A local company located in Nizwa assembles engines for customized trekking sport utility vehice SUV. During the year end 2019 financial review, the company is concerned with its bloated inventory cost for the past five years. The profitability of the company has been declining year on year due to the effect of the increasing inventory costs. The newly hired manager who is a mechanical engineer is tasked to look into this matter and will provide a comprehensive proposal report to the company CEO to reduce the bloating inventory cost. The current consumption or usage of parts of the assembly department is shown in Table Q1. This data shows the typical annual usage or consumption of component parts for its engines. He found out that there is big mismanagement or neglect of the company inventories. Currently, the company is ordering parts from its suppliers locally and abroad once every three months. (1) Develop an ABC analysis for the company's inventories. Show completely the results in tabular form using excel. (i) Create a PARETO analysis for the ABC analysis using excel (ili) Considering your 'class A' inventories, determine the economic order quantity EOQ using the following assumptions; zero safety stock for each class A inventories, stocking cost is 10% of the unit price, ordering cost for any class A inventories is 120 OMR per order. Determine the cost savings if EOQ is followed instead of the current ordering system of the company which is once every threel months for 'class A' inventories Table Q1: Annual Usage of Component Parts Part Number Annual quantity (unit) Unit cost (OMR/unit) 1.00 0.50 22.40 270.00 111D 128H 30,682 49,217 7,439 196G 205Y 216U 2,873 2,929 3,423 821 63,079 13,090 2.020 18,718 4,939 21,513 2,115 12.80 122.40 98.40 1.80 6.30 217J 228G 235D 249E 258L 261K 62.40 1.20 9.00 1.50 15.40 24.00 19.20 272J 324H 333C 334U 352S 391J 421A 4328 7,693 12,090 2,017 4,259 51.60 9.60 7.60 4,367 73,504 3,090 3,888 2,772 26,821 2,928 1,107 29,551 436S 0.25 13.50 452F 462R 463H 16.80 132.00 1.20 13.80 478L 5211 5320 610B 144.00 5.10
A local company located in Nizwa assembles engines for customized trekking sport utility vehice SUV. During the year end 2019 financial review, the company is concerned with its bloated inventory cost for the past five years. The profitability of the company has been declining year on year due to the effect of the increasing inventory costs. The newly hired manager who is a mechanical engineer is tasked to look into this matter and will provide a comprehensive proposal report to the company CEO to reduce the bloating inventory cost. The current consumption or usage of parts of the assembly department is shown in Table Q1. This data shows the typical annual usage or consumption of component parts for its engines. He found out that there is big mismanagement or neglect of the company inventories. Currently, the company is ordering parts from its suppliers locally and abroad once every three months. (1) Develop an ABC analysis for the company's inventories. Show completely the results in tabular form using excel. (i) Create a PARETO analysis for the ABC analysis using excel (ili) Considering your 'class A' inventories, determine the economic order quantity EOQ using the following assumptions; zero safety stock for each class A inventories, stocking cost is 10% of the unit price, ordering cost for any class A inventories is 120 OMR per order. Determine the cost savings if EOQ is followed instead of the current ordering system of the company which is once every threel months for 'class A' inventories Table Q1: Annual Usage of Component Parts Part Number Annual quantity (unit) Unit cost (OMR/unit) 1.00 0.50 22.40 270.00 111D 128H 30,682 49,217 7,439 196G 205Y 216U 2,873 2,929 3,423 821 63,079 13,090 2.020 18,718 4,939 21,513 2,115 12.80 122.40 98.40 1.80 6.30 217J 228G 235D 249E 258L 261K 62.40 1.20 9.00 1.50 15.40 24.00 19.20 272J 324H 333C 334U 352S 391J 421A 4328 7,693 12,090 2,017 4,259 51.60 9.60 7.60 4,367 73,504 3,090 3,888 2,772 26,821 2,928 1,107 29,551 436S 0.25 13.50 452F 462R 463H 16.80 132.00 1.20 13.80 478L 5211 5320 610B 144.00 5.10
Chapter1: Financial Statements And Business Decisions
Section: Chapter Questions
Problem 1Q
Related questions
Question

Transcribed Image Text:A local company located in Nizwa assembles engines for customized trekking sport utility vehice SUV.
During the year end 2019 financial review, the company is concerned with its bloated inventory cost for
the past five years. The profitability of the company has been declining year on year due to the effect of
the increasing inventory costs. The newly hired manager who is a mechanical engineer is tasked to look
into this matter and will provide a comprehensive proposal report to the company CEO to reduce the
bloating inventory cost. The current consumption or usage of parts of the assembly department is shown
in Table Q1. This data shows the typical annual usage or consumption of component parts for its
engines. He found out that there is big mismanagement or neglect of the company inventories. Currently,
the company is ordering parts from its suppliers locally and abroad once every three months.
(1) Develop an ABC analysis for the company's inventories. Show completely the results in tabular form
using excel.
(i) Create a PARETO analysis for the ABC analysis using excel
(ili) Considering your 'class A' inventories, determine the economic order quantity EOQ using the
following assumptions; zero safety stock for each class A inventories, stocking cost is 10% of the unit
price, ordering cost for any class A inventories is 120 OMR per order. Determine the cost savings if
EOQ is followed instead of the current ordering system of the company which is once every threel
months for 'class A' inventories
Table Q1: Annual Usage of Component Parts
Part Number Annual quantity (unit) Unit cost (OMR/unit)
1.00
0.50
22.40
270.00
111D
128H
30,682
49,217
7,439
196G
205Y
216U
2,873
2,929
3,423
821
63,079
13,090
2.020
18,718
4,939
21,513
2,115
12.80
122.40
98.40
1.80
6.30
217J
228G
235D
249E
258L
261K
62.40
1.20
9.00
1.50
15.40
24.00
19.20
272J
324H
333C
334U
352S
391J
421A
4328
7,693
12,090
2,017
4,259
51.60
9.60
7.60
4,367
73,504
3,090
3,888
2,772
26,821
2,928
1,107
29,551
436S
0.25
13.50
452F
462R
463H
16.80
132.00
1.20
13.80
478L
5211
5320
610B
144.00
5.10
Expert Solution

This question has been solved!
Explore an expertly crafted, step-by-step solution for a thorough understanding of key concepts.
This is a popular solution!
Trending now
This is a popular solution!
Step by step
Solved in 2 steps with 1 images

Knowledge Booster
Learn more about
Need a deep-dive on the concept behind this application? Look no further. Learn more about this topic, accounting and related others by exploring similar questions and additional content below.Recommended textbooks for you
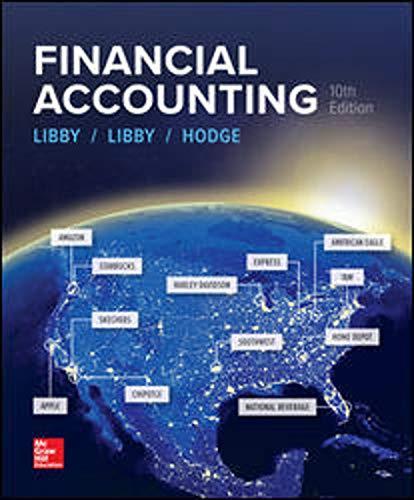
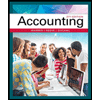
Accounting
Accounting
ISBN:
9781337272094
Author:
WARREN, Carl S., Reeve, James M., Duchac, Jonathan E.
Publisher:
Cengage Learning,
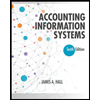
Accounting Information Systems
Accounting
ISBN:
9781337619202
Author:
Hall, James A.
Publisher:
Cengage Learning,
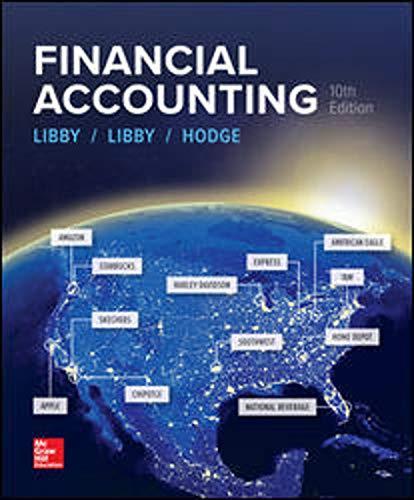
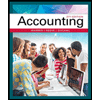
Accounting
Accounting
ISBN:
9781337272094
Author:
WARREN, Carl S., Reeve, James M., Duchac, Jonathan E.
Publisher:
Cengage Learning,
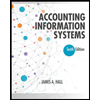
Accounting Information Systems
Accounting
ISBN:
9781337619202
Author:
Hall, James A.
Publisher:
Cengage Learning,
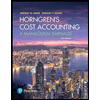
Horngren's Cost Accounting: A Managerial Emphasis…
Accounting
ISBN:
9780134475585
Author:
Srikant M. Datar, Madhav V. Rajan
Publisher:
PEARSON
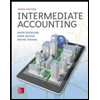
Intermediate Accounting
Accounting
ISBN:
9781259722660
Author:
J. David Spiceland, Mark W. Nelson, Wayne M Thomas
Publisher:
McGraw-Hill Education
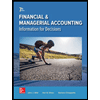
Financial and Managerial Accounting
Accounting
ISBN:
9781259726705
Author:
John J Wild, Ken W. Shaw, Barbara Chiappetta Fundamental Accounting Principles
Publisher:
McGraw-Hill Education