Wantanmen Corp manufactures cranes for commercial use. The company produces two models. Designated as regular and advanced. The company uses a job-order cost accounting system with manufacturing overhead applied on the basis of direct-labor hours. The system has been in place with little change for 25 years. Product costs and annual sales data are as follows: Annual Sales 20,000 1,000 Product Costs Direct Material $ 60 $ 150 Direct Labor 60 (1 hr at $60) 120 (2 hr at $60) Manufacturing Overhead* 630 (1 hr at $630) 1260 (2 hr at $630) Total Product Cost $ 750 $ 1530 *The calculation of manufacturing overhead rate, based on budgeted direct labor hour of 34,000 hours, is as follows: Manufacturing Overhead Budget: Depreciation, machinery $ 8,880,000 Maintenance, machinery $ 720,000 Depreciation, taxes, and insurance for factory $ 1,800,000 Engineering $ 2,100,000 Purchasing, receiving, and shipping $ 1,500,000 Inspection and repair of defects $ 2,250,000 Material handling $ 2,400,000 Miscellaneous manufacturing overhead cost $ 1,770,000 Total $ 21,420,000 Predetermined overhead rate = Manufacturing overhead budget/Direct labor hour budget = $21,420,000/34,000 hours = $630 per hour For the past 10 years, the company’s pricing formula has been to set each product’s target price at 115% of it’s full product cost. Recently, however, the regular-model has come under increasing price pressure from offshore competitors. The offshore competitor can sell similar product for $800. The result was that the price on the regular model has been lowered to $825. The controller proposed a change in product costing system and collected data needed to implement an activity-based costing system. The data are as follows: Table activity cost pool attached Required: Compare the new target price with the current actual selling price for regular model. Comment on the result. Explain briefly of this result and recommend a solution for Wantanmes Corp.
Process Costing
Process costing is a sort of operation costing which is employed to determine the value of a product at each process or stage of producing process, applicable where goods produced from a series of continuous operations or procedure.
Job Costing
Job costing is adhesive costs of each and every job involved in the production processes. It is an accounting measure. It is a method which determines the cost of specific jobs, which are performed according to the consumer’s specifications. Job costing is possible only in businesses where the production is done as per the customer’s requirement. For example, some customers order to manufacture furniture as per their needs.
ABC Costing
Cost Accounting is a form of managerial accounting that helps the company in assessing the total variable cost so as to compute the cost of production. Cost accounting is generally used by the management so as to ensure better decision-making. In comparison to financial accounting, cost accounting has to follow a set standard ad can be used flexibly by the management as per their needs. The types of Cost Accounting include – Lean Accounting, Standard Costing, Marginal Costing and Activity Based Costing.
Wantanmen Corp manufactures cranes for commercial use. The company produces two models. Designated as regular and advanced. The company uses a
Annual Sales | 20,000 | 1,000 | |
Product Costs | |||
Direct Material | $ 60 | $ 150 | |
Direct Labor | 60 | (1 hr at $60) | 120 (2 hr at $60) |
Manufacturing Overhead* | 630 | (1 hr at $630) | 1260 (2 hr at $630) |
Total Product Cost | $ 750 | $ 1530 |
*The calculation of manufacturing overhead rate, based on budgeted direct labor hour of 34,000 hours, is as follows:
Manufacturing Overhead Budget:
$ 8,880,000 | |
Maintenance, machinery | $ 720,000 |
Depreciation, taxes, and insurance for factory | $ 1,800,000 |
Engineering | $ 2,100,000 |
Purchasing, receiving, and shipping | $ 1,500,000 |
Inspection and repair of defects | $ 2,250,000 |
Material handling | $ 2,400,000 |
Miscellaneous |
$ 1,770,000 |
Total | $ 21,420,000 |
Predetermined overhead rate
= Manufacturing overhead budget/Direct labor hour budget
= $21,420,000/34,000 hours = $630 per hour
For the past 10 years, the company’s pricing formula has been to set each product’s target price at
115% of it’s full product cost. Recently, however, the regular-model has come under increasing price pressure from offshore competitors. The offshore competitor can sell similar product for $800. The result was that the price on the regular model has been lowered to $825.
The controller proposed a change in product costing system and collected data needed to implement an activity-based costing system. The data are as follows:
Table activity cost pool attached
Required:
-
Compare the new target price with the current actual selling price for regular model. Comment on the result.
-
Explain briefly of this result and recommend a solution for Wantanmes Corp.


Step by step
Solved in 3 steps with 4 images

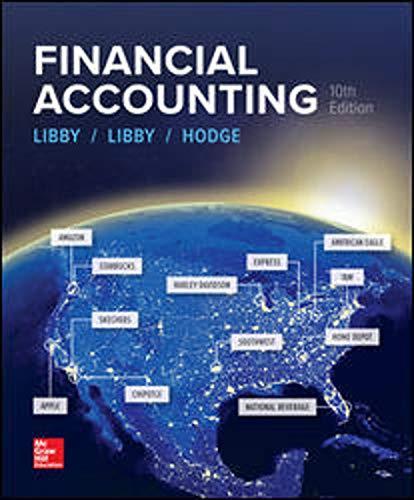
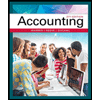
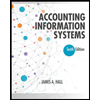
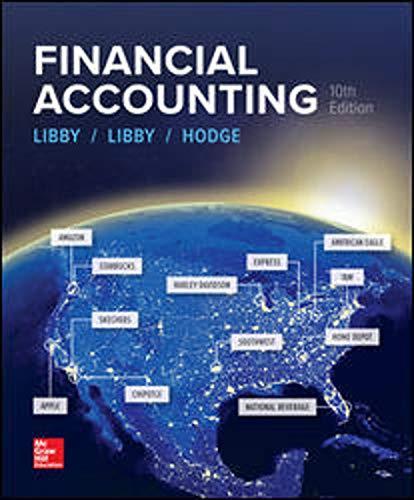
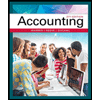
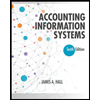
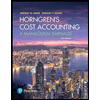
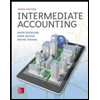
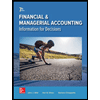