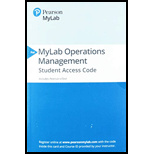
Concept explainers
a)
To determine: The optimal order quantity with the minimum annual cost for purchasing the integrated chips.
Introduction:
Quantity discount model:
Quantity discount model is a scenario where manufacturing companies receive price discount for ordering large quantities. The firm will estimate if the discount quantity is profitable for the firm and make the decision.
Economic order quantity (EOQ):
EOQ is the quantity of units a company must add to its inventory so as to minimize the total inventory costs. It will determine the ideal order quantity which will decrease the inventory management costs.
Annual holding cost:
Annual holding cost is the cost involved in holding the excess inventory present within a firm. The excess inventory will be carried on for the next year and used for production.
Annual ordering cost:
Annual ordering cost is the cost involved in making a purchase order and the following up of that order. It will account for the labor involved and other associated costs.
Purchase cost:
Purchase cost is the cost incurred to purchase the require components to satisfy the demand of the firm. The cost will vary according to the demand.
Total cost:
Total cost is the overall cost taking into estimation of the holding, ordering and the purchase cost of the materials.
a)

Answer to Problem 22P
The optimal order quantity is 200 units with the minimum annual cost of $1,446,380
Explanation of Solution
Given information:
Monthly demand (d)= 400 / month
Holding cost (H) = $35 / unit / year
Ordering cost (S) = $120 / order
Purchase price (P) = $350 / chip
Price structure:
Quantity purchased | Price / unit |
1 – 99 units | $350 |
100 – 199 units | $325 |
200 or more units | $300 |
Formula to calculate EOQ:
Formula to calculate annual holding cost:
Formula to calculate annual ordering cost:
Formula to calculate purchase cost:
Formula to calculate total cost:
Calculation of EOQ:
The obtained EOQ value is in the range of (100 – 199 units). Hence, the price of that range will be used for calculation.
Calculation of values at (EOQ = 181):
Calculation of annual holding cost at (EOQ = 181):
Calculation of annual ordering cost at (EOQ = 181):
Calculation of purchase cost:
Calculation of total cost at (EOQ = 181):
The total cost at the (EOQ = 181) is $1,566,350.
Calculation of values at discount quantity (200):
The next price break after the EOQ at 181 units is (200 or more units). The price of that range will be used in the following calculation.
Calculation of annual holding cost at (EOQ = 200):
Calculation of annual ordering cost at (EOQ = 200):
Calculation of purchase cost:
Calculation of total cost at (EOQ = 200):
The total cost at the (EOQ = 200) is $1,446,380
Calculation of difference in cost:
The total cost at (EOQ = 181) is $1,566,350. The total cost at (EOQ = 200) is $1,446,380. Therefore (EOQ = 200) has lesser cost ($1,446,380 < 1,566,350).
Hence, the optimal order quantity is 200 units with the minimum annual cost of $1,446,380
b)
To determine: The optimal order quantity with the minimum annual cost for purchasing the integrated chips.
b)

Answer to Problem 22P
The optimal order quantity is 200 units with the minimum annual cost of $1,445,880
Explanation of Solution
Given information:
Monthly demand (d)= 400 / month
Holding cost (H) = 10 % of purchase price of the price structure
Ordering cost (S) = $120 / order
Purchase price (P) = $350 / chip
Price structure:
Quantity purchased | Price / unit |
1 – 99 units | $350 |
100 – 199 units | $325 |
200 or more units | $300 |
Formula to calculate EOQ:
Formula to calculate annual holding cost:
Formula to calculate annual ordering cost:
Formula to calculate purchase cost:
Formula to calculate total cost:
Calculation of EOQ at each price structure:
EOQ at price = $350
EOQ at price = $325
EOQ at price = $300
EOQ = 181, cannot be bought at the price of $350. EOQ = 196 cannot be bought at the price of $300.
Hence, the EOQ is 188 units.
The obtained EOQ value is in the range of (100 – 199 units). Hence, the price of that range will be used for calculation.
Calculation of values at (EOQ = 188):
Calculation of annual holding cost at (EOQ = 188):
Calculation of annual ordering cost at (EOQ = 188):
Calculation of purchase cost:
Calculation of total cost at (EOQ = 188):
The total cost at the (EOQ = 188) is $1,566,319.
Calculation of values at discount quantity (200):
The next price break after the EOQ at 188 units is (200 or more units). The price of that range will be used in the following calculation.
Calculation of annual holding cost at (EOQ = 200):
Calculation of annual ordering cost at (EOQ = 200):
Calculation of purchase cost:
Calculation of total cost at (EOQ = 200):
The total cost at the (EOQ = 200) is $1,445,880
Calculation of difference in cost:
The total cost at (EOQ = 188) is $1,566,319. The total cost at (EOQ = 200) is $1,445,880. Therefore (EOQ = 200) has lesser cost ($1,445,880 < 1,566,319).
Hence, the optimal order quantity is 200 units with the minimum annual cost of $1,445,880.
Want to see more full solutions like this?
Chapter 12 Solutions
Pearson eText Principles of Operations Management: Sustainability and Supply Chain Management -- Instant Access (Pearson+)
- PepsiCo South Africa says the incident where a woman discovered part of a rodent in her loaf of bread, is anisolated occurrence.Durban woman, Nombulelo Mkumla, took to social media last week to share how she discovered the rodent.In a lengthy Facebook post, she said she purchased the loaf of bread from a local shop after work on August 27.For the next days, Mkumla proceeded to use slices of bread from the load to make toast."Then, on the morning of August 31, I took the bread out of the fridge to make toast and noticed something disgusting andscary. I took a picture and sent it to my friends, and one of them said, 'Yi mpuku leyo tshomi' [That's a rat friend]“."I was in denial and suggested it might be something else, but the rat scenario made sense - it's possible the rat got into thebread at the factory, and no one noticed," Mkumla said.She went back to the shop she'd bought the bread from and was told to lay a complaint directly with the supplier.She sent an email with a video and…arrow_forwardThe deaths are included in the discharges; this includes deaths occurring in less than 48 hours and postoperative deaths. Rehabilitation had 362 discharges, 22 deaths, 1<48 hours, 0 Postoperative. what is the gross death rate for the rehabilitation service?arrow_forwardA copy machine is available 24 hours a day. On a typical day, the machine produces 100 jobs. Each job takes about 3 minutes on the machine, 2 minutes of which is processing time and 1 minute is setup time (logging in, defining the job). About 20 percent of the jobs need to be reworked, in which case the setup time and the processing time have to be repeated. The remainder of the time, the equipment is idle. What is the OEE of the equipment?arrow_forward
- How do you think we can keep updating Toyota's ideas as new technologies come out and what customers want keeps changing?arrow_forwardGiven how TPS has helped change things in so many fields, do you think there are parts of it that might be hard to use in areas that aren’t about making things, like in healthcare or services? If so, why do you think that might be?arrow_forwardDo you feel there is anything positive about rework?arrow_forward
- Do you think technology can achieve faster setup times? How would it be implemented in the hospital workforce?arrow_forwardIn your experience or opinion, do you think process changes like organizing workspaces make a bigger difference, or is investing in technology usually the better solution for faster setups?arrow_forwardHave you seen rework done in your business, and what was done to prevent that from occurring again?arrow_forward
- Research a company different than case studies examined and search the internet and find an example of a business that had to rework a process. How was the organization affected to rework a process in order to restore a good flow unit? Did rework hurt a process or improve the organization's operational efficiency? • Note: Include a reference with supportive citations in the discussion reply in your post.arrow_forwardSetup time is very important in affecting a process and the capacity of a process. How do you reduce setup time? Give examples of reducing setup time. Please Provide a referenecearrow_forwardDo you think TPS was successful? If so, how? Are there other companies that have used TPS? If so, give examples. Please provide a referencearrow_forward
- Purchasing and Supply Chain ManagementOperations ManagementISBN:9781285869681Author:Robert M. Monczka, Robert B. Handfield, Larry C. Giunipero, James L. PattersonPublisher:Cengage LearningPractical Management ScienceOperations ManagementISBN:9781337406659Author:WINSTON, Wayne L.Publisher:Cengage,
- Contemporary MarketingMarketingISBN:9780357033777Author:Louis E. Boone, David L. KurtzPublisher:Cengage LearningMarketingMarketingISBN:9780357033791Author:Pride, William MPublisher:South Western Educational Publishing
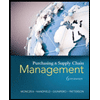
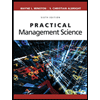
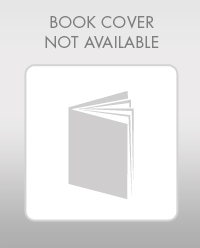