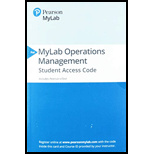
Concept explainers
a)
To develop: A net requirements plan for items.
Introduction:
Net requirements plan:
The net requirements plan is the plan which is established on the gross requirements plan formed by deducting the stock on and the
a)

Explanation of Solution
Given information:
Product structure:
Period | 8 | 9 | 10 | 11 | 12 |
Gross requirements: A | 100 | 50 | 150 | ||
Gross requirements: H | 100 | 50 |
Inventory and lead time:
Item | A | B | C | D | E | F | G | H | J | K |
Lead time | 1 | 2 | 2 | 1 | 2 | 2 | 1 | 1 | 2 | 2 |
On hand | 0 | 100 | 50 | 50 | 75 | 75 | 75 | 0 | 100 | 100 |
- 1 assembly for each item
Item A:
Week | ||||||||||||
Item A | 1 | 2 | 3 | 4 | 5 | 6 | 7 | 8 | 9 | 10 | 11 | 12 |
Gross requirements | 100 | 50 | 150 | |||||||||
Scheduled receipt | ||||||||||||
On hand (0) | 0 | 0 | 0 | |||||||||
Net requirement | 100 | 50 | 150 | |||||||||
Planned order receipt | 100 | 50 | 150 | |||||||||
Planned order release | 100 | 50 | 150 |
Week 8:
The gross requirement is 100 (1 assembly). The on hand inventory is 0. Hence, the net requirement is 100. The lead time is 1 week. Therefore, the planned order release will be 100 in week 7 which will be the planned order receipt in week 8.
Week 10:
The gross requirement is 50 (1 assembly). The on hand inventory is 0. Hence, the net requirement is 50. The lead time is 1 week. Therefore, the planned order release will be 50 in week 9 which will be the planned order receipt in week 10.
Week 12:
The gross requirement is 150 (1 assembly). The on hand inventory is 0. Hence, the net requirement is 150. The lead time is 1 week. Therefore, the planned order release will be 150 in week 11 which will be the planned order receipt in week 12.
Item H:
Week | ||||||||||||
Item H | 1 | 2 | 3 | 4 | 5 | 6 | 7 | 8 | 9 | 10 | 11 | 12 |
Gross requirements | 100 | 50 | ||||||||||
Scheduled receipt | ||||||||||||
On hand (0) | 0 | 0 | ||||||||||
Net requirement | 100 | 50 | ||||||||||
Planned order receipt | 100 | 50 | ||||||||||
Planned order release | 100 | 50 |
Week 9:
The gross requirement is 100 (1 assembly). The on hand inventory is 0. Hence, the net requirement is 1000. The lead time is 1 week. Therefore, the planned order release will be 100 in week 8 which will be the planned order receipt in week 10.
Week 11:
The gross requirement is 50 (1 assembly). The on hand inventory is 0. Hence, the net requirement is 50. The lead time is 1 week. Therefore, the planned order release will be 50 in week 9 which will be the planned order receipt in week 11.
Item B:
Week | ||||||||||||
Item B | 1 | 2 | 3 | 4 | 5 | 6 | 7 | 8 | 9 | 10 | 11 | 12 |
Gross requirements | 100 | 50 | 150 | |||||||||
Scheduled receipt | ||||||||||||
On hand (100) | 100 | 0 | 0 | |||||||||
Net requirement | 0 | 50 | 150 | |||||||||
Planned order receipt | 50 | 150 | ||||||||||
Planned order release | 50 | 150 |
Week 7:
The gross requirement is 100 (1 assembly) derived from planned order release of A. The on hand inventory is 100. Hence, the net requirement is 0. Therefore, there will be no planned order release.
Week 9:
The gross requirement is 50 (1 assembly) derived from the planned order release of A. The on hand inventory is 0. Hence, the net requirement is 50. The lead time is 2 weeks. Therefore, the planned order release will be 50 in week 7 which will be the planned order receipt in week 9.
Week 11:
The gross requirement is 150 (1 assembly) derived from planned order release of A. The on hand inventory is 0. Hence, the net requirement is 150. The lead time is 2 weeks. Therefore, the planned order release will be 150 in week 9 which will be the planned order receipt in week 11.
Item C:
Week | ||||||||||||
Item C | 1 | 2 | 3 | 4 | 5 | 6 | 7 | 8 | 9 | 10 | 11 | 12 |
Gross requirements | 100 | 100 | 50 | 50 | 150 | |||||||
Scheduled receipt | ||||||||||||
On hand (50) | 50 | 0 | 0 | 0 | 0 | |||||||
Net requirement | 50 | 100 | 50 | 50 | 150 | |||||||
Planned order receipt | 50 | 100 | 50 | 50 | 150 | |||||||
Planned order release | 50 | 100 | 50 | 50 | 150 |
Week 7:
The gross requirement is 100 (1 assembly) derived from planned order release of A. The on hand inventory is 50. Hence, the net requirement is 50. The lead time is 2 weeks. Therefore, the planned order release will be 50 in week 5 which will be the planned order receipt in week 7.
Week 8:
The gross requirement is 100 (1 assembly) derived from planned order release of H. The on hand inventory is 0. Hence, the net requirement is 100. The lead time is 2 weeks. Therefore, the planned order release will be 100 in week 6 which will be the planned order receipt in week 8.
Week 9:
The gross requirement is 50 (1 assembly) derived from the planned order release of A. The on hand inventory is 0. Hence, the net requirement is 50. The lead time is 2 weeks. Therefore, the planned order release will be 50 in week 7 which will be the planned order receipt in week 9.
Week 10:
The gross requirement is 50 (1 assembly) derived from planned order release of H. The on hand inventory is 0. Hence, the net requirement is 50. The lead time is 2 weeks. Therefore, the planned order release will be 50 in week 8 which will be the planned order receipt in week 10.
Week 11:
The gross requirement is 150 (1 assembly) derived from planned order release of A. The on hand inventory is 0. Hence, the net requirement is 150. The lead time is 2 weeks. Therefore, the planned order release will be 150 in week 9 which will be the planned order receipt in week 11.
Item J:
Week | ||||||||||||
Item J | 1 | 2 | 3 | 4 | 5 | 6 | 7 | 8 | 9 | 10 | 11 | 12 |
Gross requirements | 100 | 50 | ||||||||||
Scheduled receipt | ||||||||||||
On hand (100) | 100 | 0 | ||||||||||
Net requirement | 0 | 50 | ||||||||||
Planned order receipt | 0 | 50 | ||||||||||
Planned order release | 50 |
Week 8:
The gross requirement is 100 (1 assembly) derived from planned order release of H. The on hand inventory is 100. Hence, the net requirement is 0. Therefore, there will be no planned order release.
Week 10:
The gross requirement is 50 (1 assembly) derived from the planned order release of H. The on hand inventory is 0. Hence, the net requirement is 50. The lead time is 2 weeks. Therefore, the planned order release will be 50 in week 8 which will be the planned order receipt in week 10.
Item K:
Week | ||||||||||||
Item K | 1 | 2 | 3 | 4 | 5 | 6 | 7 | 8 | 9 | 10 | 11 | 12 |
Gross requirements | 100 | 50 | ||||||||||
Scheduled receipt | ||||||||||||
On hand (100) | 100 | 0 | ||||||||||
Net requirement | 0 | 50 | ||||||||||
Planned order receipt | 50 | |||||||||||
Planned order release | 50 |
Week 8:
The gross requirement is 100 (1 assembly) derived from planned order release of H. The on hand inventory is 100. Hence, the net requirement is 0. Therefore, there will be no planned order release.
Week 10:
The gross requirement is 50 (1 assembly) derived from the planned order release of H. The on hand inventory is 0. Hence, the net requirement is 50. The lead time is 2 weeks. Therefore, the planned order release will be 50 in week 8 which will be the planned order receipt in week 10.
Item D:
Week | ||||||||||||
Item D | 1 | 2 | 3 | 4 | 5 | 6 | 7 | 8 | 9 | 10 | 11 | 12 |
Gross requirements | 50 | 150 | ||||||||||
Scheduled receipt | ||||||||||||
On hand (50) | 50 | 0 | ||||||||||
Net requirement | 150 | |||||||||||
Planned order receipt | 150 | |||||||||||
Planned order release | 150 |
Week 7:
The gross requirement is 50 (1 assembly) derived from planned order release of B. The on hand inventory is 500. Hence, the net requirement is 0. Therefore, there will be no planned order release.
Week 9:
The gross requirement is 150 (1 assembly) derived from the planned order release of B. The on hand inventory is 0. Hence, the net requirement is 150. The lead time is 1 week. Therefore, the planned order release will be 150 in week 8 which will be the planned order receipt in week 9.
Item E:
Week | ||||||||||||
Item E | 1 | 2 | 3 | 4 | 5 | 6 | 7 | 8 | 9 | 10 | 11 | 12 |
Gross requirements | 50 | 100 | 150 | |||||||||
Scheduled receipt | ||||||||||||
On hand (75) | 75 | 25 | 0 | |||||||||
Net requirement | 0 | 75 | 150 | |||||||||
Planned order receipt | 75 | 150 | ||||||||||
Planned order release | 75 | 150 |
Week 7:
The gross requirement is 50 (1 assembly) derived from planned order release of B. The on hand inventory is 75. Hence, the net requirement is 0. Therefore, there will be no planned order release.
Week 8:
The gross requirement is 100 (1 assembly) derived from the planned order release of J and K. The on hand inventory is 25. Hence, the net requirement is 75. The lead time is 2 weeks. Therefore, the planned order release will be 75 in week 6 which will be the planned order receipt in week 8.
Week 9:
The gross requirement is 150 (1 assembly) derived from planned order release of B. The on hand inventory is 0. Hence, the net requirement is 150. The lead time is 2 weeks. Therefore, the planned order release will be 150 in week 7 which will be the planned order receipt in week 9.
Item F:
Week | ||||||||||||
Item F | 1 | 2 | 3 | 4 | 5 | 6 | 7 | 8 | 9 | 10 | 11 | 12 |
Gross requirements | 50 | 100 | 50 | 100 | 150 | |||||||
Scheduled receipt | ||||||||||||
On hand (75) | 75 | 25 | 0 | 0 | 0 | |||||||
Net requirement | 0 | 75 | 50 | 100 | 150 | |||||||
Planned order receipt | 75 | 50 | 100 | 150 | ||||||||
Planned order release | 75 | 50 | 100 | 150 |
Week 5:
The gross requirement is 50 (1 assembly) derived from planned order release of C. The on hand inventory is 75. Hence, the net requirement is 0. Therefore, there will be no planned order release.
Week 6:
The gross requirement is 100 (1 assembly) derived from planned order release of C. The on hand inventory is 25. Hence, the net requirement is 75. The lead time is 2 weeks. Therefore, the planned order release will be 75 in week 4 which will be the planned order receipt in week 6.
Week 7:
The gross requirement is 50 (1 assembly) derived from the planned order release of C. The on hand inventory is 0. Hence, the net requirement is 50. The lead time is 2 weeks. Therefore, the planned order release will be 50 in week 5 which will be the planned order receipt in week 7.
Week 8:
The gross requirement is 100 (1 assembly) derived from planned order release of C and J. The on hand inventory is 0. Hence, the net requirement is 100. The lead time is 2 weeks. Therefore, the planned order release will be 100 in week 6 which will be the planned order receipt in week 8.
Week 9:
The gross requirement is 150 (1 assembly) derived from planned order release of C. The on hand inventory is 0. Hence, the net requirement is 150. The lead time is 2 weeks. Therefore, the planned order release will be 150 in week 7 which will be the planned order receipt in week 9.
Item G:
Week | ||||||||||||
Item G | 1 | 2 | 3 | 4 | 5 | 6 | 7 | 8 | 9 | 10 | 11 | 12 |
Gross requirements | 50 | 100 | 50 | 100 | 150 | |||||||
Scheduled receipt | ||||||||||||
On hand (75) | 75 | 25 | 0 | 0 | 0 | |||||||
Net requirement | 0 | 75 | 50 | 100 | 150 | |||||||
Planned order receipt | 75 | 50 | 100 | 150 | ||||||||
Planned order release | 75 | 50 | 100 | 150 |
Week 5:
The gross requirement is 50 (1 assembly) derived from planned order release of C. The on hand inventory is 75. Hence, the net requirement is 0. Therefore, there will be no planned order release.
Week 6:
The gross requirement is 100 (1 assembly) derived from planned order release of C. The on hand inventory is 25. Hence, the net requirement is 75. The lead time is 1 week. Therefore, the planned order release will be 75 in week 5 which will be the planned order receipt in week 6.
Week 7:
The gross requirement is 50 (1 assembly) derived from the planned order release of C. The on hand inventory is 0. Hence, the net requirement is 50. The lead time is 1 week. Therefore, the planned order release will be 50 in week 6 which will be the planned order receipt in week 7.
Week 8:
The gross requirement is 100 (1 assembly) derived from planned order release of C and K. The on hand inventory is 0. Hence, the net requirement is 100. The lead time is 1 week. Therefore, the planned order release will be 100 in week 7 which will be the planned order receipt in week 8.
Week 9:
The gross requirement is 150 (1 assembly) derived from planned order release of C. The on hand inventory is 0. Hence, the net requirement is 150. The lead time is 1 week. Therefore, the planned order release will be 150 in week 8 which will be the planned order receipt in week 9.
b)
To develop: A net requirements plan for all items.
Introduction:
Net requirements plan:
The net requirements plan is the plan which is established on the gross requirements plan formed by deducting the stock on and the scheduled receipts. If the total requirement is below the safety stock levels, a planned order is made based on the given lot sizing technique.
b)

Explanation of Solution
Given information:
Product structure:
Period | 8 | 9 | 10 | 11 | 12 |
Gross requirements: A | 100 | 50 | 150 | ||
Gross requirements: H | 100 | 50 |
Inventory and lead time:
Item | A | B | C | D | E | F | G | H | J | K |
Lead time | 1 | 2 | 2 | 1 | 2 | 2 | 1 | 1 | 2 | 2 |
On hand | 0 | 100 | 50 | 50 | 75 | 75 | 75 | 0 | 100 | 100 |
- 1 assembly for each item
- 2 assemblies for item B, C and F.
Item A:
Week | ||||||||||||
Item A | 1 | 2 | 3 | 4 | 5 | 6 | 7 | 8 | 9 | 10 | 11 | 12 |
Gross requirements | 100 | 50 | 150 | |||||||||
Scheduled receipt | ||||||||||||
On hand (0) | 0 | 0 | 0 | |||||||||
Net requirement | 100 | 50 | 150 | |||||||||
Planned order receipt | 100 | 50 | 150 | |||||||||
Planned order release | 100 | 50 | 150 |
Week 8:
The gross requirement is 100 (1 assembly). The on hand inventory is 0. Hence, the net requirement is 100. The lead time is 1 week. Therefore, the planned order release will be 100 in week 7 which will be the planned order receipt in week 8.
Week 10:
The gross requirement is 50 (1 assembly). The on hand inventory is 0. Hence, the net requirement is 50. The lead time is 1 week. Therefore, the planned order release will be 50 in week 9 which will be the planned order receipt in week 10.
Week 12:
The gross requirement is 150 (1 assembly). The on hand inventory is 0. Hence, the net requirement is 150. The lead time is 1 week. Therefore, the planned order release will be 150 in week 11 which will be the planned order receipt in week 12.
Item H:
Week | ||||||||||||
Item H | 1 | 2 | 3 | 4 | 5 | 6 | 7 | 8 | 9 | 10 | 11 | 12 |
Gross requirements | 100 | 50 | ||||||||||
Scheduled receipt | ||||||||||||
On hand (0) | 0 | 0 | ||||||||||
Net requirement | 100 | 50 | ||||||||||
Planned order receipt | 100 | 50 | ||||||||||
Planned order release | 100 | 50 |
Week 9:
The gross requirement is 100 (1 assembly). The on hand inventory is 0. Hence, the net requirement is 1000. The lead time is 1 week. Therefore, the planned order release will be 100 in week 8 which will be the planned order receipt in week 10.
Week 11:
The gross requirement is 50 (1 assembly). The on hand inventory is 0. Hence, the net requirement is 50. The lead time is 1 week. Therefore, the planned order release will be 50 in week 9 which will be the planned order receipt in week 11.
Item B:
Week | ||||||||||||
Item B | 1 | 2 | 3 | 4 | 5 | 6 | 7 | 8 | 9 | 10 | 11 | 12 |
Gross requirements | 200 | 100 | 300 | |||||||||
Scheduled receipt | ||||||||||||
On hand (100) | 100 | 0 | 0 | |||||||||
Net requirement | 100 | 100 | 300 | |||||||||
Planned order receipt | 100 | 100 | 300 | |||||||||
Planned order release | 100 | 100 | 300 |
Week 7:
The gross requirement is 200 (2 assembly) derived from planned order release of A. The on hand inventory is 100. Hence, the net requirement is 100. Therefore, the planned order release will be 100 in week 5 which will be the planned order receipt in week 7.
Week 9:
The gross requirement is 100 (2 assembly) derived from the planned order release of A. The on hand inventory is 0. Hence, the net requirement is 100. The lead time is 2 weeks. Therefore, the planned order release will be 100 in week 7 which will be the planned order receipt in week 9.
Week 11:
The gross requirement is 300 (2 assembly) derived from planned order release of A. The on hand inventory is 0. Hence, the net requirement is 300. The lead time is 2 weeks. Therefore, the planned order release will be 300 in week 9 which will be the planned order receipt in week 11.
Item C:
Week | ||||||||||||
Item C | 1 | 2 | 3 | 4 | 5 | 6 | 7 | 8 | 9 | 10 | 11 | 12 |
Gross requirements | 200 | 200 | 100 | 100 | 300 | |||||||
Scheduled receipt | ||||||||||||
On hand (50) | 50 | 0 | 0 | 0 | 0 | |||||||
Net requirement | 150 | 200 | 100 | 100 | 300 | |||||||
Planned order receipt | 150 | 200 | 100 | 100 | 300 | |||||||
Planned order release | 150 | 200 | 100 | 100 | 300 |
Week 7:
The gross requirement is 200 (2 assembly) derived from planned order release of A. The on hand inventory is 50. Hence, the net requirement is 150. The lead time is 2 weeks. Therefore, the planned order release will be 150 in week 5 which will be the planned order receipt in week 7.
Week 8:
The gross requirement is 200 (2 assembly) derived from planned order release of H. The on hand inventory is 0. Hence, the net requirement is 200. The lead time is 2 weeks. Therefore, the planned order release will be 200 in week 6 which will be the planned order receipt in week 8.
Week 9:
The gross requirement is 100 (2 assembly) derived from the planned order release of A. The on hand inventory is 0. Hence, the net requirement is 100. The lead time is 2 weeks. Therefore, the planned order release will be 100 in week 7 which will be the planned order receipt in week 9.
Week 10:
The gross requirement is 100 (2 assembly) derived from planned order release of H. The on hand inventory is 0. Hence, the net requirement is 100. The lead time is 2 weeks. Therefore, the planned order release will be 100 in week 8 which will be the planned order receipt in week 10.
Week 11:
The gross requirement is 300 (2 assembly) derived from planned order release of A. The on hand inventory is 0. Hence, the net requirement is 300. The lead time is 2 weeks. Therefore, the planned order release will be 300 in week 9 which will be the planned order receipt in week 11.
Item J:
Week | ||||||||||||
Item J | 1 | 2 | 3 | 4 | 5 | 6 | 7 | 8 | 9 | 10 | 11 | 12 |
Gross requirements | 100 | 50 | ||||||||||
Scheduled receipt | ||||||||||||
On hand (100) | 100 | 0 | ||||||||||
Net requirement | 0 | 50 | ||||||||||
Planned order receipt | 0 | 50 | ||||||||||
Planned order release | 50 |
Week 8:
The gross requirement is 100 (1 assembly) derived from planned order release of H. The on hand inventory is 100. Hence, the net requirement is 0. Therefore, there will be no planned order release.
Week 10:
The gross requirement is 50 (1 assembly) derived from the planned order release of H. The on hand inventory is 0. Hence, the net requirement is 50. The lead time is 2 weeks. Therefore, the planned order release will be 50 in week 8 which will be the planned order receipt in week 10.
Item K:
Week | ||||||||||||
Item K | 1 | 2 | 3 | 4 | 5 | 6 | 7 | 8 | 9 | 10 | 11 | 12 |
Gross requirements | 100 | 50 | ||||||||||
Scheduled receipt | ||||||||||||
On hand (100) | 100 | 0 | ||||||||||
Net requirement | 0 | 50 | ||||||||||
Planned order receipt | 50 | |||||||||||
Planned order release | 50 |
Week 8:
The gross requirement is 100 (1 assembly) derived from planned order release of H. The on hand inventory is 100. Hence, the net requirement is 0. Therefore, there will be no planned order release.
Week 10:
The gross requirement is 50 (1 assembly) derived from the planned order release of H. The on hand inventory is 0. Hence, the net requirement is 50. The lead time is 2 weeks. Therefore, the planned order release will be 50 in week 8 which will be the planned order receipt in week 10.
Item D:
Week | ||||||||||||
Item D | 1 | 2 | 3 | 4 | 5 | 6 | 7 | 8 | 9 | 10 | 11 | 12 |
Gross requirements | 100 | 100 | 300 | |||||||||
Scheduled receipt | ||||||||||||
On hand (50) | 50 | 0 | 0 | |||||||||
Net requirement | 50 | 100 | 300 | |||||||||
Planned order receipt | 50 | 100 | 300 | |||||||||
Planned order release | 50 | 100 | 300 |
Week 6:
The gross requirement is 100 (1 assembly) derived from the planned order release of B. The on hand inventory is 50. Hence, the net requirement is 50. The lead time is 1 week. Therefore, the planned order release will be 50 in week 5 which will be the planned order receipt in week 6.
Week 8:
The gross requirement is 100 (1 assembly) derived from the planned order release of B. The on hand inventory is 0. Hence, the net requirement is 100. The lead time is 1 week. Therefore, the planned order release will be 100 in week 7 which will be the planned order receipt in week 8.
Week 8:
The gross requirement is 300 (1 assembly) derived from the planned order release of B. The on hand inventory is 0. Hence, the net requirement is 300. The lead time is 1 week. Therefore, the planned order release will be 300 in week 9 which will be the planned order receipt in week 10.
Item E:
Week | ||||||||||||
Item E | 1 | 2 | 3 | 4 | 5 | 6 | 7 | 8 | 9 | 10 | 11 | 12 |
Gross requirements | 100 | 100 | 100 | 300 | ||||||||
Scheduled receipt | ||||||||||||
On hand (75) | 75 | 0 | 0 | 0 | ||||||||
Net requirement | 25 | 100 | 100 | 300 | ||||||||
Planned order receipt | 25 | 100 | 100 | 300 | ||||||||
Planned order release | 25 | 100 | 100 | 300 |
Week 5:
The gross requirement is 100 (1 assembly) derived from planned order release of B. The on hand inventory is 75. Hence, the net requirement is 25. The lead time is 2 weeks. Therefore, the planned order release will be 25 in week 3 which will be the planned order receipt in week 5.
Week 7:
The gross requirement is 100 (1 assembly) derived from planned order release of B. The on hand inventory is 0. Hence, the net requirement is 100. The lead time is 2 weeks. Therefore, the planned order release will be 100 in week 5 which will be the planned order receipt in week 7.
Week 8:
The gross requirement is 100 (1 assembly) derived from the planned order release of J and K. The on hand inventory is 0. Hence, the net requirement is 100. The lead time is 2 weeks. Therefore, the planned order release will be 100 in week 6 which will be the planned order receipt in week 8.
Week 9:
The gross requirement is 300 (1 assembly) derived from planned order release of B. The on hand inventory is 0. Hence, the net requirement is 300. The lead time is 2 weeks. Therefore, the planned order release will be 300 in week 7 which will be the planned order receipt in week 9.
Item F:
Week | ||||||||||||
Item F | 1 | 2 | 3 | 4 | 5 | 6 | 7 | 8 | 9 | 10 | 11 | 12 |
Gross requirements | 300 | 400 | 200 | 300 | 600 | |||||||
Scheduled receipt | ||||||||||||
On hand (75) | 75 | 0 | 0 | 0 | 0 | |||||||
Net requirement | 225 | 400 | 200 | 300 | 600 | |||||||
Planned order receipt | 225 | 400 | 200 | 300 | 600 | |||||||
Planned order release | 225 | 400 | 200 | 300 | 600 |
Week 5:
The gross requirement is 300 (2 assembly) derived from planned order release of C. The on hand inventory is 75. Hence, the net requirement is 225. The lead time is 2 weeks. Therefore, the planned order release will be 225 in week 3 which will be the planned order receipt in week 5.
Week 6:
The gross requirement is 400 (2 assembly) derived from planned order release of C. The on hand inventory is 0. Hence, the net requirement is 400. The lead time is 2 weeks. Therefore, the planned order release will be 400 in week 4 which will be the planned order receipt in week 6.
Week 7:
The gross requirement is 200 (2 assembly) derived from the planned order release of C. The on hand inventory is 0. Hence, the net requirement is 200. The lead time is 2 weeks. Therefore, the planned order release will be 200 in week 5 which will be the planned order receipt in week 7.
Week 8:
The gross requirement is 300 (2 assembly) derived from planned order release of C and J. The on hand inventory is 0. Hence, the net requirement is 300. The lead time is 2 weeks. Therefore, the planned order release will be 300 in week 6 which will be the planned order receipt in week 8.
Week 9:
The gross requirement is 600 (2 assembly) derived from planned order release of C. The on hand inventory is 0. Hence, the net requirement is 600. The lead time is 2 weeks. Therefore, the planned order release will be 600 in week 7 which will be the planned order receipt in week 9.
Item G:
Week | ||||||||||||
Item G | 1 | 2 | 3 | 4 | 5 | 6 | 7 | 8 | 9 | 10 | 11 | 12 |
Gross requirements | 150 | 200 | 100 | 150 | 300 | |||||||
Scheduled receipt | ||||||||||||
On hand (75) | 75 | 0 | 0 | 0 | 0 | |||||||
Net requirement | 75 | 200 | 100 | 150 | 300 | |||||||
Planned order receipt | 75 | 200 | 100 | 150 | 300 | |||||||
Planned order release | 75 | 200 | 100 | 150 | 300 |
Week 5:
The gross requirement is 150 (1 assembly) derived from planned order release of C. The on hand inventory is 75. Hence, the net requirement is 75. The lead time is 1 week. Therefore, the planned order release will be 75 in week 4 which will be the planned order receipt in week 5.
Week 6:
The gross requirement is 200 (1 assembly) derived from planned order release of C. The on hand inventory is 0. Hence, the net requirement is 200. The lead time is 1 week. Therefore, the planned order release will be 200 in week 5 which will be the planned order receipt in week 6.
Week 7:
The gross requirement is 100 (1 assembly) derived from the planned order release of C. The on hand inventory is 0. Hence, the net requirement is 100. The lead time is 1 week. Therefore, the planned order release will be 100 in week 6 which will be the planned order receipt in week 7.
Week 8:
The gross requirement is 150 (1 assembly) derived from planned order release of C and K. The on hand inventory is 0. Hence, the net requirement is 150. The lead time is 1 week. Therefore, the planned order release will be 150 in week 7 which will be the planned order receipt in week 8.
Week 9:
The gross requirement is 300 (1 assembly) derived from planned order release of C. The on hand inventory is 0. Hence, the net requirement is 300. The lead time is 1 week. Therefore, the planned order release will be 300 in week 8 which will be the planned order receipt in week 9.
Want to see more full solutions like this?
Chapter 14 Solutions
Pearson eText Principles of Operations Management: Sustainability and Supply Chain Management -- Instant Access (Pearson+)
- The deaths are included in the discharges; this includes deaths occurring in less than 48 hours and postoperative deaths. Rehabilitation had 362 discharges, 22 deaths, 1<48 hours, 0 Postoperative. what is the gross death rate for the rehabilitation service?arrow_forwardA copy machine is available 24 hours a day. On a typical day, the machine produces 100 jobs. Each job takes about 3 minutes on the machine, 2 minutes of which is processing time and 1 minute is setup time (logging in, defining the job). About 20 percent of the jobs need to be reworked, in which case the setup time and the processing time have to be repeated. The remainder of the time, the equipment is idle. What is the OEE of the equipment?arrow_forwardHow do you think we can keep updating Toyota's ideas as new technologies come out and what customers want keeps changing?arrow_forward
- Given how TPS has helped change things in so many fields, do you think there are parts of it that might be hard to use in areas that aren’t about making things, like in healthcare or services? If so, why do you think that might be?arrow_forwardDo you feel there is anything positive about rework?arrow_forwardDo you think technology can achieve faster setup times? How would it be implemented in the hospital workforce?arrow_forward
- In your experience or opinion, do you think process changes like organizing workspaces make a bigger difference, or is investing in technology usually the better solution for faster setups?arrow_forwardHave you seen rework done in your business, and what was done to prevent that from occurring again?arrow_forwardResearch a company different than case studies examined and search the internet and find an example of a business that had to rework a process. How was the organization affected to rework a process in order to restore a good flow unit? Did rework hurt a process or improve the organization's operational efficiency? • Note: Include a reference with supportive citations in the discussion reply in your post.arrow_forward
- Setup time is very important in affecting a process and the capacity of a process. How do you reduce setup time? Give examples of reducing setup time. Please Provide a referenecearrow_forwardDo you think TPS was successful? If so, how? Are there other companies that have used TPS? If so, give examples. Please provide a referencearrow_forwardGiven the significant impact on finances, production timelines, and even equipment functionality, as you pointed out, what do you believe is the most effective single strategy a company can implement to significantly reduce the occurrence of rework within their operations?arrow_forward
- Practical Management ScienceOperations ManagementISBN:9781337406659Author:WINSTON, Wayne L.Publisher:Cengage,MarketingMarketingISBN:9780357033791Author:Pride, William MPublisher:South Western Educational PublishingPurchasing and Supply Chain ManagementOperations ManagementISBN:9781285869681Author:Robert M. Monczka, Robert B. Handfield, Larry C. Giunipero, James L. PattersonPublisher:Cengage Learning
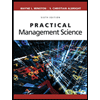
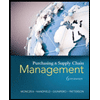