New pumper system equipment is under consideration by a Gulf Coast chemical processing plant. One crucial pump moves highly corrosive liquids from specially lined tanks on intercoastal barges into storage and preliminary refining facilities dockside. Because of the variable quality of the raw chemical and the high pressures imposed on the pump chassis and impellers, a close log is maintained on the number of hours per year that the pump operates. Safety records and pump component deterioration are considered critical control points for this system. As currently planned, rebuild and M&O cost estimates are increased accordingly when cumulative operating time reaches the 6000-hour mark. Information: You are the safety engineer at the plant. Estimates made for this pump are as follows: First cost:$800,000 Rebuild cost: $150,000 whenever 6000 cumulative hours are logged. Each rework will cost 20% more than the previous one. A maximum of three rebuilds are allowed. M&O costs: $25,000 for each year 1 through 4 $40,000 per year starting the year after the first rebuild, plus 15% per year thereafter MARR: 10% per year Year 1 - Hours per year: 500 year 2 - 1500 year 3 on - 2000Case Study Questions 1. Determine the economic service life of the pump. How does the ESL compare with the maximum allowed rebuilds?2. The plant superintendent told you, the safety engineer, that only one rebuild should be planned for, because these types of pumps usually have their minimum-cost life before the second rebuild. Determine a market value for this pump that will force the ESL to be 6 years. Comment on the practicality of ESL = 6 years, given the MV calculated.3. In a separate conversation, the line manager told you to not plan for a rebuild after 6000 hours because the pump will be replaced after a total of 10,000 hours of operation. The line manager wants to know what the base AOC in year 1 can be to make the ESL 6 years. He also told you to assume now that the 15% growth rate applies from year 1 forward. How does this base AOC value compare with the rebuild cost after 6000 hours?4. What do you think of these suggestions from the plant superintendent and the line manager?
New pumper system equipment is under consideration by a Gulf Coast chemical processing plant. One crucial pump moves highly corrosive liquids from specially lined tanks on intercoastal barges into storage and preliminary refining facilities dockside. Because of the variable quality of the raw chemical and the high pressures imposed on the pump chassis and impellers, a close log is maintained on the number of hours per year that the pump operates. Safety records and pump component deterioration are considered critical control points for this system. As currently planned, rebuild and M&O cost estimates are increased accordingly when cumulative operating time reaches the 6000-hour mark.
Information: You are the safety engineer at the plant. Estimates made for this pump are as follows:
First cost:$800,000
Rebuild cost: $150,000 whenever 6000 cumulative hours are logged. Each rework will cost 20% more than the previous one. A maximum of three rebuilds are allowed.
M&O costs: $25,000 for each year 1 through 4 $40,000 per year starting the year after the first rebuild, plus 15% per year thereafter
MARR: 10% per year
Year 1 - Hours per year: 500
year 2 - 1500 year
3 on - 2000
Case Study Questions
1. Determine the economic service life of the pump. How does the ESL compare with the maximum allowed rebuilds?
2. The plant superintendent told you, the safety engineer, that only one rebuild should be planned for, because these types of pumps usually have their minimum-cost life before the second rebuild. Determine a market value for this pump that will force the ESL to be 6 years. Comment on the practicality of ESL = 6 years, given the MV calculated.
3. In a separate conversation, the line manager told you to not plan for a rebuild after 6000 hours because the pump will be replaced after a total of 10,000 hours of operation. The line manager wants to know what the base AOC in year 1 can be to make the ESL 6 years. He also told you to assume now that the 15% growth rate applies from year 1 forward. How does this base AOC value compare with the rebuild cost after 6000 hours?
4. What do you think of these suggestions from the plant superintendent and the line manager?

Trending now
This is a popular solution!
Step by step
Solved in 1 steps

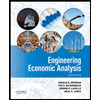
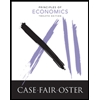
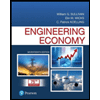
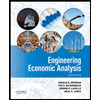
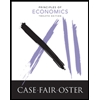
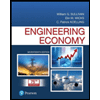
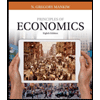
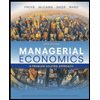
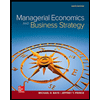