ac 03
pdf
keyboard_arrow_up
School
Kaplan Business School *
*We aren’t endorsed by this school
Course
MISC
Subject
Economics
Date
Feb 20, 2024
Type
Pages
7
Uploaded by BrigadierResolveNarwhal27
@ PART THREE INFORMATION FOR MANAGING RESOURCES ~ KEY TERMS critical i “ value - 492 practical (or attainable) standarg irect labour efficiency variance 487 pure rate variance i direct labour rate variance 487 standard cost 505 direct material price variance standard cost variance 473 B (or purche.lse price variance) 484 standard costing system o irect materlal que'mtlty variance standard direct labour quantity 408 (or direct material usage variance) 484 standard labour rate 182 ] . . r?gtlneermg rr.1ethod . 479 standard material price 982 joint rate efficiency variance 505 standard material quantity 482 m . anag.ement py exception 490 statistical control chart 582 perfection (or ideal or theoretical) time and motion studies (or task %4 standards i 479 analysis or work measurement) 479 Review Questions 10.1 10.2 10.3 104 105 10.6 10.7 10.8 10.9 10.10 10.11 10.12 Provide an example that demonstrate s how the three parts of a control syst i emw use a thermostat, a budget or standard costing.) LO 10.1 ’ Pricte acnleve o Describe the two methods for settin i g standards and G explain why you would choose to use one approach overthe Explain the type of environment in i ; a service o i ; LO 10.3 rganisation that best suits the use of standard costs for control. Explai i Sta[:}gglrgocv;;?yot? could usle standard costing for control. Focus on the cost of producing car doors to illustrate ing for control. (Car doors are produced b i . y cutting sheet metal to a patte ing it i segments and welding the segments together to form the door) LO 10.1, 10.4 ¥ s i Describe how a law firm might use standard costs. LO 10.1,10.4 List i - some of the possible causes of an unfavourable direct material quantity variance. LO 10.5 a . . . . . : ) tis the meaning of the direct material price variance? What are some possible causes? LO 10.5 What mig t an unfavourable di i irect labour ef i indi i : ih bl h ‘ g |ICIellcy variance indicate? What actions could be taken to corr ct What is a statistical control chart and how can it be used? LO 10.6 Describe the factors th at managers may consider when assessi ignifi Et ng the i to assess the significance of variances? LO 10.6 i i o - . 3 i y e generally in the best position to influence the direct labour efficiency variance: 10,18 10.19 10.20 CHAPTER TEN STANDARD COSTS FOR CONTROL: DIRECT MATERIAL AND DIRECT LABOUR @ Wwhat is the meaning of the term interaction between variances? Use an example to illustrate. LO 10.8 - Real life’ titled ‘Cost pressures and variance analysis in hospitals’ in the section ‘Calculating standard cost Jariances’ explains how labour cost variances are used in a hospital. Search the internet to find another organisation that uses standard costing or variance analysis. Contrast your findings with the techniques that are described in this chapter. LO 10.8 REALLIFE Explain how participation in setting standards can sometimes lead to more accurate standards and sometimes to less accurate standards. LO 10.9 provide a hypothetical example that demonstrates how the us < to make decisions that have negative consequences. (See ‘Standard costing and behaviour’ for an e of standard costing may create incentives for manager example from the restaurant industry.) LO 10.9 Explain how and why standard costs are used in product costing. LO 10.10 Explain the difference between the traditional direct labour rate variance and a pure rate variance. (appendix) LO 10.12 Determining standard material cost: manufacturer Tahmar Valley Chemical Company manufactures industrial chemicals. The company plans to introduce a new chemical solution and needs to develop a standard product cost. The new chemical solution is made by combining a chemical compound (nyclyn) with a solution (salex), heating the mixture to boiling point, adding a second compound (protet), and bottling the resulting solution in 10-litre containers. The initial mix, which is 11 litres in volume, consists of 12 kilograms of nyclyn and 9.6 litres of salex. A 1-litre reduction in volume occurs during the boiling process. The solution is cooled slightly before 5 kilograms of protet are added. The protet evaporates, so it does not affect the total liquid volume. The purchase prices of the raw materials used in the manufacture of this new chemical solution are as follows: Nyclyn $2.90 per kilogram Salex $3.60 per litre Protet $4.80 per kilogram Required: Determine the standard material cost of a 10 litre container of the new product. E10.22 Developing standard costs: manufacturer L010.4 Search the internet to find a manufacturer’s website that outlines new products the company has recently introduced or plans to introduce. Required: Discuss the steps you think the company would go through to develop standard costs for its new product. E10.23 straightforward calculation of variances; variance diagrams: manufacturer L0O10.5 During June, Barry Ltd’s material purchases amounted to 6500 kilograms at a price of $12 per kilogram. Actual costs incurred in the production of 2000 units were as follows: ($41.25 per hour) ($12 per kilogram) $266062.50 $ 51600 Direct labour Direct material
@ PART THREE INFORMATION FOR MANAGING RESOURCES E10.24 LO10.5 E10.25 LO10.11 The standards for one unit of Barry’s product are as follows: Direct material Quantity: 2 kilograms per unit Price: $12.25 per kilogram Direct labour Quantity: 3 hours per unit Rate: $40.50 per hour Required: 1. Calculate the direct material price and quantity variances and the direct labour rate ang offi variances. Indicate whether each variance is favourable or unfavourable. ; 2. Draw diagrams depicting the direct material and direct labour variances, similar to the diagra ms in Exhibits 10.3 and 10.5. Cienw variance diagrams: manufacturer ft drink cans. A unit of production is a box of 12 cans, The ering staff and the factory accountant: Straightforward calculation of variances; Can the Can Ltd manufactures recyclable so following standards have been set by the production engine Direct labour Quantity: 0.25 hour Rate: $33 per hour Direct material Quantity: 4 kilograms Price: $0.90 per kilogram Actual material purchases amounted to 240000 kilograms at $0.93 per kilogram. Actual costs incurfeais the production of 50000 units were as follows: $195 300 for 210000 kilograms $448 500 for 13000 hours Direct material Direct labour Required: 1. Construct an Excel spreadsheet to calculate the d labour rate and efficiency variances. Indicate whe 2. Use your spreadsheet to show how the solution will direct material price is $0.885 per kilogram and standard direct labour rate is $36. irect material price and quantity variances and the difees ther each variance is favourable or unfavourablé: hange if the following information changes: Statas Journal entries under standard costing: manufacturer Refer to the data in Exercise 10.24, above. (Ignore the new data in requirement 2.) Required: 1. Prepare journal entries to record: (@) the purchase of direct materials and the direct material price variance (b) the use of direct material in production and the direct material quantity variance (c) the use of direct labour and direct labour variances (d) the closing of variances to cost of goods sold. 2. Set up ledger accounts, and post the journal entries to the general ledger. Reconstructing standard cost information from partial data: manufacturer Part of your company’s accounting database was destroyed in the recent floods that spread th town. You have been able to gather the following data from your files. rough your Direct Jabouf Direct material ] Standard quantity per unit of output ? q Standard price or rate per unit of input $8 per kilogram ] l;ourg 3 b Actual quantity used per unit of output 4 suf . 521 peri Actual price or rate per unit of input $7 per kilogram 0000 units 10000 units 1 Actual output CHAPTER TEN STANDARD COSTS FOR CONTROL: DIRECT MATERIAL AND DIRECT LA BOUR @ Direct material Direct labour Direct material price variance Direct material quantity variance 330000 F - Total of direct material variances d -2 $10000 F Direct labour rate variance - ) - $100000 F - $ 65000 F Direct labour efficiency variance Total of direct labour variances Required: Reconstruct the remaining information (wh i . ere there is a questi i i material purchased during the period was used in produc?ion B s e e g Direct material and direct labour variances: service firm Stephen Ltd is engaged in aerial s i praying of vegetables. O i . . . Operating costs are difficul fos's ' dard. cost va'rlances are reported. The following standards were d t to control, so standard maxiprotect’ spraying service. This is one of the company’s major products N e\f'Oped e £10.27 1010.5 z Standard quantity Standard price or rate Standard cost Direct material (insecticide) 8 kilograms $3.50 Direct labour -50 per kilogram 2 hours $40 per hour b 2500 Total 80.00 $108.00 1. Constru ct an Excel spreadsheet to calculate the following variances for May, favourable or unfavourable: (@) direct material price variance (b) direct material quantity variance (c) direct labour rate variance (Lcjli direct labour efficiency variance. € your spreadsheet to show how th i i i EZ; ::::j::g j?rect Iabou.r ik increaszsfigu;gg \F/)wellr ;r;ir:ge if the following information changes: y Irect material quantity decreases to 7 kilograms. Thes avanance investigation . ccountant for Lane and Com estigate vari riances. iti follow The critical and indicate whether each is E10_28 L010_6 pany uses a statistical control chart to help management decide when to : ) value is one stand iati ing d ; ard deviation from : g direct labour efficiency variances during the second half of th:;:ean- fhe companyipEi e r: July $8000 August F October 7200U S 4000 U eptember November 7800 U 5600 U December 9600 U The sty ndard dir ; t ectlabo Rat the ur cost during each of these months was $160000. The accountant has estimated rm’s monthly di . y direct labour efficiency variances have a standard deviation of $7 000.
@ PART THREE INFORMATION FOR MANAGING RESOURCES Required: 1. (a) Draw a statistical control chart and plot the variance data given above. (b) Which variances should be investigated? Explain why. 2. Suppose that the accountant’s rule of thumb is to investigate all variances equal to or greater than 5 Pey cent of standard cost. Which variances will be investigated? 3. Would you investigate any of the variances listed above other than those indicated by the rules discusSeq in requirements 1 and 27 Explain your answer. E10.29 Developing standard costs: service firm LO10.4 You have just been appointed the cost accountant for a new comnany called Amazing Joy Flights. In its firgt 10.8 few years the company will provide three types of scenic flights: ‘Over and Around Melbourne’, ‘Up the Yarrg and ‘The Surf Coast’. Each takes a different length of time, involves different flight crews and different fooq and (sometimes very expensive) beverages. Required: 1. Explain the processes that you will undertake to develop standard costs for material and labour. Make sypa that your answer is specific to the company and to the services that are being offered. 2. Outline how the company management would use these standard costs. Once again, make sure yoyr answer is specific to the particular company. E10.30 (appendix) Joint rate efficiency variance; graphing variances: manufacturer LO10.12 Refer to the data in Exercise 10.23. Calculate the pure rate variance and joint rate efficiency variance for direct labour. Draw a graph of the direct labour variances similar to the graph in Exhibit 10.11. Problems P10.31 Direct material and labour variances: manufacturer LO10.4 During January, Microchem Ltd produced 1000 units of a special product called Stylex, and the accounting 10.5 records indicated the following: Direct material purchased 36000 kilograms @ $2.76 per kilogram 19000 kilograms 4200 hours @ $36 per hour Direct material used Direct labour Stylex has the following standard prime costs: Direct material: 20 kilograms @ $2.70 per kilogram $ 54.00 Direct labour hours: 4 hours @ $34 per hour 136.00 Standard prime cost per unit $190.00 Required: 1. Calculate the total standard direct material costs and direct labour costs for January. 2. For the month of January, calculate the following variances, indicating whether each is favourable 0Of unfavourable: (a) direct material price variance (b) direct material quantity variance (c) direct labour rate variance (d) direct labour efficiency variance. P10.32 10.11 P10.33 Lo10.5 10.7 CHAPTER TEN STANDARD COSTS FOR CONTROL: DIRECT MATERIAL AND DIRECT LABOUR @ 3. Construct an Excel spreadsheet to solve requirements 1 and 2. Demonstrate how the solution will change if the following information changes: the standard direct labour rate is $40 per hour and the standard direct material price is $3 per kilogram. Direct material variances; journal entries: service firm Rural Support Ltd has been successful in gaining a major contract to prepare and deliver meals to elderly and disabled people who reside in Windsor. These operations were previously managed by the Windsor Council, and the services were outsourced by the council as a cost-saving measure. Rural Support tendered a low price, so it is very focused on cost control. The following standard prices have been established for some major food ingredients: Standard price Lamb roast $16 per kilogram Fish fillets $24 per kilogram Chips $12 per kilogram Mixed vegies $10 per kilogram & Rural Support purchases the prepared food frozen in 10 kilogram containers, and kitchen staff produce a range of standard meals. Two popular meals are the lamb dinner and the fish dinner. Fhe standard quantities used in these two meals are as follows: Lamb dinner Fish dinner Lamb roast 200 grams Fish fillets 350 grams Mixed vegies 250 grams Chips 300 grams Chips 150 grams During March, the company produced 500 lamb dinners and 800 fish dinners. Purchase and usage data for the major material ingredients during March follow: Purchases in March Used in production Qty (kg) $ per kg (kg) Lamb roast 250 16.80 105 Fish fillets 170 25.20 300 Chips 300 10.00 320 Mixed vegies 200 10.80 120 Required: 1. Calculate the total direct material quantity variance and price variances for March. . . 2. Prepare journal entries to record the purchase of material, use of material and incurrence of variances in March. Calculation of variance; analysis: service company . _ ; George Siam runs a landscaping business in a wealthy suburb of Wellington. He provides a hlgh.quallty ‘ service and focuses on the design and installation of top of the market landscaping plans that' include ! fountains, trees, paving, lighting and exotic plants. However, his clients are continually request'll.'lg .new services. Therefore, he has recently introduced a range of lawn maintenance services, i|:1clud|n9 f?ft'“satlon- | The following data relate to the first year of his landscaping service, when he serviced ‘55'cllents. EacE | client needs six applications of fertiliser during the year and was charged $40 for ?aCh application. Forl e_?fi client, two applications involve Grade A fertiliser, which contains a special ingredient for weed control. The remaining four applications are with Grade B fertiliser. |
Your preview ends here
Eager to read complete document? Join bartleby learn and gain access to the full version
- Access to all documents
- Unlimited textbook solutions
- 24/7 expert homework help
@ PART THREE INFORMATION FOR MANAGING RESOURCES P10.34 LO10.5 10.6 10.7 10.8 Based on prior knowledge of the operation and after advice from other landscapers, George following: estimae typical wage rate per employee: $27 per hour labour time per application of fertiliser: 40 minutes purchase price of fertiliser per kilogram: Grade A, $0.50; Grade B, $0.42 fertiliser usage: 40 kilograms per application. George purchased 5000 kilograms of Grade A fertiliser at $0.53 per kilogram and 1000g kil Grade B fertiliser at $0.40 per kilogram. Actual usage amounted to 3700 and 7800 kilograms, reso ‘ A new part-time employee, Fred, was hired to spread the fertiliser. George found he haq topectwe?, $34.50 per hour due to the very tight market for fertiliser specialists, and Fred worked a total of 1235 Fre; during the year. Unfortunately, George’s new service did not go smoothly, and customer complaing hou much higher than expected. S We grams Required: 1. Calculate the direct material variances for each type of fertiliser. 2. Calculate direct labour variances. 3. Calculate the total actual cost of the new service. Was it a financial success? Explain. 4. Consider the variances that you calculated in requirements 1 and 2. (a) Was the new service a success from an overall cost-control perspective? (b) What seems to have happened that gave rise to customer complaints? 5. In view of the complaints, should the fertiliser service continue to be offered next year? Why? Analysing performance and responsibility; calculating variances: manufacturer Magic Plastics uses a standard costing system to assist in the evaluation of production operationSu. company has had so many problems in recent months with suppliers and employees that they NaVEes new production supervisor, Mark Harris. Mark has been working for the company now for five monthS aReE. brought the difficult situation under control. The director of manufacturing commented: ‘Harris has really done the trick. The change to the new Mmsies suppliers and Harris’ team building skills and morale boosting activities have really made a differences These comments were made after a plant tour, where the director observed a very contented WORKISE and a review of the monthly performance reports. Included in the latest report were the following VaNSNes direct material $9240 favourable and direct labour $12 350 favourable. These variances W€ considete outstanding as they are small and they are favourable. (Magic Plastics’ budgeted material and labour COSISS usually about $700000 in total for a similar period.) Additional information: m The company purchased and consumed 45000 kilograms of direct material at $15.40 per kilograigsss paid $32.50 per hour for 20900 direct labour hours of activity. m Total units produced were 9500. m A review of the company’s standard cost records shows that each completed unit requires . of direct material at $17.60 per kilogram, and 2.6 direct labour hours at $28 per hour. 2 kilogies Required: 1. On the basis of the information contained in the performance report, should Magic Plasti be concerned about its variances? Explain why. 2. Calculate the direct material and the direct labour variances. 3. Based on your answer to requirement 2, should management be concerned about the variances 4. Are things going as smoothly as the director of manufacturing believes? Evaluate and determine whether or not the change to a new supplier and Harris’ team building @ activities appear to be working. Explain why. 5. Consider each of the variances and explain whether or not these are likely to be an outcom 7 Explaill nd mora cs manadeis S the company e poost™ .+ aclion® ¢ of Hafl= act P10.36 010.5 LAPTER TEN STANDARD COSTS FOR CONTROL: DIRECT MATERIAL AND DIRECT LABOUR @ c tandards; responsibility for variances: publishing company d Media Graphics (AMG) is a rapidly expanding company involved in the publication of teaching ._|s. Ralph Boston, owner and manager of AMG, has made a concentrated effort to provide a quality e t a fair price with delivery on the promised date. Boston is finding it increasingly difficult to supervise rocc'::)cetrztions of AMEB personally, and he is beginning to institute an organisational structure that will facilitate the maflagemen gettingd s pssociate t control. One recent changeé made was the transfer of control over departmental operations from Boston to each tmental manager. However, the quality control department still reports directly to Boston, as do the ger°’ nd accounting departments. A materials manager was hired to purchase all raw materials and to flnanc:eathe material-handling (such as receiving and storage) and record-keeping functions. The materials so responsible for maintaining an adequate inventory based on planned production levels. The loss of personal control over the operations of AMG caused Boston to look for a method of evaluati.ng performance officiently. Dave Cress, a new management accountant, proposed thc? use of a standard costing system. Variances for material and labour could then be calculated and reported directly to Boston. overs manager 1S al Required: ' 1. Assume that AMG is going to implement a standard costing system and establish standards for materials and labour. For each of these cost components, identify and discuss: - (a) which managers should be involved in setting the standards (consider each standagd separately) (b) what types of information should be considered in establishing the standards. 9 Describe the basis that should be used to assign responsibility for variances to particular managers or departments under a standard costing system. 3 |n the light of your answers to requirements 1 and 2, outline a revised reporting structure for AMG that will allow the company to evaluate and control manufacturing performance. Multiple direct labour variances: manufacturer The accountant for Lovely Manufacturing Company compares each month’s actual results with a monthly plan. The standard direct labour rates and the standard hours allowed, given the actual output in April, are shown in the following schedule: Standard direct labour rate standard direct labour hours allowed, per hour given April output Labour class T11 $36.00 1000 Labour class 11 $32.50 1000 Labour class 1 $22.50 1000 A new union contract negotiated in March resulted in actual wage rates that differed from the standard fates. The actual direct labour hours worked and the actual direct labour rates per hour for April were as follows. Actual direct labour rate per hour Actual direct labour hours Labour class I11 $38.70 1100 Labour class 11 $33.75 1300 Labour class T $24.30 750 Required: 1. Calculate the following variances for April, indicating whether each is favourable or unfavourable: (8) direct labour rate variance for each labour class b (b) direct labour efficiency variance for each labour class. . . 4 - Discuss the advantages and disadvantages of a standard costing system in which the standard direct labour rates per hour are not changed during the year to reflect events such as a new labour contract.
T — @ PART THREE INFORMATION FOR MANAGING RESOURCES P10.38 LO10.4 10.7 10.8 3. Construct an Excel spreadsheet to solve requirement 1 above. Demonstrate how the solution wjj, ch if the following information changes: the actual labour rates were $40.50, $34.35 and $25.50 fol |abnge classes IlI, Il and |, respectively. Our Variances; process costing; journal entries: manufacturer Office Magic Ltd manufactures ergonomic office equipment. The standard cost for material and laboys ¢ $190 per unit. This includes 8 kilograms of direct material at a standard cost of $5 per kilogram, and g ho i of direct labour at $25.00 per hour. The following data relate to November: "3 m work in process inventory, 1 November: none m work in process inventory, 30 November: 800 units (75 per cefit complete as to labour; material is iSsueq at the beginning of processing) units completed: 5600 units purchase of materials: 50 000 kilograms for $249250 total actual labour costs: $917 000 actual labour hours: 36 500 hours direct material quantity variance: $1500 unfavourable. Required: 1. Calculate the following amounts for November (indicate whether each variance is favourable or unfavourable): (a) direct labour rate variance (b) direct labour efficiency variance (c) actual kilograms of material used in the production process (d) actual price paid per kilogram of direct material (e) total amounts of direct material and direct labour transferred to finished goods inventory (f) the total amount of direct material and direct labour cost in the ending balance of work in process inventory. 2. Prepare journal entries to record the following: (@) purchase of raw material (b) adding direct material to work in process inventory (c) adding direct labour to work in process inventory (d) recording of variances. Development of standard costs: manufacturer ColdKing is a small producer of fruit-flavoured frozen desserts. For many years, ColdKing’s products have had strong regional sales on the basis of brand recognition. However, other companies have begun marketing similar products in the area, and price competition has become increasingly important. John Wakefield, the company’s accountant, is planning to implement a standard costing system for ColdKing and has gathered considerable information on production and material requirements for ColdKing’s products. Wakefield believes that the use of standard costing will allow ColdKing to improve cost control and make better pricing decisions: ColdKing’s most popular product is raspberry sherbet. The sherbet is produced in 40-litre batches, and each batch requires 6 kilograms of good raspberries. The fresh raspberries are sorted by hand before entering the production process. Because of imperfections in the raspberries and normal spoilage, 1 kilogram of berries is discarded for every 4 kilograms of acceptable berries. Three minutes is the standard direct labour time for the sorting required to obtain 1 kilogram of acceptable raspberries. The acceptable raspberries are then blended with the other ingredients; blending requires 12 minutes of direct labour time per batch. After blending, the sherbet is packaged in 1-litre containers. Wakefield has gathered the following information: m ColdKing purchases raspberries at a cost of $4.40 per kilogram. All other ingredients cost a total of $0.39 per litre. Thirty-four litres of the other ingredients are required per batch. m Direct labour is paid at the rate of $27 per hour. m The total cost of material and labour required to package the sherbetis $0.28 per litre. p10.39 1010.4 10.8 10.9 P10.40 LO10.8 10.9 Required: CHAPTER TEN STANDARD COSTS FOR CONTROL: DIRECT MATERIAL AND DIRECT LABOUR @ 1. Develop the standard cost of direct material and direct labour required to produce and package a 40-litre batch of raspberry sherbet. 5. For those responsible for maintaining the standards, John Wakefield is planning training in the use of variance analysis as part of the implementation of a standard costing system at ColdKing. Wakefield is particularly concerned with the causes of unfavourable variances. (a) Discuss the possible causes of unfavourable material price variances and identify the type of manager who should be held responsible for these variances. (b) Discuss the possible causes of unfavourable labour efficiency variances and identify the type of manager who should be held responsible for these variances. Development of standard costs; responsibility for variances; behavioural impact: manufacturer Zappy Kitchens manufactures a range of household products. Susan Masters, the company’s management accountant, plans to implement a standard costing system. Masters has collected information from several people in the company that will assist her in developing standards. One of Zappy’s products is a handcrafted wooden cutting board. Each cutting board requires 1 metre of timber and 20 minutes of direct labour time to prepare and cut the timber. The cutting boards are inspected after they are cut. Because the cutting boards are made of natural wood that has imperfections, one board is normally rejected for every ten that are accepted. Four rubber footpads are attachegd-to each good cutting poard. A total of 15 minutes is required to attach all four pads and to finish each cutting board. The timber for the cutting boards costs $12.25 per metre, and each footpad costs $0.08. Direct labour is paid at the rate of $37.50 per hour. Required: 1. Develop the standard cost for direct material and direct labour of one cutting board. 2. Explain the role of each of the following people in developing the standards: (@) purchasing manager (b) production manager (c) management accountant. 3. The production manager has complained that the standards are unrealistic, stifle motivation by concentrating only on unfavourable variances, and are out of date too quickly. He noted that the recent switch from sassafras to blackwood for the cutting boards has resulted in higher material costs but decreased labour hours. The net result was no increase in the total cost to produce the boards. However, the monthly cost reports continue to show an unfavourable material variance and a favourable labour variance, despite indications that the workers are slowing down. (@) Explain how a standard costing system can strengthen cost management. (b) Provide at least two explanations of why a standard costing system might negatively impact the motivation of production employees. Responsibility for variances; behavioural impacts: manufacturer Madeleine Appliances manufactures washers and dryers on a single assembly line in its main factory. The market has deteriorated over the last five years and competition has made cost control very important. Management has been concerned about the material cost of both washers and dryers. There have been no model changes in the past two years, and economic conditions have allowed the company to negotiate price reductions for many key parts. Madeleine uses a standard costing system. The price variance is the difference between the contract price and the standard price, multiplied by the actual quantity used. When a substitute part, rather than the regular part, is used in production, a price variance is calculated that is equal to the difference between the actual cost of the part used and the standard cost of the regular part. This variance is calculated at the time of substitution in the production process. The direct material quantity variance is the actual quantity used compared with the standard quantity allowed, with the difference multiplied by the standard price.
@ PART THREE INFORMATION FOR MANAGING RESOURCES P10.41 LO10.4 10.5 P10.42 LO10.6 Roberta Speck, the purchasing manager, claims that unfavourable price variances are misle says that her department has worked hard to obtain price concessions and purchase discounts fr In addition, Speck has indicated that engineering changes have been made in several parts, in prices. These price increases are not her department’s responsibility. Speck declares that P simply no longer measure the purchasing department’s performance. Jim Buddle, the manufact thinks that responsibility for the quantity variance should be shared. Buddle states that the employees cannot control quality arising from less expensive parts, substitutions of mate otherwise obsolete stock, or engineering changes that increase the quantity of materials used. ading_ Speck om Supp“ers creasing g rice varianCeS Urlng mana manufacnmng' ral to yse up % Required: Discuss the appropriateness of Madeleine’s current method of variance analysis for materials A and ingj whether the claims of Roberta Speck and Jim Buddle are valid. ndicate Standard costing; process costing; variances: manufacturer Green Ltd produces a special valve used in the burners of gas stoves. The firm uses the first-in, first- . ; out (FIF process costing method for product costing. The costs entered into work in process inventory are standafzj) costs, which are set annually. The standards for direct material and direct labour, which are based on one equivalent unit of production, are as follows: Direct material per unit 1 kilogram @ $15 per kilogram Direct labour per unit 2 hours @ $36 per hour The following data relate to the month of April: ® The beginning inventory consisted of 2 500 units, which were 100 per cent complete as to direct materia| and 40 per cent complete as to direct labour. B An additional 10 000 units were started during the month. ® The ending inventory consisted of 2000 units, which were 100 per cent complete as to direct material and 40 per cent complete as to direct labour. m Costs applicable to April production are as follows: Actual cost Standard cost Direct material purchased and used (11000 kilograms) $181500 $150000 Direct labour (25000 hours actually worked) 937500 741600 Required: s Zor Ieach element of prime production costs (direct material and direct labour), calculate the following for pril: (@) equivalent units of production (b) cost per equivalent unit of production, at actual cost and at standard cost. (Hint: It may be useful to study Chapter 5.) Prepare a schedule that calculates the following April variances, indicating whether each variance is favourable or unfavourable: (@) direct material price variance (b) direct material quantity variance (c) direct labour rate variance (d) direct labour efficiency variance. Investigating standard cost variances: manufacturer All i ; g an Ltd manufactures gardening equipment. At a recent staff meeting, the following direct labour variance eport for the past year was presented by the management accountant: P10.43 LO10.5 10.7 CHAPTER TEN STANDARD COSTS FOR CONTROL: DIRECT MATERIAL AND DIRECT LABOUR @ Allan Ltd Direct labour variance report Direct labour rate variance Direct labour efficiency variance Percentage of Percentage of Amount standard cost Amount standard cost January $1600 F 0.16 $10000 U 1.00 February 9800 F 0.98 15000 U 1.50 March 200U 0.02 19400 U 1.94 April 4000U 0.40 25600 U 2.56 May 7600 F 0.76 40200 U 4.02 June 7800 F 0.78 34000 U 3.40 July 8400 F 0.84 57000 U 5.70 August 10200 F 1.02 76000 U 7.60 September 9600 F 0.96 74000 U 7.40 October 11400 F 1.14 84000 U & 840 November 8400 F 0.84 120000 U i 12.00 December 8600 F 0.86 104000 U “ 10.40 Allan Ltd’s management accountant uses the following rule of thumb: investigate all variances equal to or greater than $60000 or 6 per cent of standard cost. Required: 1. Which variances would have been investigated during the year? (Indicate month and type of variance.) 2. What characteristics of the variance pattern shown in the report should draw the accountant’s attention, regardless of the usual investigation rule? Explain. Given these considerations, which variances would you have investigated? Why? 3. Isitimportant to follow up on favourable variances, such as those shownin the report? Explain your answer. 4. The management accountant believes that the firm’s direct labour rate variance has a normal probability distribution with a mean of zero and a standard deviation of $10000. Prepare a statistical control chart, and plot the company’s direct labour rate variances for the year. The critical value is one standard deviation. Which variances would have been investigated under this approach? Labour variances: hospital . Mountain View Hospital has adopted a standard costing system for evaluation and control of nursing labour. Diagnosis related groups (DRGs) are used as the output measure in the standard costing system. A DRG is a classification scheme for treatments, and hospitals are reimbursed by the government based on the number of patients that they treat in each DRG category. Mountain View Hospital has developed standard nursing times for the treatment of each DRG classification, and nursing labour hours are assumed to vary with the number of DRGs treated within a period. : The nursing unit on the fourth floor treats patients with four DRG classifications. The unit is staffed with registered nurses (RN), enrolled nurses (EN) and aides. The standard nursing hours and salary rates for each DRG are as follows: DRG classification RN (hours) EN (hours) Aides (hours) 1 6 4 5 2 26 16 10 3 10 5 4 4 12 7 10 Standard hourly rates $24.00 $16.00 $12.00
Your preview ends here
Eager to read complete document? Join bartleby learn and gain access to the full version
- Access to all documents
- Unlimited textbook solutions
- 24/7 expert homework help
@ PART THREE INFORMATION FOR MANAGING RESOURCES P10.44 LO10.5 For the month of May, the number of patients and hourly rates for the fourth floor nursing ynjg 3 e follows: Actual number of patients DRG 1 250 DRG 2 90 DRG 3 240 DRG 4 140 Total \ E RN EN Aides Actual salary $200490 $70520 $50600 + Actual hours 8 150 4300 44& Actual hourly rate $ 24.60 $ 1640 $\& The accountant for Mountain View Hospital calculated the following standard times for the fourth floof nursing unit for May: Total standard hours DRG Number of Standard hours per patient classification patients RN EN Aides RN EN Aides 1 250 6 4 5 1500 1000 1250 2 90 26 16 10 2340 1440 900 3 240 10 5 4 2400 1200 960 4 140 12 7 10 1680 980 1400 Total @ fl 4510 The hospital calculates labour variances for each reporting period by labour classification (RN, EN and Aide). The variances are used by nursing supervisors and hospital administrators to evaluate the performance of nursing labour. The variances are calculated as follows: m A total nursing labour variance equal to the difference between the total actual nursing cost and the total standard nursing cost. m A nursing labour efficiency variance, calculated as the sum of the efficiency variances across the three types of nursing labour. - m A nursing labour rate variance, calculated as the sum of the rate variances across the three types nursing labour. Required: 1. Calculate the hospital’s nursing labour variances for May. - ) rsind 2 Comment on the nursing labour efficiency variance. Does this variance tell the whole story about N4 efficiency? ce: 3 5 3 jances (appendix) Direct material and direct labour variances; graphical analysis of direct labour vafi manufacturer following During July, Nemo Ltd manufactured 500 units of a special multilayer fabric called Everflex. The 10.12 jnformation from the Everflex production department pertains to July: 87200 Direct material purchased: 18 000 metres @ $10.40 per metre 3 3500 Direct material used: 9500 metres @ $10.40 per metre 96 560 7 Direct labour: 2 100 hours @ $36.60 per hour €10.45 1010.4 10.5 10.7 10.11 CHAPTER TEN STANDARD COSTS FOR CONTROL: DIRECT MATERIAL AND DIRECT LABOUR q;’ The standard prime costs for one unit of Everflex are as follows: Direct materials: 20 metres @ $10 per metre poy: Direct labour: 4 hours @ $38 per hour - Total standard prime cost per unit of output ——$352 Required: 1 Calculate the following variances for the month of July, indicating whether each variance is favourable or unfavourable: (a) direct material price variance (b) direct material quantity variance (c) direct labour rate variance (d) direct labour efficiency variance. Draw a graph depicting Nemo’s direct labour variances for July. Include the joint rate efficiency variance in your graph. (See Exhibit 10.11 for guidance.) Provide an interpretation of the variances that are revealed in the graph. e Direct material and direct labour variances; job costing; journal entries: manufacturer Business Wear Fashions manufactures one type of women’s jacket, produced in jobs to fill each customer order. These jackets are supplied to various department stores, and Business Wear sews the label of each store onto the jackets. During November, Business Wear worked on three orders. The job cost records disclose the following data: Job no. No. jackets Total material used (metres) Total hours worked AB 2000 8200 5960 CD 3400 - 13000 10260 MN 2400 10100 5780 The following additional information is available: B Business Wear purchased 90 000 metres of material during November at a cost of $990 000. ® Directlabour during November amounted to $660 000. According to payroll records, production employees were paid $30 per hour. B There was no work in process on 1 November. During November, jobs AB and CD were completed. All material was issued for job MN, which was 80 per cent complete as to direct labour. B The standard costs for a jacket are as follows: Direct material 4 metres @ $10.00 $ 40.00 Direct labour 3 hours @ $29.00 §7.00 Manufacturing overhead 3 hours @ $18.00 54.00 Standard cost per jacket $181.00
Related Documents
Recommended textbooks for you
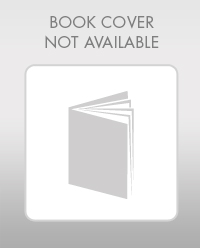
Exploring Economics
Economics
ISBN:9781544336329
Author:Robert L. Sexton
Publisher:SAGE Publications, Inc
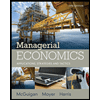
Managerial Economics: Applications, Strategies an...
Economics
ISBN:9781305506381
Author:James R. McGuigan, R. Charles Moyer, Frederick H.deB. Harris
Publisher:Cengage Learning
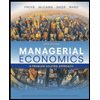
Managerial Economics: A Problem Solving Approach
Economics
ISBN:9781337106665
Author:Luke M. Froeb, Brian T. McCann, Michael R. Ward, Mike Shor
Publisher:Cengage Learning
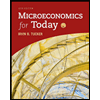
Recommended textbooks for you
- Exploring EconomicsEconomicsISBN:9781544336329Author:Robert L. SextonPublisher:SAGE Publications, IncManagerial Economics: Applications, Strategies an...EconomicsISBN:9781305506381Author:James R. McGuigan, R. Charles Moyer, Frederick H.deB. HarrisPublisher:Cengage Learning
- Managerial Economics: A Problem Solving ApproachEconomicsISBN:9781337106665Author:Luke M. Froeb, Brian T. McCann, Michael R. Ward, Mike ShorPublisher:Cengage Learning
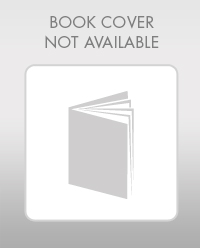
Exploring Economics
Economics
ISBN:9781544336329
Author:Robert L. Sexton
Publisher:SAGE Publications, Inc
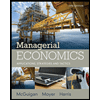
Managerial Economics: Applications, Strategies an...
Economics
ISBN:9781305506381
Author:James R. McGuigan, R. Charles Moyer, Frederick H.deB. Harris
Publisher:Cengage Learning
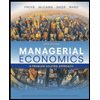
Managerial Economics: A Problem Solving Approach
Economics
ISBN:9781337106665
Author:Luke M. Froeb, Brian T. McCann, Michael R. Ward, Mike Shor
Publisher:Cengage Learning
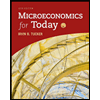