Prepare a production report for the mixing department using the weighted average method. Follow the five steps outlined in the chapter. Round unit cost to the nearest cent. If required, round final answers (except for unit cost amounts) to the nearest dollar or unit.
Process Costing
Process costing is a sort of operation costing which is employed to determine the value of a product at each process or stage of producing process, applicable where goods produced from a series of continuous operations or procedure.
Job Costing
Job costing is adhesive costs of each and every job involved in the production processes. It is an accounting measure. It is a method which determines the cost of specific jobs, which are performed according to the consumer’s specifications. Job costing is possible only in businesses where the production is done as per the customer’s requirement. For example, some customers order to manufacture furniture as per their needs.
ABC Costing
Cost Accounting is a form of managerial accounting that helps the company in assessing the total variable cost so as to compute the cost of production. Cost accounting is generally used by the management so as to ensure better decision-making. In comparison to financial accounting, cost accounting has to follow a set standard ad can be used flexibly by the management as per their needs. The types of Cost Accounting include – Lean Accounting, Standard Costing, Marginal Costing and Activity Based Costing.
Weighted Average Method, Nonuniform Inputs, Multiple Departments
Benson Pharmaceuticals uses a process-costing system to compute the unit costs of the overthe- counter cold remedies that it produces. It has three departments: mixing, encapsulating, and bottling. In mixing, the ingredients for the cold capsules are measured, sifted, and blended (with materials assumed to be uniformly added throughout the process). The mix is transferred out in gallon containers. The encapsulating department takes the powdered mix and places it in capsules (which are necessarily added at the beginning of the process). One gallon of powdered mix converts into 1,500 capsules. After the capsules are filled and polished, they are transferred to bottling, where they are placed in bottles that are then affixed with a safety seal, lid, and label. Each bottle receives 50 capsules.
During March, the following results are available for the first two departments:
Mixing | Encapsulating | ||||
Beginning inventories: | |||||
Physical units | 10 gallons | 4,000 | |||
Costs: | |||||
Materials | $252 | $32 | |||
Labor | $282 | $20 | |||
? | ? | ||||
Transferred in | $140 | ||||
Current production: | |||||
Transferred out | 140 gallons | 208,000 | |||
Ending inventory | 20 gallons | 6,000 | |||
Costs: | |||||
Materials | $3,636 | $1,573 | |||
Transferred in | — | ? | |||
Labor | $4,618 | $1,944 | |||
Overhead | ? | ? | |||
Percentage of completion: | |||||
Beginning inventory | 40% | 50% | |||
Ending inventory | 50% | 40% |
Overhead in both departments is applied as a percentage of direct labor costs. In the mixing department, overhead is 200% of direct labor. In the encapsulating department, the overhead rate is 150% of direct labor.
Required:
1. Prepare a production report for the mixing department using the weighted average method. Follow the five steps outlined in the chapter. Round unit cost to the nearest cent. If required, round final answers (except for unit cost amounts) to the nearest dollar or unit.
Benson Pharmaceuticals | |||
Mixing Department Production Report | |||
For the Month of March (Weighted Average Method) | |||
Unit Information | |||
Units to account for: | |||
Units in beginning WIP | |||
Units started | |||
Total units to account for | |||
Units accounted for: | |||
Physical Flow | Equivalent Units | ||
Units completed | |||
Units in ending WIP | |||
Total units accounted for | |||
Cost Information | |||
Costs to account for: | |||
Materials | Conversion | Total | |
Beginning WIP | $ | $ | $ |
Incurred during March | |||
Total costs to account for | $ | $ | $ |
Equivalent units | — | — | |
Cost per equivalent unit | — | — | $ |
Costs accounted for: | |||
Transferred Out | Ending Work in Process | Total | |
Goods transferred out | $ | $ | |
Ending work in process | $ | ||
Total costs to account for | $ | $ | $ |
2. Prepare a production report for the encapsulating department using the weighted average method. Follow the five steps outlined in the chapter. Round unit cost to four decimal places. If required, round final answers (except for unit cost amounts) to the nearest dollar or unit. Note: "Total costs to account for" and "Total costs to account for" would be different due to rounding.
Benson Pharmaceuticals | ||||
Encapsulating Department Production Report | ||||
For the Month of March (Weighted Average Method) | ||||
Unit Information | ||||
Units to account for: | ||||
Units in beginning WIP | ||||
Units started | ||||
Total units to account for | ||||
Units accounted for: | ||||
Equivalent Units | ||||
Physical Flow | Trans. In | Materials | Conversion | |
Units completed | ||||
Units in ending WIP | ||||
Total units accounted for | ||||
Cost Information | ||||
Costs to account for: | ||||
Trans. In | Materials | Conversion | Total | |
Beginning WIP | $ | $ | $ | $ |
Incurred during March | ||||
Total costs to account for | $ | $ | $ | $ |
Equivalent units | — | |||
Cost per equivalent unit | $ | $ | $ | $ |
Costs accounted for: | ||||
Transferred Out | Ending Work in Process | Total | ||
Goods transferred out | $ | $ | ||
Ending WIP transferred in | $ | |||
Materials | ||||
Conversion | ||||
Total costs accounted for | $ | $ | $ |

Trending now
This is a popular solution!
Step by step
Solved in 5 steps with 10 images

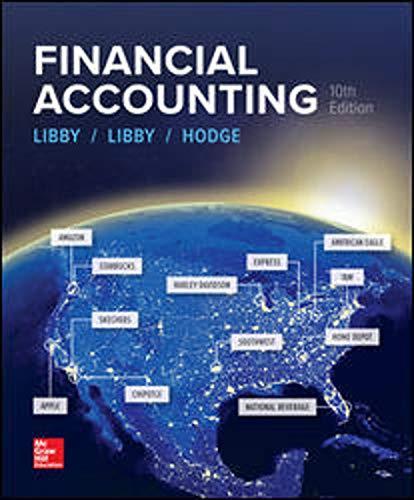
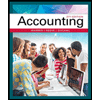
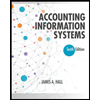
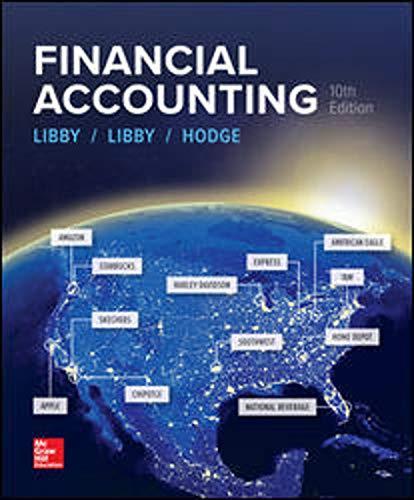
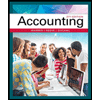
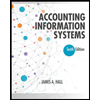
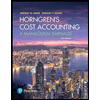
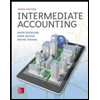
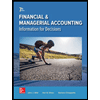