California Circuits Company (3C) manufactures a variety of components. Its Valley plant specializes in two electronic components used in circuit boards. These components serve the same function and perform equally well. The difference in the two products is the raw material. The XL-D chip is the older of the two components and is made with a metal that requires a wash prior to assembly. Originally, the plant released the wastewater directly into a local river. Several years ago, the company was ordered to treat the wastewater before its release, and it installed relatively expensive equipment. While the equipment is fully depreciated, annual operating expenses of $260,000 are still incurred for wastewater treatment. Two years ago, company scientists developed an alloy with all of the properties of the raw materials used in XL-D that generates no wastewater. Some prototype components using the new material were produced and tested and found to be indistinguishable from the old components in every way relating to their fitness for use. The only difference is that the new alloy is more expensive than the old raw material. The company has been test-marketing the newer version of the component, referred to as XL-C, and is currently trying to decide its fate. Manufacturing of both components begins in the Production Department and is completed in the Assembly Department. No other products are produced in the plant. The following provides information for the two components: XL-D XL-C Units produced 100,000 25,000 Raw material costs per unit $13.00 $15.00 Direct labor-hours per unit—Production 0.1 0.1 Direct labor-hours per unit—Assembly 0.4 0.4 Direct labor rate per hour—all labor $25.00 $25.00 Machine-hours per unit—Production 1.6 1.6 Machine-hours per unit—Assembly 0.4 0.4 Testing hours per unit (all in production) 3.0 3.0 Shipping weight per unit (pounds) 1.0 1.6 Wastewater generated per unit (gallons) 10.0 0.0 Annual overhead costs for the two departments follow: Production Department Assembly Department Supervision $ 110,000 $ 250,000 Material handling 98,000 45,000 Testing 160,000 0 Wastewater treatment 260,000 0 Depreciation on equipment 410,000 110,000 Shipping 8,000 130,000 Total $ 1,046,000 $ 535,000 The company president believes that it’s foolish to continue producing two essentially equivalent products. At the same time, the corporate image is somewhat tarnished because of a toxic dump found at another site (not the Valley plant). The president would like to be able to point to the Valley plant as an example of company research and development (R&D) working to provide an environmentally friendly product. The controller points out to the president that the company’s financial position is shaky, and it cannot afford to make products in any way other than the most cost-efficient one. Required: a. 3C’s current cost accounting system charges overhead to products based on direct labor cost using a single plantwide rate. What product costs will it report for the two products if the current allocation system is used? b. The controller recently completed an executive education course describing the two-stage allocation procedure. Assume that the first stage allocates costs to departments and the second stage allocates costs to products. The controller believes that the costs will be more accurate if machine-hours are used to allocate Production Department costs and labor-hours are used to allocate Assembly Department costs. What product costs will be reported for the two products if the two-stage allocation process is used? d. The president argues that an activity-based costing system would provide even better costs. The company decides to compute product costs assuming an ABC system is implemented only in the Production Department. Overhead in Assembly will continue to be allocated based on direct labor hours. The cost drivers selected for the activity-based costing system are as follows. Overhead Item Driver Supervision Direct labor-hours Material handling Material cost Testing Testing hours Wastewater treatment Wastewater generated Depreciation on equipment Machine-hours Shipping Weight What product costs would be reported if this ABC system were implemented? Assume that the production mix and costs would remain as originally planned.
California Circuits Company (3C) manufactures a variety of components. Its Valley plant specializes in two electronic components used in circuit boards. These components serve the same function and perform equally well. The difference in the two products is the raw material. The XL-D chip is the older of the two components and is made with a metal that requires a wash prior to assembly. Originally, the plant released the wastewater directly into a local river. Several years ago, the company was ordered to treat the wastewater before its release, and it installed relatively expensive equipment. While the equipment is fully
Two years ago, company scientists developed an alloy with all of the properties of the raw materials used in XL-D that generates no wastewater. Some prototype components using the new material were produced and tested and found to be indistinguishable from the old components in every way relating to their fitness for use. The only difference is that the new alloy is more expensive than the old raw material. The company has been test-marketing the newer version of the component, referred to as XL-C, and is currently trying to decide its fate.
Manufacturing of both components begins in the Production Department and is completed in the Assembly Department. No other products are produced in the plant. The following provides information for the two components:
XL-D | XL-C | |
Units produced | 100,000 | 25,000 |
Raw material costs per unit | $13.00 | $15.00 |
Direct labor-hours per unit—Production | 0.1 | 0.1 |
Direct labor-hours per unit—Assembly | 0.4 | 0.4 |
Direct labor rate per hour—all labor | $25.00 | $25.00 |
Machine-hours per unit—Production | 1.6 | 1.6 |
Machine-hours per unit—Assembly | 0.4 | 0.4 |
Testing hours per unit (all in production) | 3.0 | 3.0 |
Shipping weight per unit (pounds) | 1.0 | 1.6 |
Wastewater generated per unit (gallons) | 10.0 | 0.0 |
Annual
Production Department | Assembly Department | |||||
Supervision | $ | 110,000 | $ | 250,000 | ||
Material handling | 98,000 | 45,000 | ||||
Testing | 160,000 | 0 | ||||
Wastewater treatment | 260,000 | 0 | ||||
Depreciation on equipment | 410,000 | 110,000 | ||||
Shipping | 8,000 | 130,000 | ||||
Total | $ | 1,046,000 | $ | 535,000 | ||
The company president believes that it’s foolish to continue producing two essentially equivalent products. At the same time, the corporate image is somewhat tarnished because of a toxic dump found at another site (not the Valley plant). The president would like to be able to point to the Valley plant as an example of company research and development (R&D) working to provide an environmentally friendly product. The controller points out to the president that the company’s financial position is shaky, and it cannot afford to make products in any way other than the most cost-efficient one.
Required:
a. 3C’s current cost accounting system charges overhead to products based on direct labor cost using a single plantwide rate. What product costs will it report for the two products if the current allocation system is used?
b. The controller recently completed an executive education course describing the two-stage allocation procedure. Assume that the first stage allocates costs to departments and the second stage allocates costs to products. The controller believes that the costs will be more accurate if machine-hours are used to allocate Production Department costs and labor-hours are used to allocate Assembly Department costs. What product costs will be reported for the two products if the two-stage allocation process is used?
d. The president argues that an activity-based costing system would provide even better costs. The company decides to compute product costs assuming an ABC system is implemented only in the Production Department. Overhead in Assembly will continue to be allocated based on direct labor hours. The cost drivers selected for the activity-based costing system are as follows.
Overhead Item | Driver |
Supervision | Direct labor-hours |
Material handling | Material cost |
Testing | Testing hours |
Wastewater treatment | Wastewater generated |
Depreciation on equipment | Machine-hours |
Shipping | Weight |
What product costs would be reported if this ABC system were implemented? Assume that the production mix and costs would remain as originally planned.

Trending now
This is a popular solution!
Step by step
Solved in 4 steps

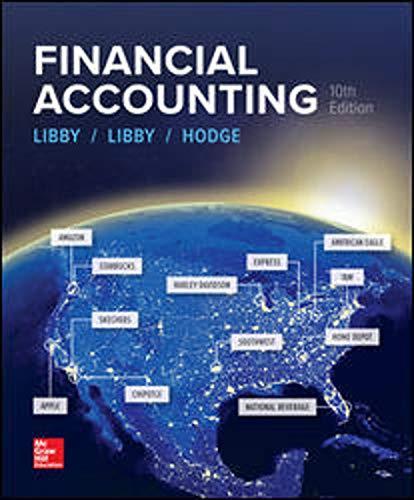
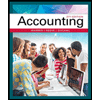
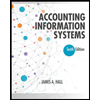
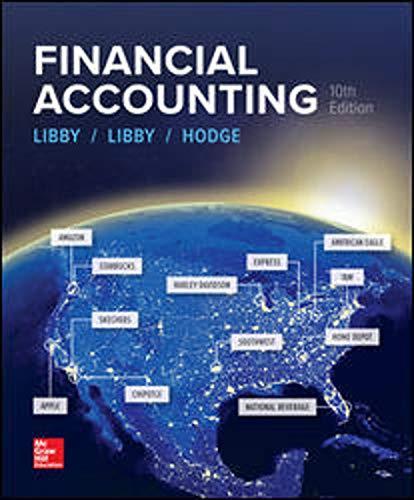
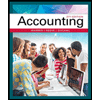
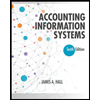
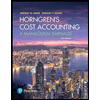
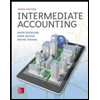
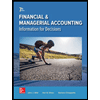