1 Describe the
docx
keyboard_arrow_up
School
Einstein College of Australia *
*We aren’t endorsed by this school
Course
113
Subject
Accounting
Date
May 21, 2024
Type
docx
Pages
6
Uploaded by ElderMeerkat4444
1. Describe the FIFO principle.
A technique for storing and rotating food is called first in, first out (FIFO). The food that has been
in storage the longest ("first in") should be the next food utilised ("first out") in a FIFO system.
This technique assists households and restaurants in organising their food storage and in using
food before it spoils
Explain how regular inventory checks can support rock rotation and replenishment.
Stock rotation is a way of minimizing potential stock loss due to expiration. When rotating stock
be sure to use the FIFO rule, and also verify expiration on all products. In some cases, you may
receive a shorter dated product then the one on the shelf. How does this happen? Sometimes
the wholesaler has made an error on FIFO, or may be trying to push their product out to you so
they don't encounter the
loss. Sometimes short items are sold to buyers at a lower cost so that the buyer can maximize
profits and the seller can minimize loss. If a stock item is nearing its sell-by date, stock may be
reduced. Its price is lowered in order to be more appealing to customers. Reduced stock is usually
included in the rotation of stock, and is therefore moved to the front of the shelf ahead of any
unreduced stock. In most cases you may consider not replenishing this item, removing it from
your inventory and removing the order sticker, or changing your reorder point on your POS. Be
sure to check with your wholesaler on the return policy and capitalize on the benefits of
returning versus discounting, or how much to discount based on how much you will get just
returning it
3. Describe the product life cycle (PLC) and cover the four stages in your answer.
A product's life cycle is the period of time between its initial consumer introduction and its
eventual removal from the market. It is often divided into four stages: introduction, growth,
maturity, and decline.
4. What is meant by the term slow-moving item?
Items that move slowly are those that have a low turnover rate and are kept in the warehouse for
a lengthy time. The reason why slow-moving products are stored or take up a lot of room is
because they sell slowly
5. LIst four reasons why an item may become a slow-moving item
This problem can be brought on by a number of things, including inaccurate sales projections, a
slowing market, aggressive rival promotions, or even your procurement team's desire to acquire
more products in order to reduce per-unit costs. 6. List two ways that you can check
for slow-moving items.
Every day, spot-check four inventory items.
Do the math for inventory turnover.
• Examine the typical days to sell (or use).
Analyse the storage costs for inventory items.
Utilise sales data to forecast trends.
®.X
TEACHERS
HEALTHY
7
Segregation of food items and non-food items reduces the risk of contamination. List three
strategies you can apply to ensure these items remain segregated.
• A bin for wet waste like leftover food, vegetable or fruit peels, tea bags, etc.
Dry waste should be further divided into plastic, metal, glass and paper.
Electronic waste like CDs, pen drives, bulbs, tube-lights, computer systems, electric cables,
keyboards, batteries, motherboards etc.
Describe each of the following inventory systems:
a) Ledger inventory system: A physical or digital record called an inventory ledger keeps track of
inventory transactions. All transactions recorded in this ledger should add up to the same amount
as the relevant account's total in the general ledger.
b) Integrated point-of-sale system: An integrated POS links the software and hardware used by
your company to handle payments, such as a credit card reader and inventory management
systems. Your payment system may become more effective and linked thanks to this connection
9. List the key procedures involved in ordering stock. Briefly explain what happens at each stage.
Order processing, a crucial component of order fulfilment, is the workflow that guarantees client
orders are accurately processed and delivered to the appropriate location. Order processing may
be carried out by a single person or small group, depending on the size of a company's activities,
or it may take place at a distribution centre or warehouse where pickers, sorters, and packers
collaborate to execute orders. Order placement: When a consumer places an order, the
company normally sends the order's data, such as the goods, quantities, shipping information,
and delivery addresses, to an order management system. Based on the delivery address and item
availability, the OMS will automatically choose the best warehouse location to ship from if the
business has several fulfilment centres or warehouse locations. Both delivery costs and travel
times are lowered as a
result. • Picking inventory: The act of removing a certain number of products from stock in order
to fill client orders. Because it directly affects the efficiency of the whole order processing
workflow, order picking must be a tightly regulated procedure. The faster orders are correctly
chosen, the faster they may be packed and sent.
• Sorting: During this step, selected things are divided into groups based on where they will be
used. For instance, each item must be sorted into its proper order before it can be packaged and
dispatched if zone or batch picking techniques are utilised.
• Packing: The act of placing products into suitable shipping boxes in a protected manner. Along
with weighing the parcels and labelling them with the recipients' addresses and any relevant
delivery instructions, packing also include packaging.
10. List two ways that an order for stock may be made.
Market orders and limit orders are the two primary forms of orders that investors can use to
purchase or sell stocks. Market orders frequently execute instantly at the current market price.
Limit orders won't go into effect until the market price reaches the investor's desired price.
11. List four pieces of information you would expect to see in a loss/wastage log or report.
Record how much is being wasted.
If you have a scale, the best option is to place the food in an empty bus tub and weigh the waste.
Record its weight in the logbook (including the weight of the bus tub). Later, a manager can
subtract the known tare weight of the bus tub.
If you do not have a scale, record the number of portions leftover or the volume (1/2 a pot, 2
gallons, etc.)
Chefs and Managers should review yesterday's waste logbook at the beginning of the following
day's shift.
The top 5 waste items should be discussed with the kitchen team at a pre-shift meeting. Ask the
team for ideas to reduce those items.
12. Why is it important to ensure that loss and wastage of items is reflected in the inventory
system?
Increases profitability and makes sure you can complete open or incoming orders. Additionally,
inventory management saves money. Understanding stock trends can help you better utilise the
stock you already have by allowing you to know how much and where you have it in stock.
13. Answer Count things up. Before you go shopping, take stock of what you already have in your
pantry, refrigerator, and freezer to avoid overspending.
Plan your meals.
Safely store and consume leftovers.
Your preview ends here
Eager to read complete document? Join bartleby learn and gain access to the full version
- Access to all documents
- Unlimited textbook solutions
- 24/7 expert homework help
• Food should be properly stored.
14. Explain the purpose of stock level reports.
A stock report has two main advantages: it can track crucial levels and provide replenishment
notifications in addition to that.
15. Explain the purpose of stock movement reports.
Report breaks out the individual sales invoices for each of your customers so you can discover
which clients are purchasing specific stock items.
16. List three types of information you would find in a supplier agreement.
Offer
Acceptance
• Consideration
17. Explain the purpose of stock valuation reports.
Stock valuation is a technique for figuring out a stock's intrinsic value, or theoretical worth. The
significance of stock valuation arises from the possibility that a stock's intrinsic value may differ
from its market price.
18. List two procedures that are appropriate to monitoring and maintaining stock reorder cycles
Reorder cycles, often known as cyclical reviews, include ordering at set, predictable intervals. A
technique for inventory control may be built using different arrangements of these systems. For
instance, cyclical stock reviews rather than ongoing ones might be required for a pure two-bin
system.
19. List two types of stock control systems used and their functions and features.
Periodic Inventory Control System:
Perpetual Inventory Control System: 20. Choose three items relevant to the area of hospitality
you are studying and explain how you would monitor them for quality.
Food and beverages, lodging, recreation, travel and tourism, and meetings and events
21. List two pieces of documentation that may be referred to during the delivery of stock.
Delivery documents generally provide the delivery instructions for an order or trip and specify
the products and quantities to deliver.
22. Briefly outline the procedures involved in taking receipt of stock.
It is appropriate procedure to check the package for visible damage before confirming that the
contents match the packing list and signing and dating the packing list as confirmation of delivery.
To guarantee correctness, the products should then be tallied and compared to the purchase
order.
23. List two stock security systems that a hospitality business may have in place to reduce risk of
theft?
Install technology to monitor storage
Count all stock items twice upon delivery
• Review each days transactions records
24. Briefly the purpose of barcodes and scanners, as well as how they are used as part of stock
control.
Product data is gathered via barcode scanners and then added to the customer's order total.
Barcode scanners are used in supply chain applications by inventory management systems to
monitor items from the moment they are received in the warehouse until they are sent out.
25. Outline the procedures involved in planning and running a stock take.
Download
• Decide how frequently to take stock. There is no getting aroun takes time and effort.
• Print vour inventory forms.
AD Before the stock take, organise your inventory. • Decide how frequently to take stock.
There is no getting around the reality that taking a stock takes time and effort.
• Print your inventory forms.
• Before the stock take, organise your inventory.
• Organise the workers.
• Stock management doesn't include making assumptions.
• Validate your inventory. 26. Explain how you can use the reports generated from a stock
take to help with stock control in future.
Developing a comprehensive program for minimizing stock losses.
Investing more time and resources in stock control processes.
Training staff members to minimize losses
27. Explain why correct ventilation, temperature control and humidity control can protect stock
from damage and spoilage.
Storage area should be completely free of sunlight, kept a cool temperature consistently, and
have exposure to minimal humidity levels. In fact, humidity levels should not exceed 50-55% in
order to keep food safe long term. The idea temperature range for dry storage is between 50 to
70 degrees Fahrenheit.
28. Explain how you can protect stock from damage by treating for vermin infestation.
• Dispose of food scraps promptly and clean food preparation areas thoroughly.
• Inspect living
and working areas for potential rodent
entrances and
them where possible with concrete, hard setting filler, steel wool or heavy gauge sheet metal.
block
• Ensure rubbish bins have tight-fitting lids and are regularly emptied.
Keep your home and property clear of rubbish.
Keep stacked materials such as wood and bricks at least 30cm above the ground to minimise
hiding / nesting / thoroughfare of rats and mice.
• Regularly clean out sheds, storage areas and dispose of unwanted items.
• Remove unwanted undergrowth - cut back grass, trees, bushes, and creepers which may
provide cover or access to the roof.
• Dispose of fallen fruit, seed and waste from aviaries and chicken pens and pet faces.
• Do not use open compost heaps.
Your preview ends here
Eager to read complete document? Join bartleby learn and gain access to the full version
- Access to all documents
- Unlimited textbook solutions
- 24/7 expert homework help
Related Documents
Related Questions
A company is trying to set up proper internal controls for their accounts payable/inventory purchasing system. Currently the purchase order is generated by the same person who receives the inventory. Together the purchase order and the receiving ticket are sent to accounts payable for payment. What changes would you make to improve the internal control structure?
Group of answer choices
1.The person in accounts payable should generate the purchase order.
2.The person in accounts payable should generate the receiving ticket once the invoice from the supplier is received.
3.No changes would be made since the person paying the bills is different from the person ordering the inventory.
4.The responsibilities of generating the purchase order and receiving the inventory should be separated among two different people.
arrow_forward
Keeping track of inventory and keeping carrying costs down. How do you think those issues would influence warehousing decisions? What might retailers do to reduce warehouse space and increase inventory accountability?
arrow_forward
Need Help on the following question.
Question #1
You have been hired by the CEO of a soon-to-be-opened bookstore to develop procedures to help control inventory. List, describe, and defend four procedures you recommend be implemented to control inventory. As part of your response, be sure to describe any potential costs associated with these procedures.
arrow_forward
Need both parts.........
arrow_forward
. A company that uses a just in time inventory system: A) has finished goods inventory on hand at all times in order to speed up shipments of customer orders. B) may find that having less inventory actually leads to increased customer satisfaction. C) assesses its value chain to create new value-added activities. D) adopts a systematic, problem-solving attitude
arrow_forward
The business rules that constitute the purchases system for the Safe Buy Grocery Stores chain are similar at all the store locations. The purchase manager at each location is responsible for selecting his or her local suppliers. If the manager needs a product, he or she chooses a supplier. Each store follows the steps described here.1. The purchasing function begins with sales representatives from suppliers periodically observing the shelves and displays at each location and recognizing the need to restock inventory. Inventory declines by direct sales to the customers or by spoilage of perishable goods. In addition, the supplier’s sales representatives review obsolescence reports that the purchase manager prepares. These reports identify slow-moving and dated products that are deemed unsalable at a particular location. These products are returned to the supplier and replaced with more successful products. The sales representatives prepare a hard-copy purchase requisition and meet with…
arrow_forward
Please answer multichoice question in photo
arrow_forward
Which of the following is least likely to affect the preparation of the purchases budget?
A.The amount of inventory stock available to purchase from suppliers.
B.How easy it is to transport inventory from delivery trucks to the warehouse.
C.The amount of warehouse space available.
D.The shelf life of inventory.
arrow_forward
OLTP VERSUS OLAP SERVERS
For each of the following processes, state whether OLTP or OLAP is appropriate, and why.
An order entry system that retrieves customer information, invoice information, and inventory information for local sales.
An order entry system that retrieves customer information, invoice information, inventory information, and several years of sales information about both the customer and the inventory items. An order entry system that retrieves customer information, invoice information, inventory information, and information to compare the current sale to sales across several geographic regions.
An order entry system that retrieves customer information, invoice information, inventory information, and accounts receivable information for sales within one marketing region.
An insurance company requires a system that will allow it to determine total claims by region, whether a relationship exists between claims and meteorological phenomena, and why one region seems to be…
arrow_forward
How are duplicate checks useful in determining expected food revenue in nonautomated food
operations?
arrow_forward
.Internal Controls and RiskReview the following description of the purchasing and AP procedures for a company and answer the questions at the end.The purchasing agent receives an inventory status report on his computer terminal from the inventory control application, which identifies the items that need to be reordered. The agent selects the suppliers and enters this information into the computer terminal to create a digital purchase order. He then prints and sends a copy of the PO to the supplier.When the goods are received directly into the warehouse, the warehouse manager counts and inspects them. The manager then creates a digital receiving report and updates the inventory subsidiary ledger from the warehouse terminal.A few days later, the supplier sends an invoice to the AP clerk who reconciles it with the digital copy of the receiving report. From her computer terminal, the clerk records the purchase in the purchases journal and records the liability by adding a record to the AP…
arrow_forward
Explain the difference between the Perpetual and Periodic inventory systems and let us know why anyone would use Periodic inventory in this computerized age.
arrow_forward
Please help me.
Thankyou.
arrow_forward
The following is an excerpt from a conversation between the store manager of Wholesome Grocery Stores, Kara Dahl, and Lynn Shutes, president of Wholesome Grocery Stores:Lynn: Kara, I’m concerned about this new scanning system.Kara: What’s the problem?Lynn: Well, how do we know the clerks are ringing up all the merchandise?Kara: That’s one of the strong points about the system. The scanner automatically rings up each item based on its bar code. We update the prices daily, so we’re sure the sale is rung up for the right price.Lynn: That’s not my concern. What keeps a clerk from pretending to scan items and then simply not charging his friends? If his friends were buying 10–15 items, it would be easy for the clerk to pass several items through putting his finger over the bar code or just pass the merchandise through the scanner with the wrong side showing. It would look normal for anyone observing. In the old days, we at least could hear the cash register ringing up each sale.Kara: I see…
arrow_forward
6. What is the major advantage of using a perpetual inventory system?
a. It minimizes error in posting receipts and issues of materials.
b. It avoids inventory shortages and overages.
c. It provides efficient internal control over materials.
d. It avoids losses due to theft.
7. Scrap materials consists of:
a. Raw materials remaining from the production cycle but usable for purposes other than the original purpose.
b. Defective units that may be used or sold.
c. Finished goods that do not meet quality control standards and cannot be reworked.
d. Raw materials remaining from the production cycle but not usable for any purpose.
8. The sale of scrap from a manufacturing process is recorded as a(n):
a. Increased in finished goods control
b. Decrease in manufacturing overhead control.
c. Decrease in finished goods control
d. Increase in manufacturing overhead control
9. In a job-order…
arrow_forward
SEE MORE QUESTIONS
Recommended textbooks for you
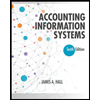
Accounting Information Systems
Accounting
ISBN:9781337619202
Author:Hall, James A.
Publisher:Cengage Learning,
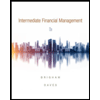
Intermediate Financial Management (MindTap Course...
Finance
ISBN:9781337395083
Author:Eugene F. Brigham, Phillip R. Daves
Publisher:Cengage Learning
Related Questions
- A company is trying to set up proper internal controls for their accounts payable/inventory purchasing system. Currently the purchase order is generated by the same person who receives the inventory. Together the purchase order and the receiving ticket are sent to accounts payable for payment. What changes would you make to improve the internal control structure? Group of answer choices 1.The person in accounts payable should generate the purchase order. 2.The person in accounts payable should generate the receiving ticket once the invoice from the supplier is received. 3.No changes would be made since the person paying the bills is different from the person ordering the inventory. 4.The responsibilities of generating the purchase order and receiving the inventory should be separated among two different people.arrow_forwardKeeping track of inventory and keeping carrying costs down. How do you think those issues would influence warehousing decisions? What might retailers do to reduce warehouse space and increase inventory accountability?arrow_forwardNeed Help on the following question. Question #1 You have been hired by the CEO of a soon-to-be-opened bookstore to develop procedures to help control inventory. List, describe, and defend four procedures you recommend be implemented to control inventory. As part of your response, be sure to describe any potential costs associated with these procedures.arrow_forward
- Need both parts.........arrow_forward. A company that uses a just in time inventory system: A) has finished goods inventory on hand at all times in order to speed up shipments of customer orders. B) may find that having less inventory actually leads to increased customer satisfaction. C) assesses its value chain to create new value-added activities. D) adopts a systematic, problem-solving attitudearrow_forwardThe business rules that constitute the purchases system for the Safe Buy Grocery Stores chain are similar at all the store locations. The purchase manager at each location is responsible for selecting his or her local suppliers. If the manager needs a product, he or she chooses a supplier. Each store follows the steps described here.1. The purchasing function begins with sales representatives from suppliers periodically observing the shelves and displays at each location and recognizing the need to restock inventory. Inventory declines by direct sales to the customers or by spoilage of perishable goods. In addition, the supplier’s sales representatives review obsolescence reports that the purchase manager prepares. These reports identify slow-moving and dated products that are deemed unsalable at a particular location. These products are returned to the supplier and replaced with more successful products. The sales representatives prepare a hard-copy purchase requisition and meet with…arrow_forward
- Please answer multichoice question in photoarrow_forwardWhich of the following is least likely to affect the preparation of the purchases budget? A.The amount of inventory stock available to purchase from suppliers. B.How easy it is to transport inventory from delivery trucks to the warehouse. C.The amount of warehouse space available. D.The shelf life of inventory.arrow_forwardOLTP VERSUS OLAP SERVERS For each of the following processes, state whether OLTP or OLAP is appropriate, and why. An order entry system that retrieves customer information, invoice information, and inventory information for local sales. An order entry system that retrieves customer information, invoice information, inventory information, and several years of sales information about both the customer and the inventory items. An order entry system that retrieves customer information, invoice information, inventory information, and information to compare the current sale to sales across several geographic regions. An order entry system that retrieves customer information, invoice information, inventory information, and accounts receivable information for sales within one marketing region. An insurance company requires a system that will allow it to determine total claims by region, whether a relationship exists between claims and meteorological phenomena, and why one region seems to be…arrow_forward
- How are duplicate checks useful in determining expected food revenue in nonautomated food operations?arrow_forward.Internal Controls and RiskReview the following description of the purchasing and AP procedures for a company and answer the questions at the end.The purchasing agent receives an inventory status report on his computer terminal from the inventory control application, which identifies the items that need to be reordered. The agent selects the suppliers and enters this information into the computer terminal to create a digital purchase order. He then prints and sends a copy of the PO to the supplier.When the goods are received directly into the warehouse, the warehouse manager counts and inspects them. The manager then creates a digital receiving report and updates the inventory subsidiary ledger from the warehouse terminal.A few days later, the supplier sends an invoice to the AP clerk who reconciles it with the digital copy of the receiving report. From her computer terminal, the clerk records the purchase in the purchases journal and records the liability by adding a record to the AP…arrow_forwardExplain the difference between the Perpetual and Periodic inventory systems and let us know why anyone would use Periodic inventory in this computerized age.arrow_forward
arrow_back_ios
SEE MORE QUESTIONS
arrow_forward_ios
Recommended textbooks for you
- Accounting Information SystemsAccountingISBN:9781337619202Author:Hall, James A.Publisher:Cengage Learning,Intermediate Financial Management (MindTap Course...FinanceISBN:9781337395083Author:Eugene F. Brigham, Phillip R. DavesPublisher:Cengage Learning
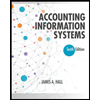
Accounting Information Systems
Accounting
ISBN:9781337619202
Author:Hall, James A.
Publisher:Cengage Learning,
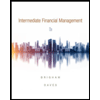
Intermediate Financial Management (MindTap Course...
Finance
ISBN:9781337395083
Author:Eugene F. Brigham, Phillip R. Daves
Publisher:Cengage Learning