UPO Manufacturing produces a range of health care appliances for hospital as well as for home use. The company has expenenced a steady demand for as products. which are highly regarded in the health care I &id. Recently the company has undertaken a review of as memory ordering procedures as pan of a larger effort to reduce costs. One of the company's products is a blood pressure testing kit. UPD manufactures all of the components for the kit in-house except for the digital display unit The display units are ordered at six-week intervals from the supplier. This ordering system began about five years ago. because the supplier insisted on it. However, that supplier was bought out by another supplier about a year ago. and the six-week ordering requirement is no longer in place. None-theless. UPO has continued to use the six- week ordering policy. According to purchasing manager Tom Chambers. "Unless some body can give me a reason for changing. I'm going to stick with what we've been doing. I don't have time to reinvent the wheel Further discussions with Tom revealed a cost of S32 to order and recceive a shipment of display units from the supplier. The company assembles 89 kits a week. Also, information from Sara James. in Accounting. indicated a weekly carrying cost of 5.08 for each display unit. The supplier has been quite reliable with deliveries, orders are received five working days after they are faxed to the supplier. Tom indicated that as far as he was concerned, lead-time variability is virtually nonexistent Questions I. Would using an order interval other than every six weeks reduce costs? If so , what order interval would be best, and what order size would that involve ? Would you recommend changing to the optimal order interval? Explain.
UPO Manufacturing produces a range of health care appliances for hospital as well as for home use. The company has expenenced a steady demand for as products. which are highly regarded in the health care I &id. Recently the company has undertaken a review of as memory ordering procedures as pan of a larger effort to reduce costs. One of the company's products is a blood pressure testing kit. UPD manufactures all of the components for the kit in-house except for the digital display unit The display units are ordered at six-week intervals from the supplier. This ordering system began about five years ago. because the supplier insisted on it. However, that supplier was bought out by another supplier about a year ago. and the six-week ordering requirement is no longer in place. None-theless. UPO has continued to use the six- week ordering policy. According to purchasing manager Tom Chambers. "Unless some body can give me a reason for changing. I'm going to stick with what we've been doing. I don't have time to reinvent the wheel
Further discussions with Tom revealed a cost of S32 to order and recceive a shipment of display units from the supplier. The company assembles 89 kits a week. Also, information from Sara James. in Accounting. indicated a weekly carrying cost of 5.08 for each display unit. The supplier has been quite reliable with deliveries, orders are received five working days after they are faxed to the supplier. Tom indicated that as far as he was concerned, lead-time variability is virtually nonexistent
Questions I. Would using an order interval other than every six weeks reduce costs? If so , what order interval would be best, and what order size would that involve ?
- Would you recommend changing to the optimal order interval? Explain.

Trending now
This is a popular solution!
Step by step
Solved in 3 steps with 2 images

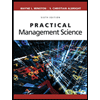
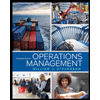
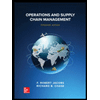
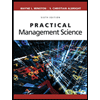
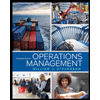
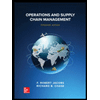
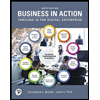
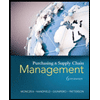
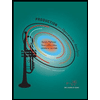