Determine the product lead time by developing a timeline from the initiation of a purchase order to product Discuss the company’s possible transportation modes and channels in China and to and within the United States, and the potential problems. Identify and discuss how international trade specialist(s), trade logistics companies, and/or Internet exchanges might help Somerset reduce its product lead time and variability
The Somerset Furniture Company was founded in 1957 in Randolph County, Virginia. It traditionally has manufactured large, medium-priced, ornate residential home wood furniture such as bedroom cabinets and chests of draws, and dining and living room cabinets, tables, and chairs, at its primary manufacturing facility in Randolph County. It employed a marketing strategy of rapidly introducing new product lines every few years. Over time it developed a reputation for high-quality, affordable furniture for a growing U.S. market of homeowners during the last half of the twentieth century. The company was generally considered to be an innovator in furniture manufacturing processes and in applying QM principles to furniture manufacturing. However, in the mid-1990s, faced with increasing foreign competition, high labor rates, and diminishing profits, the Somerset Company contracted to outsource several of its furniture product lines to manufacturers in China, simultaneously reducing the size of its own domestic manufacturing facility and labor force. This initially proved to be very successful in reducing costs and increasing profits, and by 2000 Somerset had decided to close its entire manufacturing facility in the United States and outsource all of its manufacturing to suppliers in China. The company set up a global supply chain in which it arranges for shipments of wood from the United States and South America to manufacturing plants in China where the furniture products are produced by hand by Chinese laborers. The Chinese manufacturers are very good at copying the Somerset ornate furniture designs by hand without expensive machinery. The average labor rate for furniture manufacturing in the United States is between $9 and $20 per hour, whereas the average labor rate for furniture manufacturers in China is $2 per day. Finished furniture products are shipped by container ship from Hong Kong or Shanghai to Norfolk, Virginia, where the containers are then transported by truck to Somerset warehouses in Randolph County. Somerset supplies retail furniture stores from this location. All hardware is installed on the furniture at the retail stores in order to reduce the possibility of damage during transport.
The order processing and fulfillment system for Somerset includes a great deal of variability, as does all aspects of the company’s global supply chain. The company processes order weekly and biweekly. In the United States it takes between 12 and 25 days for the company to develop a purchase order and release it to their Chinese suppliers. This process includes developing a demand
Questions:
- Determine the product lead time by developing a timeline from the initiation of a purchase order to product
- Discuss the company’s possible transportation modes and channels in China and to and within the United States, and the potential problems.
- Identify and discuss how international trade specialist(s), trade logistics companies, and/or Internet exchanges might help Somerset reduce its product lead time and variability

Trending now
This is a popular solution!
Step by step
Solved in 4 steps with 1 images

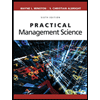
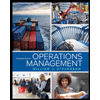
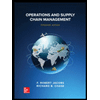
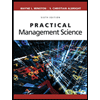
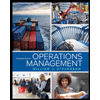
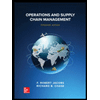
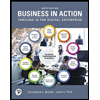
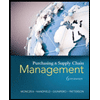
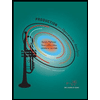