When SS Electroplating Company started the electroplating operations in a residential location in Bengaluru, it received a notice from the pollution Control Board to install the effluent treatment plant within 15 days, failing which they would seal the plant. The Director of the company collected the information that it would cost about 10,00,000 to buy an effluent treatment plant, an area of about 600 sq.feet to install it over a period of 2-3 months, & running cost of about 40,000 per month for the purchase of material like costic soda & others. The effluent contained nickel, synide, cromium, cadminum & zinc, which were to be treated separately using different chemicals. After effluent liquid of about 800 litres per day was treated, the sludge was to be dried, packed, stored & dumped in a government notified place. The entire process would not only cost substantial amount, but also would need additional area of about 600-700 sq. feet The company gathered information that some of the competitors outsourced the effluent treatment to government approved agencies, who collected the effluent liquid from these chemical & electroplating factories, & treated ( or neutralized) the chemicals at their effluent treatment plants. These agencies charged 10 to 15 per litre for the treatment of effluent liquid, depending on the type of chemicals. The cost of outsourcing was considered much higher compared to in-house effluent treatment plant. However, SS Electroplating Company, like many other chemical & electroplating factories did not have additional area for the installation of effluent treatment plant. The Director was aware that the liquid waste from the factory would have harmful effects on the surrounding residential area. He also could not violate the Government regulation on environment control. The director had very little time – two weeks – to decide & act. If you were the Director of the company, what would you do & why? Should all companies in this industry come up together as to save cost. Provide your suggestions
Critical Path Method
The critical path is the longest succession of tasks that has to be successfully completed to conclude a project entirely. The tasks involved in the sequence are called critical activities, as any task getting delayed will result in the whole project getting delayed. To determine the time duration of a project, the critical path has to be identified. The critical path method or CPM is used by project managers to evaluate the least amount of time required to finish each task with the least amount of delay.
Cost Analysis
The entire idea of cost of production or definition of production cost is applied corresponding or we can say that it is related to investment or money cost. Money cost or investment refers to any money expenditure which the firm or supplier or producer undertakes in purchasing or hiring factor of production or factor services.
Inventory Management
Inventory management is the process or system of handling all the goods that an organization owns. In simpler terms, inventory management deals with how a company orders, stores, and uses its goods.
Project Management
Project Management is all about management and optimum utilization of the resources in the best possible manner to develop the software as per the requirement of the client. Here the Project refers to the development of software to meet the end objective of the client by providing the required product or service within a specified Period of time and ensuring high quality. This can be done by managing all the available resources. In short, it can be defined as an application of knowledge, skills, tools, and techniques to meet the objective of the Project. It is the duty of a Project Manager to achieve the objective of the Project as per the specifications given by the client.
When SS Electroplating Company started the electroplating operations in a residential location in Bengaluru, it received a notice from the pollution Control Board to install the effluent treatment plant within 15 days, failing which they would seal the plant. The Director of the company collected the information that it would cost about 10,00,000 to buy an effluent treatment plant, an area of about 600 sq.feet to install it over a period of 2-3 months, & running cost of about 40,000 per month for the purchase of material like costic soda & others. The effluent contained nickel, synide, cromium, cadminum & zinc, which were to be treated separately using different chemicals. After effluent liquid of about 800 litres per day was treated, the sludge was to be dried, packed, stored & dumped in a government notified place. The entire process would not only cost substantial amount, but also would need additional area of about 600-700 sq. feet
The company gathered information that some of the competitors outsourced the effluent treatment to government approved agencies, who collected the effluent liquid from these chemical & electroplating factories, & treated ( or neutralized) the chemicals at their effluent treatment plants. These agencies charged 10 to 15 per litre for the treatment of effluent liquid, depending on the type of chemicals. The cost of outsourcing was considered much higher compared to in-house effluent treatment plant. However, SS Electroplating Company, like many other chemical & electroplating factories did not have additional area for the installation of effluent treatment plant. The Director was aware that the liquid waste from the factory would have harmful effects on the surrounding residential area. He also could not violate the Government regulation on environment control. The director had very little time – two weeks – to decide & act.
- If you were the Director of the company, what would you do & why?
- Should all companies in this industry come up together as to save cost. Provide your suggestions

Trending now
This is a popular solution!
Step by step
Solved in 3 steps

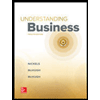
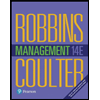
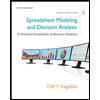
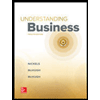
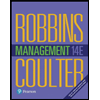
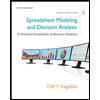
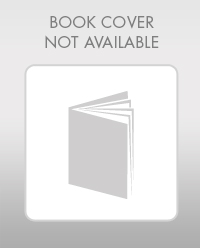
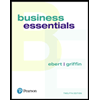
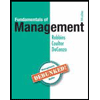