Tombro Industries is automating one of its plants and developing a flexible manufacturing system. In an effort to revise its performance measurement system, the company gathered the following data for the last four months: Quality control measures: Number of defects Number of warranty claims Number of customer complaints Material control measures: Purchase order lead time Scrap as a percent of total cost Machine performance measures: Machine downtime as a percentage of availability Use as a percentage of availability Setup time (hours) Delivery performance measures: Throughput time Manufacturing cycle efficiency (MCE) Delivery cycle time Percentage of on-time deliveries Wait time per order before start of production Inspection time per unit Process time per unit Queue time per unit Move time per unit Required 1 Required 3 Month 1 Month 2 Month 3 Month 4 Throughput Time days days 187 48 104 8.0 0.8 2.4 2.6 4.0 5.3 0.4 0.4 0.2 days days 8 days 14 5% 94% 8 Complete this question by entering your answers in the tabs below. ? Average per Month (in days) 2 3 ? ? 95% 10.8 11.0 0.7 0.7 13.0 0.7 2.1 1.6 1.0 7.6 0.7 1-a. Compute the throughput time for each month. 1-b. Compute the manufacturing cycle efficiency (MCE) for each month. 1-c. Compute the delivery cycle time for each month. Note: Round your answers to 1 decimal place. Manufacturing Cycle Efficiency (MCE) % % % % < Required 1 165 41 98 The president read in industry journals that throughput time, MCE, and delivery cycle time are important measures of performance, but no one is sure how to compute them. You have been asked to assist the company and gathered the following data: Delivery Cycle Time days days days days 7 days 1% 6% 91% 10 Required 3 > ? ? ? 94% Month Required: -a. Compute the throughput time for each month. -b. Compute the manufacturing cycle efficiency (MCE) for each month. -c. Compute the delivery cycle time for each month. 3-a. Refer to the inspection time, process time, and so forth, given for month 4. Assume in month 5 the inspection time, process time, and so forth are the same as for month 4, except the company is able to completely eliminate the queue time using Lean Production. Compute the new throughput time and MCE. 3-b. Refer to the inspection time, process time, and so forth, given for month 4. Assume in month 6 the inspection time, process time, and so forth are the same as in month 4, except the company is able to eliminate the queue time and inspection time using Lean Production. Compute the new throughput time and MCE. 126 32 81 5 days 2% 6% 88% 11 3 ? ? ? 91% 91 29 60 4 days 3% 10% 84% 12 ? ? ? 88% Show less A
Tombro Industries is automating one of its plants and developing a flexible manufacturing system. In an effort to revise its performance measurement system, the company gathered the following data for the last four months: Quality control measures: Number of defects Number of warranty claims Number of customer complaints Material control measures: Purchase order lead time Scrap as a percent of total cost Machine performance measures: Machine downtime as a percentage of availability Use as a percentage of availability Setup time (hours) Delivery performance measures: Throughput time Manufacturing cycle efficiency (MCE) Delivery cycle time Percentage of on-time deliveries Wait time per order before start of production Inspection time per unit Process time per unit Queue time per unit Move time per unit Required 1 Required 3 Month 1 Month 2 Month 3 Month 4 Throughput Time days days 187 48 104 8.0 0.8 2.4 2.6 4.0 5.3 0.4 0.4 0.2 days days 8 days 14 5% 94% 8 Complete this question by entering your answers in the tabs below. ? Average per Month (in days) 2 3 ? ? 95% 10.8 11.0 0.7 0.7 13.0 0.7 2.1 1.6 1.0 7.6 0.7 1-a. Compute the throughput time for each month. 1-b. Compute the manufacturing cycle efficiency (MCE) for each month. 1-c. Compute the delivery cycle time for each month. Note: Round your answers to 1 decimal place. Manufacturing Cycle Efficiency (MCE) % % % % < Required 1 165 41 98 The president read in industry journals that throughput time, MCE, and delivery cycle time are important measures of performance, but no one is sure how to compute them. You have been asked to assist the company and gathered the following data: Delivery Cycle Time days days days days 7 days 1% 6% 91% 10 Required 3 > ? ? ? 94% Month Required: -a. Compute the throughput time for each month. -b. Compute the manufacturing cycle efficiency (MCE) for each month. -c. Compute the delivery cycle time for each month. 3-a. Refer to the inspection time, process time, and so forth, given for month 4. Assume in month 5 the inspection time, process time, and so forth are the same as for month 4, except the company is able to completely eliminate the queue time using Lean Production. Compute the new throughput time and MCE. 3-b. Refer to the inspection time, process time, and so forth, given for month 4. Assume in month 6 the inspection time, process time, and so forth are the same as in month 4, except the company is able to eliminate the queue time and inspection time using Lean Production. Compute the new throughput time and MCE. 126 32 81 5 days 2% 6% 88% 11 3 ? ? ? 91% 91 29 60 4 days 3% 10% 84% 12 ? ? ? 88% Show less A
Chapter1: Financial Statements And Business Decisions
Section: Chapter Questions
Problem 1Q
Related questions
Question
100%
please complete entirely

Transcribed Image Text:Tombro Industries is automating one of its plants and developing a flexible manufacturing system. In an effort to revise its performance
measurement system, the company gathered the following data for the last four months:
Quality control measures:
Number of defects
Number of warranty claims
Number of customer complaints
Material control measures:
Purchase order lead time
Scrap as a percent of total cost
Machine performance measures:
Machine downtime as a percentage of availability
Use as a percentage of availability
Setup time (hours)
Delivery performance measures:
Throughput time
Manufacturing cycle efficiency (MCE)
Delivery cycle time
Percentage of on-time deliveries
Wait time per order before start of
production
Inspection time per unit
Process time per unit
Queue time per unit
Move time per unit
Required 1
2.4
2.6
0.2
Required 3
Month 1
Month 2
Month 3
Month 4
11.0
0.7
2.1 1.6
4.0 5.3
0.4
10.8
0.7
Throughput Time
days
days
days
days
187
48
104
Average per Month (in days)
1
2 3
4
8.0
Required:
1-a. Compute the throughput time for each month.
1-b. Compute the manufacturing cycle efficiency (MCE) for each month.
8 days
1%
5%
94%
8
?
?
?
95%
Complete this question by entering your answers in the tabs below.
Manufacturing Cycle
Efficiency (MCE)
%
%
%
%
1
< Required 1
1-a. Compute the throughput time for each month.
1-b. Compute the manufacturing cycle efficiency (MCE) for each month.
1-c. Compute the delivery cycle time for each month.
Note: Round your answers to 1 decimal place.
13.0
0.7
1.0
7.6
0.7
The president read in industry journals that throughput time, MCE, and delivery cycle time are important measures of performance, but
no one is sure how to compute them. You have been asked to assist the company and gathered the following data:
165
41
98
7 days
1%
6%
91%
10
Delivery Cycle Time
days
days
days
days
Required 3 >
?
?
?
94%
Month
126
32
81
5 days
2%
6%
88%
11
1-c. Compute the delivery cycle time for each month.
3-a. Refer to the inspection time, process time, and so forth, given for month 4. Assume in month 5 the inspection time, process time,
and so forth are the same as for month 4, except the company is able to completely eliminate the queue time using Lean Production.
Compute the new throughput time and MCE.
3-b. Refer to the inspection time, process time, and so forth, given for month 4. Assume in month 6 the inspection time, process time,
and so forth are the same as in month 4, except the company is able to eliminate the queue time and inspection time using Lean
Production. Compute the new throughput time and MCE.
3
?
?
?
91%
91
29
60
4 days
3%
10%
84%
12
4
?
?
?
88%
Show less A
Expert Solution

This question has been solved!
Explore an expertly crafted, step-by-step solution for a thorough understanding of key concepts.
This is a popular solution!
Trending now
This is a popular solution!
Step by step
Solved in 4 steps

Knowledge Booster
Learn more about
Need a deep-dive on the concept behind this application? Look no further. Learn more about this topic, accounting and related others by exploring similar questions and additional content below.Recommended textbooks for you
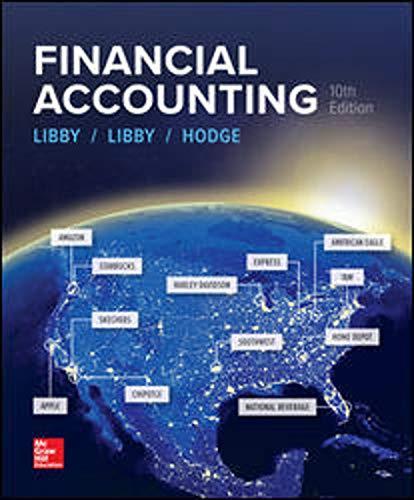
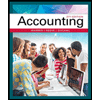
Accounting
Accounting
ISBN:
9781337272094
Author:
WARREN, Carl S., Reeve, James M., Duchac, Jonathan E.
Publisher:
Cengage Learning,
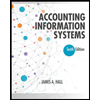
Accounting Information Systems
Accounting
ISBN:
9781337619202
Author:
Hall, James A.
Publisher:
Cengage Learning,
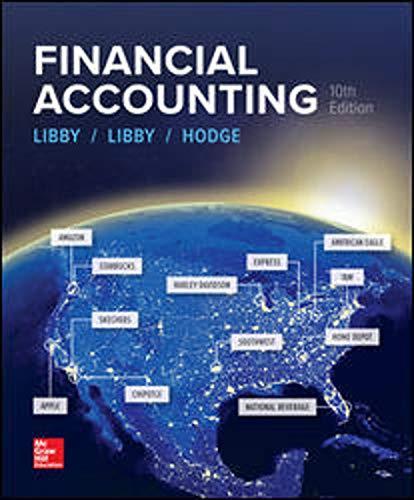
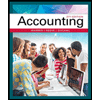
Accounting
Accounting
ISBN:
9781337272094
Author:
WARREN, Carl S., Reeve, James M., Duchac, Jonathan E.
Publisher:
Cengage Learning,
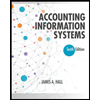
Accounting Information Systems
Accounting
ISBN:
9781337619202
Author:
Hall, James A.
Publisher:
Cengage Learning,
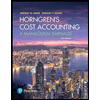
Horngren's Cost Accounting: A Managerial Emphasis…
Accounting
ISBN:
9780134475585
Author:
Srikant M. Datar, Madhav V. Rajan
Publisher:
PEARSON
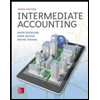
Intermediate Accounting
Accounting
ISBN:
9781259722660
Author:
J. David Spiceland, Mark W. Nelson, Wayne M Thomas
Publisher:
McGraw-Hill Education
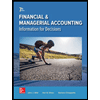
Financial and Managerial Accounting
Accounting
ISBN:
9781259726705
Author:
John J Wild, Ken W. Shaw, Barbara Chiappetta Fundamental Accounting Principles
Publisher:
McGraw-Hill Education