Engr244.Lab5.SenouciAnas
docx
keyboard_arrow_up
School
Concordia University *
*We aren’t endorsed by this school
Course
244
Subject
Mechanical Engineering
Date
Jan 9, 2024
Type
docx
Pages
14
Uploaded by mannybenka
DEFLECTION OF BEAMS
ENGR 244
Mechanics of materials
Section H-X
By
Senouci Anas
ID: 40132281
Professor: Dr. Michelle Nokken
Group members:
Senouci Anas and Rafayal Islam
Concordia University
March 30
th
2020
1
Objective:
Applying loads on simply supported beams and cantilever beams made of brass, steel and
aluminum in order to measure their deflections and finally calculate the modulus of elasticity of
each material.
Introduction:
Applying a load on a beam will cause a deflection. The amplitude of the deflection depends on
multiple factors. The location where the load is applied and the moment it creates is a factor. The
supports of the beam are another factor. The cross-section and the moment of inertia also affect
the deflection. The material and its modulus of elasticity plays also a role. In our experiment, we
are testing aluminum, steel and brass. Based on knowledge form previous experiments and the
elastic modulus of each material, I can assume that aluminum will deflect the most followed
closely by brass and finally steel, which will deflect considerably less.
Beams are the basic structural component of any building. Since under heavy loads beams bend,
it is very important to know how much they will deflect for the safety and integrity of the
structure. The bending and torsion tests are also good to calculate the modulus of elasticity.
Equipment:
Load machine
Deflection gauges
Vernier caliper
Beams of aluminum, brass and steel of rectangular cross section
2
Procedure:
1.
Simply supported beam:
-Measure the cross-sections.
-Install the beam on the supports of the load machine and make sure that the load will act on the
center of the beam.
-Place the deflection gauges at the center of the beam and at the one quarter of the length.
-Apply the load with increments of 200N until you reach 1000N.
-For each increment, note the vertical deflection at each gauge.
-Repeat the previous steps for the 2 other beams.
2.
Cantilever beam:
-Measure the cross-sections.
-Place the load hanger at the free end of the beam, under the display meter.
-Place the loads on the hanger with increments of 100g until 500g.
-For each increment, note the deflection at the free end L and at L/2
Simply-supported beams
Table 1: Width W, height H and moment of inertia I for each material
W (mm)
H (mm)
I (mm
4
)
Brass
19.10
12.72
3275
steel
19.04
12.68
3235
aluminum
19.19
12.75
3315
3
Your preview ends here
Eager to read complete document? Join bartleby learn and gain access to the full version
- Access to all documents
- Unlimited textbook solutions
- 24/7 expert homework help
Table 2: Experimental deflections
Deflection in y (m)
Brass
Steel
Aluminum
Load (N)
x=L/2
x=L/4
x= L/2
x= L/4
x= L/2
x= L/4
200
-0.00129
-0.00094
-0.00056
-0.00042
-0.00176
-0.00124
400
-0.00286
-0.00204
-0.00119
-0.00085
-0.00356
-0.00248
600
-0.00450
-0.00319
-0.00182
-0.00130
-0.00535
-0.00373
800
-0.00615
-0.00433
-0.00246
-0.00175
-0.00712
-0.00496
1000
-0.00778
-0.00547
-0.00310
-0.00220
-0.00888
-0.00620
Derivation of the elastic curve equation:
Curvature of neutral axis:
?
: radius of curvature
I: moment of inertia
E: modulus of elasticity
Mx: bending moment = load*distance x
1
ρ
=
Mx
EI
Deflection curve:
1
ρ
=
d
2
y
d x
2
(
1
+
(
dy
dx
)
2
)
3
2
It can be approximated to
1
ρ
=
d
2
y
d x
2
4
Substituting the first equation, we have
Mx
EI
=
d
2
y
d x
2
Mx
=
d
2
y
d x
2
EI
Deflection is represented by y, so in order to isolate for y we have to integrate twice.
EIy
=
∫
0
x
dx
∫
0
x
Mx dx
+
C
1
x
+
C
2
After doing the integral and finding the values for C1 and C2 with the initial conditions, we have
the following equation for the deflection:
EIy
=
−
Px
3
12
+
PL x
2
4
−
3
P L
2
x
16
+
P L
3
48
L: length of the beam
x: distance between the center of the beam and the point of application of the load P
Theoretical deflection for brass at mid-span, sample calculation:
y
=
−
P x
3
12
+
PL x
2
4
−
3
P L
2
x
16
+
P L
3
48
EI
E for brass = 105 GPa
I cross section = (1/12)WH
3
= 3275mm
4
= 3275*10
-12
m
4
5
L = 0.455m
x = 0.2275m
P = 400N
y
=
−
400
¿
0.2275
3
12
+
400
∗
0.455
∗
0.2275
2
4
−
3
∗
400
∗
0.455
2
∗
0.2275
16
+
400
∗
0.455
3
48
1.05
∗
10
11
∗
3331
∗
10
−
12
y
=−
0.002244
m
Table 3: Theoretical values of deflection for brass, steel and aluminum.
Deflection in y (m)
Brass
Steel
Aluminum
Load (N)
x=L/2
x=L/4
x=L/2
x=L/4
x=L/2
x=L/4
200
-0.001122
-0.000631
-0.000607
-0.000341
-0.001648
-0.000927
400
-0.002244
-0.001262
-0.001213
-0.000682
-0.003296
-0.001854
600
-0.003367
-0.001894
-0.001820
-0.001024
-0.004944
-0.002781
800
-0.004489
-0.002525
-0.002426
-0.001365
-0.006593
-0.003708
1000
-0.005611
-0.003156
-0.003033
-0.001706
-0.008241
-0.004635
Estimating E for each material using the experimental deflections:
Sample calculation for Brass:
P = 400N
y = -0.00327m
L = 0.2275m
x = 0.11375m
E
=
−
Px
3
12
+
PL x
2
4
−
3
P L
2
x
16
+
P L
3
48
yI
6
Your preview ends here
Eager to read complete document? Join bartleby learn and gain access to the full version
- Access to all documents
- Unlimited textbook solutions
- 24/7 expert homework help
E
=
−
400
¿
0.2275
3
12
+
400
∗
0.455
∗
0.2275
2
4
−
3
∗
400
∗
0.455
2
∗
0.2275
16
+
400
∗
0.455
3
48
−
0.00327
∗
3275
∗
10
−
12
E
=
72.06
GPa
Table 4: Estimated E for each material at x=L/2
x = 0.2275m, L = 0.455m
Brass
Steel
Aluminum
Load (N)
Deflection
(m)
E (Pa)
Deflection
(m)
E (Pa)
Deflection
(m)
E (Pa)
200
-0.00129
71846309947
-0.00056
1.78527E+11
-0.00176
6.4387E+1
0
400
-0.00286
72066023434
-0.00119
1.75863E+11
-0.00356
6.4387E+1
0
600
-0.00450
72287084855
-0.00182
1.76742E+11
-0.00535
6.4153E+1
0
800
-0.00615
72176384878
-0.00246
1.76521E+11
-0.00712
6.4830E+1
0
1000
-0.00778
71934034380
-0.00310
1.76919E+11
-0.00888
6.4599E+1
0
Average E
72061967499
Average E
1.76914E+11
Average E
6.4471E+1
0
Table 5: Estimated E vs. Theoretical E for each material
E
estimated
(GPa)
E
theoretical
(GPa)
Brass
72
105
Steel
177
200
Aluminum
64.5
70
Figure I
7
Except for Brass, the estimated values are within around 10% error compared to the theoretical
ones. The discrepancies with the values for Brass can also be seen in the following deflection
graphs.
Theoretical vs. experimental deflection at mid-span as a function of the load for each material:
Figure II
Figure III
Figure 1V
8
0
200
400
600
800
1000
1200
0
0.5
1
1.5
2
2.5
3
3.5
Steel
Experimental
Linear (Experimental)
Theoretical
Linear (Theoretical)
Load (N)
Defection (mm)
0
200
400
600
800
1000
1200
0
1
2
3
4
5
6
7
8
9
Brass
Experimental
Linear (Experimental)
Theoretical
Linear (Theoretical)
Load (N)
Deflection (mm)
0
200
400
600
800
1000
1200
0
1
2
3
4
5
6
7
8
9
10
Aluminum
Experimental
Linear (Experimental)
Theoretical
Linear (Theoretical)
Load (N)
Defection (mm)
0
200
400
600
800
1000
1200
0
1
2
3
4
5
6
7
8
9
10
Experimental Defection of Brass vs. Steel vs. Aluminum
Brass
Linear (Brass)
Steel
Linear (Steel)
Aluminum
Linear (Aluminum)
Load (N)
Defection (mm)
Cantilever beams
Table 6: Width b, height h and moment of inertia I for each material
W (mm)
H (mm)
I (mm
4
)
Brass
19.05
3.14
49.15
steel
19.01
3.51
68.50
aluminum
19.21
3.48
67.47
Table 7: Experimental deflections
Deflection in y (mm)
Brass
Steel
Aluminum
Load (N)
x=L/2
x=L
x=L/2
x=L
x=L/2
x=L
0.98
0.37
1.13
0.27
0.69
0.47
1.42
1.96
0.78
2.37
0.45
1.22
0.89
2.70
2.94
1.16
3.51
0.64
1.79
1.32
4.00
3.92
1.53
4.61
0.83
2.37
1.75
5.34
4.90
1.87
5.68
1.03
2.96
2.18
6.63
Theoretical deflection for Brass at mid-span, sample calculation:
E for brass = 105 GPa
I cross section = (1/12)WH
3
= 49.15mm
4
= 49.15*10
-12
m
4
L = 0.250m
x = 0.125m
P = 1.96N
y
=
P
(
x
3
−
3
L x
2
)
6
EI
y
=
1.96
(
0.125
3
−
3
∗
0.250
∗
0.125
2
)
6
∗
1.05
∗
10
11
∗
49.15
∗
10
−
12
9
Your preview ends here
Eager to read complete document? Join bartleby learn and gain access to the full version
- Access to all documents
- Unlimited textbook solutions
- 24/7 expert homework help
y
=
0.000618
m
Table 8: Theoretical values of deflection for brass, steel and aluminum.
Deflection in y (m)
Brass
Steel
Aluminum
Load (N)
x=0.125m
x=0.25m
0.125
0.25
0.125
0.25
0.98
0.000309093
0.000989096
0.000116427
0.000372567
0.000337727
0.001080727
1.96
0.000618185
0.001978192
0.000232854
0.000232854
0.000675455
0.002161454
2.94
0.000927278
0.002967289
0.000349281
0.000349281
0.001013182
0.003242182
3.92
0.00123637
0.003956385
0.000465709
0.000465709
0.001350909
0.004322909
4.90
0.001545463
0.004945481
0.000582136
0.000582136
0.001688636
0.005403636
Estimating E for each material using the experimental deflections:
Sample calculation for Brass:
P = 1.96N
y = 0.00078m
L = 0.250m
x = 0.125m
E
=
P
(
x
3
−
3
Lx
2
)
6
yI
E
=
1.96
(
0.125
3
−
3
∗
0.250
∗
0.125
2
)
6
∗
0.00078
∗
49.15
∗
10
−
12
E
=
83
GPa
Table 9: Estimated E for each material at x=0.125m
x = L/2
Brass
Steel
Aluminum
Load (N)
Deflection
E (Pa)
Deflection
E (Pa)
Deflection
E (Pa)
10
(m)
(m)
(m)
0.98
0.37
8.3217E+10
0.27
1.0584E+11
0.47
4.9252E+10
1.96
0.78
8.3217E+10
0.45
1.1088E+11
0.89
5.1393E+10
2.94
1.16
8.6932E+10
0.64
1.1267E+11
1.32
5.2149E+10
3.92
1.53
8.5407E+10
0.83
1.1359E+11
1.75
5.1115E+10
4.90
1.87
8.8192E+10
1.03
1.1304E+11
2.18
5.1618E+10
Average E
8.5393E+10
Average E
1.1120E+11
Average E
5.1105E+10
Table 10: Estimated E vs. Theoretical E for each material
E estimated
(GPa)
E theoretical
(GPa)
Brass
85
105
Steel
111
200
Aluminum
51
70
Theoretical vs. experimental deflection at mid-span as a function of the load for each material:
0
1
2
3
4
5
6
0
0.2
0.4
0.6
0.8
1
1.2
1.4
1.6
1.8
2
Brass
Experimental
Linear (Experimental)
Theoretical
Linear (Theoretical)
Load (N)
Defection (mm)
Figure V
11
0
1
2
3
4
5
6
0
0.2
0.4
0.6
0.8
1
1.2
Steel
Experimental
Linear (Experimental)
Theoretical
Linear (Theoretical)
Load (N)
Defection (mm)
Figure VI
0
1
2
3
4
5
6
0
0.5
1
1.5
2
2.5
Aluminum
Experimental
Linear (Experimental)
Theoretical
Linear (Theoretical)
Load (N)
Defection (mm)
Figure VII
12
Your preview ends here
Eager to read complete document? Join bartleby learn and gain access to the full version
- Access to all documents
- Unlimited textbook solutions
- 24/7 expert homework help
Discussion:
The theoretical deflections, for the most part fall in range with the experimental values. We can
note that in all the experiments the theoretical values are always lower than the experimental
ones. There are only two bigger discrepancies, for brass in the simply supported beams and for
steel in the cantilever beams. 30% error for brass and almost 100% error for steel. Since the error
for steel is so big compared to the others, it is possible that something occurred during the
experiment that could have affected the readings. Maybe because the sample wasn’t placed well
or the fatigue due to other tests could be some explanations. In general, if we compare figures 1,2
and 3 to figures 5,6 and 7 we can observe that the theoretical and experimental values are much
closer in the simply-supported beams than in the cantilever beams. The application of the load in
the cantilever experiment wasn’t as precise due to the fact that the load was hanging from the
beam and it was moving around a bit. It must be noted that for the simply supported tests, we
used ticker specimens with greater moments of inertia and we also applied a much larger load on
them, and we obtained results that were more accurate. Maybe for beam deflection experiments
it’s better to use bigger loads and ticker samples for the best results.
When we compare Table 5 to Table 10, we can again see that theoretical values of E are closer to
the experimental ones in simply supported than in cantilever. The difference in the values of E is
probably caused by material fatigue. After multiple tests, the modulus of elasticity of the
specimens decreased and it shows in our experiment. Each experimental E is lower than the
theoretical one.
Conclusion:
With the experimental data we were able to plot the graph of deflection vs. load for each material
(Figure 4) and it allows us to confirm our original assumption that aluminum will bend the most,
followed by brass and steel. This again goes in accordance with the results and conclusion of the
previous labs. Knowing how beams of different materials bend under certain loads will guide us,
engineers, in making the best decision when it comes to structural safety.
13
14
Related Documents
Related Questions
Consider the beam shown in (Eigure 1). Suppose that
w=360 N/m
Figure
Ⓒ1of1>
1 of 1
-3m
Express your answer to three significant figures and include the appropriate units
▸ View Available Hint(s)
F = 675 N
Previous Answers
✓ Correct
Correct answer is shown. Your answer 674 N was either rounded differently or used a different number of
significant figures than required for this part
Here we learn how to find a reaction force on a beam at a rocker on an inclined surface caused by an
external distributed loading, using equations of equilibrium
Part B
Determine the and y components of reaction at I using scalar notation
Express your answers in newtons to three significant figures separated by a comma.
▸ View Available Hint(s)
VAX vec
B..B,- 405,540
Submit Previous Answers
Incorrect; Try Again; 3 attempts remaining
N
arrow_forward
Could I get this question explained step for step thanks
arrow_forward
Please Provide correct solution, correct Method.
No Missing steps / calculations.
No Handwriting please
arrow_forward
15 A cantilever beam of uniform cross section and length L bears a concentrated load P at its free
end. A tensile force F also acts at the free end in the direction of the undeflected beam. By
choosing coordinates as shown in Fig. 2.9, find the equation of the deflection curve of the beam,
and the deflection of the free end relative to the fixed end.
P
(х. у)
F +
arrow_forward
Engineering Computation. Please show all work! EI=2,900,000k-in^2
arrow_forward
In order to determine the magnitude of the internal forces, a FBD must be cut.
It is difficult to determine where a cut should be made in order to reveal the Maximum Internal Forces, thus we have put the distance to the cut in terms of 'x', and plot the equation.
In my lecture we took a generic portion of a Beam and applied equilibrium and saw that Loading, Shear and Moment are related to each through differential equations. Change in Shear is the Area under the Loading diagram. Change in Moment is the Area under the Shear Diagram.
Using Graphic Integration draw the shear and moment diagrams for the given beams and loading.
arrow_forward
Beams, Shear Force and Bending
Moment in Beams
Problem#3: HOMEWORK Draw Shear Force and Moment diagram
II
100lbs
100lbs
2
1
3
5
6
Ra
Rb
arrow_forward
A propped cantilever beam is loaded by a bending moment of the magnitude MB at the point
B as shown in Figure Q1. The cross-section of the beam is a rectangle of the width w and the
hight h that are constant along the length of the beam L. The beam material's Young's
modulus is Q.
AY
O
X
Figure Q1
Assuming the positive deflections and positive vertical reaction forces are upward, calculate
the value of the reaction forces at points A and B
O the absolute value of the reaction bending moment at point A
arrow_forward
You are a structural Engineer who works in Dar Al Handasah company. Your manager has
called for a meeting and provided you with the below schematic design of a concrete beam that
might be implemented at one of the sites. You were requested to calculate the
following: (make 15 KN bold)
40
KN
15
KN
20
KN
45
30
KN
40
KN
16
20
Figure 1: Concrete Beam
1. Find the equivalent forces of the disturbed loads.
2. Sketch the beam showing all the applied forces (reaction and equivalent
forces) and allocate them into their suitable locations proper points.
3. Apply the moment equations in the equilibrium state to find the value of the reaction
forces at points A and B.
4. If the given beam in Figure 1 compressed shrank to be 19.98 meter where the
original temperature was at the given temperature T1=200 K, find the
temperature (T2) after the compression shrinking.
arrow_forward
Z5 please help on the attached question.
arrow_forward
To calculate the rotation at Point B, a suitable virtual structure needs to be created.
Which equation in the following choices most accurately represents the functional relationship between the bending moment, Mv2 ( Units: N.mm), of the virtual
structure and the spatial coordinate x (Units: mm) if the applied unit virtual moment is clockwise?
Select one:
O 1. Mv2 1.000
O 2. Mv2=x+1.000
O 3. Mv2=x+0.000
4. Mv2 = -x-1.000
O 5. Mv2 -1.000
6. Mv2=-x+0.000
arrow_forward
Hi, Could you please use moments to calculate the reaction forces of the frames in the image attached, Thank you
arrow_forward
Deform hw. Please help
arrow_forward
A
Please enter your supplied question data
(kN)
P
300 KN
Dimensions (mm)
B
65 mm
45 mm
(kNm)
M
2.5 KN
arrow_forward
SEE MORE QUESTIONS
Recommended textbooks for you
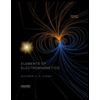
Elements Of Electromagnetics
Mechanical Engineering
ISBN:9780190698614
Author:Sadiku, Matthew N. O.
Publisher:Oxford University Press
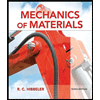
Mechanics of Materials (10th Edition)
Mechanical Engineering
ISBN:9780134319650
Author:Russell C. Hibbeler
Publisher:PEARSON
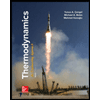
Thermodynamics: An Engineering Approach
Mechanical Engineering
ISBN:9781259822674
Author:Yunus A. Cengel Dr., Michael A. Boles
Publisher:McGraw-Hill Education
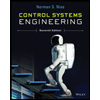
Control Systems Engineering
Mechanical Engineering
ISBN:9781118170519
Author:Norman S. Nise
Publisher:WILEY
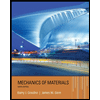
Mechanics of Materials (MindTap Course List)
Mechanical Engineering
ISBN:9781337093347
Author:Barry J. Goodno, James M. Gere
Publisher:Cengage Learning
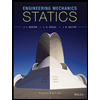
Engineering Mechanics: Statics
Mechanical Engineering
ISBN:9781118807330
Author:James L. Meriam, L. G. Kraige, J. N. Bolton
Publisher:WILEY
Related Questions
- Consider the beam shown in (Eigure 1). Suppose that w=360 N/m Figure Ⓒ1of1> 1 of 1 -3m Express your answer to three significant figures and include the appropriate units ▸ View Available Hint(s) F = 675 N Previous Answers ✓ Correct Correct answer is shown. Your answer 674 N was either rounded differently or used a different number of significant figures than required for this part Here we learn how to find a reaction force on a beam at a rocker on an inclined surface caused by an external distributed loading, using equations of equilibrium Part B Determine the and y components of reaction at I using scalar notation Express your answers in newtons to three significant figures separated by a comma. ▸ View Available Hint(s) VAX vec B..B,- 405,540 Submit Previous Answers Incorrect; Try Again; 3 attempts remaining Narrow_forwardCould I get this question explained step for step thanksarrow_forwardPlease Provide correct solution, correct Method. No Missing steps / calculations. No Handwriting pleasearrow_forward
- 15 A cantilever beam of uniform cross section and length L bears a concentrated load P at its free end. A tensile force F also acts at the free end in the direction of the undeflected beam. By choosing coordinates as shown in Fig. 2.9, find the equation of the deflection curve of the beam, and the deflection of the free end relative to the fixed end. P (х. у) F +arrow_forwardEngineering Computation. Please show all work! EI=2,900,000k-in^2arrow_forwardIn order to determine the magnitude of the internal forces, a FBD must be cut. It is difficult to determine where a cut should be made in order to reveal the Maximum Internal Forces, thus we have put the distance to the cut in terms of 'x', and plot the equation. In my lecture we took a generic portion of a Beam and applied equilibrium and saw that Loading, Shear and Moment are related to each through differential equations. Change in Shear is the Area under the Loading diagram. Change in Moment is the Area under the Shear Diagram. Using Graphic Integration draw the shear and moment diagrams for the given beams and loading.arrow_forward
- Beams, Shear Force and Bending Moment in Beams Problem#3: HOMEWORK Draw Shear Force and Moment diagram II 100lbs 100lbs 2 1 3 5 6 Ra Rbarrow_forwardA propped cantilever beam is loaded by a bending moment of the magnitude MB at the point B as shown in Figure Q1. The cross-section of the beam is a rectangle of the width w and the hight h that are constant along the length of the beam L. The beam material's Young's modulus is Q. AY O X Figure Q1 Assuming the positive deflections and positive vertical reaction forces are upward, calculate the value of the reaction forces at points A and B O the absolute value of the reaction bending moment at point Aarrow_forwardYou are a structural Engineer who works in Dar Al Handasah company. Your manager has called for a meeting and provided you with the below schematic design of a concrete beam that might be implemented at one of the sites. You were requested to calculate the following: (make 15 KN bold) 40 KN 15 KN 20 KN 45 30 KN 40 KN 16 20 Figure 1: Concrete Beam 1. Find the equivalent forces of the disturbed loads. 2. Sketch the beam showing all the applied forces (reaction and equivalent forces) and allocate them into their suitable locations proper points. 3. Apply the moment equations in the equilibrium state to find the value of the reaction forces at points A and B. 4. If the given beam in Figure 1 compressed shrank to be 19.98 meter where the original temperature was at the given temperature T1=200 K, find the temperature (T2) after the compression shrinking.arrow_forward
- Z5 please help on the attached question.arrow_forwardTo calculate the rotation at Point B, a suitable virtual structure needs to be created. Which equation in the following choices most accurately represents the functional relationship between the bending moment, Mv2 ( Units: N.mm), of the virtual structure and the spatial coordinate x (Units: mm) if the applied unit virtual moment is clockwise? Select one: O 1. Mv2 1.000 O 2. Mv2=x+1.000 O 3. Mv2=x+0.000 4. Mv2 = -x-1.000 O 5. Mv2 -1.000 6. Mv2=-x+0.000arrow_forwardHi, Could you please use moments to calculate the reaction forces of the frames in the image attached, Thank youarrow_forward
arrow_back_ios
SEE MORE QUESTIONS
arrow_forward_ios
Recommended textbooks for you
- Elements Of ElectromagneticsMechanical EngineeringISBN:9780190698614Author:Sadiku, Matthew N. O.Publisher:Oxford University PressMechanics of Materials (10th Edition)Mechanical EngineeringISBN:9780134319650Author:Russell C. HibbelerPublisher:PEARSONThermodynamics: An Engineering ApproachMechanical EngineeringISBN:9781259822674Author:Yunus A. Cengel Dr., Michael A. BolesPublisher:McGraw-Hill Education
- Control Systems EngineeringMechanical EngineeringISBN:9781118170519Author:Norman S. NisePublisher:WILEYMechanics of Materials (MindTap Course List)Mechanical EngineeringISBN:9781337093347Author:Barry J. Goodno, James M. GerePublisher:Cengage LearningEngineering Mechanics: StaticsMechanical EngineeringISBN:9781118807330Author:James L. Meriam, L. G. Kraige, J. N. BoltonPublisher:WILEY
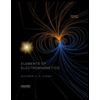
Elements Of Electromagnetics
Mechanical Engineering
ISBN:9780190698614
Author:Sadiku, Matthew N. O.
Publisher:Oxford University Press
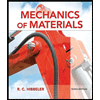
Mechanics of Materials (10th Edition)
Mechanical Engineering
ISBN:9780134319650
Author:Russell C. Hibbeler
Publisher:PEARSON
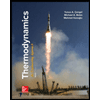
Thermodynamics: An Engineering Approach
Mechanical Engineering
ISBN:9781259822674
Author:Yunus A. Cengel Dr., Michael A. Boles
Publisher:McGraw-Hill Education
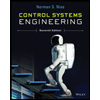
Control Systems Engineering
Mechanical Engineering
ISBN:9781118170519
Author:Norman S. Nise
Publisher:WILEY
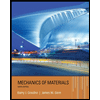
Mechanics of Materials (MindTap Course List)
Mechanical Engineering
ISBN:9781337093347
Author:Barry J. Goodno, James M. Gere
Publisher:Cengage Learning
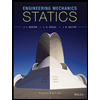
Engineering Mechanics: Statics
Mechanical Engineering
ISBN:9781118807330
Author:James L. Meriam, L. G. Kraige, J. N. Bolton
Publisher:WILEY