Prac Report 1 COMPLETE NO SHEETS
docx
keyboard_arrow_up
School
Queensland University of Technology *
*We aren’t endorsed by this school
Course
270
Subject
Civil Engineering
Date
Oct 30, 2023
Type
docx
Pages
22
Uploaded by DoctorWillpower16387
Your preview ends here
Eager to read complete document? Join bartleby learn and gain access to the full version
- Access to all documents
- Unlimited textbook solutions
- 24/7 expert homework help
Your preview ends here
Eager to read complete document? Join bartleby learn and gain access to the full version
- Access to all documents
- Unlimited textbook solutions
- 24/7 expert homework help
Your preview ends here
Eager to read complete document? Join bartleby learn and gain access to the full version
- Access to all documents
- Unlimited textbook solutions
- 24/7 expert homework help
Your preview ends here
Eager to read complete document? Join bartleby learn and gain access to the full version
- Access to all documents
- Unlimited textbook solutions
- 24/7 expert homework help
Your preview ends here
Eager to read complete document? Join bartleby learn and gain access to the full version
- Access to all documents
- Unlimited textbook solutions
- 24/7 expert homework help
Your preview ends here
Eager to read complete document? Join bartleby learn and gain access to the full version
- Access to all documents
- Unlimited textbook solutions
- 24/7 expert homework help
Your preview ends here
Eager to read complete document? Join bartleby learn and gain access to the full version
- Access to all documents
- Unlimited textbook solutions
- 24/7 expert homework help
Your preview ends here
Eager to read complete document? Join bartleby learn and gain access to the full version
- Access to all documents
- Unlimited textbook solutions
- 24/7 expert homework help
Recommended textbooks for you
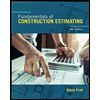
Fundamentals Of Construction Estimating
Civil Engineering
ISBN:9781337399395
Author:Pratt, David J.
Publisher:Cengage,
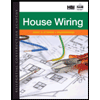
Residential Construction Academy: House Wiring (M...
Civil Engineering
ISBN:9781285852225
Author:Gregory W Fletcher
Publisher:Cengage Learning
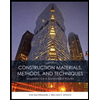
Construction Materials, Methods and Techniques (M...
Civil Engineering
ISBN:9781305086272
Author:William P. Spence, Eva Kultermann
Publisher:Cengage Learning
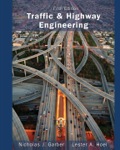
Traffic and Highway Engineering
Civil Engineering
ISBN:9781305156241
Author:Garber, Nicholas J.
Publisher:Cengage Learning
Recommended textbooks for you
- Fundamentals Of Construction EstimatingCivil EngineeringISBN:9781337399395Author:Pratt, David J.Publisher:Cengage,Residential Construction Academy: House Wiring (M...Civil EngineeringISBN:9781285852225Author:Gregory W FletcherPublisher:Cengage LearningConstruction Materials, Methods and Techniques (M...Civil EngineeringISBN:9781305086272Author:William P. Spence, Eva KultermannPublisher:Cengage Learning
- Traffic and Highway EngineeringCivil EngineeringISBN:9781305156241Author:Garber, Nicholas J.Publisher:Cengage Learning
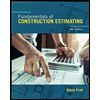
Fundamentals Of Construction Estimating
Civil Engineering
ISBN:9781337399395
Author:Pratt, David J.
Publisher:Cengage,
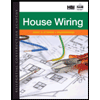
Residential Construction Academy: House Wiring (M...
Civil Engineering
ISBN:9781285852225
Author:Gregory W Fletcher
Publisher:Cengage Learning
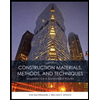
Construction Materials, Methods and Techniques (M...
Civil Engineering
ISBN:9781305086272
Author:William P. Spence, Eva Kultermann
Publisher:Cengage Learning
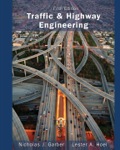
Traffic and Highway Engineering
Civil Engineering
ISBN:9781305156241
Author:Garber, Nicholas J.
Publisher:Cengage Learning
Browse Popular Homework Q&A
Q: On January 1, 20X3, Parade Corporation reported total assets of $473,000, liabilities of $271,000,…
Q: A pair of complex-conjugate poles in the s-plane is required to meet the various specifications
that…
Q: I need help with a biology question on enzyme denaturation, I need help with questions, one and two,…
Q: ICA 7-A
Spooled
t test
4 individuals were tested in the
Memory test in the congruent
condition &…
Q: Amoxycillin is often adminisstered as the sodium salt. It is more soluble form that results from the…
Q: y. A manometer is attached to a conduit, as show
the figure. Calculate
the gauge pressure inside the…
Q: DETAILS SERPSE10 19.2.OP.004.
A brass calorimeter cup with a specific heat of 380 1/(kg- °C)…
Q: -3/2
Calculate the integral of f(x, y) = (x² + y²)¯² over the region x² + y° 2 by changing to polar…
Q: An individual or group of individual professionals who assist management in the workout process is…
Q: Note that 5% of the population suffers from a
particular disease. There is a diagnostic test to…
Q: Consider the following cdf of the random variable Y. F (y) = 0 < y < 4.
3²
16
Calculate P (2y < 3).…
Q: Supply the missing constant, k, so that the resulting trinomial is a perfect square. Then factor the…
Q: 1.4.20. A person answers each of two multiple choice questions at random. If there
are four possible…
Q: 5. Suppose that we have an infinite string, and that we know the initial
position and velocity of…
Q: A 5.00 g bullet is fired horizontally at a speed of 190 m/s into a 1.00 kg wooden block resting on a…
Q: Write a trigger to put the total sale order amount before tax
(unit price * quantity for all items…
Q: The kinetic energy (T) of an object with mass m traveling at a speed v is defined as T =…
Q: Document D
Source: Adam Smith, An Inquiry into the Nature and Causes of the
Wealth of Nations (1776)…
Q: 11) Which of these statements is true of fermentation?
a) It converts lactic acid into acetyl CoA
b)…
Q: What was the long-term impact of the Crusades on Western Europe?
Q: Desk purchased July 12 for $2,000; 8-year useful life; $600 salvage value. Calculate MACRS…
Q: Find the indefinite integral. Check your result by differentiating. (Use C for the constant of…
Q: Excedrin headache pain relief extra strength also contains 65 mg of caffeine, C8H10N4O2. How many…
Q: hat will be your first step to generating a busine
Q: Pizza Corporation purchased 100 percent of the common stock of Slice Corporation on January 1, 20X2,…