MalikFProject2
docx
keyboard_arrow_up
School
Southern New Hampshire University *
*We aren’t endorsed by this school
Course
830
Subject
Business
Date
Feb 20, 2024
Type
docx
Pages
10
Uploaded by fmalik89
BUSI830 Project2 1
School of Business, Liberty University
Faizan Malik
Discussion Thread: Solutions that Incorporate Lean Six Sigma
By submitting this assignment, I attest this submission represents my work, and not that of another student, scholar, or internet source. I understand I am responsible for knowing and correctly utilizing referencing and bibliographical guidelines. I have not submitted this work for any other class.
BUSI830 Project2 2
Abstract
In many industries, the convergence of Six Sigma and Lean Thinking methodologies has gained traction as organizations strive to optimize internal processes and minimize wastage to enhance efficiency and achieve superior business outcomes. This has given rise to Lean Six Sigma, a robust framework that empowers organizations to elevate operational efficiency and product quality, ultimately delivering enhanced value to their customers. While these methodologies share intertwined principles, they also exhibit distinct advantages, equipping organizations with tools to streamline workflows and enhance experiences for stakeholders. While traditionally applied in business contexts, the Lean Six Sigma approach can also be effectively employed in earlier stages to enhance research and development aimed at crafting more effective business solutions. This integration allows organizations to navigate evolving business landscapes with agility and foresight.
BUSI830 Project2 3
Introduction
The convergence of Six Sigma and Lean Thinking as methodologies finds application in a diverse spectrum of industries, each striving to streamline internal processes and minimize wastage in pursuit of improved efficiency and business outcomes. The combination of these two methodologies gives rise to Lean Six Sigma, a formidable framework enabling organizations not only to elevate their operational efficiency and product quality but also to deliver elevated value to their clientele. Though closely intertwined, these methodologies boast distinctive principles and advantages, ultimately furnishing organizations with tools such as the DMAIC (define, measure, analyze, improve, control) methodology to optimize workflows and enhance experiences for both internal and external stakeholders. While often the realm of business, the Lean Six Sigma approach can also be harnessed in earlier stages to enhance research aimed at devising more effective business solutions.
Lean Six Sigma and Lean Thinking
A combination of two methodologies, Lean Six Sigma (LSS), is utilized by organizations across varying industries to improve processes, eliminate waste, and achieve better outcomes. LSS provides organizations with the attributes from Six Sigma allowing for measurement, analysis, and improvement of processes while also using core fundamentals of lean thinking that focuses on identifying and eliminating waste (Steere et al., 2018). When utilized correctly, Lean Six Sigma becomes a powerful resource for organizations to enhance their efficiency, quality, and overall business performance. However, to truly understand the benefits of LSS, a deeper understanding of Six Sigma and Lean Thinking is required to appreciate the impact of this integrated methodology. According to Sreedharan and Sunder (2018), Six Sigma stands is a quality management methodology that relies on statistical methods to identify and subsequently
Your preview ends here
Eager to read complete document? Join bartleby learn and gain access to the full version
- Access to all documents
- Unlimited textbook solutions
- 24/7 expert homework help
BUSI830 Project2 4
eliminate defects within a given process, with the overarching goal being to achieve “near-
perfect” quality with no more than 3.4 defects per million opportunities (DPMO) (Sreedhara & Sunder, 2018). The data-driven analysis of Six Sigma allows organizations to pinpoint inefficiencies within their internal processes, inefficiencies that previously may have been masked by variations or irregularities, by refining all processes until optimal outcomes are achieved. Six Sigma methods are not isolated to internal improvements but rather are seen by an organization's customers as well. A study performed by Pereira et al. (2019) found that organizations that implemented Six Sigma methodologies not only reduced product defects by upwards of 50% but also increased customer satisfaction related to those products by approximately 20% (Pereira et al., 2019). Based on the principles of kaizen, a combination of two Japanese now referred to as “continuous improvement,” lean thinking is a methodology that focuses on eliminating waste and enhancing value throughout all aspects of an organization's processes and operations (Anderson et al., 2019). By focusing on the identification and elimination of various forms of waste within internal processes, such as overproduction or excessive inventory, lean thinking can aid organizations in streamlining workflows to allow for continuous improvement. Like Six Sigma, organizations utilizing lean thinking are often rewarded with increased customer satisfaction. A study performed by Goshime et al. (2019), found that lean thinking helped organizations reduce defects by upwards of 50% and increased customer satisfaction by 10% (Goshime et al., 2019). When combined, LSS harnesses the analytics precision of Six Sigma and waste-reducing principles of lean thinking to form a powerful framework for organizational success.
BUSI830 Project2 5
Benefits of Lean Six Sigma
As explained by Singh and Rathi (2019), LSS provides benefits across varying industries such as manufacturing by increasing productivity, healthcare by improving patient safety, and financial services by reducing costs (Sigh & Rathi, 2019). In addition to improved quality and increased customer satisfaction discussed earlier, Singh and Rathi (2019) provide five major benefits of LSS which include cost reduction, increased employee satisfaction, and improved environmental sustainability (Sigh & Rathi, 2019). For cost reduction, LSS relies on the core principle of lean thinking, waste elimination. By minimizing or eliminating wasteful processes, LSS can help organizations reduce costs associated with unutilized resources, excessive inventory holding, and unnecessary labor. While the customer satisfaction benefits discussed earlier may be considered the top benefit, the employee satisfaction benefits can be equally significant. LSS allows for employees to have more autonomy over their work, while also creating more efficient workflows for the organization, and provides employees with opportunities for training and development that can lead to career advancement (Minh et al., 2019). Finally, environmental sustainability has proven to be another benefit of the LSS methodology, which aims to reduce waste including physical waste, and can improve efficiency within an organization such as the reuse or reallocation of resources. A study performed by Zhu et al. (2018), found hospitals in the United States were able to reduce their waste by 20%, their energy consumption by 15%, and their water consumption by 10% after implementing LSS methodologies, which ultimately led to $1 million in savings (Zhu et al., 2018).
Principles of Lean and Lean Six Sigma
Both Lean thinking and LSS carry guiding principles that underscore their effectiveness in enhancing organizational performance, yet they do so through distinct yet complementary
BUSI830 Project2 6
approaches. Lean thinking centers its ideology around the concept of value, the core principles of
value, value stream, flow, pull, and perfection. As explained by Srem et al. (2018), organizations must understand the value from the customer perspective and then map to visualize their flow to that customer (Srem et al., 2018). Once completed, the organization will act on the mapped value
stream by creating a flow in which waste is reduced and the flow is geared toward the customer, after which pull can be enacted to identify and address demand without creating surplus (Srem et
al., 2018). Finally, as explained by Srem et al. (2018), organizations must always seek continual improvement. While the principles of LSS are similar in that they are centered on the customer, they differ in that they integrate analytical tools and methodologies to systematically identify the root causes of defects and variations within processes. Ricciardi et al. (2019) provide the seven principles of LSS of focusing by first focusing on the customer and their needs, then defining, measuring, analyzing, and improving a process, and then adopting a culture of continuous improvement (Ricciardi et al., 2019). While both lean thinking and LSS have differing principles, one commonality is their final phases call for continuous improvement. Similarly, God has decreased and willed us to constantly seek growth be it in our personal, professional, or spiritual lives. Jeremiah 12:2 states, “You have planted them, and they have taken root; they grow and bear fruit. You are always on their lips but far from their hearts." In this passage, Jeremiah expresses frustration about the prosperity of the wicked and the suffering of the righteous. In essence, this too was a calling from God, to test Jeremiah and to allow him to have continuous growth in the context of his faith
and relationship with God, rather than mere outward displays of religiosity or success. This aligns with the essence of lean thinking and LSS, emphasizing the importance of genuine
Your preview ends here
Eager to read complete document? Join bartleby learn and gain access to the full version
- Access to all documents
- Unlimited textbook solutions
- 24/7 expert homework help
BUSI830 Project2 7
progression beyond superficiality, just as Jeremiah's faith was challenged to deepen beyond outward displays.
DMAIC
DMAIC (define, measure, analyze, improve, control) is a dynamic problem-solving methodology and core component of LSS, in which organizations can make more well-informed decisions to achieve optimal business outcomes. Within the Define phase, the organization’s problem is defined, project goals and objectives are set, and key stakeholders are identified. During the Measure phase, relevant data is collected to understand the state of the current processes which leads into the Improve phase in which the organization can test various solutions for process enhancements. Finally, in the Control phase, the organization works to sustain its improvements to ensure continuous improvement (Widodo and Soediantono, 2022). Widodo and Soediantono (2022) elaborate on the benefits of DMAIC across various industries, including the defense industry where the methodology has been proven effective in improving the quality, efficiency, and profitability of organizations (Widodo & Soediantono, 2022). Application of Lean Six Sigma Through All Types of Research
While the focus of LSS application is typically within the context of business, the same principles can be applied to the field of research that drives business solutions as well. Organizations looking to reduce the number of defects within their products may look to perform
quantitative analysis in which they focus on potential areas of concern and use analytical tools such as DPMO to further enhance customer satisfaction with products. Qualitative-based research is integral for stakeholder engagement, specifically on customers and their perceptions of an organization or product. Finally, mixed method approaches combine quantitative data and
BUSI830 Project2 8
qualitative insights to provide a comprehensive understanding of complex business issues and the subsequent solutions. Conclusion
Lean Six Sigma has become a proven commodity across a diverse array of industries, each of which has a shared goal of improving internal processes and minimizing waste to enhance efficiency and ultimately lead to better business outcomes. By integrating the precision of Six Sigma's data-driven analysis and the waste-reducing principles of Lean Thinking, organizations harness a dynamic framework that not only heightens their operational efficacy and product quality but also catapults their capacity to deliver elevated value and customer satisfaction. The approach not only yields improved business outcomes but also fosters cultures of innovation and progress with the framework applied to research that drives business solutions.
This integration of quantitative and qualitative methodologies provides organizations with a deeper understanding of complex business challenges, empowering organizations to navigate an ever-evolving landscape and customer demands with agility and foresight.
BUSI830 Project2 9
References
Anderson, J. B., Marstiller, H., & Shah, K. (2019). Lean thinking for primary care.
Primary care:
clinics in office practice
,
46
(4), 515-527.
Goshime, Y., Kitaw, D., & Jilcha, K. (2019). Lean manufacturing as a vehicle for improving productivity and customer satisfaction: A literature review on metals and engineering industries.
International Journal of Lean Six Sigma
,
10
(2), 691-714.
Minh, K. S., Zailani, S., Iranmanesh, M., & Heidari, S. (2019). Do lean manufacturing practices have negative impact on job satisfaction?.
International Journal of Lean Six Sigma
,
10
(1), 257-274.
The Holy Bible, New International Version. (2011).
Blue Letter Bible.
https://www.blueletterbible.org/niv/index.cfm
(Original work published 1973)
Pereira, M. T., Bento, M. I., Ferreira, L. P., Sá, J. C., Silva, F. J. G., & Baptista, A. (2019). Using Six Sigma to analyse Customer Satisfaction at the product design and development stage.
Procedia Manufacturing
,
38
, 1608-1614.
Ricciardi, C., Fiorillo, A., Valente, A. S., Borrelli, A., Verdoliva, C., Triassi, M., & Improta, G. (2019). Lean Six Sigma approach to reduce LOS through a diagnostic-therapeutic-
assistance path at AORNA Cardarelli.
The TQM Journal
,
31
(5), 657-672.
Singh, M., & Rathi, R. (2019). A structured review of Lean Six Sigma in various industrial sectors.
International Journal of Lean Six Sigma
,
10
(2), 622-664.
Your preview ends here
Eager to read complete document? Join bartleby learn and gain access to the full version
- Access to all documents
- Unlimited textbook solutions
- 24/7 expert homework help
BUSI830 Project2 10
Sreedharan V, R., & Sunder M, V. (2018). Critical success factors of TQM, Six Sigma, Lean and Lean Six Sigma: A literature review and key findings.
Benchmarking: An International Journal
,
25
(9), 3479-3504.
Sremcev, N., Lazarevic, M., Krainovic, B., Mandic, J., & Medojevic, M. (2018). Improving teaching and learning process by applying Lean thinking.
Procedia Manufacturing
,
17
, 595-602.
Zhu, Q., Johnson, S., & Sarkis, J. (2018, January). Lean six sigma and environmental sustainability: a hospital perspective. In
Supply Chain Forum: An International Journal
(Vol. 19, No. 1, pp. 25-41). Taylor & Francis.
Recommended textbooks for you
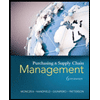
Purchasing and Supply Chain Management
Operations Management
ISBN:9781285869681
Author:Robert M. Monczka, Robert B. Handfield, Larry C. Giunipero, James L. Patterson
Publisher:Cengage Learning
Marketing
Marketing
ISBN:9780357033791
Author:Pride, William M
Publisher:South Western Educational Publishing
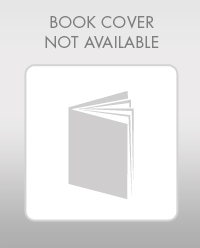
Contemporary Marketing
Marketing
ISBN:9780357033777
Author:Louis E. Boone, David L. Kurtz
Publisher:Cengage Learning
Recommended textbooks for you
- Purchasing and Supply Chain ManagementOperations ManagementISBN:9781285869681Author:Robert M. Monczka, Robert B. Handfield, Larry C. Giunipero, James L. PattersonPublisher:Cengage LearningMarketingMarketingISBN:9780357033791Author:Pride, William MPublisher:South Western Educational Publishing
- Contemporary MarketingMarketingISBN:9780357033777Author:Louis E. Boone, David L. KurtzPublisher:Cengage Learning
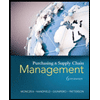
Purchasing and Supply Chain Management
Operations Management
ISBN:9781285869681
Author:Robert M. Monczka, Robert B. Handfield, Larry C. Giunipero, James L. Patterson
Publisher:Cengage Learning
Marketing
Marketing
ISBN:9780357033791
Author:Pride, William M
Publisher:South Western Educational Publishing
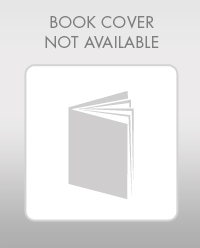
Contemporary Marketing
Marketing
ISBN:9780357033777
Author:Louis E. Boone, David L. Kurtz
Publisher:Cengage Learning