
The technical efficiency ensures no more units of input than the required number is used for any mix of inputs.
The allocative efficiency ensures the use of an inexpensive and most technically efficient mix.
Compute the total cost of productive efficiency:
Particulars | Number of Units (A) | Cost per Unit (B) | |
2014 | |||
Cost of materials | 33,000 | $ 60 | $ 1,980,000 |
Cost of labor | 66,000 | $ 15 | $ 990,000 |
Total Cost | $ 2,970,000 | ||
2015 Change 1 | |||
Cost of materials | 38,500 | $ 60 | $ 2,310,000 |
Cost of labor | 44,000 | $ 15 | $ 660,000 |
Total Cost | $ 2,970,000 | ||
2015 Change 2 | |||
Cost of materials | 27,500 | $ 60 | $ 1,650,000 |
Cost of labor | 55,000 | $ 15 | $ 825,000 |
Total Cost | $ 2,475,000 | ||
Optimal Input | |||
Cost of materials | 22,000 | $ 60 | $ 1,320,000 |
Cost of labor | 44,000 | $ 15 | $ 660,000 |
Total Cost | $ 1,980,000 |
Table (1)
Compute the total cost of productive inefficiency:
Compute the cost of productive inefficiency for 2014:
Compute the cost of productive inefficiency for 2015 Change 1:
Compute the cost of productive inefficiency for 2015 Change 2:
Compute the potential improvement:
Compute the potential improvement for 2015 Change 1:
Compute the potential improvement for 2015 Change 2:
The Change 1 has greater technical efficiency but the allocative efficiency is reduced, on the other hand Change 2 is able to attain both technical and allocative efficiency.
3.
Compute and describe the price recovery component.
3.

Explanation of Solution
Profit-linked productivity measurement and analysis: The profit-linked productivity measurement and analysis is the ascertainment of the amount of change in profit, from the base period to the current period, due to the various changes in the productivity.
Compute the profit-linked productivity measurement:
Compute the profit-linked productivity measurement for 2015 Change 1:
Compute the profit-linked productivity measurement for 2015 Change 2:
The profit-linked productivity measurement takes into consideration only the changes in the input with no regards to the base or optimal combination.
Want to see more full solutions like this?
Chapter 15 Solutions
EBK CORNERSTONES OF COST MANAGEMENT
- Suntech Corporation disposed of equipment at the end of the fourth year of its estimated life for $28,000 cash. The equipment's life was originally estimated to be 7 years. The original cost was $95,000, with an estimated residual value of $11,000. The equipment was being depreciated using the straight-line method. What was the gain or loss on the disposal? Solve thisarrow_forwardSuntech Corporation disposed of equipment at the end of the fourth year of its estimated life for $28,000 cash. The equipment's life was originally estimated to be 7 years. The original cost was $95,000, with an estimated residual value of $11,000. The equipment was being depreciated using the straight-line method. What was the gain or loss on the disposal?arrow_forwardPlease provide the solution to this general accounting question with accurate financial calculations.arrow_forward
- Cleopatra Production Inc. estimated its manufacturing overhead costs for 2024 to be $360,000, based on 120,000 estimated machine hours. The actual machine hours for 2024 were 110,000. The manufacturing overhead account contains debit entries totaling $352,000. Determine whether the manufacturing overhead for 2024 was overallocated or underallocated.arrow_forwardPlease explain the solution to this financial accounting problem using the correct financial principles.arrow_forwardI am looking for help with this general accounting question using proper accounting standards.arrow_forward
- Cornerstones of Cost Management (Cornerstones Ser...AccountingISBN:9781305970663Author:Don R. Hansen, Maryanne M. MowenPublisher:Cengage LearningEssentials of Business Analytics (MindTap Course ...StatisticsISBN:9781305627734Author:Jeffrey D. Camm, James J. Cochran, Michael J. Fry, Jeffrey W. Ohlmann, David R. AndersonPublisher:Cengage LearningManagerial AccountingAccountingISBN:9781337912020Author:Carl Warren, Ph.d. Cma William B. TaylerPublisher:South-Western College Pub
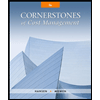
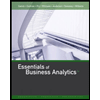
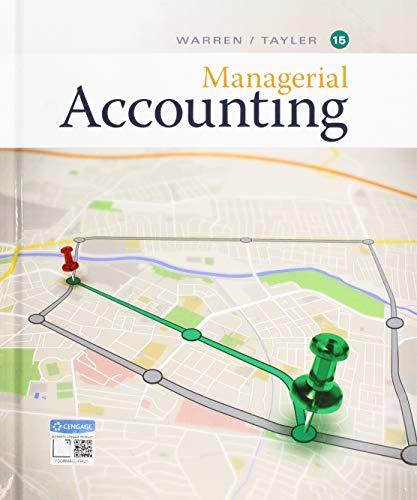