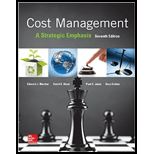
1.
Describes the terms value-added time, non-value added time, and process cycle efficiency (PCE) and specifies how tasks included in the value-added, non-value - added time will be measured.
1.

Explanation of Solution
Operational performance measures are the primary measures used to assess a company's operational efficiency.
Just-in-time (JIT) manufacturing is a strategy that aims to minimize the time a product spends on production while simultaneously reducing the response time for suppliers. Controlling the variables is the secret to keeping down production costs while enhancing efficiency.
Processing cycle efficiency (PCE) is a measure of operating performance defined as the
ratio of processing time to total manufacturing time. It is a method of assessing process efficiency, based on the relationship between actual processing time and total production time. Excluded from this calculation are the "non-value - added" periods associated with the commodity being transported, processed or checked. A time-efficiency calculation is called the "Processing Cycle Efficiency (PCE)" which is defined as follows:
The formula to calculate PCE is:
PCE = Processing time/Total manufacturing time
OR
PCE = Processing Time ÷ (Processing Time + Moving Time + Storage Time + Inspection Time)
Value added time is the production or manufacturing processes and operations that enhance the product or add value to it.
Non-value added time is the amount of time in the manufacturing process that does not produce products or services directly. That is, in other words, the amount of time that the products are not being actively handled.
In the customer's viewpoint the terms "value-added" and "non-value-added" are defined (i.e. an external viewpoint is taken). The conceptions of "value-added" vs. "non-value-added" are not explicitly or specifically defined, because the viewpoint is external. When classifying behaviors the main question is whether the user should "pay" for the operation. It is one way the two concepts can be operationalised. These terminologies are extracted from the literature of activity-based costing (ABC).
2.
Define the terms cycle time and processing (manufacturing) time and mention that how the processing time will be broken down further.
2.

Explanation of Solution
Cycle time (or manufacturing lead time) is the total time from the beginning of manufacturing to the moment when the product is finished.
Cycle time is the total time needed from production start up to output completion. The time required for production (or refining or manufacturing) reflects the time currently needed is known as the processing (manufacturing) time. As such, cycle time includes processing time, preparation time, travel time, configuration time, and inspection time, all of which can be viewed from the customer's perspective as "non-value added."
3.
Calculate and interpret the PCE for both the current manufacturing process and the proposed process after implementing JIT.
3.

Explanation of Solution
Operational performance measures are the primary measures used to assess a company's operational efficiency.
Just-in-time (JIT) manufacturing is a strategy that aims to minimize the time a product spends on production while simultaneously reducing the response time for suppliers. Controlling the variables is the secret to keeping down production costs while enhancing efficiency.
Processing cycle efficiency (PCE) is a measure of operating performance defined as the
ratio of processing time to total manufacturing time. It is a method of assessing process efficiency, based on the relationship between actual processing time and total production time. Excluded from this calculation are the "non-value - added" periods associated with the commodity being transported, processed or checked. A time-efficiency calculation is called the "Processing Cycle Efficiency (PCE)" which is defined as follows:
The formula to calculate PCE is:
PCE = Processing time/Total manufacturing time
OR
PCE = Processing Time ÷ (Processing Time + Moving Time + Storage Time + Inspection Time)
Calculate Processing Cycle Efficiency (PCE), Pre-JIT:
OR
Hence, the processing Cycle Efficiency (PCE), pre-JIT is 30.77%.
Calculate Processing Cycle Efficiency (PCE), Post-JIT Implementation:
OR
Hence, the Processing Cycle Efficiency (PCE), Post-JIT Implementation is 37.50%.
4.
Calculate the percentage change expected under JIT for the average PCE.
4.

Explanation of Solution
Operational performance measures are the primary measures used to assess a company's operational efficiency.
Just-in-time (JIT) manufacturing is a strategy that aims to minimize the time a product spends on production while simultaneously reducing the response time for suppliers. Controlling the variables is the secret to keeping down production costs while enhancing efficiency.
Processing cycle efficiency (PCE) is a measure of operating performance defined as the
ratio of processing time to total manufacturing time. It is a method of assessing process efficiency, based on the relationship between actual processing time and total production time. Excluded from this calculation are the "non-value - added" periods associated with the commodity being transported, processed or checked. A time-efficiency calculation is called the "Processing Cycle Efficiency (PCE)" which is defined as follows:
The formula to calculate PCE is:
PCE = Processing time/Total manufacturing time
OR
PCE = Processing Time ÷ (Processing Time + Moving Time + Storage Time + Inspection Time)
Calculate the percentage change expected under JIT for the average PCE:
Hence, the % change expected under JIT for the average PCE is 22%.
5.
Mention of additional nonfinancial performance metrics that will be tracked by management in accordance with the transition to JIT.
5.

Explanation of Solution
Operational performance measures are the primary measures used to assess a company's operational efficiency.
Just-in-time (JIT) manufacturing is a strategy that aims to minimize the time a product spends on production while simultaneously reducing the response time for suppliers. Controlling the variables is the secret to keeping down production costs while enhancing efficiency.
The transition to a JIT manufacturing method should be followed by improvements in efficiency, declines in waste and inefficiencies, reduction in inventories kept, improvements in cycle times (and customer response time, CRT), and, perhaps, increases in sales. Such standards indicate that the following non-financial performance metrics will be tracked and reported by the
The following are the supplier-Related Measures:
- Deadline from placement of the order (for raw materials) and receipt by the manufacturer of these materials
- On-time delivery percentage
- Percentage of orders issued from placement of order (for raw materials) and receipt by the manufacturer of these materials
- Through companies directly active in the manufacturing process
- Percentage of defects (supplies, components and sub-assemblies)
- The percentage of accredited suppliers (i.e., eligible to supply without incoming inspections);
The following are the production-Related Measures
• Parts-per-million (ppm) defect rates
• Scrap and waste percentage
• % first-pass yield
• Inventory turnover rates
• Machine uptime
• % capacity utilization (i.e., managing the supply of resource capacity)
• Actual production as % of planned production
The following are the distribution activities measures:
• % of items delivered with no (zero) defects
• Number and frequency of customer complaints
• % on-time delivery
• lead time from placement of order to delivery
• Delivery time (i.e., time from completion of production to delivery to customer)
Want to see more full solutions like this?
Chapter 14 Solutions
Cost Management: A Strategic Emphasis
- Hello tutor please given General accounting question answer do fast and properly explain all answerarrow_forwardQuintana Corporation projected current year sales of 42,000 units at a unit sale price of $32.50. Actual current year sales were 39,500 units at $33.75 per unit. Actual variable costs, budgeted at $22.75 per unit, totaled $21.90 per unit. Budgeted fixed costs totaled $375,000, while actual fixed costs amounted to $392,000. What is the sales volume variance for total revenue? I want answerarrow_forwardWhat is hemingway corporation taxable income?arrow_forward
- Please given correct answer for General accounting question I need step by step explanationarrow_forwardArmour vacation cabin was destroyed by a wildfire. He had purchased the cabin 14 months ago for $625,000. He received $890,000 from his insurance company to replace the cabin. If he fails to rebuild the cabin or acquire a replacement property in the required time, how much gain must he recognize on this conversion? A. $375,000 B. $160,000 C. $265,000 D. $0 E. None of the above helparrow_forwardI am looking for the correct answer to this financial accounting question with appropriate explanations.arrow_forward
- AccountingAccountingISBN:9781337272094Author:WARREN, Carl S., Reeve, James M., Duchac, Jonathan E.Publisher:Cengage Learning,Accounting Information SystemsAccountingISBN:9781337619202Author:Hall, James A.Publisher:Cengage Learning,
- Horngren's Cost Accounting: A Managerial Emphasis...AccountingISBN:9780134475585Author:Srikant M. Datar, Madhav V. RajanPublisher:PEARSONIntermediate AccountingAccountingISBN:9781259722660Author:J. David Spiceland, Mark W. Nelson, Wayne M ThomasPublisher:McGraw-Hill EducationFinancial and Managerial AccountingAccountingISBN:9781259726705Author:John J Wild, Ken W. Shaw, Barbara Chiappetta Fundamental Accounting PrinciplesPublisher:McGraw-Hill Education
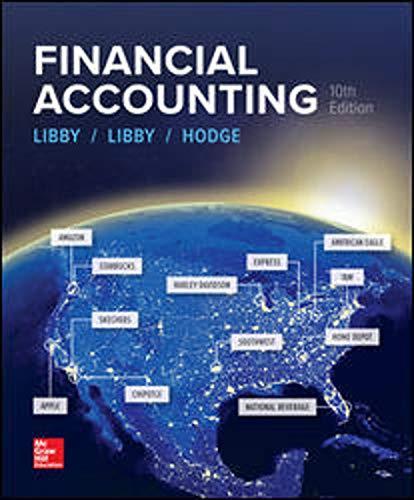
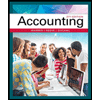
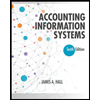
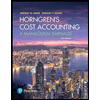
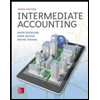
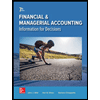