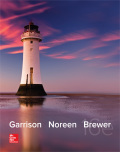
1)
Delivery Cycle, Throughput Time, Manufacturing Cycle Efficiency:
The time taken from the start of the sale process, i.e. the receipt of a confirmed sales order, to the completion of the transfer of goods or services, i.e. dispatch of goods is known as the Delivery Cycle.
It consists of throughput time, Value added time and non-value added time.
To depict delivery cycle in the formula form, the following formula maybe used:
Delivery Cycle = Value added Elements of Throughput Time + Non Value Added Elements of Throughput Time.
Manufacturing Cycle Efficiency is an internal business performance parameter with respect to manufacturing processes and industries. It measures the total time taken by value added activities in relation to the throughput time.
- Throughput Time
- Delivery Cycle
- Manufacturing Cycle Efficiency
1)

Answer to Problem 19P
Solution:
Average Time per month (in days) | ||||
Particulars | 1 | 2 | 3 | 4 |
Throughput Time | 7.30 | 8.10 | 8.80 | 9.60 |
Delivery Cycle | 16.30 | 19.60 | 20.80 | 23.60 |
Manufacturing Cycle Efficiency | 0.29 | 0.25 | 0.22 | 0.19 |
Explanation of Solution
- Throughput time comprises of two main categories of elements i.e. Value added and Non Value added elements.
- Value added elements refer to the time taken for those activities that add quality and value to the overall production process concerning manufacture of goods. Example − Process Time.
- Process time is the time spent on actually producing the product. It refers to the time taken to convert the goods from raw materials to interim or final finished products
- Non Value added elements refer to the time taken for those activities that do not add quality and value to the overall production process concerning manufacture of goods and that need to be eliminated to the greatest extent possible. Example - Inspection Time, Move Time and Queue time
- Inspection time is the amount of time spent assuring that the product is defect free to the best possible extent
- Move time is the time required to transfer raw materials or interim or final finished products from one location to another, such as factory to job workers’ location.
- Queue time is the amount of time that is spent waiting for the actually production activities to commence since other products are being produced or worked upon.
- Given:
Average Time per month (in days) | ||||
Particulars | 1.0 | 2.0 | 3.0 | 4.0 |
Move time per unit | 0.3 | 0.4 | 0.4 | 0.5 |
Process Time per unit | 2.1 | 2.0 | 1.9 | 1.8 |
Wait time per order | 9.0 | 11.5 | 12.0 | 14.0 |
Queue Time per unit | 4.3 | 5.0 | 5.8 | 6.7 |
Inspection Time per unit | 0.6 | 0.7 | 0.7 | 0.6 |
- Formulas Used:
- Total Throughput Time = Time Taken by value added activities + Time Taken by Non value added activities (Except Wait Time)
- Delivery Cycle = Non Value Added activities + Total Throughput Time
- Manufacturing cycle efficiency = Time Taken by value added activities / Total Throughput Time.
- Time Taken by value added activities = Time taken for Process Time
- Time Taken by Non value added activities = Time taken for Move Time + Queue Time + Inspection Time
- Calculations:
Average Time per month (in days) | ||||
Particulars | 1.0 | 2.0 | 3.0 | 4.0 |
Move time per unit | 0.3 | 0.4 | 0.4 | 0.5 |
Queue Time per unit | 4.3 | 5.0 | 5.8 | 6.7 |
Inspection Time per unit | 0.6 | 0.7 | 0.7 | 0.6 |
Total Time For Non Value Added Activities (A) | 5.2 | 6.1 | 6.9 | 7.8 |
Process Time per unit | 2.1 | 2.0 | 1.9 | 1.8 |
Total Time For Non Value Added Activities (B) | 2.1 | 2.0 | 1.9 | 1.8 |
Throughput Time (A+B) [C] | 7.3 | 8.1 | 8.8 | 9.6 |
Wait time per order [D] | 9.0 | 11.5 | 12.0 | 14.0 |
Delivery Cycle (C+D) | 16.3 | 19.6 | 20.8 | 23.6 |
Manufacturing Cycle Efficiency | Time Taken by value added activities / Total Throughput Time. | |||
Manufacturing Cycle Efficiency | 0.29 | 0.25 | 0.22 | 0.19 |
Hence the throughput time, delivery cycle, and manufacturing cycle efficiency has been calculated for each months.
2)
Evaluation of Manufacturing Cycle efficiency and its’ components
The time taken from the start of the sale process, i.e. the receipt of a confirmed sales order, to the completion of the transfer of goods or services, i.e. dispatch of goods is known as the Delivery Cycle.
It consists of throughput time, Value added time and non-value added time.
To depict delivery cycle in the formula form, the following formula maybe used:
Delivery Cycle = Value added Elements of Throughput Time + Non Value Added Elements of Throughput Time.
Manufacturing Cycle Efficiency is an internal business performance parameter with respect to manufacturing processes and industries. It measures the total time taken by value added activities in relation to the throughput time.
Hence evaluation has to be done of the following parameters:
- Throughput time
- Delivery Cycle Time
- Manufacturing Cycle Efficiency
- Areas where company’s performance is improving.
- Areas where company’s performance is deteriorating.

Answer to Problem 19P
Solution:
- Areas where company’s performance is improving are None
- Areas where company’s performance is deteriorating are throughput time and delivery cycle time and manufacturing cycle efficiency.
Explanation of Solution
- Throughput time comprises of two main categories of elements i.e. Value added and Non Value added elements.
- Value added elements refer to the time taken for those activities that add quality and value to the overall production process concerning manufacture of goods. Example − Process Time.
- Non Value added elements refer to the time taken for those activities that do not add quality and value to the overall production process concerning manufacture of goods and that need to be eliminated to the greatest extent possible. Example - Inspection Time, Move Time and Queue time
- Following are the Throughput time for four months:
Average Time per month (in days) | ||||
Particulars | 1 | 2 | 3 | 4 |
Throughput Time | 7.30 | 8.10 | 8.80 | 9.60 |
- Since the total throughput time is increasing, it can be said the company’s performance is deteriorating.
- The time taken from the start of the sale process, i.e. the receipt of a confirmed sales order, to the completion of the transfer of goods or services, i.e. dispatch of goods is known as the Delivery Cycle.
- Following are the Delivery cycle times for four months:
Average Time per month (in days) | ||||
Particulars | 1 | 2 | 3 | 4 |
Delivery Cycle | 16.30 | 19.60 | 20.80 | 23.60 |
- Since the total delivery cycle time is increasing, it can be said the company’s performance is deteriorating.
- Manufacturing cycle efficiency helps keep track of where time and cost is incurred in non-value added activities and performance efficiency measurement.
- Manufacturing cycle efficiency is denoted by the following formula:
Manufacturing cycle efficiency = Time Taken by value added activities / Total Throughput Time.
Total Throughput Time = Time Taken by value added activities + Time Taken by Non value added activities
- For example if the time Taken by value added activities is 25 minutes per unit and the Time Taken by non-value added activities is 35 minutes then manufacturing cycle efficiency would be 0.42.
- Thus it can be interpreted as, the value added activities take up only 42 % of the total time taken to complete the manufacturing process and the rest is attributable to non-value added activities.
Average Time per month (in days) | ||||
Particulars | 1 | 2 | 3 | 4 |
Manufacturing Cycle Efficiency | 0.29 | 0.25 | 0.22 | 0.19 |
- Since the Manufacturing Cycle Efficiency is decreasing, the company’s performance is deteriorating.
Hence the performance measures where the company’s performance is increasing and decreasing are enumerated.
3)
a)
Throughput Time, Manufacturing Cycle Efficiency
The time taken from the start of the sale process, i.e. the receipt of a confirmed sales order, to the completion of the transfer of goods or services, i.e. dispatch of goods is known as the Delivery Cycle.
It consists of throughput time, Value added time and non-value added time.
To depict delivery cycle in the formula form, the following formula maybe used:
Delivery Cycle = Value added Elements of Throughput Time + Non Value Added Elements of Throughput Time.
Manufacturing Cycle Efficiency is an internal business performance parameter with respect to manufacturing processes and industries. It measures the total time taken by value added activities in relation to the throughput time.
- Throughput Time for Month 5
- Manufacturing Cycle Efficiency for Month 5

Answer to Problem 19P
Solution:
Average Time per month (in days) | ||
Particulars | 4 | 5 |
Throughput Time | 9.60 | 2.90 |
Manufacturing Cycle Efficiency for month 5 | 0.19 | 0.62 |
Explanation of Solution
- Throughput time comprises of two main categories of elements i.e. Value added and Non Value added elements.
- Value added elements refer to the time taken for those activities that add quality and value to the overall production process concerning manufacture of goods. Example − Process Time.
- Process time is the time spent on actually producing the product. It refers to the time taken to convert the goods from raw materials to interim or final finished products
- Non Value added elements refer to the time taken for those activities that do not add quality and value to the overall production process concerning manufacture of goods and that need to be eliminated to the greatest extent possible. Example - Inspection Time, Move Time and Queue time
- Inspection time is the amount of time spent assuring that the product is defect free to the best possible extent
- Move time is the time required to transfer raw materials or interim or final finished products from one location to another, such as factory to job workers’ location.
- Queue time is the amount of time that is spent waiting for the actually production activities to commence since other products are being produced or worked upon.
- Given:
Particulars | 4 | 5 |
Move time per unit | 0.5 | 0.5 |
Queue Time per unit | 6.7 | 0.0 |
Inspection Time per unit | 0.6 | 0.6 |
Process Time per unit | 1.8 | 1.8 |
- Total Throughput Time = Time Taken by value added activities + Time Taken by Non value added activities (Except Wait Time)
- Manufacturing cycle efficiency = Time Taken by value added activities / Total Throughput Time.
- Time Taken by value added activities = Time taken for Process Time
- Time Taken by Non value added activities = Time taken for Move Time + Queue Time + Inspection Time
- Calculations:
Average Time per month (in days) | ||
Particulars | 4 | 5 |
Move time per unit | 0.5 | 0.5 |
Queue Time per unit | 6.7 | 0.0 |
Inspection Time per unit | 0.6 | 0.6 |
Total Time For Non Value Added Activities (A) | 7.8 | 1.1 |
Process Time per unit | 1.8 | 1.8 |
Total Time For Value Added Activities (B) | 1.8 | 1.8 |
Throughput Time (A+B) [C] | 9.6 | 2.9 |
Manufacturing Cycle Efficiency | Time Taken by value added activities / Total Throughput Time. | |
Manufacturing Cycle Efficiency | 0.19 | 0.62 |
Hence the throughput time and manufacturing cycle efficiency has been calculated for month 5.
3)
b)
Throughput Time, Manufacturing Cycle Efficiency
The time taken from the start of the sale process, i.e. the receipt of a confirmed sales order, to the completion of the transfer of goods or services, i.e. dispatch of goods is known as the Delivery Cycle.
It consists of throughput time, Value added time and non-value added time.
To depict delivery cycle in the formula form, the following formula maybe used:
Delivery Cycle = Value added Elements of Throughput Time + Non Value Added Elements of Throughput Time.
Manufacturing Cycle Efficiency is an internal business performance parameter with respect to manufacturing processes and industries. It measures the total time taken by value added activities in relation to the throughput time.
- Throughput Time for Month 6
- Manufacturing Cycle Efficiency for Month 6

Answer to Problem 19P
Solution:
Average Time per month (in days) | ||
Particulars | 4 | 6 |
Throughput Time | 9.60 | 2.30 |
Manufacturing Cycle Efficiency for month 6 | 0.19 | 0.78 |
Explanation of Solution
- Throughput time comprises of two main categories of elements i.e. Value added and Non Value added elements.
- Value added elements refer to the time taken for those activities that add quality and value to the overall production process concerning manufacture of goods. Example − Process Time.
- Process time is the time spent on actually producing the product. It refers to the time taken to convert the goods from raw materials to interim or final finished products
- Non Value added elements refer to the time taken for those activities that do not add quality and value to the overall production process concerning manufacture of goods and that need to be eliminated to the greatest extent possible. Example - Inspection Time, Move Time and Queue time
- Inspection time is the amount of time spent assuring that the product is defect free to the best possible extent
- Move time is the time required to transfer raw materials or interim or final finished products from one location to another, such as factory to job workers’ location.
- Queue time is the amount of time that is spent waiting for the actually production activities to commence since other products are being produced or worked upon.
- Given:
Particulars | 4 | 6 |
Move time per unit | 0.5 | 0.5 |
Queue Time per unit | 6.7 | 0.0 |
Inspection Time per unit | 0.6 | 0.0 |
Process Time per unit | 1.8 | 1.8 |
- Total Throughput Time = Time Taken by value added activities + Time Taken by Non value added activities (Except Wait Time)
- Manufacturing cycle efficiency = Time Taken by value added activities / Total Throughput Time.
- Time Taken by value added activities = Time taken for Process Time
- Time Taken by Non value added activities = Time taken for Move Time + Queue Time + Inspection Time
- Calculations:
Average Time per month (in days) | ||
Particulars | 4 | 6 |
Move time per unit | 0.5 | 0.5 |
Queue Time per unit | 6.7 | 0.0 |
Inspection Time per unit | 0.6 | 0.0 |
Total Time For Non Value Added Activities (A) | 7.8 | 0.5 |
Process Time per unit | 1.8 | 1.8 |
Total Time For Value Added Activities (B) | 1.8 | 1.8 |
Throughput Time (A+B) [C] | 9.6 | 2.3 |
Manufacturing Cycle Efficiency | Time Taken by value added activities / Total Throughput Time. | |
Manufacturing Cycle Efficiency | 0.19 | 0.78 |
Hence the throughput time and manufacturing cycle efficiency has been calculated for month 6.
Want to see more full solutions like this?
Chapter 11 Solutions
Managerial Accounting
- Accounting discuss, please expand upon and add some extra infoarrow_forwardPlease provide the solution to this financial accounting question using proper accounting principles.arrow_forwardI need help finding the accurate solution to this financial accounting problem with valid methods.arrow_forward
- Can you explain this financial accounting question using accurate calculation methods?arrow_forwardI am looking for help with this financial accounting question using proper accounting standards.arrow_forwardPlease provide the correct answer to this financial accounting problem using accurate calculations.arrow_forward
- AccountingAccountingISBN:9781337272094Author:WARREN, Carl S., Reeve, James M., Duchac, Jonathan E.Publisher:Cengage Learning,Accounting Information SystemsAccountingISBN:9781337619202Author:Hall, James A.Publisher:Cengage Learning,
- Horngren's Cost Accounting: A Managerial Emphasis...AccountingISBN:9780134475585Author:Srikant M. Datar, Madhav V. RajanPublisher:PEARSONIntermediate AccountingAccountingISBN:9781259722660Author:J. David Spiceland, Mark W. Nelson, Wayne M ThomasPublisher:McGraw-Hill EducationFinancial and Managerial AccountingAccountingISBN:9781259726705Author:John J Wild, Ken W. Shaw, Barbara Chiappetta Fundamental Accounting PrinciplesPublisher:McGraw-Hill Education
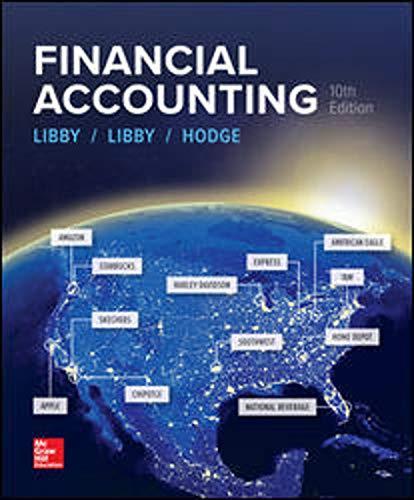
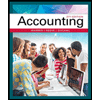
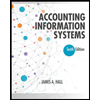
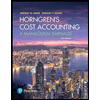
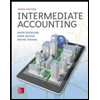
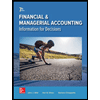