Digital Imaging (DI) produces color printers for both the professional and consumer markets. The DI consumer division recently introduced two new color printers. The DI-910 model can produce a 4”×6” borderless color print in approximately 37 seconds. The more sophisticated and faster DI-950 can even produce a 13”×19” borderless color print. Financial projections show profit contributions of $42 for each DI-910 and $87 for each DI-950. The printers are assembled, tested, and packaged at DI’s plant located in New Bern, North Carolina. This plant is highly automated and uses two manufacturing lines to produce the printers. Line 1 performs the assembly operation with times of 3 minutes per DI‑910 printer and 6 minutes per DI-950 printer. Line 2 performs both the testing and packaging operations with times of 4 minutes per DI-910 printer and 2 minutes per DI-950 printer. The shorter time for the DI-950 printer is a result of its faster print speed. Both manufacturing lines are in operation one 8-hour shift per day. Managerial Report Perform an analysis for Digital Imaging in order to determine how many units of each printer to produce. Prepare a report to DI’s president presenting your findings and recommendations. Include (but do not limit your discussion to) a consideration of the following: The recommended number of units of each printer to produce to maximize the total contribution to profit for an 8-hour shift. What reasons might management have for not implementing your recommendation? Suppose that management also states that the number of DI-910 printers produced must be at least as great as the number of DI-950 units produced. Assuming that the objective is to maximize the total contribution to profit for an 8-hour shift, how many units of each printer should be produced? Does the solution you developed in part (2) balance the total time spent on line 1 and the total time spent on line 2? Why might this balance or lack of it be a concern to management? Management requested an expansion of the model in part (2) that would provide a better balance between the total time on line 1 and the total time on line 2. Management wants to limit the difference between the total time on line 1 and the total time on line 2 to 30 minutes or less. If the objective is still to maximize the total contribution to profit, how many units of each printer should be produced? What effect does this workload balancing have on total profit in part (2)? Suppose that in part (1) management specified the objective of maximizing the total number of printers produced each shift rather than total profit contribution. With this objective, how many units of each p
Digital Imaging (DI) produces color printers for both the professional and consumer markets. The DI consumer division recently introduced two new color printers. The DI-910 model can produce a 4”×6” borderless color print in approximately 37 seconds. The more sophisticated and faster DI-950 can even produce a 13”×19” borderless color print. Financial projections show profit contributions of $42 for each DI-910 and $87 for each DI-950.
The printers are assembled, tested, and packaged at DI’s plant located in New Bern, North Carolina. This plant is highly automated and uses two manufacturing lines to produce the printers. Line 1 performs the assembly operation with times of 3 minutes per DI‑910 printer and 6 minutes per DI-950 printer. Line 2 performs both the testing and packaging operations with times of 4 minutes per DI-910 printer and 2 minutes per DI-950 printer. The shorter time for the DI-950 printer is a result of its faster print speed. Both manufacturing lines are in operation one 8-hour shift per day.
Managerial Report
Perform an analysis for Digital Imaging in order to determine how many units of each printer to produce. Prepare a report to DI’s president presenting your findings and recommendations. Include (but do not limit your discussion to) a consideration of the following:
The recommended number of units of each printer to produce to maximize the total contribution to profit for an 8-hour shift. What reasons might management have for not implementing your recommendation?
Suppose that management also states that the number of DI-910 printers produced must be at least as great as the number of DI-950 units produced. Assuming that the objective is to maximize the total contribution to profit for an 8-hour shift, how many units of each printer should be produced?
Does the solution you developed in part (2) balance the total time spent on line 1 and the total time spent on line 2? Why might this balance or lack of it be a concern to management?
Management requested an expansion of the model in part (2) that would provide a better balance between the total time on line 1 and the total time on line 2. Management wants to limit the difference between the total time on line 1 and the total time on line 2 to 30 minutes or less. If the objective is still to maximize the total contribution to profit, how many units of each printer should be produced? What effect does this workload balancing have on total profit in part (2)?
Suppose that in part (1) management specified the objective of maximizing the total number of printers produced each shift rather than total profit contribution. With this objective, how many units of each printer should be produced per shift? What effect does this objective have on total profit and workload balancing?
Develop a copy of your linear programming model and graphical solution.

Trending now
This is a popular solution!
Step by step
Solved in 6 steps with 10 images

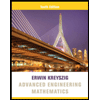
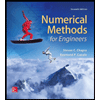
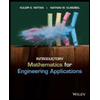
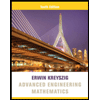
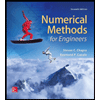
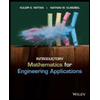
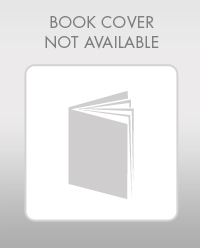
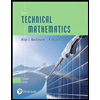
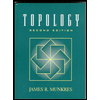