a) To minimize cost, how many units should be ordered each time an order is placed? 104.50 units (10 response to two decimal places). b) How many orders per year are needed with the optimal policy? 2.50 orders (round your response to two decimal places) What is the average inventory if costs are minimized? units (round your response to two decimal places)
a) To minimize cost, how many units should be ordered each time an order is placed? 104.50 units (10 response to two decimal places). b) How many orders per year are needed with the optimal policy? 2.50 orders (round your response to two decimal places) What is the average inventory if costs are minimized? units (round your response to two decimal places)
Practical Management Science
6th Edition
ISBN:9781337406659
Author:WINSTON, Wayne L.
Publisher:WINSTON, Wayne L.
Chapter2: Introduction To Spreadsheet Modeling
Section: Chapter Questions
Problem 20P: Julie James is opening a lemonade stand. She believes the fixed cost per week of running the stand...
Related questions
Question
100%
![**Cotteleer Electronics Inventory Management Case Study**
Cotteleer Electronics supplies microcomputer circuitry to a company that incorporates microprocessors into refrigerators and other home appliances. One of the components has an annual demand of 260 units, which remains consistent throughout the year. The carrying cost is estimated at $1.00 per unit per year, and the ordering (setup) cost is $21 per order.
**Questions:**
a) To minimize cost, how many units should be ordered each time an order is placed?
- Optimal Order Quantity: 104.50 units (rounded to two decimal places)
b) How many orders per year are needed with the optimal policy?
- Number of Orders: 2.50 orders (rounded to two decimal places)
c) What is the average inventory if costs are minimized?
- Average Inventory: [ ] units (please round your response to two decimal places)
**Discussion:**
This scenario examines the inventory management strategy using the Economic Order Quantity (EOQ) model, which aims to minimize total inventory costs. Key components of the EOQ model include demand, ordering cost, and carrying cost. The optimal order quantity is calculated to balance these costs, minimizing the total cost associated with ordering and holding inventory.
The calculation of the number of orders per year is derived by dividing the annual demand by the optimal order quantity. Average inventory is typically half of the optimal order quantity under EOQ assumptions.](/v2/_next/image?url=https%3A%2F%2Fcontent.bartleby.com%2Fqna-images%2Fquestion%2F60cc00fc-693b-4e82-b9bb-ca697f96a628%2F57eb6813-1237-4994-9a32-f9e7cfb751a1%2F1qbvnr_processed.jpeg&w=3840&q=75)
Transcribed Image Text:**Cotteleer Electronics Inventory Management Case Study**
Cotteleer Electronics supplies microcomputer circuitry to a company that incorporates microprocessors into refrigerators and other home appliances. One of the components has an annual demand of 260 units, which remains consistent throughout the year. The carrying cost is estimated at $1.00 per unit per year, and the ordering (setup) cost is $21 per order.
**Questions:**
a) To minimize cost, how many units should be ordered each time an order is placed?
- Optimal Order Quantity: 104.50 units (rounded to two decimal places)
b) How many orders per year are needed with the optimal policy?
- Number of Orders: 2.50 orders (rounded to two decimal places)
c) What is the average inventory if costs are minimized?
- Average Inventory: [ ] units (please round your response to two decimal places)
**Discussion:**
This scenario examines the inventory management strategy using the Economic Order Quantity (EOQ) model, which aims to minimize total inventory costs. Key components of the EOQ model include demand, ordering cost, and carrying cost. The optimal order quantity is calculated to balance these costs, minimizing the total cost associated with ordering and holding inventory.
The calculation of the number of orders per year is derived by dividing the annual demand by the optimal order quantity. Average inventory is typically half of the optimal order quantity under EOQ assumptions.
Expert Solution

This question has been solved!
Explore an expertly crafted, step-by-step solution for a thorough understanding of key concepts.
This is a popular solution!
Trending now
This is a popular solution!
Step by step
Solved in 3 steps

Recommended textbooks for you
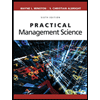
Practical Management Science
Operations Management
ISBN:
9781337406659
Author:
WINSTON, Wayne L.
Publisher:
Cengage,
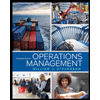
Operations Management
Operations Management
ISBN:
9781259667473
Author:
William J Stevenson
Publisher:
McGraw-Hill Education
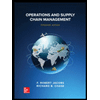
Operations and Supply Chain Management (Mcgraw-hi…
Operations Management
ISBN:
9781259666100
Author:
F. Robert Jacobs, Richard B Chase
Publisher:
McGraw-Hill Education
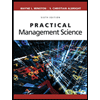
Practical Management Science
Operations Management
ISBN:
9781337406659
Author:
WINSTON, Wayne L.
Publisher:
Cengage,
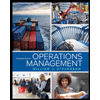
Operations Management
Operations Management
ISBN:
9781259667473
Author:
William J Stevenson
Publisher:
McGraw-Hill Education
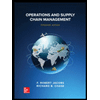
Operations and Supply Chain Management (Mcgraw-hi…
Operations Management
ISBN:
9781259666100
Author:
F. Robert Jacobs, Richard B Chase
Publisher:
McGraw-Hill Education
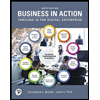
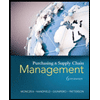
Purchasing and Supply Chain Management
Operations Management
ISBN:
9781285869681
Author:
Robert M. Monczka, Robert B. Handfield, Larry C. Giunipero, James L. Patterson
Publisher:
Cengage Learning
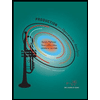
Production and Operations Analysis, Seventh Editi…
Operations Management
ISBN:
9781478623069
Author:
Steven Nahmias, Tava Lennon Olsen
Publisher:
Waveland Press, Inc.