Moison_2019
pdf
keyboard_arrow_up
School
University of Wisconsin, Milwaukee *
*We aren’t endorsed by this school
Course
787
Subject
Business
Date
Jun 1, 2024
Type
Pages
39
Uploaded by DeanClover24035
Joint Replenishment and Base Stock Model for the U.S. Beer Industry By Nathan George Moison Bachelor of Science, Business Administration, University of South Carolina, 2015 SUBMITTED TO THE PROGRAM IN SUPPLY CHAIN MANAGEMENT IN PARTIAL FULFILLMENT OF THE REQUIREMENTS FOR THE DEGREE OF MASTER OF APPLIED SCIENCE IN SUPPLY CHAIN MANAGEMENT AT THE MASSACHUSETTS INSTITUTE OF TECHNOLOGY JUNE 2019 © 2019 Nathan George Moison. All rights reserved. The authors hereby grant to MIT permission to reproduce and to distribute publicly paper and electronic copies of this capstone document in whole or in part in any medium now known or hereafter created. Signature of Author: ____________________________________________________________________ Nathan George Moison Department of Supply Chain Management May 10, 2019 Certified by: __________________________________________________________________________ Dr. Josu
é
C. Vel
á
zquez Mart
í
nez Executive Director, Supply Chain Management Blended Program Capstone Advisor Certified by: __________________________________________________________________________ Dr. Sergio Caballero Research Scientist, Center for Transportation & Logistics Capstone Co-Advisor Accepted by: __________________________________________________________________________ Dr. Yossi Sheffi Director, Center for Transportation and Logistics Elisha Gray II Professor of Engineering Systems Professor, Civil and Environmental Engineering
2 Joint Replenishment and Base Stock Model for the U.S. Beer Industry by Nathan George Moison and Submitted to the Program in Supply Chain Management on May 10, 2019 in Partial Fulfillment of the Requirements for the Degree of Master of Applied Science in Supply Chain Management ABSTRACT The United States beer industry operates, by law, under a three-tier distribution network. MillerCoors has made the strategic decision to open distribution centers across the United States to handle complexity while maintaining service levels. Opening new distribution centers, and introducing a new tier to the supply chain, requires MillerCoors to define a new inventory deployment strategy to maintain their service levels to their customers. This project provides a solution to the inventory deployment problem by determining how a joint replenishment approach combined with the base stock inventory policy improves the deployment of inventory across MillerCoors supply chain. A repeatable and scalable heuristic is developed which employs joint replenishment to determine economic production frequencies and links to the base stock policy across all echelons within the supply chain. The results showed inventory reductions across 75% of all products analyzed. The results also demonstrate the importance of distribution centers to pool demand and improve alignment of inventory deployment across the supply chain. Capstone Advisor: Dr. Josue Velazquez Title: Executive Director, Supply Chain Management Blended Program Capstone Co-Advisor: Dr. Sergio Caballero Title: Research Scientist, Center for Transportation & Logistics
3 ACKNOWLEDGMENTS I would like to thank my advisors Dr. Josue Velazquez Martinez and Dr. Sergio Caballero for their mentorship, guidance, and encouragement throughout this capstone project. I would also like to thank the following members of the MillerCoors team for their engagement and support to make this project a success. Lisa Vanlerberghe is an incredible coach, advocate, mentor, and sponsor from the time we developed the project proposal all the way through completion. She has made herself available and showed support by attending my presentations here at MIT. She has rallied the support from her network and team at MillerCoors to support any and all data needs and has helped me grow as a supply chain professional. This project would not be possible without her. John Stonebraker believed in my ambitions to attend MIT and advocated for me to make this dream a reality. Other colleagues that contributed to the success of this project are Russ Riecken, Steve Ahles, Nancy Servigna, Cara Stoltz, Jon Trimm, Rob Barringer, Will Dunlap, Sherry Walsh, and Mike Hogan. I would also like to thank my sister and her fiancée for their encouragement and for helping me translate my industry knowledge and experience into an academic voice. Lastly, I would like to thank my parents for their support on this journey. Thank you. Nate Moison
Your preview ends here
Eager to read complete document? Join bartleby learn and gain access to the full version
- Access to all documents
- Unlimited textbook solutions
- 24/7 expert homework help
4 TABLE OF CONTENTS Abstract
......................................................................................................................
2 Acknowledgements
....................................................................................................
3 Table of Contents
.......................................................................................................
4 List of Figures
............................................................................................................
5 List of Tables
.............................................................................................................
5 1.
Introduction
...........................................................................................................
6 1.1.
Problem Statement
.........................................................................................
7 1.2.
Relevance
.......................................................................................................
7 1.3.
Motivation
......................................................................................................
7 2.
Literature Review
..................................................................................................
8 2.1.
SKU Classification
.........................................................................................
8 2.2.
Analytical Hierarchy Process (AHP)
.............................................................
9 2.3.
Data Envelopment Analysis (DEA)
...............................................................
12 2.4.
Multi-Echelon Inventory Optimization
..........................................................
14 2.5.
Joint Replenishment Problem (JRP)
..............................................................
16 2.6.
Base Stock Model
..........................................................................................
17 3.
Methodology
.........................................................................................................
19 4.
Case Study
.............................................................................................................
23 4.1.
The Company
.................................................................................................
23 4.2.
The Supply Chain
...........................................................................................
23 4.3.
Golden Brewery Business Unit
......................................................................
24 4.4.
“3.2” Portfolio
................................................................................................
25 4.5.
Current Process
..............................................................................................
26 5.
Results and Analysis
.............................................................................................
29 6.
Conclusion and Managerial Implications
..............................................................
35 References
...................................................................................................................
37
5 LIST OF FIGURES Figure 1: Methodology
...................................................................................................
19 Figure 2: Current SKU Run Strategies for “3.2” Portfolio
............................................
28 Figure 3: Distributor Change in DOI
.............................................................................
32 Figure 4: Distributor Change in Barrels
........................................................................
33 LIST OF TABLES Table 1: Recommended Run Strategy
vs. Actual Run Strategy
....................................
30
6 1. Introduction
Multi-echelon supply chains exist across a variety of industries. A multi-echelon supply chain is one where inventories are distributed across multiple layers, called echelons. Throughout this capstone we use tiers, levels, and echelons interchangeably. One example of a multi-echelon supply chain would be one where finished goods flow from a manufacturing plant to a distribution center to a fulfillment center to a customer and inventory is stored at each of these locations. In some cases, inventories are maintained at echelons as close to the end user as possible. In other situations, inventories are aggregated and stored at higher echelons to help organizations better handle fluctuations in demand. There are merits to both approaches. A single organization can be responsible for several echelons or just a single echelon. The tiers in a supply chain can also be managed through coordination of internal and external suppliers and customers. In addition to the multiple levels of the supply chain, organizations are constantly trying to more effectively manage an ever-increasing number of stock keeping units (SKUs). Studies have shown that organizations also struggle to retire SKUs. This is due largely in part to the fact that any removal of a SKU represents a perceived reduction in sales revenue without a clear replacement to recover that lost revenue. The supply chain becomes more complex to manage as the tiers and number of SKUs increase. As a result, organizations have employed various strategies to manage these large portfolios of SKUs including Pareto Analysis and ABC classification. These typically focus on cost-based metrics or volume-based metrics and are one-
dimensional. This project investigates the inventory strategy of the multi-echelon supply chain at MillerCoors. This real-world context supports, motivates, and validates the insights gained from the analysis.
Your preview ends here
Eager to read complete document? Join bartleby learn and gain access to the full version
- Access to all documents
- Unlimited textbook solutions
- 24/7 expert homework help
7 1.1 Problem Statement The purpose of this capstone project is to improve the way MillerCoors allocates SKUs to production frequencies and inventory policies. More specifically, we seek to answer the question – how does a joint replenishment approach improve the way we determine inventory policy for multi-echelon supply chains? By answering that question, supply chain professionals and researchers should understand how connecting the optimal production frequency for subsets of SKUs can help form base stock inventory policies in multi-echelon supply chains. Readers will then be able to make better decisions when determining the inventory policy for new products due to the general and scalable solution we present. 1.2 Relevance Many articles and papers have been written on the topics of multi-echelon supply chains, inventory policy, data envelopment analysis (DEA) and joint replenishment problems (JRP). Many papers also exist using DEA to classify SKUs and then a linear optimization to determine the appropriate inventory policies. However, there are still avenues which have not yet been explored. A gap exists in the current body of knowledge to simultaneously optimize the production frequencies within a repeating cyclical production cadence and inventory policies across a multi-echelon supply chain. We show that a heuristic combining JRP and base stock policy improves the deployment of inventory across a multi-echelon supply chain. We further support this by including actual data from industry within this capstone project to provide insights of interest to both industry professionals as well as researchers. 1.3 Motivation
The motivation of this capstone project is to address an issue faced by MillerCoors and many other consumer packaged goods (CPG) companies. As consumer preferences continually
8 change, organizations are faced with an ever-increasing quantity of SKUs to manage. As the quantity of SKUs increases, managing the inventory becomes equally as challenging. SKU count reduction efforts are often challenging, due to the revenue implications of eliminating products. Solving the inventory management problem for MillerCoors helps position the organization for success in a challenging market which demands ever-increasing service level delivery to customers. 2.0 Literature Review In this section, we review the literature relevant to our research. We begin with a discussion of the evolution of inventory classification and the key approaches, models, and limitations. We then move into the body of knowledge surrounding multi-echelon supply chain inventory policies and strategies. We selected these topics because they build the foundation on which to conduct our analysis. Based on past research, we knew which techniques were applied to similar problems and were able to combine them to solve the multi-echelon inventory problem for MillerCoors. 2.1 SKU Classification Companies and organizations have long looked for ways to classify products, parts, inventory, and other items in order to improve the efficiency of decision making. A single individual cannot effectively manage and make decisions on an individual SKU basis for the thousands of SKUs many companies maintain in their portfolios. This has become even more important than ever before in recent years due in part to the proliferation of unique products available in the marketplace. The earliest insights on classifying and prioritizing items dates back to the late 1800’s (Kenton, 2019). Vilfredo Pareto, an Italian economist, made the observation that roughly 80
9 percent of outputs are a result of 20 percent of the inputs. The Pareto Principle has been applied and adapted widely since the late 19
th
century, from sales management, to economic status, to portfolio management. In the case of inventory management, Pareto analysis is more commonly known as ABC Classification. A items represent the “Critical Few”; the 20 percent of SKUs that comprise 80 percent of the sales, inventory value, etc. C items represent the trivial few, and B items fall somewhere in between. Some organizations will also introduce additional classifications beyond C items to further segment their inventories. One of the strengths of the Pareto Principle is that it is a heuristic that is easy to understand, calculate, interpret, and action against. It is also easy to plot and display visually. On the other hand, this approach is only one-
dimensional. By that, we mean that it takes into account only a single metric to rank and classify items. Over the years, researchers and professionals realized that by including more than one factor for classification, they could better understand their portfolios, make better decisions and improve the financial performance of organizations. Their approaches typically fall into one of three categories, subjective ratings with Analytic Hierarchy Process, optimizations, and artificial intelligence techniques (Ravinder & Ph, 2015). 2.2 Analytical Hierarchy Process (AHP) The Analytical Hierarchy Process (AHP) has also been researched as a method for multicriteria inventory classification. Flores et. al (Flores, Olson, & Dorai, 1992) were one of the first to propose a repeatable methodology to classify SKUs using multiple criteria. Their methodology begins by identifying the criteria relevant to the decision they are trying to make. Once the criteria have been identified, they are organized into a hierarchy based on relative importance. A certain amount of subjectivity occurs at this step; however, the subsequent
Your preview ends here
Eager to read complete document? Join bartleby learn and gain access to the full version
- Access to all documents
- Unlimited textbook solutions
- 24/7 expert homework help
10 analytical processes help to minimize the impacts of subjectivity. Due to the human involvement in the hierarchy and ranking at this stage, Flores notes that no more than 7 total criteria should be analyzed because humans struggle to efficiently and consistently rank any more than that. Flores leveraged computer software to compare the criteria at each node in the hierarchy and generate the weights for each of the key criteria. Flores also notes the importance of normalizing the values for each SKU within each of the criteria between 0 and 1. Without normalizing the performance, our view of the relative performance of dollar value and lead time would be skewed. Flores applies the outlined methodology to a set of 47 SKUs for a hospital. The analysis considers average unit cost, annual dollar usage, a critical factor, and lead time as criteria for the classification. One key foundational model for multi-criteria classification is the Ramanathan Model (Ramanathan, 2006). Ramanathan uses weighted linear optimization, however they do not normalize the scores for each of the criteria before optimizing. The objective function seeks to maximize the output and assign a score for each individual decision-making unit. In order to find the optimal score for each SKU within the data set, the user changes the objective function to maximize the score of the j
th
item. The approach must be repeated for each item within the data set. While simple in structure and formulation, Ramanathan’s approach is cumbersome and inefficient for large sets of SKUs. The other key model we will focus on is the Ng model (Ng, 2007). Ng noted that prior approaches to inventory classification were either too subjective or too complicated to implement in practice. As a result, they developed a linear optimization model that can be solved with or without a solver program which is easily understood by all stakeholders. Ng reduces the subjectivity of scoring criteria, a drawback of AHP modeling, by having the inventory manager
11 rank the criteria in order of importance. The inventory manager only decides that one criterion is more important than another, but not by how much. While this does not completely eliminate subjectivity, it substantially reduces it. New weights are generated each time the optimization is run and normalized between 0 and 1. This allows the model the flexibility to add or remove SKUs from the analysis and then reassign weights and classifications. After the optimization runs, the resulting weights can be sorted into their ABC classifications. Ng applies their model to the same 47 SKU dataset used by Ramanathan and others and compares the results. This model is limited because it becomes more difficult to solve as more criteria and SKUs are introduced. In addition, if the priority of a particular criteria changes, the classification of a particular SKU changes roughly 40% of the time. One can expect that this would only be magnified as additional criteria are introduced and the combination of partial averages increases. In the data used in this particular example, item number 5 can be classified as an A item, a B item, or a C item depending on the priority order. This example demonstrates that while the Ng Model is easy to understand and calculate, its results are sensitive to the number of criteria and the relative importance chosen by managers. Hadi-Vencheh and Mohamadghasemi used fuzzy set theory to determine the weights of the criteria for AHP (Hadi-Vencheh & Mohamadghasemi, 2011), They argue that fuzzy theory helps to handle the subjectivity of decision makers while ranking quantitative and qualitative factors. Terms (Very High, High, Medium, Low, Very Low) are used by decision makers to rank each SKU for each of the criteria. While compared to the Flores approach, the Fuzzy AHP can be applied to any number of criteria, limitations still exist. As the number of SKUs increases, the demand on inventory managers to rank each individual SKU increases as well.
12 This capstone aims to address this gap, by developing an approach that involves minimal intervention from decision makers, regardless of the number of SKUs. 2.3 Data Envelopment Analysis (DEA) Data Envelopment Analysis (DEA) has a variety of applications from determining the efficiency of a process to resource allocation to classification of items. In contrast to traditional regression approaches, which determine a function that applies to all points within a data set, DEA calculates an optimal objective for each individual point (Hatami-Marbini, Emrouznejad, & Tavana, 2011). Efficiencies of each individual point are scored in comparison to all other points within the dataset (Charnes, Cooper, Seiford, & Tone, 1994)
.
The scores typically follow a Pareto-like form when plotted. Traditional DEA approaches can lead to potential incorrect classifications of SKUs in order to satisfy arbitrary distributions of A, B, and C items. Ishizaka, Lolli, Balugani, Cavallieri and Gamberini present an extension to DEA, called DEASort, which uses a decision tree to sort items based on their weighted average scores (Ishizaka, Lolli, Balugani, Cavallieri, & Gamberini, 2018). DEASort uses input from inventory managers to determine the upper and lower bounds for each of the criteria. Once the DEA calculation runs, the output scores are classified using the decision tree. By using predetermined score boundaries for A, B, and C items, the model avoids classification error. For example, if we were trying to classify 100 SKUs using a traditional DEA approach we may decide on the following distribution: 20 A items, 35 B items, and 45 C items. We may have 2 items with identical scores after the DEA analysis, but because we decided on assigning 35 items a ‘B’ classification, one will be classified as a ‘B’ and the other a ‘C’. DEASort, on the other hand, looks at where the scores fall in relation to ranges of scores for each classification. This may mean we do not adhere to a strict number of SKUs for
Your preview ends here
Eager to read complete document? Join bartleby learn and gain access to the full version
- Access to all documents
- Unlimited textbook solutions
- 24/7 expert homework help
13 each classification and thus the number of SKUs in each category will fluctuate each time the analysis is performed. One aspect of DEASort that needs to be expanded is the inclusion of qualitative criteria. Liu and Huang modify the classical DEA approach by including suggested ranges of the weights for each criteria as constraints in their linear optimization (Liu & Huang, 2006). The model, like many others, includes only quantitative criteria. Hatefi, Torabi, and Bagheri extended a prior model developed by Cook, Kress, and Seiford, which incorporates quantitative and qualitative criteria (Hatefi, Torabi, & Bagheri, 2014). Hatefi, et al also include a discrimination value, e
, in their model which sets a minimum for the weights of each criteria as well as the difference between different levels of the qualitative criteria. The proposed model is applied to the same 47 SKU set as the Ramanathan model, which also extends Ramanathan’s conclusions. They also minimize the subjectivity found in prior models by using a dimensional unit vector to categorize the qualitative factors instead of a Likert scale. The number of levels in the unit vector corresponds to the values of the qualitative criteria. In their example, the qualitative factors can take the value of very critical, moderately critical, or non-critical
. Therefore, the unit vector would have 3 levels. Millstein, Yang, and Li propose an extension to multi-criteria inventory classification that optimizes the number of groups in which to categorize SKUs along with their respective service levels. The methodology is then able to classify a set of SKUs into the appropriate categories (Millstein, Yang, & Li, 2014). Other approaches using Machine Learning Algorithms have emerged to support multi-
criteria inventory classification. Both supervised (Lolli, Ishizaka, Gamberini, Balugani, & Rimini, 2017) and unsupervised approaches (Ladhari, Babai, & Lajili, 2013) have been used.
14 Decision trees and random forests are commonly used for these types of analyses, as they perform well when a data set needs to be sorted. Further opportunities exist to include qualitative data in the machine learning analyses. Yu analyzed different machine learning techniques including support vector machines, backpropagation networks, and k-nearest neighbors and compared them to a multiple discriminant analysis (Yu, 2011). Yu analyzed the same set from the Ramanathan study and concluded that the support vector machine approach yielded the most accurate results. 2.4 Multi-Echelon Inventory Optimization Researchers have also studied multi-echelon supply chain inventory strategies since the middle of the 20
th
century. Multi-echelon inventory management, unlike individualized approaches, focuses on optimizing the entire supply chain rather than just a single stage (Sbai & Berrado, 2018). Recently, a comprehensive taxonomy paper was written for the area of researching multi-echelon inventory models. The review paper includes an organized classification of the papers based on the assumptions, research goals, and methodologies (de Kok et al., 2018). From this review, we see that opportunities remain to better understand multi-
echelon supply chains with capacity constraints as well as provide research with field study-
based analyses, less than 5% of papers reviewed. This capstone addresses both of those gaps in addition to incorporating SKU Classification as an input to determine the inventory policy. Li and Liu formulated a comprehensive multi-objective multi-echelon inventory model which incorporates constraints that impact the end to end supply chain. The model uses thorough production, transportation, and cost constraints to optimize all objectives (Li & Liu, 2010). The formulation of this model may be difficult to implement in the field, due to its complexity which may not be easily understood by supply chain managers. Tjhin and Pandey
15 compare a variety of multi-echelon inventory strategies for a medical device manufacturer. They conclude that the Strategic Inventory Placement method may improve the overall supply chain by shifting more of the system inventory to finished goods rather than components (Tjhin & Pandey, 2012). Various inventory replenishment strategies have also been modeled, including a continuous review (R,Q) policy for a three echelon supply chain (Amiri, Seifbarghy, Olfat, & Hajiagha, 2012). Scott and Xu studied the design of multi-echelon supply chains and determined that for their proposed model the reduction in safety stock was almost entirely offset by increases in pipeline inventory. The primary driver for the increase was lead time variability (Scott & Xu, 2017). Giacomantonio analyzed a large consumer goods manufacturer and noted a similar phenomenon when the transportation lead times significantly exceed customer expectations. In these situations, inventory increases and is pushed to the lowest echelon in order to maintain service levels (Giacomantonio, 2013). Thus, aggregating inventory alone will not always yield a solution with cost benefits. Before attempting to implement such a strategy, supply chain managers would want to address their lead times in addition to aggregating inventory. The Guaranteed Service Model (GSM), developed by Graves and Willems, is one of the strategies used to understand and improve the performance of multi-echelon supply chains. Graves and Schoenmeyr developed an extension to the GSM which incorporates capacity constraints. This methodology reveals that at each stage with capacity constraints, the demand signal will be impacted as it moves upstream. Graves and Schoenmeyr recommend maintaining safety stock at each echelon upstream from the capacitated tier(Graves & Schoenmeyr, 2016). GSM has also been extended and combined with the stochastic service (SS) approach to form a hybrid approach. The hybrid approach segments the supply chain into a combination of SS and
Your preview ends here
Eager to read complete document? Join bartleby learn and gain access to the full version
- Access to all documents
- Unlimited textbook solutions
- 24/7 expert homework help
16 GSM nodes, which takes advantage of the benefits of both strategies(Klosterhalfen, Dittmar, & Minner, 2013). Further extensions of GSM have looked at optimizing reorder intervals as well as the addition of new constraints (Eruguz, Jemai, Sahin, & Dallery, 2014). Researchers have started adding capacity constraints, but they pertain mainly to the volume of units the system can process at a single stage (Eruguz, Sahin, Jemai, & Dallery, 2016). More recently, studies have looked at combining multi-echelon inventory policies with segmentation by allocating products to a particular supply chain segment based on their classifications (Fichtinger, Chan, & Yates, 2017). Gupta further extends GSM and combines traditional single criteria SKU classification with a multi echelon inventory strategy to determine the optimal distribution network design (Gupta, 2008). 2.5 Joint Replenishment Problem (JRP) While the approaches highlighted above have certainly contributed greatly to the understanding of inventory policies in multi-echelon supply chains, we feel there are further opportunities using a joint replenishment problem (JRP) approach. Joint replenishment refers to the economies of scale which can be achieved by combining the replenishment of items and reducing the ordering costs. The total costs can be reduced by pooling the replenishment orders and spreading the fixed order costs across multiple products instead of a single product. The DEA approach has certain limitations which are difficult to effectively mitigate, such as subjectivity and human interaction. In addition, these approaches typically also meet challenges when trying to expand to broad product portfolios. JRP, explored as early as the 1960’s (Khouja & Goyal, 2008), addresses many of these shortcomings. The main objective of a JRP model is to determine the replenishment scheme for a group of SKUs which minimizes the overall cost.
17 This uses very similar assumptions to the economic order quantity (EOQ) model. The joint replenishment model also relates to principles from the Toyota Production system around production smoothing and mixed model scheduling. Chopra and Meindl present an algorithm, which applies the JRP principles, to calculate a near optimal ordering frequency for portfolios of SKUs which minimizes the total cost (Chopra & Meindl, 2013). The approach presents a five-step process to calculate the relative order frequencies as compared to the portfolio item which must be ordered the most frequently. Another approach takes into account not only the joint fixed costs associated with production, but also the variable product specific cost to determine an optimal solution for all product offerings (Bayindir, Birbil, & Frenk, 2006). This focused on a single stage inventory model while multi-echelon applications of this approach still need to be explored. Another JRP model focused on a single item and multiple locations, instead of multiple items and multiple locations (Silva & Gao, 2013). Other solutions include constraints for minimum order quantities, which better simulate real-world operations (Porras & Dekker, 2006). Various capacity restrictions have also been explored to solve the JRP in order to generate more practical operational solutions (Moon & Cha, 2006; Amaya, Carvajal, & Castaño, 2013; Ongkunaruk, Wahab, & Chen, 2016). 2.6 Base Stock Model The base stock model has been widely discussed in literature. Graves and Willems discuss the base stock policies for multi-echelon supply chains (Graves & Willems, 2003). The base stock model ties a target inventory level to the level of service a supply chain wishes to deliver. It balances both the cycle stock and safety stock to determine the appropriate level of inventory. They model a supply network with deterministic lead-times, stationary demand, common review
18 periods, and infinite capacity. The assertion is also made to differentiate strategic safety stock from standard safety stock. The main differentiation being that strategic safety stock enables tiers of the supply chain to function independently from one another, due to the quantity of inventory maintained. We will model similar assumptions to Graves and Willems, but with JRP production frequencies. Our research enhances the current body of knowledge because we are connecting the joint replenishment problem for production with inventory policy decision making in a single model. We provide a heuristic framework to link production frequency with a base stock policy in a single calculation for a product portfolio. Furthermore, we align the production frequencies into a repeatable cadence for organizational stability period to period. The cadence ensures that all SKUs are produced at least once during a four-week period.
Your preview ends here
Eager to read complete document? Join bartleby learn and gain access to the full version
- Access to all documents
- Unlimited textbook solutions
- 24/7 expert homework help
19 3. Data and Methodology In this chapter, we present the methodology used to simultaneously determine the production frequencies and the inventory policies for a multi-echelon supply chain. We begin by outlining the formulation used for the heuristic. We will then introduce a case study of MillerCoors where we apply the methodology to actual data and present our outcomes. The main steps of the methodology are as follows, which will be further elaborated throughout the remainder of this chapter. First, we must collect and clean the relevant data. We then calculate the recommended run strategies based on the joint replenishment (JRP) algorithm. This allows us to categorize the SKUs and prepare them for the inventory policy portion of the heuristic. The classification and run strategy then feed into the base stock calculation as the lead time. We calculate the appropriate inventory policy for the Distribution Center as well as all distributors. All pertinent and relevant formulas are included in section 3.1. Figure 1: Methodology 3.1 Heuristic Our analysis involves a combination of the joint replenishment process heuristic and the base stock policy. In the following section, we will define all of the equations and variables used to generate our production cadence driven inventory policies. ࠵?
"
# = %
&’
(
)
(
*(,-.
(
)
(Eq.1) Collect and Clean Data
Calculate Run Strategies
(JRP)
Calculate Base Stock Policy
20 We will start by defining all variables within Eq.1. ℎ
represents the holding cost, as a percentage of unit cost. For our analysis, we will assume a 15% holding cost. ࠵?
࠵?
represents the Unit Cost for each SKU, ࠵?
. ࠵?
࠵?
represents the Annual Demand for each SKU, ࠵?
. ࠵?
represents the fixed setup cost for each production run. ࠵?
࠵?
represents the unique cost for each SKU, ࠵?
. For our analysis, we will interpret ࠵?
7
as the cost of complexity for each SKU based on the annual volume. Cost of complexity refers to the increased costs and decreased efficiencies that develop as the number of low volume SKUs increases. The cost is used to quantify the added burden on the supply chain for each incremental SKU added to a portfolio. Finally, we are solving for ࠵?
#
, which is the economic number of production runs for each SKU per year. Once we have calculated ࠵?
#
7
, we identify which SKU has the largest value. This will become our reference point to determine the frequency to produce every other SKU, relative to the ࠵?
#
SKU. ࠵?
8
7
= %
&’
(
)
(
*.
(
(Eq.2) Next, in Eq.2, we calculate ࠵?
࠵?
9
, which is the economic production frequency for all SKUs which are not ࠵?
#
. All other variables are the same as in Eq.1. The reason that the fixed cost, S, is no longer included is because the most frequently produced SKU absorbs all of this cost. The heuristic assumes that the most frequently produce SKU is produced with every run of the other SKUs. ࠵?
7
= ;
<
<
=
888
#
>
(Eq.3)
Eq.3 determines the production frequency, ࠵?
࠵?
, for every ࠵?
9
7
relative to ࠵?
#
, for each SKU, ࠵?.
The brackets surrounding the equation signify us to round the result up to the nearest integer.
21 Once we have determined all of the ࠵?
࠵?
, we need to assign each SKU to a production frequency, also referred to as a production run strategy. We have seven options to choose from. The available run strategies are listed below: 1.
Produced weekly (Weeks 1, 2, 3, 4)
2.
Produced bi-weekly, on odd weeks (Weeks 1 and 3)
3.
Produced bi-weekly, on even weeks (Weeks 2 and 4)
4.
Produced one out of four weeks, on first odd (Week 1)
5.
Produced one out of four weeks, on first even (Week 2)
6.
Produced one out of four weeks, on second odd (Week 3)
7.
Produced one out of four weeks, on second even (Week 4)
Based on the outputs, we will use the following logic sequence to map the SKUs to a run strategy. If ࠵?
࠵?
is equal to 1, assign to run strategy 1. If ࠵?
࠵?
is equal to 2, assign to run strategy 2 or 3. If ࠵?
࠵?
is greater than 2, assign to run strategy 4, 5, 6, or 7. For the purposes of this analysis, we will treat the bi-weekly run frequencies as comparable to each other, and can assume we would evenly split the SKUs between even and odd week production cycles. Similarly, we will assume that the SKUs assigned to a one out of four-week production cycle will be evenly divided across. When calculating the inventory policy, the distinction will not influence the resulting policy. We must next define the equations and key variables for the base stock policy. We will then also discuss how the JRP formulation fits into our base stock calculations. Here, we display the formula: ࠵?࠵?࠵?࠵?࠵?࠵? ࠵?࠵?࠵?࠵?࠵? ࠵?࠵? ࠵?࠵?࠵?࠵?࠵?࠵?࠵?࠵?࠵? = ࠵? ∙ ࠵?
7
+ ࠵?࠵?
7
√࠵?
(Eq.4)
Your preview ends here
Eager to read complete document? Join bartleby learn and gain access to the full version
- Access to all documents
- Unlimited textbook solutions
- 24/7 expert homework help
22 Eq.4 can be broken into two terms: the cycle stock term, ࠵?
T
,
and safety stock terms, ࠵?࠵?
7
√࠵?
.
R
represents the review period under which we assess our inventory and make decisions to replenish. We will use weeks as a unit of measure to explain review period. ࠵?
represents the average demand, in the same units of measure as the review period and all other variables. For this analysis, it will represent average weekly demand. ࠵?
represents the cycle service level we maintain for the downstream customers. It is calculated by taking the inverse of the cumulative distribution function of the normal distribution for a given service level, for example 95%. In this project, we assume a 99% service level. ࠵?
represents the standard deviation of weekly demand. ࠵?
represents the lead time for each item. This variable is the link between the JRP calculation and the base stock policy. ࠵?
will take one of three values in our calculations for the distribution center, based on how frequently it is produced. If a SKU is produced weekly, ࠵? = 1
. If a SKU is produced every other week, ࠵? = 2
. If a SKU is produced one out of four weeks, ࠵? = 4
. For the distributors, ࠵? = 2
for all SKUs. This is because distributors place weekly orders which deliver in two weeks. We then calculate the base stock for all SKUs at the distribution center as well as each distributor serviced by the distribution center. This completes the heuristic used to determine production frequencies and link them to inventory policies across the multi-echelon supply chain of MillerCoors.
Your preview ends here
Eager to read complete document? Join bartleby learn and gain access to the full version
- Access to all documents
- Unlimited textbook solutions
- 24/7 expert homework help
23 4. Case Study In this section, we introduce an industry case study to demonstrate the application of our approach. This will help motivate the analytical approach and provide real-world context which supports the relevance of our research.
4.1 The Company Our case study focuses on the operations of MillerCoors. MillerCoors is the United States business unit of Molson Coors (NYSE: TAP). Molson Coors is broken down into four different business units: MillerCoors, Molson Coors Canada, Molson Coors International, and Molson Coors Europe. According to the 2018 Q4 Molson Coors earnings release, MillerCoors makes up roughly 65% of the net sales of Molson Coors (Swartzber & Wheeler, 2019). MillerCoors formed in 2008 as a joint venture between SABMiller and Molson Coors. In 2016, as AB InBev expressed interest in acquiring the international portion of SABMiller’s business, the joint venture ended and MillerCoors became wholly owned by Molson Coors. In the United States market, MillerCoors is the second largest brewery behind AB InBev. MillerCoors produces 64 million hectoliters (54.7 million barrels) annually. One barrel is equivalent to 31 gallons, or 14 case equivalents (United States Tax and Trade Bureau, Title 27 – Alcohol, Tobacco Products and Firearms, 2019). They produce a wide variety of beers, ciders, and flavored malt beverages. Examples of brands MillerCoors produces are Coors Light, Miller Lite, Blue Moon, Leinenkugel’s, Crispin Cider, Arnold Palmer Spiked, and Henry’s Hard Sparkling Water. 4.2 The Supply Chain The alcoholic beverage industry in the US requires a three-tier distribution system. The three-tier system involves a manufacturer, distributor, and retailer. The manufacturer brews,
Your preview ends here
Eager to read complete document? Join bartleby learn and gain access to the full version
- Access to all documents
- Unlimited textbook solutions
- 24/7 expert homework help
24 packs, and ships beer to distributors. Distributors then fulfill the demand at various retail outlets including restaurants, bars, grocery stores, and convenience stores. Within these supply chains, distributors, rather than the manufacturers, typically manage and maintain the inventories of finished goods. This is because manufacturers are restricted by law from selling beer directly to consumers. This presents unique issues and challenges for the supply chain. Each tier must collaborate and communicate closely in order to be successful. The MillerCoors brewery network consists of seven large breweries and six regional craft breweries. The large breweries are located in Elkton, VA; Albany, GA; Fort Worth, TX; Irwindale, CA; Golden, CO; Milwaukee, WI; and Trenton, OH. These breweries are strategically located to efficiently satisfy demand in all of the markets across the US. Each brewery has a production cadence, or run strategy, for each SKU they produce because of the limited storage capacity in brewery warehouses. MillerCoors seeks to improve the connection between their run strategies and the inventory deployment across the three-tier system. In MillerCoors’ current supply chain, distributors own 95% of the finished goods inventory. MillerCoors brewery warehouses are not designed to store high volumes of inventory and on average turn their inventory in less than three days. This forces operations to produce in a make-
to-order model. MillerCoors is making the strategic move to buffer distributors from the breweries’ run strategies by opening distribution centers (DCs) at each of its facilities to fulfill distributor demand amidst growing portfolio complexity. MillerCoors operates DCs in Golden, CO, Portland, OR, Elkton, VA, Albany, GA, Milwaukee, WI, Elizabeth, NJ, and Fort Worth, TX, to fulfill demand within their orbits. Orbit refers to the specific set of nodes and arcs which satisfy demand from a brewery or DC origin to a distributor destination. 4.3 The Golden Brewery Business Unit
Your preview ends here
Eager to read complete document? Join bartleby learn and gain access to the full version
- Access to all documents
- Unlimited textbook solutions
- 24/7 expert homework help
25 This research focuses on the most complex operation within the MillerCoors supply chain, the Golden Brewery, and its orbit within the MillerCoors network. Orbit refers to the collection of arcs and nodes that connect the Golden Brewery to three DCs and 519 distributors. The Golden Brewery produces 18% of MillerCoors’ annual volume and supplies approximately 1,000 unique SKUs. This is a mature supply chain that provides ample data to support the research. More specifically, we will focus on products that flow from the Golden Brewery to the Golden Distribution Center to the distributors. 4.4 “3.2” Portfolio We are focusing on the “3.2” portion of the MillerCoors portfolio. “3.2” refers to the alcohol by volume (ABV) percentage of the products in this subset. During the early 1930’s, Franklin Roosevelt argued for a revision of the Volstead Act, which had previously restricted alcohol sales to products with less than .005% alcohol (National Institute on Alcohol Abuse and Alcoholism, Alcohol Policy Information System,2019). States were also given the liberty to choose their own alcohol policies, and legislators must grapple with the tax revenue pressures associated with keeping the laws in place. Because of this state legislature, alcohol beverage manufacturers wanting to sell in certain states needed to develop “3.2” versions of existing products. This adds a layer of complexity both from a supply chain perspective and commercial brand management perspective. For MillerCoors, brands like Blue Moon Belgian White, Coors Banquet, Foster’s, Miller Lite, Coors Light, and Keystone Light are produced in two different sales alcohol strengths to meet the legal requirements for the particular state it will be sold in. These brands are created, brewed, marketed, and sold at the brands alcohol target level, typically between 4%-5% ABV, in states allowing higher alcohol levels. For states with the “3.2” provisions, these brands are then adapted and produced to meet the state requirements, which
Your preview ends here
Eager to read complete document? Join bartleby learn and gain access to the full version
- Access to all documents
- Unlimited textbook solutions
- 24/7 expert homework help
26 adds complexity for the organization. We selected this portfolio for the research study because it contains a representative sample of brands and SKUs that flow through the supply chain in a similar fashion to the broader MillerCoors portfolio. This also enables us to narrow the scope of the project to a manageable size, which is easier to interpret and thus maximizes the insights we gain. The “3.2” portfolio represents roughly 5% of the total number of SKUs within MillerCoors’ portfolio. By limiting to these roughly 50 SKUs, we are able to generate generalizable results which can then be extended across the broader portfolio.
4.5 Current Processes MillerCoors, like most consumer goods companies, has experienced a steady increase in the number of products within their portfolio. As a result, the increase in complexity for the breweries has added a new dimension of capacity constraints. Breweries are now running many more SKUs, which require additional changeovers between products and results in a less efficient operation. To optimize this, MillerCoors developed a run strategy for every SKU. The run strategy corresponds to how frequently an SKU will be produced at each brewery. The run strategy defines a repeating four-week cycle. Thus, instead of planning the supply of products in monthly buckets, the team plans around thirteen four-week periods. To determine the appropriate run strategy, members of the supply chain and operations teams map the entire end-to-end production process. They identify critical processing steps, the capability of the system, and other factors that impact capacity. Once the team has a clear picture of the operation, they begin to balance and group SKUs together into the run strategy to optimize the brewery operations and improve the availability of SKUS to the distributors. The team then assigns the most appropriate classification for each SKU, as discussed in the literature review.
Your preview ends here
Eager to read complete document? Join bartleby learn and gain access to the full version
- Access to all documents
- Unlimited textbook solutions
- 24/7 expert homework help
27 An SKU can have one of seven different run strategies. The available run strategies are listed below: 1.
Produced weekly (Weeks 1, 2, 3, 4)
2.
Produced bi-weekly, on odd weeks (Weeks 1 and 3)
3.
Produced bi-weekly, on even weeks (Weeks 2 and 4)
4.
Produced one out of four weeks, on first odd (Week 1)
5.
Produced one out of four weeks, on first even (Week 2)
6.
Produced one out of four weeks, on second odd (Week 3)
7.
Produced one out of four weeks, on second even (Week 4)
The run strategies also help to satisfy run size constraints. For example, if a low-volume SKU were run weekly, it may not have enough demand volume to economically justify the production run. By assigning it to a different run strategy, the demand can be pooled in order to satisfy the minimum run size. The figure below displays the current run strategies for the “3.2” portfolio.
Your preview ends here
Eager to read complete document? Join bartleby learn and gain access to the full version
- Access to all documents
- Unlimited textbook solutions
- 24/7 expert homework help
28 Figure 2: Current SKU Run Strategies for “3.2” Portfolio Distributors place orders to MillerCoors weekly. The orders are delivered two weeks after the order is placed. MillerCoors recommends an inventory stocking level for each SKU at the distributor based on the run strategy. This is to ensure distributors have sufficient inventory on hand to fulfill sales to retailers. The recommended amount of inventory on the shelves increases for the broader production intervals. To illustrate, an SKU produced weekly will have a lower target inventory level than an SKU produced one out of every four weeks. MillerCoors has predefined inventory targets, expressed in days of inventory, based on the run strategies. For SKUs produced weekly, the inventory target is 7 days of inventory. For SKUs produced bi-
weekly, the inventory target is 14 days of inventory. For SKUs produced one-out-of-four weeks, the inventory target is 28 days of inventory. MillerCoors is opening additional distribution centers across the country that will enable distributors to order every SKU every week. In the past, distributors were restricted to ordering
Your preview ends here
Eager to read complete document? Join bartleby learn and gain access to the full version
- Access to all documents
- Unlimited textbook solutions
- 24/7 expert homework help
29 SKUs only as frequently as they were produced. The distribution center model facilitates an enhanced customer experience and may change the target inventory levels for each distributor. The strategy is to transform from a make-to-order model to a make-to-stock model. A make-to-
stock model leads to higher product availability, and increased customer satisfaction, while reducing lead times and inventories. Transitioning to a make-to-stock strategy may yield a different optimal run strategy and inventory policy than the current state of operations. The purpose of this case study is to determine how MillerCoors should deploy inventory across their network. This applies to existing distribution centers in the network as well as new facilities which MillerCoors opens. 5. Results and Analysis In this section we present the results of executing our heuristic against data provided by MillerCoors and compare them to the company’s current run strategy and inventory policy. Our focus remains on how to improve the current inventory deployment strategy by combining a joint replenishment approach with the base stock policy. Throughout the chapter, figures are provided to explain and support the results. We begin by discussing the run strategy assignments and then move to comparing the current state and proposed inventory policies. First, we interpret the results of the run strategy portion of the heuristic. Out of 54 SKUs analyzed our heuristic assigned 28 SKUs, 52%, to the same run strategy as the current state (shaded green below). Of the remaining 26 SKUs, 21 SKUs were assigned to a run strategy in the adjacent tier either one level up or down (shaded yellow below). For example, if under the current-state assignment a SKU was produced weekly, our heuristic assigned the same SKU to be produced every other week. 5 SKUs were assigned to a run strategy more than one tier away
Your preview ends here
Eager to read complete document? Join bartleby learn and gain access to the full version
- Access to all documents
- Unlimited textbook solutions
- 24/7 expert homework help
30 (shaded red). For example, if under the current-state assignment a SKU was produced weekly, our heuristic assigned the same SKU to be produced one out of four weeks. The table below shows a matrix comparing the recommended and actual run strategies. Actual Run Strategy 4wk Cycle Every Other Week Weekly Total Recommended Run Strategy 4wk Cycle 23 10 2 35 Every Other Week 9 2 0 11 Weekly 3 2 3 8 Total 35 14 5 Table 1: Recommended Run Strategy vs. Actual Run Strategy The results, and differences in assignment, can be stratified into three decision classes. The first decision class is the SKUs assigned to the same run strategy by both MillerCoors and the heuristic outlined in this capstone. These represent an agreement between theoretical calculations and practical applications and are near-optimal solutions. The insights we can derive from these results are that both the heuristic and MillerCoors processes converge at a near-optimal solution and there is little to no case for change to reassign these SKUs, unless a significant shift in volume or cost occurs. Next, we discuss the SKUs which were assigned to an adjacent run strategy. There are a few explanations for the discrepancies between the theoretical solution and the practical applications. The run strategies at MillerCoors are not determined within a vacuum. A cross-functional team collaborates, with representation from brewery operations as well as corporate supply chain, and gains a consensus decision on which run strategies to assign or change for the SKUs they discuss. During these discussions, the representatives from operations may call out line-specific or equipment capability considerations to influence the run strategy assignment. For SKUs within this decision class, the heuristic model can be used to facilitate and support discussions within the cross functional team about whether or not to reassign the SKUs. The
Your preview ends here
Eager to read complete document? Join bartleby learn and gain access to the full version
- Access to all documents
- Unlimited textbook solutions
- 24/7 expert homework help
31 model includes financial impact calculations so that the inventory adjustments can be better understood. We see the most significant financial benefits for high volume SKUs that are reassigned to a run strategy with a greater production frequency. This is driven primarily due to the reduction in ࠵?
, which reduces the safety stock required in the system. Furthermore, within this decision class, the heuristic model shows that the greatest improvements occur when reassigning a SKU from a one-in-four-week cadence to a bi-weekly cadence. Finally, we discuss the third decision class. This class includes SKUs which were assigned to a weekly run strategy by MillerCoors but a one-in-four week run strategy by the heuristic, or vice versa. SKUs within this decision class need to be further analyzed. As mentioned before, by decreasing ࠵?
, we can reduce the on-hand inventory required under a base stock policy. The heuristic exposes these discrepancies, particularly on high-volume SKUs assigned to a one-in-
four week policy by MillerCoors. Over 30% of the total estimated financial impact to reassigning run strategies is captured by three SKUs within this decision class. All three of the SKUs shifted to a weekly run strategy based on the heuristic model. Other factors that may have influenced the discrepancies between the heuristic solution and MillerCoors assignments, which are not included in the model, are minimum run size constraints and minimum order quantities for distributors. These also may influence the results but based on the shifts identified in this model and the volume of each of those SKUs, we do not find the influence significant. We will now shift our focus to the inventory policy results of our heuristic. Under the base stock policy, all SKUs ordered by distributors have the same value for ࠵?
, which is 2. This is because distributors receive their orders from the distribution center two weeks after placing their orders. Currently, MillerCoors uses a blanket inventory policy for SKUs based on the run strategies. This originates from the structure of the supply chain prior to a couple key
Your preview ends here
Eager to read complete document? Join bartleby learn and gain access to the full version
- Access to all documents
- Unlimited textbook solutions
- 24/7 expert homework help
32 organizational transformations. One transformation, as outlined earlier, is the expansion of the MillerCoors’ owned distribution center network. This enables a shift to an indirect fulfillment model instead of a direct brewery to distributor path. As a result, the distributors are less impacted by the run strategies at the breweries since the distribution centers carry inventory to fulfill demand. The other major transformation is the consolidation of legacy ordering systems into a single ordering tool. Prior to this transformation, the ordering frequencies were anywhere from one week to one month. Because of this variation, the organization required a one-size-fits all inventory solution so that humans could efficiently manage the inventories. Our analysis shows that when comparing the new base stock policies to the current run-
strategy driven policies, we will increase the inventory of 20% of the SKUs analyzed and reduce the inventory of 80% of the SKUs. Figure 3: Distributor Change in DOI
Your preview ends here
Eager to read complete document? Join bartleby learn and gain access to the full version
- Access to all documents
- Unlimited textbook solutions
- 24/7 expert homework help
33 The total inventory increase is approximately 2,800 barrels and the reduction is approximately 8,600 barrels. Figure 4: Distributor Change in Barrels We are not calculating any costs of inventory reduction for the distributors, because MillerCoors does not own this subset of inventory. The policy instead provides stock coverage to satisfy 99% of the fluctuations in weekly demand. The shifts in the model show us that in some cases MillerCoors deployed excess inventory to distributors and in others deployed insufficient inventory. As is typically the case when discussing inventory, the total aggregate inventory amount is generally correct, but a mismatch occurs at the individual product level.
Your preview ends here
Eager to read complete document? Join bartleby learn and gain access to the full version
- Access to all documents
- Unlimited textbook solutions
- 24/7 expert homework help
34 The heuristic developed in this project addresses the aforementioned imbalance while maintaining high customer service levels.
Your preview ends here
Eager to read complete document? Join bartleby learn and gain access to the full version
- Access to all documents
- Unlimited textbook solutions
- 24/7 expert homework help
35 6. Conclusion and Managerial Insights In this chapter, we summarize the key insights and managerial implications derived from our research. This project develops a heuristic to combine joint replenishment with the base stock policy to improve the inventory policy of the multi-echelon supply chain at MillerCoors. Three key insights emerge from our data analysis. First, by engaging a MillerCoors-owned distribution center tier in the supply chain between the brewery and its customers, the supply chain absorbs the variation in run strategies for each SKU and smooths the inventory planning process for the distributors. This is especially important for low-volume, high-complexity SKUs. This is important because it helps facilitate MillerCoors’ strategic transition to a make-to-stock model, for the aforementioned low-volume, high-complexity SKUS, while still maintaining the shelf-life commitments associated with perishable products. Second, implementing a base stock policy for distributors improves the alignment between demand and inventory. This is important because both cycle stock and safety stock are now tied to the replenishment cycle from the distribution center rather than the run strategy cycle. Inventory levels are also more closely aligned to how each SKU flows through the distributor’s supply chain rather than MillerCoors’ supply chain. The base stock policy also allows the supply chain to determine the cycle service level to deliver and make adjustments to inventory accordingly. Lastly, this heuristic provides change management tools to facilitate conversations between MillerCoors and the distributors. The supply chain technology transformation, which aligned all ordering frequencies for SKUs sourced from a DC to a weekly cadence, also cultivated discussions around inventory levels. The more frequent order frequency tends to lead
Your preview ends here
Eager to read complete document? Join bartleby learn and gain access to the full version
- Access to all documents
- Unlimited textbook solutions
- 24/7 expert homework help
36 to lower required inventory levels. However, with a two-week lead time on all SKUs, seven days of coverage may lead to stockout situations under current inventory strategies. This heuristic provides numerical justification for proposed increases and decreases to inventory balances. Future research could expand on this heuristic by including transportation-related costs and variables. Other extensions could involve introducing different sourcing strategies and additional distribution centers into the system. Overall, this heuristic improves the alignment of the production run strategies with the inventory deployed across all three tiers of the supply chain at MillerCoors. By leveraging the distribution center tier, the entire supply chain benefits.
Your preview ends here
Eager to read complete document? Join bartleby learn and gain access to the full version
- Access to all documents
- Unlimited textbook solutions
- 24/7 expert homework help
37 References Amaya, C. A., Carvajal, J., & Castaño, F. (2013). A heuristic framework based on linear programming to solve the constrained joint replenishment problem (C-JRP). International Journal of Production Economics
, 144
(1), 243–247. https://doi.org/10.1016/j.ijpe.2013.02.008 Amiri, M., Seifbarghy, M., Olfat, L., & Hajiagha, S. H. (2012). Determination of a Desirable Inventory Policy in a three Echelon Multilayer Supply Chain with Normal Demand. International Journal of Industrial Engineering
, 23
(1), 65–72. Retrieved from http://www.iust.ac.ir/ijieen/files/site1/user_files_2hops2/admin-A-10-1-134-24447d2.pdf Bayindir, Z. P., Birbil, Ş
. I., & Frenk, J. B. G. (2006). The joint replenishment problem with variable production costs. European Journal of Operational Research
, 175
(1), 622–640. https://doi.org/10.1016/j.ejor.2005.06.005 Charnes, A., Cooper, W. W., Seiford, L. M., & Tone, K. (1994). Data Envelopment Analysis: Theory
. Data Envelopment Analysis: A Comprehensive Text with Models, Applications, References and DEA-Solver Software: Second Edition
. https://doi.org/10.1007/978-0-387-
45283-8 Chopra, S., & Meindl, P. (2013). Supply Chain Management: Strategy, Planning, and Operation
(Fifth Edit). de Kok, T., Grob, C., Laumanns, M., Minner, S., Rambau, J., & Schade, K. (2018). A typology and literature review on stochastic multi-echelon inventory models. European Journal of Operational Research
, 269
(3), 955–983. https://doi.org/10.1016/j.ejor.2018.02.047 Eruguz, A. S., Jemai, Z., Sahin, E., & Dallery, Y. (2014). Optimising reorder intervals and order-
up-to levels in guaranteed service supply chains. International Journal of Production Research
, 52
(1), 149–164. https://doi.org/10.1080/00207543.2013.831188 Eruguz, A. S., Sahin, E., Jemai, Z., & Dallery, Y. (2016). A comprehensive survey of guaranteed-service models for multi-echelon inventory optimization. International Journal of Production Economics
, 172
, 110–125. https://doi.org/10.1016/j.ijpe.2015.11.017 Fichtinger, J., Chan, C. (Wan-C., & Yates, N. (2017). A joint network design and multi-echelon inventory optimisation approach for segmentation. International Journal of Production Economics
, 3
(2), 64. https://doi.org/10.1016/j.ijpe.2017.09.003 Flores, B. E., Olson, D. L., & Dorai, V. K. (1992). Management of multicriteria inventory classification. Mathematical and Computer Modelling
, 16
(12), 71–82. https://doi.org/10.1016/0895-7177(92)90021-C Giacomantonio, R. (2013). Multi-Echelon Inventory Optimization in a Rapid-Response Supply Chain. MIT Sloan School of Management
, 168. Graves, S. C., & Schoenmeyr, T. (2016). Strategic Safety-Stock Placement in Supply Chains with Capacity Constraints. Manufacturing & Service Operations Management
, 18
(3), 445–
460. https://doi.org/10.1287/msom.2016.0577 Graves, S. C., & Willems, S. P. (2003). Erratum: Optimizing Strategic Safety Stock Placement in
Your preview ends here
Eager to read complete document? Join bartleby learn and gain access to the full version
- Access to all documents
- Unlimited textbook solutions
- 24/7 expert homework help
38 Supply Chains. Manufacturing & Service Operations Management
, 5
(2), 176–177. https://doi.org/10.1287/msom.5.2.176.16074 Gupta, H. (2008). Network Design and Safety Stock Placement for a Multi-Echelon Supply Chain, 80. Hadi-Vencheh, A., & Mohamadghasemi, A. (2011). A fuzzy AHP-DEA approach for multiple criteria ABC inventory classification. Expert Systems with Applications
, 38
(4), 3346–3352. https://doi.org/10.1016/j.eswa.2010.08.119 Hatami-Marbini, A., Emrouznejad, A., & Tavana, M. (2011). A taxonomy and review of the fuzzy data envelopment analysis literature: Two decades in the making. European Journal of Operational Research
, 214
(3), 457–472. https://doi.org/10.1016/j.ejor.2011.02.001 Hatefi, S. M., Torabi, S. A., & Bagheri, P. (2014). Multi-criteria ABC inventory classification with mixed quantitative and qualitative criteria. International Journal of Production Research
, 52
(3), 776–786. https://doi.org/10.1080/00207543.2013.838328 Ishizaka, A., Lolli, F., Balugani, E., Cavallieri, R., & Gamberini, R. (2018). DEASort: Assigning items with data envelopment analysis in ABC classes. International Journal of Production Economics
, 199
(February), 7–15. https://doi.org/10.1016/j.ijpe.2018.02.007 Kenton, W. (2019, March 12). Pareto Principle. Retrieved from https://www.investopedia.com/terms/p/paretoprinciple.asp Khouja, M., & Goyal, S. (2008). A review of the joint replenishment problem literature: 1989-
2005. European Journal of Operational Research
, 186
(1), 1–16. https://doi.org/10.1016/j.ejor.2007.03.007 Klosterhalfen, S. T., Dittmar, D., & Minner, S. (2013). An integrated guaranteed- and stochastic-
service approach to inventory optimization in supply chains. European Journal of Operational Research
, 231
(1), 109–119. https://doi.org/10.1016/j.ejor.2013.05.032 Ladhari, T., Babai, M. Z., & Lajili, I. (2013). Multi-criteria inventory classification: new consensual procedures. IMA Journal of Management Mathematics
, (March 2015), 483. https://doi.org/10.1093/imaman/dpv003 Li, F., & Liu, Y. (2010). Modelling Supply Chain Multi-echelon Inventory Control, 265–273. Liu, Q., & Huang, D. (2006). Classifying ABC inventory with multicriteria using a data envelopment analysis approach. Proceedings - ISDA 2006: Sixth International Conference on Intelligent Systems Design and Applications
, 1
, 1185–1190. https://doi.org/10.1109/ISDA.2006.122 Lolli, F., Ishizaka, A., Gamberini, R., Balugani, E., & Rimini, B. (2017). Decision Trees for Supervised Multi-criteria Inventory Classification. Procedia Manufacturing
, 11
(June), 1871–1881. https://doi.org/10.1016/j.promfg.2017.07.326 Millstein, M. A., Yang, L., & Li, H. (2014). Optimizing ABC inventory grouping decisions. International Journal of Production Economics
, 148
, 71–80. https://doi.org/10.1016/j.ijpe.2013.11.007
Your preview ends here
Eager to read complete document? Join bartleby learn and gain access to the full version
- Access to all documents
- Unlimited textbook solutions
- 24/7 expert homework help
39 Moon, I. K., & Cha, B. C. (2006). The joint replenishment problem with resource restriction. European Journal of Operational Research
, 173
(1), 190–198. https://doi.org/10.1016/j.ejor.2004.11.020 National Institute on Alcohol Abuse and Alcoholism. (2019). Alcohol Policy Information System. Retrieved from https://alcoholpolicy.niaaa.nih.gov/beer-with-an-alcohol-content-
of-32-percent-or-less
. Ng, W. L. (2007). A simple classifier for multiple criteria ABC analysis. European Journal of Operational Research
, 177
(1), 344–353. https://doi.org/10.1016/j.ejor.2005.11.018 Ongkunaruk, P., Wahab, M. I. M., & Chen, Y. (2016). A genetic algorithm for a joint replenishment problem with resource and shipment constraints and defective items. International Journal of Production Economics
, 175
, 142–152. https://doi.org/10.1016/j.ijpe.2016.02.012 Porras, E., & Dekker, R. (2006). An efficient optimal solution method for the joint replenishment problem with minimum order quantities. European Journal of Operational Research
, 174
(3), 1595–1615. https://doi.org/10.1016/j.ejor.2005.02.056 Ramanathan, R. (2006). ABC inventory classification with multiple-criteria using weighted linear optimization. Computers and Operations Research
, 33
(3), 695–700. https://doi.org/10.1016/j.cor.2004.07.014 Ravinder, H., & Ph, D. (2015). Multi-criteria Inventory Categorization
: A Review of the Literature. Academy of Business Research Journal
, 3
, 39–53. Sbai, N., & Berrado, A. (2018). A literature review on multi-echelon inventory management
: the case of pharmaceutical supply chain, 00013
. Scott, P., & Xu, B. (2017). Multi-Echelon Inventory Modeling and Supply Redesign, 1–49. Silva, F., & Gao, L. (2013). A Joint Replenishment Inventory-Location Model. Networks and Spatial Economics
, 13
(1), 107–122. https://doi.org/10.1007/s11067-012-9174-2 Swartzberg, M., & Wheeler, C. (2019, February 12). Molson Coors Reports 2018 Full Year and Fourth Quarter Results. Retrieved from https://www.businesswire.com/news/home/20190212005444/en/ Tjhin, P. C., & Pandey, R. (2012). Inventory management strategy for the supply chain of a medical device company, 1–98. Retrieved from http://oatd.org/oatd/record?record=%22handle:1721.1/77474%22 United States Taxes and Trade Bureau. (2019). Title 27 – Alcohol, Tobacco Products, and Firearms. Retrieved from https://www.ttb.gov/spirits/regs/27cfr25.html
. Yu, M. C. (2011). Multi-criteria ABC analysis using artificial-intelligence-based classification techniques. Expert Systems with Applications
, 38
(4), 3416–3421. https://doi.org/10.1016/j.eswa.2010.08.127
Your preview ends here
Eager to read complete document? Join bartleby learn and gain access to the full version
- Access to all documents
- Unlimited textbook solutions
- 24/7 expert homework help
Related Documents
Recommended textbooks for you
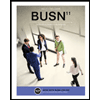
BUSN 11 Introduction to Business Student Edition
Business
ISBN:9781337407137
Author:Kelly
Publisher:Cengage Learning
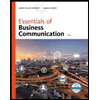
Essentials of Business Communication (MindTap Cou...
Business
ISBN:9781337386494
Author:Mary Ellen Guffey, Dana Loewy
Publisher:Cengage Learning
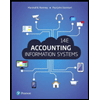
Accounting Information Systems (14th Edition)
Business
ISBN:9780134474021
Author:Marshall B. Romney, Paul J. Steinbart
Publisher:PEARSON
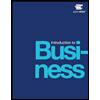
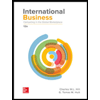
International Business: Competing in the Global M...
Business
ISBN:9781259929441
Author:Charles W. L. Hill Dr, G. Tomas M. Hult
Publisher:McGraw-Hill Education
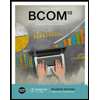
Recommended textbooks for you
- BUSN 11 Introduction to Business Student EditionBusinessISBN:9781337407137Author:KellyPublisher:Cengage LearningEssentials of Business Communication (MindTap Cou...BusinessISBN:9781337386494Author:Mary Ellen Guffey, Dana LoewyPublisher:Cengage LearningAccounting Information Systems (14th Edition)BusinessISBN:9780134474021Author:Marshall B. Romney, Paul J. SteinbartPublisher:PEARSON
- International Business: Competing in the Global M...BusinessISBN:9781259929441Author:Charles W. L. Hill Dr, G. Tomas M. HultPublisher:McGraw-Hill Education
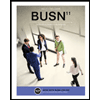
BUSN 11 Introduction to Business Student Edition
Business
ISBN:9781337407137
Author:Kelly
Publisher:Cengage Learning
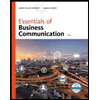
Essentials of Business Communication (MindTap Cou...
Business
ISBN:9781337386494
Author:Mary Ellen Guffey, Dana Loewy
Publisher:Cengage Learning
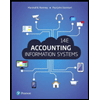
Accounting Information Systems (14th Edition)
Business
ISBN:9780134474021
Author:Marshall B. Romney, Paul J. Steinbart
Publisher:PEARSON
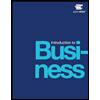
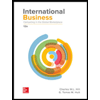
International Business: Competing in the Global M...
Business
ISBN:9781259929441
Author:Charles W. L. Hill Dr, G. Tomas M. Hult
Publisher:McGraw-Hill Education
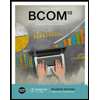