Develop a production schedule to produce the exact production requirements by varying the workforce size for the following problem. The monthly forecasts for Product X for January, February, and March are 950, 1,510, and 1,220, respectively. Safety stock policy recommends that half of the forecast for that month be defined as safety stock. There are 22 working days in January, 19 in February, and 21 in March. Beginning inventory is 550 units. Manufacturing cost is $270 per unit, storage cost is $4 per unit per month, standard pay rate is $7 per hour, overtime rate is $11 per hour, cost of stockout is $11 per unit per month, hiring and training cost is $190 per worker, layoff cost is $290 per worker, and worker productivity is 0.1 unit per hour. Assume that you start off with 40 workers and that they work 8 hours per day. (Leave no cells blank - be certain to enter "0" wherever required. Input all values as positive values. Round Workers Required up to next higher whole number. Round all other variables to nearest whole number.) January February March 950 Forecast Safety stock 1,510 755 1,220 610 755 Ⓡ Beginning inventory 475 Net production required 1790 Workers required 118 Hired 68 Laid off Actual production Ending inventory Labor Inventory Hiring Layoff Total January $ 61600 1900 0 $ 10 >> 0 475 550 875 50 Ⓒ 10 0 875 475 February $ 125,552 12920 $ 00 1790 755 10 Ⓡ 00 Total 1075 64 0 54 1075 610 March $ 75,264 O 10 >> 00 15660 O $ $
Master Budget
A master budget can be defined as an estimation of the revenue earned or expenses incurred over a specified period of time in the future and it is generally prepared on a periodic basis which can be either monthly, quarterly, half-yearly, or annually. It helps a business, an organization, or even an individual to manage the money effectively. A budget also helps in monitoring the performance of the people in the organization and helps in better decision-making.
Sales Budget and Selling
A budget is a financial plan designed by an undertaking for a definite period in future which acts as a major contributor towards enhancing the financial success of the business undertaking. The budget generally takes into account both current and future income and expenses.


Trending now
This is a popular solution!
Step by step
Solved in 2 steps with 3 images

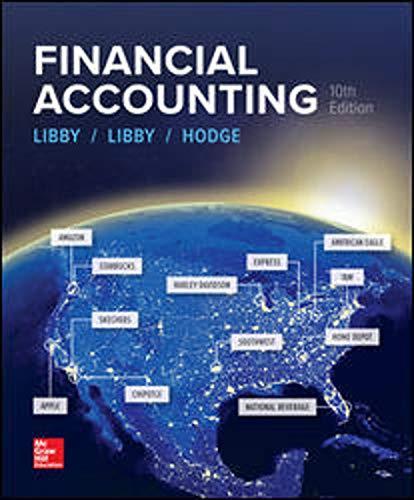
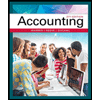
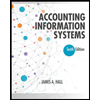
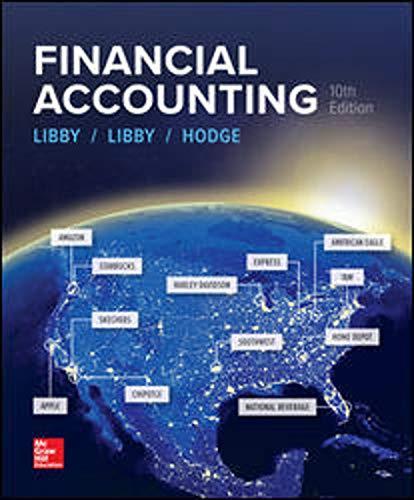
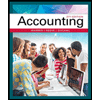
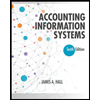
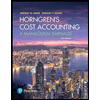
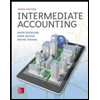
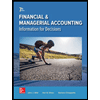