What will be the percent change in total cost per kg of product if the plant is switched from the orig design rate of 10 to the 6 power kg/year of product to a time and rate schedule which will produce 0.5x10 to the 6 power kg or half that amount of product per year at the least total cost.
A chemical processing plant has a capacity producing 1M kg of a product per year. After the plant has been put into operation, it is found that only 500,000 kg of the product can be sold per year. An analysis of the existing situation shows that all fixed and other invariant charges , which must be paid whether or not the plant is operating, amount to 35% of the total product cost when operating at full capacity. Raw material costs and other production costs that are directly proportional to the to the quantity of (i.e. constant per kg of product at any production rate) amount to 40% of the total product cost at full capacity. The remaining 25% of the total product cost is for variable overhead and miscellaneous expenses and the analysis indicates that these costs are directly proportional to the production rate during operation raised to the 1.5 power.
What will be the percent change in total cost per kg of product if the plant is switched from the orig design rate of 10 to the 6 power kg/year of product to a time and rate schedule which will produce 0.5x10 to the 6 power kg or half that amount of product per year at the least total cost.

Step by step
Solved in 2 steps with 2 images

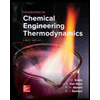
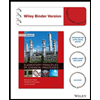
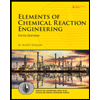
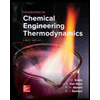
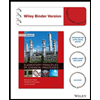
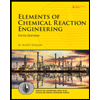
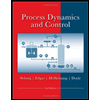
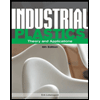
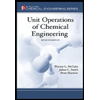