Concept explainers
Joe Birra needs to purchase malt for his microbrewery production. His supplier charges $35 per delivery (no matter how much is delivered) and $1.20 per gallon. Joe’s annual holding cost per unit is 35 percent of the price per gallon. Joe uses 250 gallons of malt per week.
- a. Suppose Joe orders 1000 gallons each time. What is his average inventory (in gal)?
- b. Suppose Joe orders 1500 gallons each time. How many orders does he place with his supplier each year?
- c. How many gallons should Joe order from his supplier with each order to minimize the sum of the ordering and holding costs?
- d. Suppose Joe orders 2500 gallons each time he places an order with the supplier. What is the sum of the ordering and holding costs per gallon?
- e. Suppose Joe orders the quantity from part (C) that minimizes the sum of the ordering and holding costs each time he places an order with the supplier. What is the annual cost of the EOQ expressed as a percentage of the annual purchase cost?
- f. If Joe’s supplier only accepts orders that are an integer multiple of 1000 gallons, how much should Joe order to minimize ordering and holding costs per gallon?
- g. Joe’s supplier offers a 3 percent discount if Joe is willing to purchase 8000 gallons or more. What would Joe’s total annual cost (purchasing, ordering, and holding) be if he were to take advantage of the discount?
a)

To determine: The average inventory in gallon.
Explanation of Solution
Given information:
Weekly demand (d) = 250 gallons
Purchase price (P) per gallon = $1.20
Order cost (O) per order = $35
Annual holding cost (H) = 35%
Weeks per year (W) = 52
Order quantity (Q) = 1,000 gallons
Calculation of average inventory:
The average inventory is 500 gallons.
b)

To determine: The number of orders placed each year.
Explanation of Solution
Given information:
Weekly demand (d) = 250 gallons
Purchase price (P) per gallon = $1.20
Order cost (O) per order = $35
Annual holding cost (H) = 35%
Weeks per year (W) = 52
Order quantity (Q) = 1,500 gallons
Calculation of number of orders each year:
The number of orders each year is 8.67 orders.
c)

To determine: The gallons that must be ordered in each order to minimize the sum of ordering and holding costs.
Explanation of Solution
Given information:
Weekly demand (d) = 250 gallons
Purchase price (P) per gallon = $1.20
Order cost (O) per order = $35
Annual holding cost (H) = 35%
Weeks per year (W) = 52
Calculation of order quantity:
The gallons that must be ordered in each order to minimize the sum of ordering and holding costs is 1,472 gallons.
d)

To determine: The sum of the annual ordering cost and holding costs per gallon.
Explanation of Solution
Given information:
Weekly demand (d) = 250 gallons
Purchase price (P) per gallon = $1.20
Order cost (O) per order = $35
Annual holding cost (H) = 35%
Weeks per year (W) = 52
Order quantity (Q) = 2,500 gallons
Calculation of sum of annual ordering cost and holding costs:
Annual ordering cost:
Annual holding cost:
Sum of annual ordering cost and holding cost:
The sum of the annual ordering cost and holding costs per gallon is $0.0544.
e)

To determine: The annual cost of EOQ expressed as a percentage of the annual purchase cost.
Explanation of Solution
Given information:
Weekly demand (d) = 250 gallons
Purchase price (P) per gallon = $1.20
Order cost (O) per order = $35
Annual holding cost (H) = 35%
Weeks per year (W) = 52
Order quantity (Q) = 1,472 gallons
Calculation of sum of annual ordering cost and holding costs:
Annual ordering cost:
Annual holding cost:
Annual purchase cost:
Annual cost of EOQ as a percentage of the annual purchase cost:
The annual cost of EOQ expressed as a percentage of the annual purchase cost is 3.96%.
f)

To determine: The ordering quantity if the supplier only accepts orders in the integer multiple of 1,000 gallons.
Explanation of Solution
Given information:
Weekly demand (d) = 250 gallons
Purchase price (P) per gallon = $1.20
Order cost (O) per order = $35
Annual holding cost (H) = 35%
Weeks per year (W) = 52
Calculation of sum of annual ordering cost and holding costs:
The EOQ is 1,472 gallons. The cost is calculated for 1,000 gallons and 2,000 gallons and the quantity with the lowest cost is selected.
Cost when Q is 1,000 gallons:
Annual ordering cost:
Annual holding cost:
Sum of annual ordering cost and holding cost:
Cost when Q is 2,000 gallons:
Annual ordering cost:
Annual holding cost:
Sum of annual ordering cost and holding cost:
An order size of 2,000 gallons has lower cost compared to an order size of 1,000 gallons ($647.50 < $665). Therefore, the best order quantity is 1,000 units.
The ordering quantity if the supplier only accepts orders in the integer multiple of 1,000 gallons is 1,000 gallons.
g)

To determine: The sum of the annual ordering cost, purchase cost, and holding costs if Person J takes advantage of the discount.
Explanation of Solution
Given information:
Weekly demand (d) = 250 gallons
Purchase price (P) per gallon = $1.20
Order cost (O) per order = $35
Annual holding cost (H) = 35%
Weeks per year (W) = 52
Discount % (D) = 3%
Order quantity (Q) = 8,000 gallons
Calculation of sum of annual ordering cost, purchase cost, and holding costs:
Annual ordering cost:
Annual holding cost:
Purchase cost
Sum of annual ordering cost, purchase cost, and holding cost:
The sum of the annual ordering cost, purchase cost, and holding costs is $16,818.48.
Want to see more full solutions like this?
Chapter 12 Solutions
OPERATIONS MANAGEMENT LL W/CONNECT CODE
Additional Business Textbook Solutions
Intermediate Accounting (2nd Edition)
Financial Accounting, Student Value Edition (5th Edition)
Principles of Operations Management: Sustainability and Supply Chain Management (10th Edition)
Horngren's Accounting (12th Edition)
Marketing: An Introduction (13th Edition)
Auditing And Assurance Services
- Currently a company that designs Web sites has five customers in its backlog. The time since the order arrived, processing time, and promised due dates are given in the following table. The customers are ready to be scheduled today, which is the start of day 190. Time Since Order Arrived Customer (days ago) Processing Time (days) Due Date (days from now) A 3 24 58 B 2 32 100 с 10 20 26 D E 8 6 12 28 50 66 a. Develop separate schedules by using the FCFS and EDD rules. Compare the schedules on the basis of average flow time and average days past due. Using the FCFS (first come, first served) decision rule for sequencing the customers, the order is: Sequence Customer 1 2 3 4 5arrow_forwardThe Donald Fertilizer Company produces industrial chemical fertilizers. The projected manufacturing requirements (in gallons) for the next four quarters are 60,000, 90,000, 90,000, and 140,000 respectively. A level workforce is desired, relying only on anticipation inventory as a supply option. Stockouts and backorders are to be avoided, as are overtime and undertime. a. Determine the quarterly production rate required to meet total demand for the year, and minimize the anticipation inventory that would be left over at the end of the year. Beginning inventory is 0. The quarterly production rate is ☐ gallons. (Enter your response as an integer.)arrow_forwardHow would you design an operations plan and schedule for a new product/service? What factors would you consider and what challenges would you anticipate? Why are these factors and challenges relevant and how would you address them?arrow_forward
- You are the newly appointed CEO of TechSouth, a South African multinational technology company based in Cape Town. TechSouth specialises in manufacturing smartphones, laptops, and smart home devices. The company has a significant presence in the African market and has recently expanded into Europe and Asia. However, TechSouth is facing several critical challenges:· Declining Market Share - Over the past three years, TechSouth has lost considerable market share to both localcompetitors and international giants like Samsung and Apple. The company's products are perceived as outdated and lacking innovation.· Employee Engagement Issues - Recent employee surveys indicate low morale and engagement levels, particularly among the younger workforce, leading to high turnover rates. Many employees feel disconnected from the company's vision and mission.· Siloed Departments - The organizational structure at TechSouth is highly siloed, with departments operatingindependently rather than…arrow_forwardWhat is the best way to manage emotions and thoughts? How to work through Emotions and thoughts?arrow_forwardWhat are the emotions or stressful thoughts? What are the differences between them? How can we work through the emotions or stressful thoughts? How can we avoid or prevent emotions or stressful thoughts from happening or occurring? What are the obstacles?arrow_forward
- Main Challenges at TechInnovateStrategic DirectionTechInnovate's board of directors is pushing for a more aggressive expansion into emerging markets, particularly in Africaand Southeast Asia. However, there's internal disagreement about whether to focus on these new markets or consolidatetheir position in existing ones. Sarah Chen favors rapid expansion, while some senior executives advocate for a morecautious approach.Ethical ConcernsThe company's AI algorithms have come under scrutiny for potential biases, particularly in facial recognition technology.There are concerns that these biases disproportionately affect minority groups. Some employees have voiced ethicalconcerns about selling this technology to law enforcement agencies without addressing these issues.Team Leadership and DiversityTechInnovate's leadership team is predominantly male and Western, despite its global presence. There's growing pressurefrom employees and some board members to diversify the leadership team to…arrow_forwardSarah Anderson, the Marketing Manager at Exeter Township's Cultural Center, is conducting research on the attendance history for cultural events in the area over the past ten years. The following data has been collected on the number of attendees who registered for events at the cultural center. Year Number of Attendees 1 700 2 248 3 633 4 458 5 1410 6 1588 7 1629 8 1301 9 1455 10 1989 You have been hired as a consultant to assist in implementing a forecasting system that utilizes various forecasting techniques to predict attendance for Year 11. a) Calculate the Three-Period Simple Moving Average b) Calculate the Three-Period Weighted Moving Average (weights: 50%, 30%, and 20%; use 50% for the most recent period, 30% for the next most recent, and 20% for the oldest) c) Apply Exponential Smoothing with the smoothing constant alpha = 0.2. d) Perform a Simple Linear Regression analysis and provide the adjusted…arrow_forwardRuby-Star Incorporated is considering two different vendors for one of its top-selling products which has an average weekly demand of 70 units and is valued at $90 per unit. Inbound shipments from vendor 1 will average 390 units with an average lead time (including ordering delays and transit time) of 4 weeks. Inbound shipments from vendor 2 will average 490 units with an average lead time of 2 weeksweeks. Ruby-Star operates 52 weeks per year; it carries a 4-week supply of inventory as safety stock and no anticipation inventory. Part 2 a. The average aggregate inventory value of the product if Ruby-Star used vendor 1 exclusively is $enter your response here.arrow_forward
- Sam's Pet Hotel operates 50 weeks per year, 6 days per week, and uses a continuous review inventory system. It purchases kitty litter for $13.00 per bag. The following information is available about these bags: > Demand 75 bags/week > Order cost = $52.00/order > Annual holding cost = 20 percent of cost > Desired cycle-service level = 80 percent >Lead time = 5 weeks (30 working days) > Standard deviation of weekly demand = 15 bags > Current on-hand inventory is 320 bags, with no open orders or backorders. a. Suppose that the weekly demand forecast of 75 bags is incorrect and actual demand averages only 50 bags per week. How much higher will total costs be, owing to the distorted EOQ caused by this forecast error? The costs will be $higher owing to the error in EOQ. (Enter your response rounded to two decimal places.)arrow_forwardYellow Press, Inc., buys paper in 1,500-pound rolls for printing. Annual demand is 2,250 rolls. The cost per roll is $625, and the annual holding cost is 20 percent of the cost. Each order costs $75. a. How many rolls should Yellow Press order at a time? Yellow Press should order rolls at a time. (Enter your response rounded to the nearest whole number.)arrow_forwardPlease help with only the one I circled! I solved the others :)arrow_forward
- Purchasing and Supply Chain ManagementOperations ManagementISBN:9781285869681Author:Robert M. Monczka, Robert B. Handfield, Larry C. Giunipero, James L. PattersonPublisher:Cengage LearningPractical Management ScienceOperations ManagementISBN:9781337406659Author:WINSTON, Wayne L.Publisher:Cengage,MarketingMarketingISBN:9780357033791Author:Pride, William MPublisher:South Western Educational Publishing
- Foundations of Business (MindTap Course List)MarketingISBN:9781337386920Author:William M. Pride, Robert J. Hughes, Jack R. KapoorPublisher:Cengage LearningFoundations of Business - Standalone book (MindTa...MarketingISBN:9781285193946Author:William M. Pride, Robert J. Hughes, Jack R. KapoorPublisher:Cengage Learning
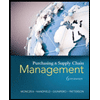
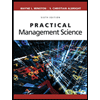
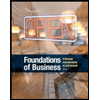
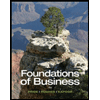