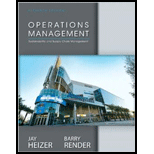
Concept explainers
Parker Hi-Fi Systems
Parker Hi-Fi Systems, located in Wellesley, Massachusetts, a Boston suburb, assembles and sells the very finest home theater systems. The systems are assembled with components from the best manufacturers worldwide. Although most of the components are procured from wholesalers on the east coast, some critical items, such as LCD screens, come directly from their manufacturer. For instance, the LCD screens are shipped via air from Foxy, Ltd., in Taiwan, to Boston’s Logan airport, and the top-of-the-line speakers are purchased from the world-renowned U.S. manufacturer Boss.
Parker’s purchasing agent, Raktim Pal, submits an order release for LCD screens once every 4 weeks. The company’s annual requirements total 500 units (2 per working day), and Parker’s per unit cost is $1,500. (Because of Parker’s relatively low volume and the quality focus—rather than volume focus—of many of Parker’s supplies, Parker is seldom able to obtain quantity discounts.) Since Foxy promises delivery within 1 week following receipt of an order release, Parker has never had a shortage of LCDs. (Total time between date of the release and date of receipt is 1 week or 5 working days.)
Parker’s activity-based costing system has generated the following inventory-related costs. Procurement costs, which amount to $500 per order, include the actual labor costs involved in ordering, custom inspection, arranging for airport pickup, delivery to the plant, maintaining inventory records, and arranging for the bank to issue a check Parker’s holding costs take into account storage, damage, insurance, taxes, and so forth on a square-foot basis. These costs equal $150 per LCD per year.
With added emphasis being placed on efficiencies in the supply chain, Parker’s president has asked Raktim to seriously evaluate the purchase of the LCDs One area to be closely scrutinized for possible cost savings is inventory procurement.
Discussion Questions
- 1. What is the optimal order number of LCDs that should be placed in each order?
- 2. What is the optimal reorder point (ROP) for LCDs?
- 3. What cost savings will Parker realize if it implements an order plan based on EOQ?

Want to see the full answer?
Check out a sample textbook solution
Chapter 12 Solutions
Operations Management
- The deaths are included in the discharges; this includes deaths occurring in less than 48 hours and postoperative deaths. Rehabilitation had 362 discharges, 22 deaths, 1<48 hours, 0 Postoperative. what is the gross death rate for the rehabilitation service?arrow_forwardA copy machine is available 24 hours a day. On a typical day, the machine produces 100 jobs. Each job takes about 3 minutes on the machine, 2 minutes of which is processing time and 1 minute is setup time (logging in, defining the job). About 20 percent of the jobs need to be reworked, in which case the setup time and the processing time have to be repeated. The remainder of the time, the equipment is idle. What is the OEE of the equipment?arrow_forwardHow do you think we can keep updating Toyota's ideas as new technologies come out and what customers want keeps changing?arrow_forward
- Given how TPS has helped change things in so many fields, do you think there are parts of it that might be hard to use in areas that aren’t about making things, like in healthcare or services? If so, why do you think that might be?arrow_forwardDo you feel there is anything positive about rework?arrow_forwardDo you think technology can achieve faster setup times? How would it be implemented in the hospital workforce?arrow_forward
- In your experience or opinion, do you think process changes like organizing workspaces make a bigger difference, or is investing in technology usually the better solution for faster setups?arrow_forwardHave you seen rework done in your business, and what was done to prevent that from occurring again?arrow_forwardResearch a company different than case studies examined and search the internet and find an example of a business that had to rework a process. How was the organization affected to rework a process in order to restore a good flow unit? Did rework hurt a process or improve the organization's operational efficiency? • Note: Include a reference with supportive citations in the discussion reply in your post.arrow_forward
- Setup time is very important in affecting a process and the capacity of a process. How do you reduce setup time? Give examples of reducing setup time. Please Provide a referenecearrow_forwardDo you think TPS was successful? If so, how? Are there other companies that have used TPS? If so, give examples. Please provide a referencearrow_forwardGiven the significant impact on finances, production timelines, and even equipment functionality, as you pointed out, what do you believe is the most effective single strategy a company can implement to significantly reduce the occurrence of rework within their operations?arrow_forward
- Purchasing and Supply Chain ManagementOperations ManagementISBN:9781285869681Author:Robert M. Monczka, Robert B. Handfield, Larry C. Giunipero, James L. PattersonPublisher:Cengage LearningContemporary MarketingMarketingISBN:9780357033777Author:Louis E. Boone, David L. KurtzPublisher:Cengage Learning
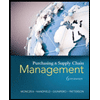
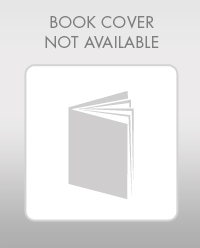
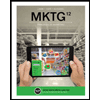