BOS 4025 Unit III Case Study
docx
keyboard_arrow_up
School
Columbia Southern University *
*We aren’t endorsed by this school
Course
4025
Subject
Mechanical Engineering
Date
Apr 3, 2024
Type
docx
Pages
6
Uploaded by ccomeaux
Running head: UNIT III CASE STUDY Unit III Case Study
Columbia Southern University
Welding Personal Protective Equipment (PPE) Assessment
1
UNIT III CASE STUDY
Working in a welding fabrication facility offers many PPE challenges. Due to the nature of some hazards, many of the hazards faced by the individual welder will also affect other workers in the area around the welder who may have no direct relation to the fabrication.
Using the Occupational Safety and Health Administration (OSHA) 1910 Subpart I Appendix B, Nonmandatory Compliance Guidelines for Hazard Assessment and Personal Protective Equipment Selection, we are able to review and identify sources of hazards such as; impact, compression, heat, and light, which are common with the task of welding. Once identified, employees will be protected by various means including the use of PPE. Welders are working in designated sections of the fabrication shop. General PPE requirements for all employees in the fabrication facility are hard hat, safety glasses, and steel toe safety shoes/boots. Welders will adhere to these general PPE requirements as well. While welding, the employee will be exposed to heat and light radiation due to the welding process. Welders shall utilize the correct lens shading in their hoods in accordance with the chart supplied in OSHA 1910.252(b)(2)(ii)(G), which has been added as Appendix A. Protective clothing is required to protect the welder from the heat and light radiation generated by welding. Rated welding shirts, leather welding sleeves or a leather welding jacket shall always be used while welding along with the correct gloves.
The radiant light given off by the welding process also poses a significant hazard to the employees around the designated welding area. It is not practical for all employees working around the designated welding area to be subject to the same PPE requirements as the individual welder. To protect these employees, the designated welding area should be enclosed as much as possible, using a low reflectivity paint finish on enclosures and ensuring proper ventilation 2
UNIT III CASE STUDY
(OSHA, 1910.252). Barriers can be created by using a rated transparent vinyl welding screen which is designed to block sparks and harmful ultra violate radiation from other employees. Along with the actual welding, welders are subject to other hazards using portable hand grinders. General PPE requirements are still in place, along with the use of gloves and a face shield. The welder can continue to use his welding shield as a face shield, provided that his tinted lens flips up to expose a clear lens. As required in OSHA 1910.24(c)(3), vertical portable grinders being used shall have a safety guard for protection should a grinding wheel kick back or
shatter. 3
Your preview ends here
Eager to read complete document? Join bartleby learn and gain access to the full version
- Access to all documents
- Unlimited textbook solutions
- 24/7 expert homework help
UNIT III CASE STUDY
References
Occupational Safety and Health Administration, (1970). Nonmandatory Compliance Guidelines for Hazard Assessment and Personal Protective Equipment Selection (Standard No. 1910 Subpart I, Appendix B). Retrieved from: https://www.osha.gov/laws-regs/regulations/standardnumber/1910/1910SubpartIAppB
Occupational Safety and Health Administration, (1970). Welding Cutting and Brazing (Standard
No. 1910.252). Retrieved from: https://www.osha.gov/laws-regs/regulations/standardnumber/1910/1910.252
Occupational Safety and Health Administration, (1970). Guarding of portable powered tools (Standard No. 1910.243). Retrieved from: https://www.osha.gov/pls/oshaweb/owadisp.show_document?
p_id=9850&p_table=STANDARDS
4
UNIT III CASE STUDY
APPENDIX A
1910.252(b)(2)(ii)(H)
The following is a guide for the selection of the proper shade numbers. These recommendations may be varied to suit the individual's needs.
____________________________________________________________________
|
Welding operation | Shade No.
_________________________________________________________|__________
|
Shielded metal-arc welding - 1/16-, 3/32-, 1/8-, |
5/32-inch electrodes .................................
| 10
Gas-shielded arc welding (nonferrous) - 1/16-, 3/32-, |
1/8-, 5/32-inch electrodes ..........................
| 11
Gas-shielded arc welding (ferrous) - 1/16-, 3/32-, 1/8-, |
5/32-inch electrodes .................................
| 12
Shielded metal-arc welding: |
3/16-, 7/32-, 1/4-inch electrodes ....................
| 12
5/16 -, 3/8-inch electrodes ..........................
| 14
Atomic hydrogen welding ................................
| 10-14
Carbon arc welding .....................................
| 14
Soldering ..............................................
| 2
Torch brazing ..........................................
| 3 or 4
Light cutting, up to 1 inch ............................
| 3 or 4
Medium cutting, 1 inch to 6 inches .....................
| 4 or 5
Heavy cutting, 6 inches and over .......................
| 5 or 6
Gas welding (light) up to 1/8 inch
.....................
| 4 or 5
Gas welding (medium) 1/8 inch to 1/2 inch ..............
| 5 or 6
Gas welding (heavy) 1/2 inch and over ..................
| 6 or 8
_________________________________________________________|__________
5
UNIT III CASE STUDY
NOTE: In gas welding or oxygen cutting where the torch produces a
high yellow light, it is desirable to use a filter or lens that
absorbs the yellow or sodium line in the visible light of the
operation.
6
Your preview ends here
Eager to read complete document? Join bartleby learn and gain access to the full version
- Access to all documents
- Unlimited textbook solutions
- 24/7 expert homework help
Related Documents
Related Questions
I need answers to parts 10, 11, and 12, pertaining to the print provided.
arrow_forward
I need answers to parts 1, 2, and 3, pertaining to the print provided.
arrow_forward
In GTAW the welding cable is connected to the tungsten electrode through a water-cooled copper contact tube, as shown in picture below. Why is the tube positioned near the lower end of the electrode instead of the top?
arrow_forward
Name
Part 11
1. What does the following welding symbol indicate?
100
(5)
c-d
GTAW
4. Describe the following weld(s).
ASW
2. Describe the weld(s) indicated by the following welding symbol.
d
3. Sketch in the weld(s) indicated by the welding symbol.
b-c
GMAW
000000
w
a.
C.
d.
e.
b.
b.
C.
d.
e
C.
d
a.
b.
e.
5. Sketch the welding symbol describing the following spot weld(s).
375
18 Spot, Seam, and Projection Welds 255
0.31
Copyright Goodheart-Wilcox Co., Inc. May not be reproduced or posted to a publicly accessible website
arrow_forward
1) This type of welding sequence shown in
Fig. 1 is called as :
(2)
5)
(3
Overall welding direction
Fig. 1
Stepping stone method
Symmetrical method
Backward method
O Forward method
arrow_forward
4) Which material cannot be weld using
friction stir welding process?
O Steel
O Aluminum
O Magnesium
Gold
arrow_forward
The design below is used for a bridge construction. All parts of the assembly are made of ASTM A36 steel and are welded with an E60 electrode. Under these conditions, the minimum size weld, according to table 20-4, should be:
5/16
3/16
3/8
1/4
1/2
5/8
arrow_forward
The strength in the weld zone of an age-hardening aluminium alloy is often higher than in the heat affect zone (HAZ). Which of the following is NOT a reason for this?
O The maximum temperature is higher in the weld pushing more of the hardening phase into solution.
O Particles that don't dissolve might transform into equilibrium phases instead. This is more likely in the HAZ.
O The greater dissolution of particles in the weld leads to greater solid solution strengthening.
O The increase in solute in the matrix allows more subsequent natural aging to occur in the weld zone.
O Particles in the HAZ tend to dissolve, while those in the weld coarsen. The increase in particle size and spacing reduces the strength of HAZ.
arrow_forward
SEE MORE QUESTIONS
Recommended textbooks for you
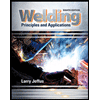
Welding: Principles and Applications (MindTap Cou...
Mechanical Engineering
ISBN:9781305494695
Author:Larry Jeffus
Publisher:Cengage Learning
Related Questions
- I need answers to parts 10, 11, and 12, pertaining to the print provided.arrow_forwardI need answers to parts 1, 2, and 3, pertaining to the print provided.arrow_forwardIn GTAW the welding cable is connected to the tungsten electrode through a water-cooled copper contact tube, as shown in picture below. Why is the tube positioned near the lower end of the electrode instead of the top?arrow_forward
- Name Part 11 1. What does the following welding symbol indicate? 100 (5) c-d GTAW 4. Describe the following weld(s). ASW 2. Describe the weld(s) indicated by the following welding symbol. d 3. Sketch in the weld(s) indicated by the welding symbol. b-c GMAW 000000 w a. C. d. e. b. b. C. d. e C. d a. b. e. 5. Sketch the welding symbol describing the following spot weld(s). 375 18 Spot, Seam, and Projection Welds 255 0.31 Copyright Goodheart-Wilcox Co., Inc. May not be reproduced or posted to a publicly accessible websitearrow_forward1) This type of welding sequence shown in Fig. 1 is called as : (2) 5) (3 Overall welding direction Fig. 1 Stepping stone method Symmetrical method Backward method O Forward methodarrow_forward4) Which material cannot be weld using friction stir welding process? O Steel O Aluminum O Magnesium Goldarrow_forward
- The design below is used for a bridge construction. All parts of the assembly are made of ASTM A36 steel and are welded with an E60 electrode. Under these conditions, the minimum size weld, according to table 20-4, should be: 5/16 3/16 3/8 1/4 1/2 5/8arrow_forwardThe strength in the weld zone of an age-hardening aluminium alloy is often higher than in the heat affect zone (HAZ). Which of the following is NOT a reason for this? O The maximum temperature is higher in the weld pushing more of the hardening phase into solution. O Particles that don't dissolve might transform into equilibrium phases instead. This is more likely in the HAZ. O The greater dissolution of particles in the weld leads to greater solid solution strengthening. O The increase in solute in the matrix allows more subsequent natural aging to occur in the weld zone. O Particles in the HAZ tend to dissolve, while those in the weld coarsen. The increase in particle size and spacing reduces the strength of HAZ.arrow_forward
arrow_back_ios
arrow_forward_ios
Recommended textbooks for you
- Welding: Principles and Applications (MindTap Cou...Mechanical EngineeringISBN:9781305494695Author:Larry JeffusPublisher:Cengage Learning
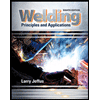
Welding: Principles and Applications (MindTap Cou...
Mechanical Engineering
ISBN:9781305494695
Author:Larry Jeffus
Publisher:Cengage Learning