The production process at General Manufacturing, Inc., involves the planning, scheduling, and controlling of the physical products through the manufacturing process. General’s manufacturing process begins in the production planning and control department, where the clerk determines the materials and operations requirements based on the marketing department sales forecast and the inventory status report from the storeroom. The clerk reviews this information and prepares a hardcopy purchase requisition, which she sends to the purchasing department. From her department PC the clerk then accesses the bill of materials and route sheets files and prints the following hard copy documents: work orders, move tickets, and materials requisitions. Three copies of each document are prepared. One copy of the work order, move ticket, and materials requisitions document are sent to cost accounting. The remaining copies are sent to the work center supervisor. Upon receipt of the production control documents, the work center supervisor initiates the production process. The production employees submit a copy of the materials requisitions to the inventory storeroom in exchange for necessary raw material. When additional raw material is needed for a job in process, the storeroom clerk provides them on request. Materials in excess of those needed for production are kept in the work center and used for future production. When the job passes through all production stages and is complete, the work center supervisor sends the finished product to the finished goods warehouse. He files one copy each of the work order, move ticket, and materials requisition and sends the remaining copies of the work order and move ticket to the cost accounting department. The supervisor reviews the job tickets and the employee time cards, which he sends to cost accounting and payroll, respectively. The inventory storeroom clerk accepts materials requisitions from the work center employees and releases the raw material to the work centers. He updates the raw material inventory records from the PC and files the materials requisitions in the storeroom. At the end of the day, he creates a journal voucher and sends it to the general ledger department. The cost accounting clerk receives the following documents: work orders, move tickets, and materials requisitions from the production planning department; job tickets, work orders, and move tickets from the work center. The clerk uses these to initiate a WIP account and to update the WIP as work progresses. At the day’s end, the cost accounting clerk prepares a journal voucher reflecting the WIP status and files all documents in the department. The general ledger clerk receives the journal vouchers, posts to the appropriate GL accounts and files the journal vouchers in the department. Required Create a data flow diagram of the current system. Create a system flowchart of the existing system.
GENERAL MANUFACTURING INC.—INTERNAL CONTROLS ASSESSMENT (MANUAL SYSTEM WITH STAND ALONE PC SUPPORT)
The production process at General Manufacturing, Inc., involves the planning, scheduling, and controlling of the physical products through the manufacturing process. General’s manufacturing process begins in the production planning and control department, where the clerk determines the materials and operations requirements based on the marketing department sales
Upon receipt of the production control documents, the work center supervisor initiates the production process. The production employees submit a copy of the materials requisitions to the inventory storeroom in exchange for necessary raw material. When additional raw material is needed for a job in process, the storeroom clerk provides them on request. Materials in excess of those needed for production are kept in the work center and used for future production. When the job passes through all production stages and is complete, the work center supervisor sends the finished product to the finished goods warehouse. He files one copy each of the work order, move ticket, and materials requisition and sends the remaining copies of the work order and move ticket to the cost accounting department. The supervisor reviews the job tickets and the employee time cards, which he sends to cost accounting and payroll, respectively.
The inventory storeroom clerk accepts materials requisitions from the work center employees and releases the raw material to the work centers. He updates the raw material inventory records from the PC and files the materials requisitions in the storeroom. At the end of the day, he creates a journal voucher and sends it to the general ledger department.
The cost
The general ledger clerk receives the journal vouchers, posts to the appropriate GL accounts and files the journal vouchers in the department.
Required
- Create a data flow diagram of the current system.
- Create a system flowchart of the existing system.

Trending now
This is a popular solution!
Step by step
Solved in 2 steps with 2 images

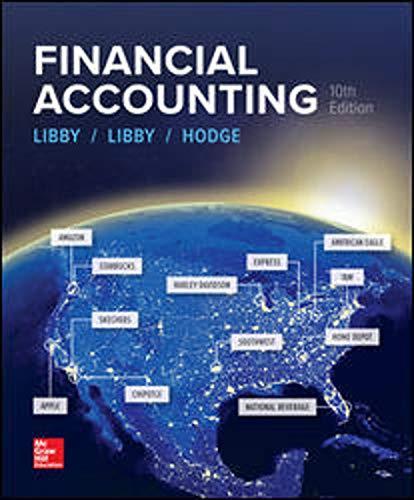
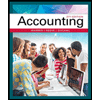
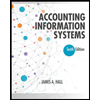
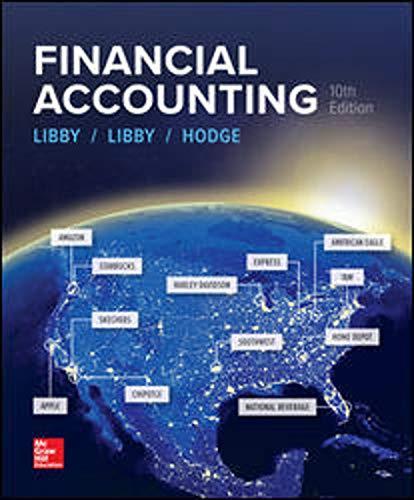
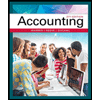
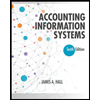
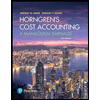
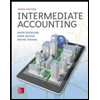
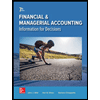